Обработка внутренних цилиндрических поверхностей (отверстий )
По форме отверстия разделяются на:
- цилиндрические;
- ступенчатые;
- конические;
- фасонные (рисунок 6.29).
По расположению отверстия могут быть: сквозными и глухими.
К отверстиям предъявляются следующие требования:
- точность диаметрального размера;
- качество поверхности;
- круглость;
- цилиндричность;
- соосность ступеней.
![]() | Рисунок 6.29 – Типы отверстий а) сквозное цилиндрическое; б) ступенчатое; в) коническое; г) фасонное; д) глухое |
Для обработки отверстий используют методы со снятием и без снятия стружки:
- лезвийным и абразивным инструментами;
- пробивкой в штампах;
- калиброванием и раскатыванием;
- плазменной резкой;
- электрохимическим и электроэрозионным методами;
- лучевыми и ультразвуковыми методами.
Обработка отверстий лезвийным инструментом
Образование отверстий в сплошном материале осуществляется сверлением. Точность диаметрального размера отверстия после сверления не превышает 12…13-го квалитета при качестве поверхности Rz=40…80 мкм. Для повышения точности размеров и качества поверхности используются зенкерование, развертывание, растачивание, протягивание, шлифование, хонингование и доводка.
При обработке отверстия без снятия стружки применяются:
- пробивка отверстий в штампах;
- выглаживание поверхности отверстия закаленными шариками;
- раскатывание отверстий роликами и шариками.
Для получения отверстий в деталях изготовляемых из высокопрочных материалов используются электрофизические, электрохимические плазменные и лучевые методы обработки.
|
|
Для уменьшения силы резания отверстия диаметром более 30 мм сверлят в два приема диаметром 15…20 мм, а затем рассверливают или растачивают до нужного диаметра.
Отверстия диаметром 15…20 мм с точностью 10…11 квалитет обрабатываются после сверления зенкером, а для получения точности 8…9 квалитета – отверстия после зенкерования обрабатываются развертками. Отверстия с диаметром более 30 мм с точностью 10…12 квалитет получают сверлением и зенкерованием.
На рисунке 6.30 показана обработка отверстий в сплошном материале.
![]() | Рисунок 6.30 – обработка отверстий в сплошном материале а – сверление отверстия 12-го квалитета точности; б – обработка отверстия 7-го квалитета точности: 1 – сверление; 2 – зенкерование; 3 – черновое развертывание; 4 – чистовое развертывание |
Для повышения точности расположения оси отверстия, применяют обработку зенкерами с направляющими хвостовиками (рисунок 6.31). В этом случае хвостовик 3 перед началом резания входит в кондукторную втулку 4 и тем самым фиксируется положение оси зенкера.
В крупносерийном и массовом производствах для обработки отверстий, расположенных на одной оси, используются насадные зенкеры.
|
|
Для обработки фасок в отверстиях используют зенковки (рисунок 6.32,а). Цилиндрические углубления и торцовые поверхности отверстий обрабатываются цековками (рисунок 6.32,б).
В крупносерийном и массовом производствах применяются комбинированные зенкеры – цельные (рисунок 6.33,а) и со вставными ножами (рисунок 6.33,б,в), обрабатывающие одновременно отверстия, торец и фаску. Направление таким зенкерам дается либо верхнее (рисунок 6.33,б), либо нижнее (рисунок 6.33,в).
| ![]() |
Рисунок 6.32 – Обработка фасок зенковками (а), углублений (б) и торцов (в) цековками отверстий | |
![]() | |
1 – обрабатываемое отверстие; 2 – зенкер; 3 – направляющий хвостовик; 4 – кондукторная втулка Рисунок 6.31– Обработка отверстия зенкером с направляющим хвостовиком | Рисунок 6.33 – Обработка отверстий комбинированными зенкерами |
Точные отверстия диаметром 35 мм и выше обрабатываются растачиванием на расточных станках (рисунок 6.34).
![]() |
Рисунок 6.34 - Обработка отверстий на горизонтально-расточном станке |
В крупносерийном и массовом производствах используют комбинированные инструменты для обработки отверстий сверло-развертка или сверло-зенкер-развертка.
|
|
Основное время обработки отверстий лезвийными инструментами определяется по формуле:
,
где – расчетная длина обработки (рисунок 6.35);
– длина обрабатываемого отверстия по чертежу;
– длина врезания;
– длина перебега.
