Виробнича база будівельних керамічних виробів
Виробнича база будівельних керамічних виробів - це підприємство, де виготовляються вироби будівельної кераміки, а саме: цегла, керамічна плитка, санітарно-технічні вироби, покрівельна глиняна черепиця та інше.
При проектуванні виробничих баз будівельних керамічних виробів треба враховувати місце розташування сировини.
Сировинні матеріали, які використовуються при виготовленні виробів будівельної кераміки, поділяють на дві групи: глинисті (пластичні) і непластичні. Глинисті матеріали (глини і каоліни) - основна сировина. Непластичні матеріали у залежності від їх ролі в технологічному процесі поділяють на отощаючі і флюси (плавні) [30].
Отощаючі матеріали вводять у масу для зменшення усадки при сушінні йвипалюванні виробів, щоб зберігати форму виробу в процесі його виготовлення, полегшити і прискорити процеси сушіння й випалу виробів. При виробництві виробів будівельної кераміки як отощаючі матеріали застосовують кварцовий пісок, шамот і деякі інші матеріали (шлаки, золу та інше).
Флюси поліпшують спікання керамічного черепка при випалюванні, знижують температуру випалювання виробів. У процесі сушіння виробів флюси звичайно відіграють роль отощаючих матеріалів. Як флюси до складу маси для виготовлення виробів будівельної кераміки вводять польові шпати, пегматити, нефелінові концентрати, перліти, склобій.
Слово "глина" має два значення. Глинами називають визначені види гірських порід і тонкодисперсні (пилуваті) фракції глинистої породи.
|
|
В іншому випадку розрізняють власне глинисту частину породи і включення, які входять до складу глинистої гірської породи. Глинистою сировиною є тонкообламочні гірські породи різного хіміко-мінералогічного складу, що зустрічаються в природі у пухкому, пастоподібному або ущільненому стані.
Способи підготовки глини до виробництва будівельних виробів. Існують природні способи підготовки глини і механічні.
Природний спосіб полягає у використанні погодно-кліматичних умов для зміни властивостей сировини. Видобуту глину витримують тривалий час у вологій атмосфері. При вилежуванні чи виморожуванні в глині відбуваються наступні процеси. За рахунок збільшення обсягу води в глині при її замерзанні й набряканні порушуються зв'язки, глиняні грудки розпадаються на окремі зерна. Унаслідок цього зростає питома поверхня глини, збільшується кількість зв'язаної води, поліпшуються технологічні властивості матеріалу. Однак цей спосіб оброблення глин не застосується на підприємствах великої потужності, тому що для його здійснення необхідні великі виробничі площі, значні витрати на транспортування сировини. Природне оброблення використовують на заводах з невеликою річною витратою сировини.
|
|
При механічному способі структуру сировини руйнують, усереднюють сировину за речовинним складом і вологістю за рахунок впливу робочих органів механізмів. Механічний спосіб оброблення найбільш поширений на підприємствах керамічної промисловості. У залежності від технології виготовлення виробів механічне оброблення глини виконують різними способами. Глину, призначену для приготування пластичних мас, дозують, відокремлюють від неї кам'янисті добавки, подрібнюють, висушують, розмелюють (сухий помел). Для одержання шлікера глину дозують, подрібнюють, розпускають у воді, ведуть мокрий помел.
Устаткування виробничої бази будівельної кераміки. Для руйнування грудок глини застосовують глинорозрихлювач. Глинорозрихлювач (рис. 4.1) має ротори 5, які, обертаючись над живильником і зубцями, руйнують грудки глини.
Через решітку глина подається на транспортуючий орган живильника. У промисловості застосовуються глинорозрихлювачі СМ-1031-Б і СМ-1033 продуктивністю 18-30 мЗ/год [28]. Живильник забезпечує безупинне і рівномірне подавання глини.
Для кожного виду сировини застосовують окремий живильник, який налаштований на визначену продуктивність у залежності від вмісту даного матеріалу в шихті. Для подавання глини використовують ящикові живильники. Ящиковий живильник становить собою металеву ємність, дном у якій служать металеві пластинчасті конвеєри 4 (рис. 4.2) або гумова стрічка на капроновій основі. Місткість шухляди - 2-2,9 мЗ, продуктивність живильника - 24-45 мЗ/год [28].
|
|
Рис. 4.1. Глинорозрихлювач:
1 – корпус; 2 – електродвигун; 3 – редуктор; 4 – бункер;
5 – ротори з лопатями; 6 - шестерна передача
Валкові дробарки (вальці) застосовують для попереднього здрібнювання пластичних глиняних матеріалів, для подрібнення порід середньої і великої міцності, для вторинного подрібнення твердих і м'яких порід. Поверхня валків може бути гладкою, рифленою, зубцюватою або ребристою. У залежності від призначення дробарки (вальці) можуть бути різних типів. Зубцюваті вальці призначені для подрібнення пластичних глин.
Дискозубчаста дробарка подрібнює великі й морожені грудки глини розміром від 700-800 до 200-250мм двома валками діаметром 1200мм зі складальними фрезами. Валки обертаються назустріч один одному з різними кутовими швидкостями, що виключає замазування фрез глиною під час їх роботи. Дробарку встановлюють у технологічну лінію, яка вмикає приймальний бункер, стрічковий живильник, дробарку та відбірковий конвеєр. Продуктивність дробарки 60 т/год.
|
|
Рис. 4.2. Ящиковий живильник:
1 – била; 2 — шибер; 3 — корпус; 4 — пластинчастий конвеєр;
5 — електродвигун; 6 — редуктор
Каменевидільні вальці призначені для подрібнення глин, які мають тверді кам'янисті й інші сторонні домішки, з виділенням кам'янистих добавок. Кам'янисті добавки порушують структуру відформованого виробу, служать джерелом виникнення тріщин при його сушінні й випалюванні, зменшують міцність виробу. Крім того, кам'янисті добавки можуть спричинити поломку устаткування при обробленні глини. Для виділення каменів застосовують дезінтегратори і вальці з ребристим валком та вальці з гвинтовим валком.
Дезінтеграторні вальці з ребристим валком (рис. 4.3) складаються з двох валків різного діаметра - дробильного 1; подавального 2. Валки встановлені із зазором. Валок меншого діаметра (600мм) ребристий, обертається з більшою швидкістю, ніж гладенький валок більшого діаметра (1000мм). Глина, потрапляючи між валками, переминається, дробиться і проходить униз між валками, кам'янисті добавки 3 видаляються в отвір корпуса. Продуктивність вальців 25 мЗ/год.
Рис. 4.3. Дезінтеграторні вальці:
1 - дробильний валок; 2 - подавальний валок; 3 - кам'янисті добавки
Каменевидільні вальці з гвинтовим валком мають також два валки, але однакового діаметра - 750мм. На поверхні одного з них зроблена нарізка. Глина, потрапляючи між валками, переминається, дробиться і проходить униз. Кам'янисті добавки при обертанні валків змішуються гвинтовими поверхнями убік і віддаляються. Продуктивність вальців 35 м3/год.
Гладкі вальці (рис. 4.4) застосовують для подрібнення вологої глини і матеріалів середньої міцності - кварцу, польового шпату, вапняку, шлаків, шамоту. Вальці подрібнюють матеріал роздавлюванням, стиранням чи вигином валками 3, які обертаються один назустріч одному з різною швидкістю. При подрібненні вологої глини вальці працюють з максимальною ефективністю при зазорі між ними 2-3мм і вологості, близькій до формувальної.
Дірчасті вальці застосовують для подрібнення і часткового перетирання глиняної маси з метою руйнування структури глинистої породи. Вальці мають один тихохідний та інший швидкохідний валок. Робочий зазор між валками - 5мм. Глиняна маса, яка затягується і подрібнюється валками, продавлюється через отвори валків у вигляді окремих гранул і далі відводиться. Продуктивність вальців змінюється в залежності від отворів у сорочці валка й складає 8-30 м3/год.
Рис. 4.4. Гладкі вальці:
1 — рама; 2 — пружини; 3 — валки; 4 — завантажувальна лійка; 5 — шкребок
Рис. 4.5. Стругач з горизонтальним диском:
1 – лійка; 2 — лопати; 3 — ножі; 4 — тарілка шестерні; 5 — ріжучий диск;
6 — вертикальна вісь; 7 — станина; 8 — шкребок
Сухі, крихкі, мерзлі та вологі глини подрібнюють до шматків розміром 10-15мм на ножових глинорізках (стругачах). Стругачі бувають з горизонтальним і вертикальним ріжучим диском. Стругачі з горизонтальним ріжучим диском (рис. 4.5) найбільш поширені.
При обертанні диска 5 ножі 3 ріжуть глину, яка завантажується в лійку 1. Глина у вигляді стружки провалюється через отвори в диску нарозвантажувальну тарілку 4, упирається в шкребок 8 і направляється в розвантажувальне вікно. Товщину стружки регулюють висотою ножів над поверхнею диска. Продуктивність стругача 7-12 м3/год.
