Элементы резания. Основные понятия и определения
Методы обработки деталей машин
Обработка металлов и других конструкционных материалов применяется для придания исходным материалам (заготовкам) требуемой геометрической формы и размеров, а также необходимой точности и чистоты поверхностей получаемых деталей.
Все методы обработки различаются видом и способом использования энергии воздействия на заготовку (рисунок 6.1).
При обработке используются следующие виды энергии:
- механическая (обработка резанием и обработка деформированием);
- химическая – снятие припуска за счет химического растворения материала заготовки;
- электрическая – электрофизический метод;
- электромагнитная – воздействие на заготовку электромагнитным полем;
- светолучевая – использование оптических квантовых генераторов и других источников световой энергии;
- ультразвуковая – разрушение материала воздействием ультразвука;
- плазменная энергия – воздействие на поверхность заготовки плазменными горелками.
К механическим методам относятся.
- обработка резанием (со снятием стружки);
- пластическое деформирование (без снятия стружки);
- слесарная обработка (ручная).
Ручным способом выполняют разрезание, опиливание, притирку, шабрение.
Рисунок 6.1 – Классификация методов обработки
Обработка резанием разделяется по видам используемого оборудования и обрабатываемой поверхности:
- точение (обработка тел вращения);
- сверление (обработка внутренней поверхности вращения на станках сверлильной группы);
- обработка плоских поверхностей (фрезерование, строгание, долбление);
- протягивание поверхности на станках протяжной группы;
- шлифование поверхности на станках шлифованной группы круглошлифовальных (наружная поверхность вращения), внутришлифовальных (обработка отверстий), плоскошлифовальных (обработка плоскостей), бесцентровошлифовальных (обработка поверхностей вращения);
- отделочные методы обработки (финишные методы): притирка, доводка, шлифование, полировка, хонингование.
Из рассмотренных методов наибольшее распространение получили методы обработки резанием. Они являются универсальными и позволяют получать высококачественную и точную поверхность.
|
|
Более прогрессивным является обработка давлением, но этот метод требует больших энергозатрат, не позволяет получить высокую точность. Эти методы изучаются в курсе «Обработка металлов давлением».
Электрофизические, химические и лучевые методы позволяют получить высококачественную и точную поверхность. они используются при обработке заготовок из высокопрочных и твердых материалов таких как высокопрочные и закаленные стали, твердые сплавы, керамика, алмаз и алмазоподобные материалы.
|
|
Вопросы для самоконтроля
- Назовите основные виды энергий, используемых для обработки материалов.
- Назовите виды механических методов обработки.
- Перечислите электрофизические и электрохимические методы обработки.
- Назовите виды обработки материалов пластическим деформированием.
- Назовите виды обработки материалов резанием.
- Назовите комбинированные методы обработки материалов.
Резание как технологический способ обработки
Сущность процесса резания
Сущность технологии изготовления деталей машин состоит в последовательном использовании различных методов воздействия на заготовку с целью придания ей требуемой формы, качества поверхности и точности размеров. Одним из таких способов является обработка резанием. Этот вид обработки осуществляется режущими инструментами и выполняется на металлорежущих станках. Обработка резанием заключается в срезании с поверхности заготовки некоторой массы материала специально оставленной для обработки (припуска).
Припуск может удаляться с одной поверхности либо одновременно с нескольких поверхностей или последовательно с нескольких поверхностей одними или несколькими инструментами. После удаления всего припуска заготовка превращается в готовую деталь. Материал, удаляемый с поверхности заготовки, подвергается пластической деформации с последующим разрушением.
|
|
В результате этого удаляемый материал приобретает особую характерную форму и в таком виде называется стружкой.
Таким образом, характерным признаком обработки резанием является образование стружки. Поэтому все виды и методы обработки, основанные на срезании припуска и превращении его в стружку, составляют группу методов объединенных термином «обработка резанием».
![]() | Образование стружки |
Все виды резания подчиняются одним и тем же закономерностям.
По сравнительной обрабатываемости резанием, энергоемкости образования новых поверхностей на заготовке все конструкционные материалы делятся на следующие группы:
- легкообрабатываемые (латунь, бронза, мягкий чугун);
- средней обрабатываемости (углеродистые и низколегированные стали, силумины, чугун средней твердости);
- ниже средней обрабатываемости (высоколегированные стали мартенситного, аустенитно-мартенситного и мартенситно-ферритного классов, твердый чугун);
- труднообрабатываемые (высоколегированные стали аустенитного класса, жаро- и кислотостойкие стали на никелевой основе, тугоплавкие сплавы).