![]() |
Рисунок 6.35 – Схема для определения расчетной длины хода инструмента |
Длина врезания при сверлении
,
где – диаметр сверла;
– длина перемычки сверла;
– главный угол в плане сверла;
1…3 – поправка на безударный подход сверла.
При развертывании, рассверливании и зенкеровании длина врезания будет
,
где – глубина резания.
Длина перебега принимается равной 0,5…3 мм.
Обработка точных конических отверстий (рисунок 6.36) осуществляется комплектом инструментов: сначала сверлом (переход 1), потом коническим зенкером (переход 2), после чего нужная точность достигается обработкой комплектом конических разверток
(переходы 3,4).
![]() |
Рисунок 6.36 – Обработка конических отверстий |
В крупносерийном и массовом производствах обработка отверстий ведется на многошпиндельных станках.
Финишная обработка отверстий
Высокая точность размера и качество поверхности достигается применением финишной обработки.
|
|
Финишная обработка отверстий ведется следующими методами:
- тонким растачиванием;
- протягиванием;
- шлифованием;
- хонингованием;
- притиркой;
- пластическим деформированием.
Тонкое растачивание – выполняют на станках токарного типа повышенной точности и на расточных станках (рисунок 6.37). Сущность обработки заключается в том, что обработка ведется на больших скоростях резания. Так, чугун обрабатывается на скоростях 120…150 м/мин, бронза 300…400 м/мин, алюминиевые сплавы 500…1500 м/мин, сталь 100…150 м/мин.
Глубина резания при тонком точении принимается равной t=0,05…0,1 мм., подача S=0,01…0,08 мм/об.
Основным достоинством растачивания является – высокая точность 5,6 квалитет при качестве поверхности Rа=0,01…0,32 мкм.
![]() | 1 – заготовка; 2 – расточной кондуктор; 3 – рабочий стол; 4 – кондукторные втулки; 5 – борштанга Рисунок 6.37 – Обработка отверстий в корпусных деталях на расточном станке |
Поверхность, полученная после растачивания, не имеет посторонних включений.
Протягивание применяется в крупносерийном и массовом производствах для получения цилиндрических и шлицевых отверстий.
Ззаготовка для протягивания устанавливается на жесткой или шаровой опоре. Установку на жесткой опоре применяют, если опорный торец заготовки предварительно подрезан перпендикулярно оси отверстия. Если торец не подрезан (черновая база), то заготовка устанавливается на шаровой опоре (рисунок 6.38).
![]() | 1 – пружина; 2 – опорная шайба; 3 – шаровая опора; 4 – обрабатываемая заготовка; 5 – протяжка Рисунок 6.38 – Обработка отверстия протягиванием |
Цилиндрические отверстия протягиваются после сверления или зенкерования. Точность полученных отверстий 7…8 квалитет, при качестве поверхности Rа=0,32…3,2 мкм.
Обработка ведется на специальных протяжных станках при скорости резания 1,5…15 м/мин.
Основное время обработки протягиванием определяется по формуле
,
где – длина рабочей части протяжки, мм;
– длина протягиваемой поверхности, мм;
– скорость резания, м/мин;
– скорость обратного хода, м/мин.
Шлифование отверстий выполняют на внутришлифовальных станках по следующим схемам:
- при вращении детали закрепленной в патроне станка;
- при неподвижной детали – на станках с планетарным движением шпинделя;
- бесцентровое шлифование.
Внутреннее шлифование. Схема обработки отверстия на внутришлифовальном станке показана на рисунке 6.39. Обрабатываемая деталь 1 закрепляется в патроне станка и приводится во вращение с окружной скоростью . Шлифовальный круг 2, вращающийся со скоростью резания , совершает возвратно-поступательное движение со скоростью продольной подачи
и поперечное перемещение за каждый двойной продольный ход на величину
. Направления вращения детали и шлифовального круга должны быть противоположными. Диаметр шлифовального круга принимают равным 0,8…0,9 диаметра отверстия.