Після подрібнення глина через живильник на конвеєрі надходить у сушильний барабан або у шахтний млин. Сушильний барабан (рис. 4.6) становить собою зварний металевий циліндр, внутрішня порожнина якого служить сушильним простором.
Рис. 4.6. Сушильний барабан:
1, 5 — вивантажувальна і газова камери; 2 — циклон; 3 — димосос;
4 — бункер; 6 — топка; 7 — корпус сушильного барабана
Барабан установлюють з ухилом 5-6° у бік виходу висушеного матеріалу. Корпус 7 барабана, який обертається зі швидкістю 4-6 об/хв, кінцями входить у камери: газову 5, через яку гарячі гази надходять у барабан, і вивантажувальну 1, через яку відводяться відпрацьовані гази й вивантажується висушена глина. До газової камери прибудована топка 6, конструкція якої залежить від роду спалюваного палива. Перед подачею в барабан гази звичайно розбавляють холодним повітрям у камері для зниження температури до постійної величини. Відпрацьовані гази відсмоктують димососом 3 і пропускають через пиловловлюючий циклон 2, де відокремлюються дрібні частинки матеріалу, які знаходяться в газах у зваженому стані. Температура газів, які надходять у сушильний барабан, - 600-88О°С, на виході - 110-120°С. Останнім часом застосовують сушильні барабани з відкотними топками (рис. 4.7) [74].
|
Рис. 4.7. Сушильний барабан з відкотною топкою:
1 — візок з фіксатором; 2— зазор; 3 — підпірне кільце; 4—пальник; 5— завантажувальна тічка; 6 — торцева стінка; 7 — обичайка; 8 — приймальні лопати; 9— корпус сушильного барабана; 10 — розвантажувальна камера; 11 — система пилоочищення; 12 — димосос
Спалювання газу в них здійснюється безпосередньо у приймальній частині сушильного барабана, де продукти згорання розбавляються зовнішнім повітрям, яке надходить у барабан через зазори між торцевою стінкою 6 й обичайкою 7. Такий сушильний барабан працює наступним чином. Продукти згорання від пальників 4 надходять безпосередньо в корпус 9 обертального барабана, де розбавляються до заданої температури, наприклад, 800°С, який просмоктується через зазор 2 зовнішнім повітрям.
До змішування з продуктами згорання повітря нагрівається за рахунок теплообміну з торцевою стінкою 6, підпірним кільцем 3 й обичайкою 7 у вигляді поверхні обертання, яка виконує роль направляючої для підсмоктуючого всередину барабана повітря. Торцева стінка може переміщуватися вздовж осі барабана на візку 1 з фіксатором. Частина повітря за рахунок ежектуючої дії продуктів згорання відсмоктується до устя пальників і тічки, вмонтованих у вертикальну стінку, і охолоджує їх. Матеріал через завантажувальну тічку 5 надходить на приймальні лопати 8 і далі, пересипаючись, рухається до розвантажувальної камери 10 разом із теплоносієм, контактуючи з ним і висихаючи до заданої вологості. Гази, що відходять, проходять систему пилоочищення 11 та димосос 12 і викидаються в атмосферу.
Використання відкотної топки дозволяє помітно зменшити витрати палива на сушіння глини (на 20-25%), знизити кількість і температуру газів, що відходять, за рахунок різкого (майже вдвічі) скорочення підсмоктувань повітря, значно поліпшити умови експлуатації сушильних барабанів.
Сушать глину в сушильних барабанах прямотоком, тобто і матеріал, і підігріті гази рухаються в одному напрямку, тому що при протитечії глина може перегріватися, що призведе до втрати нею пластичних властивостей. При проходженні глини через сушильний барабан змінюється її зерновий склад. Дрібні шматки висихають і розсипаються в пил, великі запарюються й закатуються в грудки. Це зумовлює велику різнорідність з вологості як між окремими шматками, так і в межах одного шматка. Для усереднення вологості застосовують ланцюгові завіси всередині барабана, що частково подрібнюють глину, а також створюють проміжний запас висушеної глини, у якому з часом відбувається перерозподіл вологості.
Сушильний барабан запускають у такій послідовності: вмикають привід барабана; подають гарячі гази; вмикають живильні пристрої і конвеєри для висушеного матеріалу.
Якщо в процесі роботи сушильний барабан сповзає вздовж осі нагору, змазують робочі поверхні роликів на верхній опорі; якщо барабан переміщується вниз, необхідно насухо протерти робочі поверхні опорних роликів і бандажа; якщо барабан продовжує опускатися, потрібно протерти ролики і на нижній опорі.
Сушильний барабан повинен працювати при постійній температурі вихідних газів. При зміні вологості матеріалу чи інтенсивності подачі його в барабан, режим сушіння регулюють тільки кількістю гарячих газів, які надходять у барабан; змінювати температуру газів рекомендується лише в незначних межах, збільшуючи або зменшуючи подачу холодного повітря в змішувальну камеру. Вологість матеріалу, який надходить у барабан та виходить з нього, контролює лабораторія і результати аналізів повідомляє робітникам, які обслуговують сушильний барабан.
Зупиняють сушильний барабан у такий спосіб. За 30 хв до зупинки барабана припиняють подавання сирого матеріалу. Потім перестають подавати теплоносій у барабан. Після цього вимикають привід і пристрій для транспортування висушеного матеріалу. При раптових зупинках припиняють подаання палива.
Для сушіння глини застосовують сушильні барабани продуктивністю 2, 5 і 15т/год. [28].
Існують технологічні схеми підготовки глини, в яких поєднуються процеси сушіння і розмелення глини в одному агрегаті.
Шахтний млин (рис. 4.8) - агрегат для одночасного розмелення і сушіння глини.
Працює млин таким чином. Глина після попереднього подрібнення надходить через тічку 6 у сепараційну шахту 5. Вона падає шматками назустріч потоку гарячих газів, що рухаються нагору по шахті. Гарячі гази з топки засмоктуються в млин по газоходу 2. У шахті найдрібніші часточки відносяться в пиловловлюючі пристрої, а більші шматки падають у млин і подрібнюються. Під дією газового потоку, а також завдяки великій кількості обертів ротора 3 з билами 4, глиняні частки викидаються знову в сепараційну шахту, де дрібні часточки відносяться газами нагору, а великі - повертаються на
домелювання. Таким чином тонкість помелу глиняного порошку визначається швидкістю газів у сепараційній шахті, яка регулюється. У млині, куди надходять гарячі гази, глина одночасно розмелюється й сушиться, у шахті над млином розсіюється і частково досушується. Із шахти гази несуть глиняний порошок у пилоосаджувачі, які працюють послідовно. Готовий порошок подається в бункери, а очищені гази викидаються в атмосферу. Продуктивність млина досягає 25 т/год порошку глини.
Глиняні порошки, отримані в шахтному млині, відрізняються від порошків глини, висушеної у сушильному барабані з наступним розмелом, більшою питомою поверхнею навіть при рівних результатах гранулометричного аналізу, осколковою формою зерен і меншими перепадами вологості по фракціях. Ці особливості порошків, одержуваних у шахтному млині, сприяють збільшенню швидкості та ступеня набрякання глини при подальшому зволоженні, поліпшенню якості маси.
Висушену в сушильних барабанах глину розмелюють, щоб одержати порошок заданого зернового складу. Для помелу глини застосовують корзинчасті дезінтегратори, бігуни сухого помелу.
Корзинчасті дезінтегратори застосовують на багатьох заводах. Дезінтегратор (рис. 4.9) складається з двох циліндричних кошиків, які обертаються один всередині іншого у різних напрямках (назустріч один одному).
Кошики становлять собою сталеві диски 4, 5, прикріплені до ступиць 6, 7, які мають три ряди жорстко закріплених пальців 3. Матеріал для помелу подається всередину обертових кошиків через завантажувальну тічку 2.
Потрапивши при падінні на пальці внутрішнього ряду малого кошика, шматки глини під дією удару пальців розбиваються, відкидаються і потрапляють на наступний ряд пальців великого кошика, що обертається в протилежний бік. Потім матеріал відкидається на третій, четвертий ряди пальців і т.д., доки подрібнені часточки не пройдуть через усі ряди. Тонкість помелу в дезінтеграторі підвищується зі збільшенням кількості рядів пальців і частоти обертання кошика. При збільшенні частоти обертання з підвищенням тонкості помелу матеріалу деякий час зростає і продуктивність дезінтегратора, але потім, унаслідок труднощів проходу матеріалу, при великій кількості обертів від центру до периферії продуктивність знижується. Подрібнений матеріал надходить у нижню частину кожуха, звідки потрапляє в бункери або на подальше перероблення.
Рис. 4.9. Дезінтегратор:
1,8 — приводні вали;2 — завантажувальна тічка; 3 — пальці;
4, 5 — диски; 6, 7 – ступиці
Нормальна робота дезінтегратора забезпечується при рівномірному живленні шматками глини розміром 25-30мм, вологістю 8-12%. Підвищення вологості спричиняє злипання й замазування дезінтегратора глиною. Їх продуктивність складає від 2 до 10 т/год.