Стальной прокат поставляется в отожженном в состоянии. Поэтому для получения требуемых механических характеристик готовых деталей они подвергаются термообработке, после которой твердость и прочность материала значительно возрастают (в среднем на 40%). Применение термообработки приводит к изменению обрабатываемости материала. Поэтому эти показатели (твердость и предел прочности) используются как режимные показатели, выражающие качественно и количественно влияние механических свойств на уровень режимов их обработки резанием.
|
|
Выпускаемый промышленностью прокат в виде прутков, полос, лент, листов, уголков и т.п. разделяется в заготовительных цехах на мерные куски (заготовки). Часть этих заготовок поступает непосредственно в механические цеха для дальнейшей обработки. Другая часть в кузнечно-прессовых цехах перерабатывается в поковки и штамповки, которые по форме более близки к форме готовых деталей.
Продукция заготовительных производств (кузнечно-прессовых, литейных, сварочных, термических, холодно-штамповочных и др.) предназначенная для последующей механической обработки с целью изготовления из них необходимых деталей, называют заготовками.
Вопросы для самоконтроля
- В чем состоит сущность технологии изготовления деталей машин?
- Что такое стружка?
- Основной признак метода обработки резанием.
- Дать развернутую характеристику понятия «обработка резанием».
- Как разделяются все конструкционные материалы по обрабатываемости?
Элементы резания. Основные понятия и определения
Заготовка имеет исходные поверхности. В процессе обработки резанием с заготовки слой за слоем срезается припуск.
Поверхности на заготовке, срезаемые за каждый рабочий ход обрабатываемыми поверхностями (рисунок 6.2).
![]() |
Рисунок 6.2 – Поверхности обрабатываемой заготовки а – при точении; б – при строгании |
Поверхности на заготовке, вновь образуемые во время рабочего хода инструмента, называются обработанными поверхностями.
Промежуточная поверхность, временно существующая в процессе резания между обработанной и обрабатываемой поверхностями, называется поверхностью резания.
Чтобы срезать слой материала, оставленный на припуск, лезвие режущего инструмента должно проникнуть в глубь материала на величину равную припуску, в этом случае весь припуск снимается за одни рабочий ход. Если припуск велик, то он может сниматься за несколько рабочих ходов.
Глубина проникновения лезвия инструмента в материал заготовки за один рабочий ход называется глубиной резания «обозначается буквой », то есть иначе глубина резания – это расстояние между обрабатываемой и обработанной поверхностями заготовки.
Для удаления припуска необходимо непрерывное взаимное перемещение лезвия инструмента и заготовки (подача). Эти движения задаются механизмами станка в соответствии с настройкой их кинематических цепей. Движения подачи могут быть заданы и заготовке и инструменту и выполняться либо одновременно, либо одному из этих элементов, либо попеременно, то одному, то другому.
Движение, осуществляемое с наибольшей скоростью, называется главным движением (рисунок 6.2). Поступательное или вращательное движение других органов, осуществляемое с меньшей скоростью, называется движением подачи. Движение подачи необходимо для обеспечения непрерывности процесса врезания лезвия инструмента в материал заготовки и отделения срезаемого слоя в виде стружки.
При осуществлении главного движения и движения подачи необходима их оценка (определение величины). Главное движение определяет скорость деформации и разрушения материала. поэтому скорость главного движения называется скоростью резания.
Скорость резания может сообщаться либо заготовке (станки токарного типа), либо инструменту (фрезерные, сверлильные, шлифовальные станки). Скорость резания обозначается буквой v и имеет размерность в м/мин. Для вращательного движения
, м/мин,
где – диаметр обрабатываемой поверхности, мм;
– частота вращения заготовки (или инструмента), об/мин.
Подача обозначается буквой . Количественно подача оценивается по расстоянию, проходимому режущим инструментом в направлении движения подачи за соответствующее число циклов главного движения (обычно за один оборот заготовки или режущего инструмента). В настоящее время используются следующие виды подач:
– величина перемещения режущего инструмента за время одного оборота заготовки (для токарных станков), мм/об;
– подача на зуб – величина перемещения заготовки за время поворота инструмента на один зуб (для фрезерных станков), мм/зуб;
– минутная подача (для станков с ЧПУ), мм/мин;
– подача на двойной ход (на станках с прерывистым характером процесса резания (строгальные и долбежные станки), мм/дв.ход.