![]() |
Основное время шлифования с продольной подачей круга определяется по формуле
,
где – припуск на сторону;
– коэффициент, учитывающий точность обработки (поправка на выхаживание);
– число двойных ходов стола в минуту;
– поперечная подача на один двойной ход стола.
,
где – скорость продольного хода стола, м/мин.
,
где – продольная подача за один оборот детали (выражается в долях от ширины круга);
– частота вращения детали;
– расчетная длина хода стола
– при шлифовании на проход;
– при шлифовании в упор;
– длина шлифуемой поверхности.
Планетарное шлифование. На рисунке 6.40 показано шлифование при неподвижной детали на станке с планетарным движением шлифовального круга.
![]() |
Шпиндель с шлифовальным кругом 1 имеет четыре движения:
I – вращение вокруг своей оси (движение резания);
II – планетарное движение по окружности внутренней поверхности заготовки (круговая подача);
III – возвратно-поступательное движение вдоль оси заготовки (продольная подача);
IV – поперечное перемещение (поперечная подача).
Станки с планетарным движением шлифовального круга имеют низкую производительность, поэтому они применяются только для обработки отверстий в крупных деталях.
Бесцентровое шлифование. При бесцентровом шлифовании заготовка не закрепляется, а свободно укладывается на опорный нож или на опорный ролик. Деталь, предварительно прошлифованная по наружному диаметру, направляется и поддерживается тремя роликами (рисунок 6.41). Ролик 1 большого диаметра является ведущим. Он вращает деталь 2 со скоростью . Ролик 4 является опорным. Прижимной ролик 5 прижимает деталь 2 к ведущему 1 и опорному 4 роликам. Шлифование осуществляется шлифовальным кругом 3, вращающимся со скоростью резания
.
![]() | 1 – ведущий ролик; 2 – обрабатываемая деталь; 3 – шлифовальный круг; 4 – опорный ролик; 5 – зажимной ролик; Рисунок 6.41 – Схема бесцентрового шлифования отверстия |
Бесцентровое шлифование позволяет получить высокую точность диаметрального размера и высокую точность по концентричности внутренней и наружной поверхностей шлифуемой детали. Способ применим для обработки деталей диаметром
Хонингование – выполняют на специальных станках, но может выполняться и на сверлильных станках. Сущность хонингования заключается в доводке предварительно развернутого, расшлифованного или расточенного отверстия специальным инструментом – хоном. Режущим элементом хона является мелкозернистые абразивные бруски установленные в пазах хонинговальной головки. Бруски постоянно прижимаются к обрабатываемой поверхности механическими, гидравлическими или пневматическими устройствами. Хон вращается со скоростью 60…75 м/мин при обработке чугуна или 45…60 м/мин при обработке стали, и совершает возвратно-поступательные движения вдоль оси отверстия со скоростью 12…15 м/мин. Операция выполняется с применением СОЖ, в качестве которой используется керосин.
Припуск на хонингование 0,05…0,1 мм.
Хонингование обеспечивает точность обработки по 5…6 квалитету, при качестве поверхности Rа=0,06…0,25 мкм. используются е бруски, операция выполняется с использованием в качестве смазочной охлаждающей жидкости керосин.
Преимущества хонингования по сравнению с шлифованием:
- высокая цилиндричность отверстия;
- отсутствие вибраций при обработке;
- плавность хода хонинговальной головки.
На рисунке 6.42,а представлена конструкция хонинговальной головки с механическим раздвижением абразивных брусков, а на рисунке 6.42,б – схема для определения расчетной длины перемещения.
![]() |
Основное время обработки для хонинг-процесса определяется по формуле
,
где – припуск на сторону, мм;
– радиальная подача на один двойной ход хонинговальной головки, мм;
– число двойных ходов хонинговальной головки в минуту
,
где – скорость возвратно-поступательного движения головки, м/мин;
– расчетный ход хонинговальной головки.
где – длина обрабатываемого отверстия;
– перебег головки;
– длина абразивного бруска.
Притирка – выполняется специальным инструментом притиром, выполненным из чугуна или меди. на поверхность притира наносится абразивная паста. Операция выполняется с применением СОЖ (керосина). Притир совершает вращательные движения на пол оборота попеременно в обе стороны и возвратно-поступательные движения вдоль оси обрабатываемого отверстия.
В качестве СОЖ используется керосин.