Недоліки дезінтеграторів: швидке зношення пальців і порушення балансування, порівняно велика витрата електроенергії, розпушеність глини після помелу, що ускладнює пресування. При потраплянні металевих предметів у дезінтегратор він виходить з ладу. У зв'язку з цим, перед дезінтеграторами обов'язково встановлюють магнітні уловлювачі, а при помелі глини з твердими добавками - машини для максимального їх виділення. Бігуни сухого помелу (рис. 4.10) використовують при вологості глин не вище 8-9%.
Дія бігунів основана на роздавлюванні й одночасному стиранні матеріалу при обертанні чаші 3 навколо вертикального вала 2, якщо катки 1 рухливі, або при качанні катків по нерухомій чаші. Матеріал, що надходить, під дією сили ваги катків роздавлюється, а при ковзанні катків по чаші стирається. Ковзання катків утворюється різницею швидкостей руху окремих точок зовнішньої поверхні циліндричного обода катка по довжині її утворюючої. Величина ковзання прямо пропорційна ширині катка. Порошки, отримані в бігунах, відрізняються підвищеною щільністю і малими пружними деформаціями, що сприяє хорошому формуванню. Недоліки бігунів - невелика продуктивність при великій масі та висока експлуатаційна вартість (великі витрати змінних деталей спожитої електроенергії). Крім того, при їх роботі виділяється багато пилу через недостатню герметичність.
Рис. 4.10. Бігуни сухого помелу:
1 — катки; 2 — вертикальний вал; 3 — обертаюча чаша; 4 — нерухомий піддон;
5 - кільцеве сито; 6 — шкребок
Електромагнітний барабан (рис. 4.11) застосовують для очищення від магнітних часток меленої глини, кварцеполевошпатових матеріалів або шихти [28].
Рис. 4.11. Схема електромагнітного барабана:
1 – лоток; 2 – барабан; 3 - електромагнітна система; 4 - залізовмісні домішки;
5 - розділова стійка; 6 - матеріал, очищений від залізовмісних домішок
Очищений матеріал лотком 1 подають рівномірним шаром на обертовий барабан 2, виготовлений з латуні або сталі, що втрачає магнітні властивості після виходу з магнітного поля. Усередині обертового барабана нерухомо закріплена електромагнітна система 3, яка складається з котушок та магнітів і встановлена так, що магнітне поле знаходиться на тому боці барабана, по якому переміщується матеріал. Переміщуючись разом із барабаном, матеріал 6, очищений від залізовмісних домішок, зісковзує з барабана, не доходячи до розділової стійки, а залізовмісні домішки 4 випадають за розділовою стійкою 5, виходячи із сфери впливу магнітного поля [74].
Стрічковий живильник з електромагнітним ведучим барабаном має таку ж конструкцію, як і електромагнітний барабан, який відрізняється тільки тим, що матеріал подається не лотком, а стрічковим конвеєром невеликої довжини, який обгинає електромагнітний барабан.
Підвісні електромагніти призначені для вилучення залізних предметів, особливо з верхніх шарів сипучої маси товщиною не більше 100мм, які переміщуються конвеєрною стрічкою зі швидкістю не більше 2 м/сек. Поміщений у металевий кожух електромагніт підвішують вертикально або під кутом, що відповідає куту нахилу конвеєрної стрічки, на відстані від її поверхні не більше 0,12-0,13м. Полюсний наконечник періодично очищають від налиплих на нього залізних предметів.
Для формування виробів будівельної кераміки застосовують горизонтальні й вертикальні стрічкові вакуум-преси.
Стрічковий вакуумний прес (рис. 4.12) діє таким чином: підготовлена пластична маса надходить у змішувач (або приймальну камеру), де перемішується й у разі потреби дозволожується і прогрівається паром. Лопаті 2, розташовані на валу змішувача, просувають глиняну масу до вхідного отвору вакуум-камери 5. Перед входом у вакуум-камеру глиняна маса, за допомогою гвинта 3, заповнює конусну вихідну частину змішувача, проходить через отвори решітки 4, розрізається ножами на дрібні шматки і потім потрапляє у вакуум-камеру [93].
Розрідження у вакуум-камері преса створюється водокільцевими (ВВН-1-3, ВВН-1-6, ВВН-1-12) і плунжерними (ВН-4, ВН-6) вакуумними насосами (остання цифра в марці вказує на продуктивність насоса в м3/хв).
За рахунок зниженого тиску у вакуум-камері з глиняної маси відсмоктується повітря, частки вологої глини зближуються, маса ущільнюється й набуває нових властивостей, завдяки яким для пластичного формування труб, черепиці та інших тонкостінних керамічних виробів можна застосовувати дрібні маси, а міцність, щільність і однорідність обпалених виробів значно підвищуються. Грудки безповітряної (вакуумованої) глиняної маси збираються в нижній частині вакуум-камери і спільним зусиллям нагнітального валка та приймальних лопат вала 6 захоплюються і просуваються в корпус 7 преса. Тут ущільнена глиняна маса подається двозахідним гвинтом у перехідну голівку 8, у якій маса додатково ущільнюється і швидкість її руху по перетину голівки вирівнюється. Остаточно маса ущільнюється в мундштуці 9, з якого
виходить сформований брус заданої форми.
При формуванні кислототривких виробів (цегли, плитки) відношення площ перетину циліндрів пресу і вихідного отвору повинно знаходитися у межах 2,5 - 4, а діаметра циліндра і діагоналі вихідного отвору мундштука -1,4 - 1,65. Внутрішні стінки мундштука мають для кращого ущільнення маси конусність у межах 5-7%, що визначається властивостями маси. Довжина мундштука - 150-300мм.
При формуванні на вакуумних пресах часто застосовують короткі металеві мундштуки з незначною конусністю. Використовують також формуючі мундштуки, поверхні яких виготовляють із твердого сплаву ВК8 або із зносостійкого чавуна. Термін служби деталей формуючого інструмента, виготовленого зі сталі Ст3, складає 3-7 діб, стійкість деталей зі зносостійкого чавуна в 9-14 разів вища, ніж зі сталі Ст3, деталі з твердого сплаву ВК8 служать 1-1,5 роки.
Перед пуском вакуумного преса перевіряють герметичність і чистоту решітки, справність ножів, що розрізають глиняну масу у вакуумній камері, чистоту фільтра на лінії до вакуум-насоса, справність вакуум-насоса, надійність його приєднання до вакуум-камери, вмикання лампи освітлення вакуум-камери. Крім того, оглядають кріплення лопаток у змішувачі й кут їх повороту (не повинен перевищувати 20°), величину зазорів між лопатами в змішувачі і його корпусом. Контролюють також стан, центрування і чистоту мундштука, стан кріпильних деталей, справність огороджувальних пристроїв. У робочих лопатах преса не повинно бути сторонніх предметів. Зазор між лопатами вала і внутрішньою поверхнею сорочки циліндра преса (при всіх положеннях лопат) не повинен перевищувати 2-3мм. Не повинно бути вібрації або хитання вихідного кінця вала (перевіряють на холостому ходу). Якщо в процесі роботи циліндр преса перегрівається, що відбувається при зворотному русі глиняної маси в зазорі між лопатами і сорочкою циліндра, необхідно зупинити прес і наварити лопати вала твердим сплавом (сталінітом) так, щоб зазор становив не більше 2-3мм. Продуктивність преса багато в чому залежить від стану лопат преса. При застосуванні шліфованих лопат поліпшується ковзання маси по гвинту і полегшується її просування в циліндрі преса. Лопати шліфують у звичайних галтовочних барабанах, які заповнюють водою, глиною і піском або шліфувальним порошком.
Вакуумний прес запускають у такій послідовності. Спочатку вмикають вакуум-насос і вентиль на всмоктувальному трубопроводі насоса, перевіряють, щоб у вакуум-камері було потрібне розрідження, а у вакуумній системі не було підсмоктування повітря. Потім умикають електродвигун, муфту вмикання преса, живлення преса глиняною масою і, нарешті, живлення змішувача.
У початковий період роботи перевіряють величину розрідження у вакуум-камері й рівномірність швидкості виходу бруса по периметру мундштука. Якщо в брусі містяться грудки сухої маси і в окремих місцях відбувається розрив маси, варто зупинити прес й очистити мундштук та перехідну голівку преса. Якщо одна сторона бруса рухається швидше іншої, необхідно перевірити центрування мундштука і при необхідності зрушити його у бік прискореного руху маси. При короткочасній зупинці преса припиняють живлення преса, вмикають муфту вмикання, не від’єднуючи електродвигуна і вакуум-насоса. При зупинці преса на тривалий період спочатку припиняють подачу глиняної маси в прес, а після виробки всієї маси в циліндрі преса, приймальній частині та вакуум-камері вмикають муфту зчеплення, від’єднують електродвигун преса, перекривають усмоктувальний трубопровід і від’єднують вакуум-насос.