Вопросы для самоконтроля
- Поясните сущность понятий «обрабатываемая поверхность», «обработанная поверхность», «поверхность резания».
- Что такое «глубина резания»?
- Какие движения задаются режущему инструменту и заготовке при обработке резанием?
- Какое движение называется «главным движением»?
- Какое движение называется движением подачи?
- Поясните понятие «скорость резания». Как определяется скорость резания?
- Назовите основные виды подач. Как они взаимосвязаны?
Сечение срезаемого слоя
Сечение срезаемого слоя определяют микрогеометрию обработанной поверхности и энергозатраты на обработку.
Форма и размеры сечения срезаемого слоя зависят от кинематики процесса формообразования обрабатываемой поверхности.
На рисунке 6.3 показано произвольное положение режущих кромок резца с главным углом в плане и вспомогательным углом в плане
при срезании слоя металла глубиной
. Положение резца через один оборот заготовки показано пунктиром.
Размеры поперечного сечения срезаемого слоя измеряются в плоскости, проходящей через ось вращения заготовки.
Формообразование поверхности при продольном точении осуществляется за счет двух движений: вращения заготовки и прямолинейного перемещения резца параллельно оси заготовки. При этом вершина резца описывает в пространстве винтовую линию и на поверхности заготовки режущими лезвиями резца формируется винтовая поверхность.
При этом с поверхности заготовки срезается слой 1–2–4–5–-1 вместо теоретически расчетного (или номинального) 1–2–4–3–-1. Таким образом, часть материала в сечении 1–5–3–1 остается не удаленным, образуя шероховатость поверхности с гребешками высотой . Площадь остаточного сечения
относительно мала и не превышает 1% от площади номинального сечения, поэтому в расчетах принимают
.
![]() | ![]() |
Высота микронеровностей зависит от
. В свою очередь величина
зависит от углов
и
, а также от величины подачи
. На рисунке 6.4 изображен участок 1–5–3–1 остаточного сечения. Точка 1 обозначена буквой А, точка 3 – буквой В, точка 5 – буквой С. Найдем высоту неровностей
.
Из точки С опустим перпендикуляр на сторону АВ. Тогда из треугольника ADC имеем
.
Из треугольника DBC
.
Откуда .
Но
.
Тогда
.
Откуда
.
Решая это уравнение относительно , и учитывая, что
, получим
.
Энергозатраты на процесс резания определяются площадью сечения срезаемого слоя 1–2–4–3–1 поскольку сопротивление материала пластическому деформированию и образование стружки определяется размерными параметрами срезаемого слоя (толщиной и шириной).
Толщиной срезаемого слоя называется расстояние между двумя последовательными за один оборот заготовки положениями главной режущей кромки.
Ширина срезаемого слоя – это длина стороны сечения срезаемого слоя вдоль главной режущей кромки или иначе это расстояние между обрабатываемой и обработанной поверхностями, измеренное вдоль поверхности резания.
На рисунке 6.5 показан срезаемый слой в увеличенном масштабе.
![]() |
Из рисунка следует
,
.
Площадь срезаемого слоя
Таким образом, площадь срезаемого слоя равна произведению подачи на глубину резания . То есть площадь поперечного сечения срезаемого слоя является функцией подачи
и глубины резания
.
Вопросы для самоконтроля
- На какие параметры процесса резания влияет толщина срезаемого слоя материала?
- Вывести зависимость высоты микронеровностей обработанной поверхности от основных геометрических параметров режущего инструмента.
- Как определяются ширина и толщина срезаемого слоя?
Износ инструмента
В процессе резания передняя и задняя поверхности лезвия инструмента подвержены переменному давлению и находятся в состоянии подвижного контакта (трения) с обрабатываемым материалом. При этом передняя поверхность контактирует со стружкой, а задняя с воспроизводимой поверхностью резания.
Следовательно, по этим поверхностям будет происходить износ режущего лезвия. Наибольшее давление стружка оказывает на переднюю поверхность на некотором удалении от вершины резца, поэтому максимальный износ по передней поверхности будет наблюдаться также на некотором расстоянии (рисунок 6.6). Износ наблюдается в форме лунки (лунка износа). Величина износа оценивается по глубине и ширине
лунки. Наличие лунки износа ослабляет режущее лезвие, при этом изменяется геометрия передней поверхности. Это может привести к поломке лезвия.