Притирка позволяет получать точность отверстия по 4…5 квалитету точности при шероховатости поверхности Rz=0,03…0,05 мкм и точности формы 1…2 мкм.
Притирка – процесс малопроизводительный и поэтому используется сравнительно редко.
Обработка отверстий пластическим деформированием. Метод применяется для получения высокого качества поверхности отверстий в пластичных материалах. Обработка заключается в проталкивании через отверстие дорнов, прошивок или закаленных шариков, а также в раскатывании отверстия закаленными роликами и шариками.
Прошивки (рисунок 6.43,а) не имеют режущих зубьев. При проталкивании через отверстие они уплотняют поверхность отверстия, сглаживают неровности.
Калибрование шариком (рисунок 6.43,б) осуществляется продавливанием через отверстие закаленного шарика.
При калибровании дорнами, прошивками и шариками размер отверстия практически не изменяется.
Раскатывание (рисунок 6.43,в) применяют для изменения диаметра отверстия и получения хорошего качества поверхности. Раскатывание осуществляется специальными инструментами – раскатниками, в корпусе которого размещены закаленные ролики или шарики. Раскатывание эффективно при обработке отверстий в высокопластичных материалах. Недостатком раскатывания является трудность получения точного отверстия. Раскатывание требует усиленной смазки.
![]() | 1 – обрабатываемая деталь; 2 – прошивка; 3 – шарик; 4 – раскатник; 5 – ролик Рисунок 6.43 – Обработка отверстий пластическим деформированием а – обработка прошивкой; б – обработка шариком; в – раскатывание роликами |
Обработка систем отверстий
Во многих деталях машин имеются системы отверстий, расположенные в одной или нескольких плоскостях. Для их получения используются следующие методы:
- сверление по предварительной разметке;
- сверление по кондуктору;
- кернение с последующим сверлением;
- пробивка в штампах;
- засверливание и сверление на координатно-расточных станках.
Обработка отверстий с предварительной разметкой и сверлением дает низкую точность координат расположения осей отверстий. Метод применяется только в единичном и мелкосерийном производствах при низких требованиях к точности расположения осей отверстий.
Если требуется высокая точность расположения отверстий, то после сверления отверстия растачивают на координатно-расточном станке. Межцентровое расстояние при этом определится по формуле
,
где – координаты осей отверстий.
Тогда погрешность межцентрового расстояния будет
,
где – погрешности отработки координат.
Сверление по кондуктору является малопроизводительным методом из-за потерь времени на установку в кондуктор и выемку из него детали.. Точность расположения оси отверстия выше чем при сверлении по разметке, но ниже, чем при других методах обработки. Сверление по кондуктору менее точно потому, что к погрешности сверления вследствие наличия зазора между сверлом и кондукторной втулкой, добавляется погрешность изготовления кондуктора.
Кернение с последующим сверлением ведется с помощью керновочных штампов и применяется в серийном и массовом производствах. керновочные штампы применяются и в мелкосерийном производстве взамен дорогостоящих кондукторов. При сверлении по кернам достигается точность расположения оси отверстия до 0,03 мм.
Получение системы точно расположенных отверстий в плоских деталях осуществляют пробивкой их в штампах. Метод высокопроизводителен и позволяет получать до 20 отверстий и более за один ход ползуна пресса. При высоких требованиях к точности межцентровых расстояний, после пробивки отверстия обрабатываются в зачистном штампе, а затем в калибровочном со снятием стружки. При этом может быть получена точность отверстий по диаметру до 0,05 мм, а по межцентровому расстоянию до 0,0075 мм при высоком качестве поверхности отверстий.
Вопросы для самоконтроля
Дата добавления: 2018-02-15; просмотров: 3731; Мы поможем в написании вашей работы! |
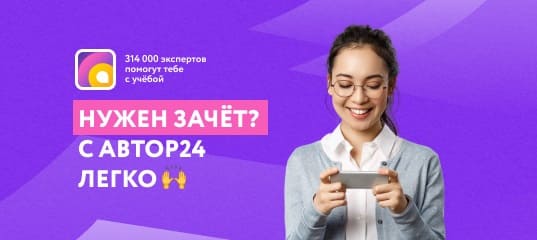
Мы поможем в написании ваших работ!