Стрічкові преси обладнують звуковою сигналізацією для оповіщення обслуговуючого персоналу про пуск і зупинку преса. Не дозволяється запускати прес зі знятими або несправними огородженнями. Чистити, змазувати, ремонтувати, регулювати і налагоджувати прес можна тільки після зупинки преса та зняття електромонтером запобіжних пускових пристосувань або вилок розриву живильної електролінії. Не дозволяється під час роботи преса очищувати поверхню живильного валка і стінки приймальної коробки преса від глини, проштовхувати масу в приймальну коробку, відбирати проби, витягувати сторонні предмети з приймальної коробки преса.
Розрізання бруса. Глиняний брус, який виходить із преса, розрізають на відрізки заданих розмірів на різальних автоматах [93].
Автомат для різання цегли-сирцю (рис. 4.13) працює у такий спосіб. Вихідний з мундштука преса глиняний брус приймається на приймальний стрічковий конвеєр
2. Глиняний брус надає рух конвеєру за рахунок сили тертя бруса об стрічку конвеєра. Від стрічки, що рухається, одержує обертання регулювальний барабан автомата і через систему передач 5 надає лучку 4 зворотно-поступального руху.
Таким чином глиняний брус відрізається лучком при одночасному поступальному русі лучка зі швидкістю руху глиняного бруса. Недоліки автомата: не забезпечує точного відрізання, часто доводиться замінювати струни, які лопнули. Під час роботи преса періодично відбирають по одній-дві відрізаних заготовки і заміряють довжину, перпендикулярність зрізу і правильність форми. При обриванні ріжучої струни привод преса й автомата негайно вимикають. Умикають прес у роботу після установки й натягування нової струни. При обслуговуванні різальних автоматів необхідно дотримуватися таких правил. Не можна працювати на автоматі, якщо знято огородження лучка. Забороняється виконувати роботи в зоні руху. Для налагодження автомата та його змазування зупиняють і виключають муфти зчеплення преса.
Допресування бруса. Заготовка кислототривкої цегли і плиток, після відрізання їх різальними верстатами, має недостатньо чітку форму й точні розміри, тому їх при вологості 17-18% допресовують. При цьому усувають такі недоліки пресування, як неоднорідність структури маси, внутрішні тріщини. Для допресування сирцю застосовують преси Самаріна, СМ-308А, ССМ-81, СМ-1208.
Допресувальний прес Самаріна (рис. 4.14) буває пересувним і стаціонарним. На плиті 5 із двома вертикальними стійками 3, зв'язаними нижньою нерухомою траверсою 2, встановлено форму для допресування виробів. Над формою до траверси прикріплено столик 6 з кареткою, призначеною для подачі заготовок і знімання допресованого сирцю. Верхній штамп преса прикріплено до рухливої траверси 1, що одержує вертикальний рух через закріплений на валу ексцентрик 4, який перетворює обертальний рух у зворотно-поступальний, що забезпечує у момент знімання допресованих виробів паузу відповідної тривалості. Допресований виріб виштовхується рухливим днищем форми. Рештки маси (0,5-1% обсягу сирцю) виходять з форми через отвір. Тиск допресування не перевищує 2МПа. Продуктивність преса Самаріна 1,3-1,4 тис шт/год, пресів СМ-308, СМ-1208 і ССМ-81 -1,8-2,3 тис шт/год.
Рис. 4.13. Автомат для різання цегли-сирцю:
1 – станина; 2 – конвеєр; 3 - глиняний брус; 4 – лучок; 5 – приводний пристрій
Вид А
Рис. 4.14. Допресувальний прес Самаріна:
1 – рухлива траверса з верхнім штампом; 2- нижня нерухома траверса;
3 - вертикальні стійки; 4 – ексцентрик; 5 – плита; 6 - столик з кареткою
На допресувальних пресах СМ-308 А, СМ-І208 і ССМ-81 забезпечується двостороннє пресування, що сприяє поліпшенню якості виробів. Для уникнення прилипання до штампів заготовки змазують сумішшю гасу (90%) зі стеарином (10%) на пресі Самаріна вручну, на інших - механічно.
Цегла глиняна звичайна суцільна і пустотіла, пластичного і напівсухого пресування, становить собою штучний камінь, виготовлений із глини з добавками або без них, і обпалена. За зовнішнім виглядом цегла повинна мати форму прямокутного паралелепіпеда з прямими ребрами й кутами, з рівними гранями. Цеглу виготовляють одинарним розміром 250x120x65мм і модульним 250x120x88мм. Модульна цегла з технологічними порожнинами має масу не більше 4кг. У цеглі технологічні порожнини можуть бути наскрізними або ненаскрізними й повинні розташовуватися перпендикулярно постелі; діаметр великих наскрізних порожнин складає не більше 16мм, а ширина прямокутних порожнин - 12 мм. Як сировину застосовують легкоплавкі глини, які містять 50-75% кремнезему. Виготовлення будівельної цегли здійснюють двома способами - пластичним і напівсухим. Найбільш розповсюджений пластичний спосіб [31].
Пластичний спосіб виробництва глиняної цегли здійснюється за наступною схемою (рис. 4.15).
Глину, яка надійшла на завод, обробляють до одержання пластичної однорідної маси. Для цього глиняну сировину спочатку подрібнюють на вальцях: глиняна маса надходить на поверхню двох валків, які обертаються назустріч один одному, в результаті чого глина втягується в зазор між ними і подрібнюється.
Валки можуть мати різні діаметри й обертатися з неоднаковою швидкістю, в результаті чого подрібнювання відбувається інтенсивніше. Для більш ефективного подрібнювання до вальців додають бігуни. Потім суміш надходить у глиномішалку, де вона зволожується до 18-25% і перемішується до одержання однорідної пластичної маси. Ретельно приготована однорідна маса надходить потім у стрічковий прес. Для одержання цегли більш високої щільності й поліпшення формувальних властивостей глин застосовують вакуумні стрічкові преси (рис. 4.16).
Рис. 4.15. Технологічна схема виробництва глиняної цегли
за пластичним способом формування:
1 - ящиковий подавач; 2 - транспортер; 3 - подрібнення глини і відділення каменю на дезінтеграторних вальцях; 4 - помел глини на бігунах; 5 - транспортер; 6 - формування цегли на стрічковому пресі; 7 - різання цегли-сирцю на автоматі
Рис. 4.16. Стрічковий вакуум-прес:
1 – ніж; 2 – вакуум-камера; 3 – решітка; 4 - глином’ялка; 5 - шнековий вал преса;
6 - пресувальна голівка; 7 – мундштук; 8 - глиняний брус
Глиняну масу, яка надходить у стрічковий прес, за допомогою шнека ущільнюють, після чого вона направляється до вихідного отвору-мундштука. З останнього виходить безперервний глиняний брус, який потрапляє на автомат для різання й укладання цегли-сирцю на вагонетки камерних або тунельних сушарок. Продуктивність стрічкових пресів до 10000 штук за годину. Термін сушіння цегли – 1-3 доби.
Процес випалювання умовно можна розділити на три періоди: прогрівання, власне випалювання й охолодження. У період прогрівання із сирцю віддаляється гігроскопічна і гідратна волога, згорають органічні домішки, рівномірно прогрівається маса і розкладаються карбонати. При власне випалюванні відбувається розплавлювання найбільш плавкої складової частини глини, яка обволікає частки глини, щоб вони не розплавилися, спікаючи масу. Період охолодження супроводжується утворенням каменю.
Рис. 4.17. Тунельна піч:
1 - корпус печі; 2 - вагонетка з цеглою
Випалювання цегли здійснюють у печах безперервної дії - кільцевих і тунельних. Кільцева піч становить собою замкнутий випалювальний канал, умовно поділений на камери. Ці печі відрізняються високою трудомісткістю і важкими умовами праці, тому на нових заводах їх не будують. Тунельна піч (рис. 4.17) є найсучаснішою.
Вона становить собою канал перетином 3,5-5,5м2, довжиною до 100м. У каналі покладені рейки, по яких рухаються вагонетки з цеглою-сирцем. Тунельна піч має три зони: підігрівання, випалювання й охолодження, через які послідовно, протягом 18-36 годин, проходять вагонетки з цеглою-сирцем.
Тунельні печі найбільш економічні через більш механізоване виробництво, а також краще використання тепла. Витрати цегли в тунельних печах порівняно невеликі.
Напівсухий спосіб виробництва глиняної цегли має переваги перед пластичним. Він не потребує сушіння виробів і дозволяє використовувати малопластичні глини. Разом з тим зменшуються потреби у виробничих площах і робочій силі. Однак, якість цегли, одержуваної напівсухим способом, зокрема, морозостійкість, нижча, ніж цегли, одержаної пластичним пресуванням. При напівсухому способі формування (рис. 4.18) сировинні матеріали, після попереднього подрібнювання на вальцях, висушують у сушильному барабані до вологості 6-8%, потім ще подрібнюють у дезінтеграторі, просівають, зволожують до 8-12% і ретельно перемішують.
Підготовлену масу формують (пресують) на гідравлічних або механічних пресах продуктивністю до 10000 шт./год. Відформовану цеглу направляють у піч на випалювання і далі на склад.