![]() |
Износ по задней поверхности происходит в виде появления фаски размером . Износ задней поверхности изменяет геометрию задней поверхности и приводит к увеличению сил резания.
Трение стружки о переднюю поверхность и задней поверхности резца о поверхность резания приводит к выделению большого количества тепла и разогреву области резания, что снижает режущие свойства резца. Кроме того, износ по задней грани изменяет положение режущей кромки, а, следовательно, и вершины резца, что вызывает погрешность в обработке.
Наиболее важным для работоспособности инструмента является износ по задней грани. Кривая износа имеет вид, показанный на рисунке 6.7.
Кривые износа строятся в координатах , где
– время работы инструмента. Кривая износа имеет три явно выраженных участка:
![]() |
участок I – период интенсивного износа, то есть период приработки. В этот период изнашивается поверхностный слой, получивший структурные повреждения при заточке инструмента;
участок II – установившийся период износа;
участок III – период катастрофического износа. В этот период сильно возрастают силы трения, повышается температура в зоне резания и связанные с этим структурные изменения в приграничных слоях. Дальнейшая работа инструмента недопустима.
Интенсивность износа зависит не только от продолжительности резания, но также и от других факторов: скорости резания
, подачи
, главного заднего угла
, физико-механических свойств материалов инструмента и заготовки и др. Для конкретных условий может быть построена своя кривая износа. Например, для разных скоростей резания
Точки 1,4 и 5 соответствуют моменту времени, когда инструмент полностью выработает свой ресурс. Соединив эти точки, получим кривую оптимального износа, кривые износа будут иметь вид, показанный на рисунке 6.8. которая может быть использована для выбора момента смены инструмента при заданной скорости резания. Этот критерий иногда целесообразно использовать при обработке на станках с числовым программным управлением (ЧПУ), на автоматических линиях.
![]() |
Однако на практике использование этой зависимости для управления процессом смены инструмента весьма затруднительно, а зачастую и неэкономично, особенно когда обработка ведется несколькими инструментами.
По техническим и экономическим показателям приходится ограничивать предельно допустимую величину максимально износа . Например, если технологическая операция выполняется несколькими инструментами, то максимально допустимый износ удобнее задать одинаковым
для всех инструментов, как предельно допустимый для наиболее нагруженного инструмента. Это критерий равного износа (рисунок 6.8, точки 1,2,3). Но тогда время работы каждого инструмента до достижения
будет разным
. Следовательно, при такой методике управления процессом смены инструмента, инструменты не вырабатывают свой ресурс, что может оказаться неэкономичным.
Максимально допустимый износ определяет максимально допустимое время работы инструмента при заданных режимах обработки, Это время называется стойкостью режущего инструмента. Таким образом, стойкость инструмента это регламентированное время его непрерывной работы, когда максимальный износ лезвия достигает допустимого значения, по истечении которого он должен быть заменен. Стойкость инструмента задается при выборе режимов резания и приводится в справочниках по выбору режимов.
Вопросы для самоконтроля
- Чем вызывается износ рабочих поверхностей режущего инструмента?
- Какими физическими явлениями сопровождается износ рабочих поверхностей режущего инструмента?
- Как оценивается величина износа?
- Нарисуйте график зависимости износа от времени работы инструмента. Дайте его характеристику.
- Как влияет на износ скорость резания?
- Как определяется линия оптимального износа? При решении каких задач используется эта зависимость?
- Как назначается предельно допустимая величина износа при многоинструментной обработке?
- Поясните термин «стойкость режущего инструмента». Как назначается стойкость инструмента?
Режимы резания
Под термином режимы резания понимают совокупность численных значений глубины резания , подачи
, скорости резания
, геометрических параметров режущего инструмента
, стойкости инструмента
, а также силы резания, эффективной мощности резания
и других параметров рабочего процесса, от которых зависят его технико-экономические показатели.
Силы резания определяют энергетические затраты на обработку. Режимы резания будут оптимальными, если они позволяют получить высокие технико-экономические показатели. Режимные параметры взаимосвязаны, и поэтому нельзя произвольно изменять хотя бы один параметр. При выборе параметров необходимо производить согласование их значений с учетом возможностей их реализации на используемом оборудовании.
Режимы обработки определяются либо по экспериментальным зависимостям, либо по статистическим данным, приведенным в справочниках по обработке материалов резанием.
Предварительный выбор режимов проводится в следующей последовательности.