Напівсухим методом можна пресувати не тільки повнотілу цеглу, але й п'ятистінну, дірчасту, а також різну керамічну плитку.
Властивості цегли. Якість цегли, незалежно від способу виробництва, повинна задовольняти вимогам ДСТУ Б.В.2.7-61-97. Марка цегли визначається за межею міцності при стискуванні й вигинанні. Цеглу випускають семи марок: 75, 100, 125, 150, 200, 250 і 300.
Цегла кожної марки повинна мати відповідну межу міцності при вигинанні - 1,8; 2,2; 2,5; 2,8; 3,4; 4,0 і 4,4 МПа. Цеглу випускають таких розмірів: довжина - 250±4, ширина - 120±3 і товщина - 88 або 65 + 3 - 2. Скривлення ребер і граней не повинно перевищувати 3мм, механічні пошкодження не допускаються; окремі незначні відбитості ребер і кутів не повинні перевищувати 15мм по довжині ребра і більше двох на одній цеглі. Вапняні добавки (дутики), недовипалювання і перепалення не допускаються. Випалювання цегли повинно відповідати кольору еталона. Недовипалена цегла має недостатню міцність і морозостійкість, а перепалена має підвищену міцність і теплопровідність, але, як правило, перекручену форму. Необхідно, щоб нормально обпалена цегла, для марок вище 150, мала водопоглинення не менше 6% від маси цегли, висушеної до постійної маси, а для цегли інших марок - не менше 8%. За морозостійкістю цеглу розподіляють на чотири марки: Мрз 15; 25; 35 і 50.
Цеглу глиняну звичайну застосовують для виготовлення цегельних панелей зовнішніх і внутрішніх стін, кладки зовнішніх і внутрішніх стін, стовпів, склепінь та інших несучих конструкцій. Цеглу глиняну, напівсухого пресування, використовувати для фундаментів і цоколів нижче гідроізоляційного шару не дозволяється внаслідок зниженої її морозостійкості.
Цегла глиняна пустотіла, легка. Цеглу глиняну пустотілу виготовляють з легкоплавких глин з добавками або без них за способом пластичного і напівсухого пресування. Масу для пустотілої цегли обробляють більш ретельно, формування бажано робити на вакуумних пресах зі спеціальним пристосуванням (кернами) для утворення отворів (порожнин) у цеглі. Порожнини в цеглі розташовуються перпендикулярно постелі. За формою вони бувають круглими, діаметром не більше 15 мм, або прямокутними з шириною щілини не більше 15 мм. Пустотілу цеглу виготовляють розмірами 250x120x88 та 250x120x65 мм; марками за міцністю на стискування 75, 100, 125 і 150; об'ємною масою - 1300-1450 кг/м3; водопоглинанням - не менше 6% і морозостійкістю не нижче 15 [30].
Цеглу глиняну пустотілу застосовують для несучих зовнішніх і внутрішніх стін, перегородок та інших частин будівель і споруд. Не рекомендується застосовувати зазначену цеглу для фундаментів, цоколів та стін мокрих приміщень. Цегла будівельна легка становить собою штучний камінь, виготовлений з діатомітів або трепелів з добавками глини або глини і вигоряючих добавок, шляхом формування і випалювання. У порівнянні зі звичайною цеглою ця цегла має меншу об'ємну масу та знижену теплопровідність. Її застосування дозволяє зменшити товщину стіни, полегшити конструкцію і збільшити площу будівлі [55].
Рис. 4.18. Технологічна схема виробництва цегли методом напівсухого формування:
1 — ящиковий подавач; 2 — стрічковий транспортер; 3 — дезінтеграторні вальці;
4 — циклон; 5 — сушильний барабан; 6 — бункер; 7 — тарілчастий живильник;
8 — дезінтегратор; 9 — елеватори; 10 — грохот; 11 — глиномішалка з парозволожувачем; 12 — живильник; 13 — прес
Технологічна схема виробництва легковагої цегли мало відрізняється від процесу виробництва звичайної глиняної цегли пластичного формування. Цеглу будівельну легку випускають розміром 250x120x88 мм. Цегла з об'ємною масою 700-1000 кг/мЗ має міцність 3,5; 5,0 і 7,5 МПа; при об'ємній масі 1000-1300 кг/см3 - міцність цегли 5,0 і 7,5 МПа, а при об'ємній масі 1300-1450 кг/мЗ - міцність 5,0; 7,5 і 10,0 МПа. Морозостійкість повинна бути не менше 10. Застосовують легку цеглу для стін будівель і споруд з нормальною вологістю приміщень.
Сушіння і випалювання. Якщо ж сирець, який має високу вологість, відразу після формування обпалити, то він розтріскується. При сушінні сирцю штучним способом як теплоносій використовують димові гази випалювальних печей, а також спеціальних топок. При виготовленні виробів тонкої кераміки застосовують гаряче повітря, утворене в калориферах. Штучне сушіння здійснюють у сушилах періодичної дії - камерних сушарках (рис. 4.19) або безперервної дії - тунельних сушарках (рис. 4.20).
Процес сушіння становить собою комплекс явищ, пов'язаних з тепло- і масообміном між матеріалом та навколишнім середовищем. У результаті відбувається переміщення вологи з внутрішньої частини виробів на поверхню і її випарювання. Одночасно з видаленням вологи частки матеріалу стискуються і відбувається усадка. Зменшення обсягу глиняних виробів при сушінні відбувається до певної межі, незважаючи на те, що вода до цього моменту повністю ще не випарувалася.
Рис. 4.19. Камерне сушило
Рис. 4.20. Тунельне сушило
З метою одержання високоякісних керамічних виробів процеси сушіння і випалювання повинні здійснюватися у строгих режимах.
При нагріванні виробу в інтервалі температур 0-150°С з нього видаляється гігроскопічна волога. При температурі 70°С тиск водяної пари всередині виробу може досягти значної величини, при цьому для попередження тріщин температуру слід піднімати повільно (50-80° С/год), щоб швидкість пароутворення всередині матеріалу не випереджала швидкість фільтрації пари через її товщину.
Випалювання є завершальною стадією технологічного процесу. У піч сирець надходить з вологістю 8-12%, де в початковий період відбувається досушування сирцю. В інтервалі температур 550-800°С відбувається дегідратація глинистих мінералів та видалення хімічно зв'язаної конституційної води. При цьому руйнуються кристалічні решітки мінералу, глина втрачає пластичність, у цей час відбувається усадка виробів. При температурі 200-800°С виділяється летюча частина органічних домішок глини та вигораючих добавок, уведених до складу шихти при формуванні виробів, і, крім того, окисляються органічні домішки в межах температури їх загорання. Цей період характерний дуже високою швидкістю підйому температур - 300-350°С, а для ефективних виробів - 400-450°С/год, що сприяє швидкому вигоранню палива, запресованого в сирець.
Потім вироби витримують при цій температурі в окисній атмосфері до повного вигорання залишків вуглецю. Подальше підвищення температури від 800°С до максимальної пов'язаний із руйнуванням кристалічної решітки глинистих мінералів та значною структурною зміною черепка, тому швидкість підвищення температури сповільнюють до 100-150°С, а для пустотілих виробів - 200-220°С/год. Після досягнення максимальної температури випалювання виріб витримують для вирівнювання температури по всій його товщині, після чого температуру знижують на 100-150°С, у результаті виріб здійснює усадку та пластичні деформації. Потім інтенсивність охолодження при температурі нижче 800°С збільшується до 250-300°С/год і більше, обмеженням зниження температури можуть бути лише умови зовнішнього теплообміну. За таких умов випалювання цегли можна здійснити за 6-8 годин. Однак, у звичайних тунельних печах швидкісні режими випалювання не можуть бути реалізовані через велику нерівномірність температурного поля по перетину випалювального каналу. Вироби з легкоплавких глин обпалюють при температурі 900-1100°С. У результаті випалювання виріб набуває каменеподібного стану, високої водостійкості, міцності, морозостійкості та інших цінних будівельних якостей.
Тунельні печі. Керамічні вироби пластичного формування обпалюють у тунельних печах прямої дії, у яких продукти згорання стикаються безпосередньо з обпалювальною продукцією, і муфельних, де керамічні вироби обпікаються гарячим повітрям.
Тунельні печі (рис. 4.21) поділені на три зони - підігрівання 1, випалювання 2 і охолодження 3, які, у свою чергу, поділені на позиції за кількістю вагонеток, що знаходяться в зоні.
Обпалювані в тунельних печах вироби транспортують через піч на вагонетках. Для захисту від високих температур металева частина вагонетки закрита вогнетривкою футерівкою товщиною 300-400мм. Для створення герметичності між вагонетками і піччю по всій довжині печі знаходяться піскові затвори. До бокових сторін вагонетки кріпляться бічні листи-фартухи піскового затвору, які рівномірно завантажені в пісок затвору. Між дотичними торцевими сторонами вагонеток, за рахунок футерівки, утворюється лабіринтове з'єднання, додатково ущільнене підшитим до металевих рам азбестовим шнуром. Це ущільнення перешкоджає потраплянню гарячих газів у підподовий простір печі.
Тунельні печі працюють за принципом протитечії. Спочатку вагонетки з виробами підігріваються продуктами згорання, які відходять із зони випалювання, потім проходять через зону випалювання, піддаючись дії високих температур, після чого надходять у зону охолодження, де охолоджуються, віддаючи тепло повітрю. Тепло може передаватися при прямому контакту полум'я з обпалювальним виробом або через муфель. Димові гази відбираються на початку печі через вікна, повітря на охолодження і горіння подається на виході вагонеток зпечі. Оскільки на горіння потрібно менше повітря, ніж на охолодження, частина гарячого повітря з зони охолодження відбирається для використання поза піччю. Для зменшення різниці температур по перетину печі й підвищення швидкості прогрівання низу садки в зону підігрівання подають гаряче повітря із зони охолодження або на цій ділянці здійснюють рециркуляцію димових газів.
Вагомий недолік тунельних печей полягає у тому, що в них важко підтримувати стійкий режим у робочому потоці. У робочому просторі печі підтримують значне розрідження, що необхідно для того, щоб гази просмоктувалися через піч. Через нещільності стиків вагонеток, затворів, на вході й виході печі підсмоктується холодне повітря, підсилюючи перепад температур по перетину каналу. Підсмоктування повітря в піч недопустиме, особливо якщо обпалювання йде у відновному середовищі. Для зменшення розрідження в зону охолодження подають холодне повітря, у результаті чого зона охолодження знаходиться під тиском, зона випалювання - при нульовому тиску, зона підігрівання - під невеликим розрідженням. На початку та в кінці печі влаштовують вхідні й вихідні шлюзові камери на одну вагонетку, що ізолює робочий простір під час штовхання вагонетки. Завдяки цьому досягається стійкий газовий режим у робочому потоці печі.
Вагонетки в тунельних печах періодично проштовхують на довжину однієї вагонетки відповідно до заданого режиму випалювання. Недоліком періодичного проштовхування вагонеток є те, що в період проштовхування порушується температурний режим печі, а вироби, швидко переходячи з однієї позиції на іншу, піддаються температурним коливанням, що несприятливо впливає на їх якість. Щоб усунути цей недолік, застосовують імпульсний спосіб проштовхування вагонеток. Суть його полягає в наступному. Шлях руху вагонеток, з однієї позиції на іншу, умовно поділений на десять відрізків. Тривалість перебування вагонетки на одній позиції, після чергового штовхання, також поділена на десять рівних проміжків часу. У момент штовхання вагонетка переходить у чергову позицію печі на 1/10 своєї довжини та знаходиться на цьому відрізку 1/10 заданого часу, після чого процес повторюється. Наприклад, вагонетка на позиції повинна знаходитися 30 хв. Вона проштовхується на 1/10 своєї довжини через кожні 3 хвилини і повністю переходить на наступну позицію через 30 хв. У результаті не порушується температурний режим роботи печі.
У більшості випадків у промисловості будівельної кераміки тунельні печі опалюються газом, мазутом, іноді твердим паливом. Печі з електрообігріванням мають переваги. У них легко встановлюється і досить точно регулюється необхідна температура випалювання.
Обслуговування тунельних печей. При обслуговуванні тунельної печі дотримуються таких правил. У кожній тунельній печі обпалюють вироби одного виду. Завантажують піч за графіком. Перед піччю повинен бути запас вагонеток, при цьому кількість вагонеток, завантажених продукцією для випалювання, і кількість пустих вагонеток регламентують технологічні карти відповідно до наявності виробничих площ [55].
Вироби завантажують на справні вагонетки так, щоб максимально використовувати пічний обсяг і зберегти достатню газопроникність садки виробів у подовжньому і поперечному напрямках. У піч вагонетки подають через габаритні пристрої. Після кожного технологічного обороту вагонетку оглядають, змазують і, якщо потрібно, ремонтують.
Навколо печі повинен зберігатися постійний запас перевірених горілок (20% від встановлених на печі). Запас шамоту для піскових затворів повинен складати не менше добової потреби. Після кожного проштовхування вагонеток піскові затвори підсипають.
Температурний режим печі регулюють тільки з дозволу майстра. Затверджені параметри роботи печі змінюють лише за вказівкою головного інженера. На кожну зупинку печі з пропуском більше одного штовхання складають акт із докладним аналізом причин пропуску штовхання та вказівкою вжитих заходів щодо видалення несправностей і порядку введення печі в режим.
Для врахування роботи тунельної печі ведуть журнали ремонтів, завантаження та вивантаження із обліком номерів вагонів, часу завантаження, кількості й виду виробів на вагоні, часу проходження через позицію з максимальною температурою, кінцевої температури випалювання, простоїв і причин, які породжують їх; показання приладів фіксують щогодини. На кожен вагон ведеться маршрутний лист.
При експлуатації тунельних печей особливу увагу приділяють завантаженню і розвантаженню вагонеток, стійкості садки. Для того щоб садка виробів на вагонетці була стійкою, перевіряють вагонетки - вони повинні бути справними, з ходовою частиною, що вільно рухається, і рівним ходом. Температура виробів на вивантаженні не повинна перевищувати 50°С. Передавальні візки повинні бути обладнані сигналізацією. Усі частини вентиляторів, що рухаються, і штовхальників повинні бути огороджені.
Печі пускають відповідно до інструкції під керівництвом відповідального працівника, призначеного наказом по підприємству. Аеродинамічний режим роботи тунельних печей повинен бути відрегульований таким чином, щоб зони підігрівання і частково зона випалювання печі працювали під розрідженням.
У цеху, де встановлені тунельні печі, повинні бути вивішені схеми трубопроводів газу, пари, повітря і води з покажчиком номерів і місць розташування вентиляторів та засувок. Трубопроводи повинні мати розпізнавальний колір, попереджувальні знаки і маркування. Запірні пристрої усіх трубопроводів повинні бути розташовані осторонь від вогняних отворів, у місцях, зручних і безпечних для обслуговування. Вентилі й засувки повинні мати покажчики і написи "Відчинено", "Зачинено".
Перед розпалюванням пальників піч необхідно вентилювати протягом 10-15хв при включеному димососі й вентиляторі та продувати газопровід через продувну свічу до відсутності в газопроводі вибухонебезпечної газоповітряної суміші. Умикати газові пальники дозволяється тільки тоді, коли тиск газу на відводах до точок живлення знаходиться у встановлених межах. Регулювати продуктивність пальників можна тільки робочими кранами. Не допускається регулювати полум'я пальників контрольними кранами.
Пальники потрібно негайно вимикати у таких випадках: аварії в печі; аварії газопроводу; при зміні тиску газу понад встановленої межі; пожежі в цеху. При виявленні витоку газу з печі необхідно створити зворотний тиск шляхом повного підняття шиберів.
Зупиняють піч у такому порядку: припиняють подавання повітря; закривають газові крани перед палаючими пальниками та засувку на газовому вводі до печі; відкривають кран продувної лінії; через 5-7 хвилин після вимикання пальників від’єднують димосос до всіх нагнітаючих й відсмоктувальних вентиляторів. Приямки для вентиляційного устаткування, сходові марші для спуску обслуговуючого персоналу в підпічний коридор повинні мати освітлення, під´єднане до аварійної електромережі напругою не більше 12 В.
Роботи, пов'язані з ліквідацією завалів виробів у тунельній печі, розтаскуванням вагонеток, а також роботи, здійснювані в підподовому каналі печі, виконують тільки під керівництвом відповідального виконавця робіт. Чистити пальники, які труться об частини механізмів та інше, можна тільки при повній зупинці механізму та перекритті пальників.
До санітарних керамічних виробів (рис. 4.22) належать фаянсові, напівпорцелянові та порцелянові вмивальники, унітази, бачки, пісуари, біде, деталі керамічні для санітарно-технічних виробів і арматури, раковини лабораторні, мийки, ванни й інші вироби [55].
Керамічні умивальники (ГОСТ 30493-96, СТ СЕВ 3980-83) встановлюють у санітарних вузлах у побутових та інших приміщеннях будівель різного призначення, а також у залізничних вагонах, на морських і річкових судах. Умивальники виготовляють напівкруглої, овальної, прямокутної і трапецієподібної форми, зі спинкою або без спинки, кутові, на постаменті. Нові види умивальників мають у плані переважно овальну форму, передній борт виробу піднятий відносно його бічних сторін, борт має дуже випуклу поверхню, а поверхня, яка межує з чашею, навпаки, увігнута, вироби кріплять на болтах з опорою на суцільнолиті керамічні кронштейни.
Керамічні унітази (ГОСТ 30493-96, СТ СЕВ 3980-83) і напільні унітази встановлюють у санітарних вузлах будівель різного призначення. Унітази бувають тарілчасті, козиркові, з цільновідлитими або приставними поличками для приєднання змивних бачків, із прямими або косими випусками. Найбільш гігієнічними є унітази тарілчастого типу, проте вони більш трудомісткі при виготовленні.