Сначала определяют глубину резания. Она связана с величиной припуска. при черновой обработке следует назначать возможно большую глубину резания, соответствующую припуску на обработку. Количество проходов свыше одного при черновой обработке допускается в исключительных случаях, при снятии повышенных припусков и обработке на маломощных станках. Величина припуска для обработки поверхности детали может быть назначена на основе расчета аналитическим методом или определена по соответствующим справочным таблицам.
Обычно глубина резания при черновом обтачивании находится в пределах 4…8 мм и не превышает10 мм. Получистовая обработка часто производится в 2 прохода.
Первый, черновой проход осуществляется с глубиной резания =0,6…0,75 припуска, а второй, окончательный при
= 0,3…0,25 припуска.
Глубина резания при получистовой обработке принимается в пределах =1...4 мм.
При шероховатости поверхности обработанной детали глубина резания назначается
= 0,5…2,0 мм; при
=0,1…0,4 мм, а если
, то
< 0,1 мм [6].
Количество проходов при чистовой обработке зависит от требуемого качества и точности поверхности, жесткости системы станок-приспособление-инструмент-деталь (СПИД) и погрешности предшествующей обработки.
Значение подачи определяется видом выполняемой операции, а также требуемым качеством обработки поверхности.
На финишных операциях подача не превышает величины S= 0,1 мм/об – на чистовых S=0,1…0,04 мм/об. При черновой обработке подача ограничивается мощностью привода подач станка.
Скорость резания определяется по экспериментальной формуле:
,
где – постоянный коэффициент зависящий от вида обработки;
Т – период стойкости инструмента; НВ – твердость материала заготовки по Бринелю;
К – поправочный коэффициент, учитывающий реальные условия обработки;
– показатели степеней.
Твердость заготовки НВ устанавливается по технической документации на деталь.
Стойкость режущего инструмента Т – назначается по рекомендациям из справочника в зависимости от характера выполняемой операции, материалов режущей части инструмента и заготовки.
Скорость резания может быть также назначена по нормативам из справочника.
По найденной скорости резания определяют частоту вращения заготовки
,
где – диаметр обрабатываемой поверхности.
Расчетное значение частоты вращения заготовки уточняют по паспортным данным станка.
Стойкость инструмента может быть назначена по справочнику либо вычислена по экспериментальной формуле:
.
Сила резания определяется по экспериментальной формуле:
.
Для удобства расчетов результирующую силу резания PP рассматривают в пространственной декартовой системе координат XYZ. Приняты следующие принципы ориентации координатной системы. Начало системы координат совмещают с вершиной резца, установленной на высоте оси вращения заготовки. Ось X располагается горизонтально и параллельно оси вращения заготовки; ось Y горизонтальна и перпендикулярна оси вращения заготовки; ось Z вертикальна и направлена вниз.
![]() |
Проекция силы PP на ось X (рисунок 6.9) называется осевой составляющей PX силы резания. Эта составляющая равна сопротивлению обрабатываемого материала врезанию резца в направлении подачи S и действующих в этом направлении сил трения.
Проекция силы PP на ось Y называется радиальной составляющей PY силы резания. Она вызывает изгиб обрабатываемой заготовки в горизонтальной плоскости, что служит причиной снижения точности обработки заготовок, а также вызывает нежелательные вибрации технологической системы.
Проекция силы PP на ось Z называется вертикальной (главной) составляющей силы резания.
Мощность, непосредственно затрачиваемая на осуществление процесса резания, называетсяэффективной мощностью резанияи обозначаются Ne. Если при резании направления действующей силы резания и скорости резания
совпадают, то
.
Учитывая, что к.п.д. кинематических цепей станка h<1, мощность электродвигателя привода станка может быть определена по формуле
.
Для того чтобы на заданном станке можно было осуществлять процесс резания, необходимо, чтобы мощность электродвигателя станка NСТ была больше расчетной эффективной мощности резания, то есть
.
Вопросы для самоконтроля
Дата добавления: 2018-02-15; просмотров: 2686; Мы поможем в написании вашей работы! |
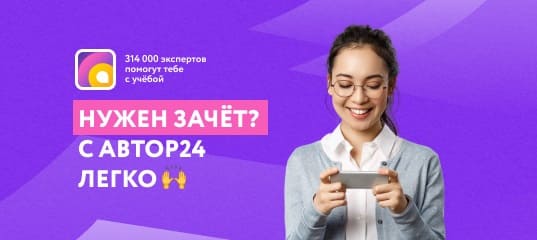
Мы поможем в написании ваших работ!