Напільні унітази виготовляють із шамотованої маси, їх водопоглинення не перевищує 18%. Унітази забезпечують повне змивання й ополіскування чаші за одне промивання.
Змивні керамічні бачки (ГОСТ 21485-94, 21485.5-76) і бачки високорозташовані (ТУ 21-26-148-76) встановлюють у санітарних вузлах будівель різного призначення.
Змивні керамічні бачки виготовляють з верхнім та з боковим спуском. Виробництво високорозташованих бачків сьогодні скорочується внаслідок широкого впровадження змивних бачків з безпосереднім приєднанням до унітазів. Корпус і кришка бачків повинні мати глазуровану поверхню. У бачках з фаянсу та напівпорцеляни дозволяється не глазурувати зовнішню поверхню днища і верхню торцеву поверхню стінок корпуса, внутрішню поверхню бортика кришки по контуру, що стикається зі стінками корпусу бачка. У бачках з фарфору допускається також не глазурувати внутрішні поверхні корпусу та кришки.
Настінні керамічні пісуари (ДСТУ Б.В.2.7-55-96) і пісуари (уринали) напільні встановлюють у санітарних вузлах і побутових приміщеннях будівель різного призначення. Пісуари настінні виготовляють трьох типів: І - з цільновідлитим керамічним сифоном; ІІ - без цільновідлитого керамічного сифона; III - подовжені з цільновідлитим керамічним сифоном. Пісуари напільні (уринали) виготовляють із шматованої маси, покривають ангобом і білою глухою глазур'ю. Водопоглинення їх не перевищує 18%.
Біде керамічні - порцелянові й напівпорцелянові (ГОСТ 30493-96), встановлюють у санітарних вузлах будівель різного призначення.
Санітарні керамічні прилади і гарнітури з них (ТУ 21 -28-34-80) установлюють у санітарних вузлах будівель різного призначення, а також будівель підвищеної комфортності. Прилади, які входять до гарнітури, поставляє підприємство-виготовлювач комплектно.
До керамічних деталей для санітарно-технічних виробів і арматури (ГОСТ 30493-96) належать маховички вентильної голівки, вставки-покажчики до маховичків, ковпачок вентильної голівки, рукоятки душової сітки на гнучкому шлангу, рукоятки змішувача для ванн, рукоятки для спуску води із змивного бачка, рукоятки дверки топки водогрійної колонки. Керамічні деталі повинні мати гладку поверхню, покриту рівномірним шаром глазурі. Колір і білизна деталей повинні відповідати кольору і білизні санітарних керамічних виробів. На невидимих після монтажу або закритих арматурою поверхнях деталей відхилення за показниками зовнішнього вигляду не нормуються, якщо вони не перешкоджають монтажу й експлуатації виробів.
Лабораторні напівпорцелянові та порцелянові раковини (ГОСТ 30493-96) встановлюють у лабораторіях, у яких використовують кислоти і луги. Раковини повинні бути кислото- і лугостійкими.
Усі види санітарних керамічних виробів повинні відповідати вимогам та стандартам технічних умов на вироби, загальним технічним умовам на санітарні, керамічні вироби (ГОСТ 15167-93).
Рис. 4.22. Види деяких санітарних керамічних виробів:
Умивальники: а — напівкруглий; б — прямокутний; в — овальний на постаменті.
Пісуари: г — настінний; д — напільний (уринал); е — біде.
Унітази: ж — тарільчастий з косим випуском; з — у комплекті зі змивним бачком
Питання для повторення
1. Вироби з глини, що широко застосовуються у будівництві.
2. Кількість груп глин, які застосовуються при виробництві будівельної кераміки та їх призначення.
3. Необхідність застосування флюсу у виробництві керамічного черепка.
4. При сушінні керамічного сирцю відбувається велика усадка, Ваші дії?
5. Чому виникає необхідність застосування піску, шамоту, подрібнених шлаків і попелу у виробництві керамічних виробів?
6. Чим викликана необхідність при виробництві будівельних керамічних виробів уводити до суміші польові шпати, пегматити, нефелінові концентрати, перліти, склобій?
7. Яке значення має слово «глина»?
8. Скільки існує способів підготовки глини до виробництва керамічних будівельних виробів? Назвіть іх.
9. Методи підготовки глини до виробництва керамічних будівельних виробів.
10. Необхідність застосування глинорозпилювача.
11. Призначення ящикового підживлювача.
12. Операція, що проводиться дискозубчастою дробаркою.
13. Технологічна операція, у якій беруть участь каменеподібні валки.
14. Технологічна операція, що проводиться за допомогою стругача.
15. Операція, у якій беруть участь дезінтеграторні валки.
16. Операція, у якій беруть участь гладенькі валки.
17. Операція, у якій беруть участь дірчасті валки.
18. Технологічний процес, що відбувається у сушильному барабані.
19. Технологія підготовки глини до виробництва замісу.
20. Що таке корзинчасті інтегратори?
21. Призначення бігунів сухого помелу.
22. Яке значення має вологість глини перед формуванням виробів?
23. Як визначити нормальну вологість глини?
24. Який процент вологості глини є оптимальним?
25. Як впливає підвищення вологості глини на міцність свіжовідформованих виробів?
26. Як впливає зниження вологості глини на міцність свіжовідформованих виробів?
27. Технологічний процес заготовки глини для формування керамічних виробів.
28. Що таке пластичний спосіб виробництва глиняної цегли?
29. Що таке напівсухий спосіб виробництва глиняної цегли?
30. Які переваги або недоліки технології виготовлення напівсухого способу
виробництва глиняної цегли над пластичним способом виробництва глиняної цегли?
31. Яка необхідність у тунельній печі при виробництві керамічної глиняної цегли і послідовність проходження операції у тунельній печі?
32. Який цикл проходження вагонетки з цеглою-сирцем через тунельну піч до повного спікання і виходу готової цегли з печі?
33. Які розміри тунельної печі, тобто довжина і площа січення?
34. Технологія обпалювання цегли у тунельній печі, поопераційна послідовність.
35. Яка ставиться мета при виготовленні пустотілої цегли?
36. Призначення та мета камерної сушарки цегли-сирцю.
З7. Які вироби називають «санітарно-технічними»?
38. Мета і призначення санітарно-технічних виробів.
39. Технологічний процес виготовлення санітарно-технічних виробів.
40. Технологічний процес виготовлення санітарно-технічних виробів методом роздільного помелу.
41. Пристрій і призначення пропелерної мішалки у технологічному процесі виготовлення санітарно-технічних виробів.
42. Технологія стендового способу відливання санітарно-технічних виробів.
43. Технологічний процес виготовлення санітарно-технічних виробів методом гідростатичного пресування.
44. Процес сушіння санітарно-технічних виробів.
45. Технологія виробництва керамзиту.
46.Який пристрій пресового механізму називають мундштуком?
47. Що служить ножем пресового механізму і яка його роль?
5. Підприємства виробництва будівельного скла та будівельних скловиробів
Скломатеріал має комплекс різноманітних, не властивих іншим видам будівельних матеріалів властивостей, характерними з яких можна вважати пропускання світла і крихкість.
Властивості скла залежать від багатьох факторів: складу, режиму теплооброблення, стану поверхні, розмірів зразка та інше. Міцність скла на стискування досягає 700-1000 МПа, на розтягування - 30-80 МПа, міцність на розтягування скловолокна діаметром 1 - 4 см становить 200-500 МПа, тобто в 10 разів більше. На міцність скла впливають внутрішні дефекти, сторонні добавки (непровар, частки вогнетриву від футеровки печі та інше) та свиль (хімічно неоднорідні ділянки) [46].
Основним недоліком скла є крихкість, зумовлена рядом факторів. Основний із них - відношення модуля пружності матеріалу до міцності при розтягуванні Е/Rр; чим більше це відношення, тим при меншій деформації напруження в матеріалі досягається межі міцності. Модуль пружності скла становить 4,5*04 - 9,8*104 МПа.
Звичайне силікатне скло добре пропускає усю видиму частину спектра та практично не пропускає ультрафіолетові (довжина хвилі менше 300 ммк) й інфрачервоні (довжина хвилі більш 3000 ммк) промені. Змінюючи хімічний склад скла і його колір, можна регулювати світлопропускання скла в цих межах.
Показник заломлення будівельного скла (1,50-1,52) визначає силу відбитого світла та світлопропускання скла при різних кутах падіння світла. Так, при зміні кута падіння світла з 0 (перпендикулярно площині скла) до 75° світлопропускання скла зменшується з 92 до 50%. Світлозаломлення віконного скла дорівнює 1,5, а світлопропускання скла в залежності від довжини хвилі видимого спектра досягає 97%.
За оптичними властивостями розрізняють прозоре, пофарбоване, безбарвне і розсіююче світло скло.
Силікатне скло має високу стійкість до більшості агентів, за винятком плавикової і фосфорної кислот.
Віконне листове скло є найбільш поширеним видом плоского скла. Світлопропускання скла в залежності від товщини, яка становить 2-6 мм, дорівнює 85-90%. Вихідною сировиною для одержання будівельного листового скла служать кварцові піски, сульфат натрію або кальцинована сода, вапняк, доломіт, вугілля та деякі інші речовини. Виробництво будівельного скла (рис. 5.1) складається з таких основних операцій [46].
Рис. 5.1. Технологічна схема виробництва будівельного скла:
1 — сушильний барабан; 2 — циклон; 3 — вентилятор; 4 — елеватор; 5 — сито; 6 — бункер;
7 — транспортер; 5 — секційний бункер (склад сировини — крейда, вугілля, сода та ін.);
9 — дезінтегратор; 10 — бігуни; 11 — молоткова дробарка; 12 — щокова дробарка;
13 — вагонетка-ваги; 14 — змішування шихти; 15 — скловарна піч;
16 — машина для витягування скла
Підготовка складових матеріалів полягає в сушінні й очищенні піску від сторонніх домішок, подрібненні та сушінні крейди, доломіту й помелу вугілля. Складові матеріали дозують і перемішують. Підготовлена шихта розплавляється у спеціальних печах непереривної (ванні печі) чи періодичної (горшкові печі) дії. Варіння сировинної шихти відбувається при температурі 1100-1200°С до повного відділення всіх домішок, які збираються на поверхні у вигляді піни. У цей період відбувається і знебарвлення скла шляхом уведення спеціальних добавок, а також видалення пухирців повітря та газу. Потім з розплавленої маси, за допомогою машин вертикального чи горизонтального типу, витягують стрічку скла, яка проходить між валками машини, охолоджується і випалюється для зниження крихкості. На рис. 5.2 наведено безчовниковий спосіб витягування скла.
Рис. 5.2. Схема поперечного розрізу підмашинної камери
для безчовникового витягування скла:
1 - блок; 2 - шамотне тіло (поплавець); 3 - протисвильний міст; 4 - холодильник;
5 - машина ВВС; 6 - коробки для уловлювання битого скла
Листове скло можна одержати способом лиття з наступною прокаткою. Для цього скляну масу виливають на гладеньку поверхню та прокочують гладкими чи візерунковими валками.
Різновидом листового скла є орнаментне, одержуване способом лиття; це скло має один бік гладенький, а інший - тиснений, візерунковий.
Армоване скло одержують способом безперервного прокату з одночасним закочуванням усередину листа металевої сітки. Армоване скло може мати гладеньку, ковану чи візерункову поверхню, бути безбарвним або кольоровим. Воно має підвищену вогнестійкість (до 1,3 год). При його руйнуванні осколки втримуються армованою металевою сіткою. Світлопропускання скла складає не менше 60%. Армоване скло випускають довжиною 1200-2000 (±3) мм, шириною - 400-1500 (±3) мм і товщиною 5,5 (±0,7) мм. Межа міцності при стискуванні - 600 МПа, при вигинанні - 30-40 МПа. Армоване скло застосовують для скління ліхтарів верхнього освітлення, віконних плетінь, пристроїв перегородок, огородження балконів, сходових маршів та ін.
Установку армованого скла виконують на еластичних прокладках з морозостійкої гуми або на нетвердіючих мастиках.
Кольорове армоване скло має золотавий колір, одержують його шляхом нанесення окисометалевої плівки на поверхню безбарвного армованого скла. Застосовують таке скло для огороджень балконів, лоджій, сходів, ліфтових шахт, для пристрою декоративних світлопрозорих плафонів і перегородки в житлових будинках та санаторіях, пансіонатах, на підприємствах громадського харчування і торгівлі, а також в інших громадських і промислових будівлях. Максимальні розміри кольорового армованого скла 1000x1500 мм при товщині 7мм.
Захисне скло одержують спеціальним термічним обробленням (для підвищення міцності й пружності); призначене воно для скління автотранспорту.
Сонцезахисне та теплозахисне скло виготовляють на машинах вертикального витягування шляхом аерозольного оброблення поверхні скла спеціальними розчинами. Залежно від складу розчинів та умов оброблення, можна одержати скло з неоднаковим ступенем пропускання і відображення в різних частинах спектра. Сонцезахисне та теплозахисне скло застосовують для скління будівель і засобів транспорту з метою зменшення сонячної й теплової радіації. Розміри скла - 1600x2000 мм, товщина - 3-6 мм. Пропускання видимого світла - 30-70%, теплових променів - 40-60%.
"Вітрасил" - скло, яке має здатність розсіювати світло по всьому приміщенню. Воно не діє надто сліпучо, не викликає стомлювання людини. Це скло є також хорошим тепло- і звукоізолятором.
Теплопоглинальне скло, пофарбоване в масі, має у своєму складі спеціальні добавки, які забезпечують переважне поглинання інфрачервоних променів сонячного спектра. Теплопоглинальне листове скло має легке блакитне чи блакитнувато-зелене забарвлення, яке майже не спотворює предмет, що проглядається крізь нього. Воно призначене для заповнення віконних прорізів з метою зменшення сонячної радіації. Пропускна здатність видимого світла - не менше 65%, інфрачервоних променів - не більше 35%. Розміри скла до 1600x2000мм, товщина 3-4мм.
Скляна вата становить собою матеріал, що складається з тонких (5-6 мкм) гнучких ниток. Скляна вата має високу міцність на розрив, хімічну стійкість, низьку звуко- і теплопровідність. Скляну вату одержують способом механічного витягування, відцентровим та дуттєвим (газоструминним) способами.
При відцентровому способі одержання скловати сировиною служить скляний пляшковий бій, який миють і завантажують у спеціальний ківш, де він розплавляється, і при температурі 1300-1400°С скло стікає в чашу. Далі скляна маса тонким струменем направляється на диск що швидко обертається. Відцентровою силою розплавлена маса відривається від диска і витягується в тонкі нитки [20, 29].
При дуттєвому способі формування волокон відбувається шляхом роздування розплавленої скляної маси струменем газу (рис. 5.3).
Струмінь газу, виходячи з великою швидкістю, витягує скляну масу в тонкі волокна, які потім підхоплюються транспортером з тонкої сітки та подаються для наступного оброблення.
Скляну вату використовують як тепло- та звукоізоляційний матеріал у промисловості й будівництві. Вона еластична, стійка до температурних змін, хімічно стійка, не гниє і не горить. Скляну вату можна застосовувати як наповнювач (замість азбесту) при виготовленні азбоцементних виробів, а також як тонкий заповнювач для штукатурних і оздоблювальних розчинів. У суміші з полімерами одержують матеріал -склопластик.
Рис. 5.3. Схема виробництва скляної вати дуттєвим способом:
1 - канал для відсмоктування; 2 - транспортер з тонкої сітки; 3 - відвідний жолоб;
4 - відвідне парове сопло; 5 - платинова ванночка; 6 - фідер (краплинний живильник);
7 - плавильна піч
За кордоном (в Японії та інших країнах) скляну вату використовують для виготовлення антикорозійних скломатеріалів на фенольній смолі. Скломатеріали мають високі діелектричні властивості, стійкі проти корозії в агресивних хімічних середовищах. Скломатеріали випускають у вигляді рулонного матеріалу й використовують для ізоляції газових та водяних трубопроводів.
Піноскло і газоскло одержують шляхом спучування розплаву розмеленого скла, змішаного з речовиною (вапняком, вугіллям), яке при температурі 750-850°С здатне виділяти газ. Піноскло є чудовим тепло- і звукоізоляційним матеріалом, має малу щільність (150-750 кг/м3) і низький коефіцієнт теплопровідності (0,06-0,2Вт/м °С). Піноскло застосовують у народному господарстві як теплоізоляцію теплових і холодильних установок, звукоізоляцію громадських і комунально-побутових приміщень та ін.
Питання для повторення
1. Технологія виробництва будівельного скла.
2. Основні властивості віконного скла.
3. Компоненти для виробництва скла.
4. При якій температурі відбувається варіння скла?
5. Технологія виробництва армованого скла.
6. Технологія виробництва захисного скла.
7. Яку ще назву має захисне скло?
8. Якими властивостями володіє скло «Вітросил»?
9. Технологія виготовлення і застосування теплопоглинаючого скла.
10. Технологія виготовлення та мета застосування скляної вати.
11. Застосування скловати у будівництві.
12. Компоненти, які застосовуються для отримання піно- та газоскла.
Дата добавления: 2018-02-18; просмотров: 1633; Мы поможем в написании вашей работы! |
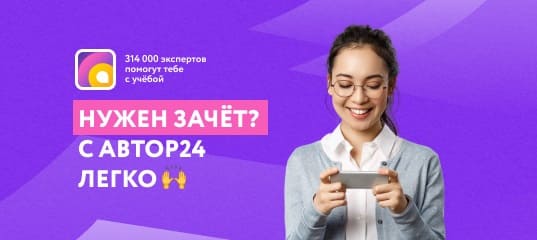
Мы поможем в написании ваших работ!