Назначение и устройство индукционного нагревателя, используемого в процессе демонтажа букс с подшипниками на горячей посадке.
Назовите основные этапы истории и развития вагоноремонтного производства в России. История развития инфраструктуры вагонного хозяйства железных дорог России берет свое начало в конце 19 века. Царскосельской дороги, открытие которой состоялось 11ноября 1837 г. протяженностью 650 км и шириной колеи 1524 мм, строительство которой началось В 1843 году. Вагоны для Петербург-Московской железной дороги начал выпускать в 1846 г. единственный в то время в России Петербургский Александровский завод. В ходе 1-й мировой и гражданской войн в начале 20 века было разрушено более 60% сети, 90% локомотивного и 80% вагонного парка. Уже с 1920 г. началось восстановление вагонного парка железных дорог, а с 1923 г. возобновилось строительство новых вагонов. К 1928 г. удалось в основном восстановить разрушенный железнодорожный транспорт и перевозки довести до объёма 1913 г. Значительных достижений, отечественное вагоностроение и вагоноремонтное производство достигло в 30-х годах, когда были созданы новые четырехосные грузовые и пассажирские вагоны. 1930 – 1940 годы В 1932 принято решение СНК о реконструкции железных дорог В 1933 -1935 гг были пущены в эксплуатацию многие из ныне действующих вагонных депо. Вагоностроительные и вагоноремонтные предприятия оснащались новой техникой. Ручные процессы производства заменялись механизированными. 1941 – 1950 годы Во время Великой Отечественной войны европейская часть сети железных дорог была полностью разрушена, потеряно 40% вагонов и 50% локомотивов. Несмотря на это, железнодорожный транспорт полностью обеспечил военные перевозки и доставку грузов на фронт. В послевоенное время, завершив восстановление разрушенного хозяйства, МПС выступило с инициативой перспективного (на 20 лет) развития и модернизации железнодорожного транспорта. Программой предусматривалась дальнейшая электрификация, внедрение тепловозной тяги, автоматизация и механизация производств 1950 – 1970 годы Введено в эксплуатацию 17 вагонных депо, в том числе 4 пассажирских, 16 пунктов ремонта вагонов на путях сортировочных парков, 8 промывочно-пропарочных станций и пунктов, служебно-производственные помещения для работников 47 пунктов технического осмотра вагонов. 1970 -1990 годы В этот период главное направление развития вагоноремонтного производства состояло в его дальнейшей индустриализации, основой которой служит система машин, обеспечивающая комплексную механизацию и автоматизацию технологических процессов ремонта вагонов и производства запасных частей. 2. Назовите основные задачи и содержание этапов реализации Программы структурной реформы железнодорожного транспорта. Реформирование железнодорожного транспорта проводится в три этапа: · первый этап - 2001-2002 годы; · второй этап - 2003-2005 годы; (этап был продлен до 2006 года) · третий этап - 2006-2010 годы.(фактически реализация основных мероприятий третьего этапа начата в 2007 году). На первом этапе реформирования железнодорожного транспорта были приняты Федеральные законы: · "О железнодорожном транспорте в Российской Федерации" от 10 января 2003 года № 17-ФЗ, · "Устав железнодорожного транспорта Российской Федерации" от 10 января 2003 года № 18-ФЗ, · железнодорожного транспорта» от 27 февраля 2003 года N 29-ФЗ (установил позволившие провести на железнодорожном транспорте разделение функций государственного регулирования и хозяйственного управления, а также выбрать оптимальную организационно – правовую форму для единого хозяйствующего субъекта – открытое акционерное общество. Основополагающей задачей первого этапа реформирования являлось создание правовых основ обеспечения недискриминационного доступа перевозчиков к услугам, предоставляемым владельцами инфраструктуры железнодорожного транспорта общего пользования. На втором этапе: формирование ОАО РЖД как компании холдингового типа, в дочерние общества ушло всё имущество, кроме того которое не отнесено к оборнному комплексу. На третьем этапе : В числе основных задач третьего этапа реформирования - проведение оценки целесообразности полного организационного отделения инфраструктуры от перевозочной деятельности Этап продлен до 2015 г. 3. Назовите основные задачи и содержание этапов структурных преобразований вагонного комплекса в процессе реформирования железнодорожного транспорта России. На сети железных дорог функционируют 82 эксплуатационных депо, являющихся структурными подразделениями железных дорог – филиалов ОАО «РЖД». В составе эксплуатационных депо: 239 пунктов технического обслуживания вагонов (ПТО), 123 пункта подготовки вагонов под погрузку (ППВ), 30 эксплуатационных депо определены как базовые, из них 12 сформированы на базе ПТО сетевого значения, остальные 18 депо будут поэтапно оснащаться в соответствии с требованиями регламента технической оснащенности депо. Кроме того, в комплекс технического обслуживания грузовых вагонов входят: пункты опробования автотормозов на станциях смены локомотива (ПОТ); пункты технической передачи вагонов на подъездные пути промышленных и других предприятий (ПТП); контрольные посты выявления неисправностей у вагонов на ходу поезда (КП); пункты текущего отцепочного ремонта вагонов (ПТОР); промывочно-пропарочные станции (ППС). На сети - 17 основных ППС. Промывочно-пропарочная станция предназначена для комплексной подготовки цистерн к наливу нефтепродуктов, а также их текущего ремонта. В 2009 году 11 ППС из 17 , принадлежащих ОАО «РЖД» передано в аренду на инвестиционных условиях. 4. Назовите основные нормативные документы, определяющие вопросы технической оснащенности вагонных ремонтных депо. Регламент технической оснащенности производственных подразделений вагонных депо по ремонту и эксплуатации грузовых вагонов 665-2003 ПКБ ЦВ от 29 декабря 2003 г.; Нормы технологического проектирования депо для ремонта грузовых и пассажирских вагонов: ВНТП 02-86/МПС. М.: Транспорт, 1992. - 33с.; Каталог проектов технологической оснастки, рекомендуемых для использования предприятиями вагонного хозяйства, проектными институтами МПС и Минтрансстроя № 568-89 ПКБ ЦВ. - М.: Изд-во ПКБ ЦВ МПС, 1990.-106 с.; Руководство по деповскому ремонту вагонов ЦВ-587 от 21 августа 1998 г.; Руководство по капитальному ремонту вагонов ЦВ-4860 от 24 сентября 1991 г. в ред. Указания МПС России от 30.12.2004 N Н-1157у; 5. Назовите функциональные задачи инфраструктурной (эксплуатационной) и ремонтной частей вагонного комплекса холдинга ОАО «РЖД». – обеспечение бесперебойного перевозочного процесса (подготовка вагонов под погрузку, контроль за возникновением неисправностей вагонов в пути следования, технический осмотр вагонов в составе поездов, контроль за работоспособным состоянием автотормозов, допуск вагонов на пути общего пользования, текущий отцепочный ремонт). Данная услуга должна оказываться своевременно в обязательном порядке всем без исключения компаниям-владельцам подвижного состава на недискриминационых условиях в период обращения грузовых вагонов на путях ОАО «РЖД» (железнодорожные пути общего пользования). Инфраструктурная часть вагонного комплекса сохранена в структуре ОАО «РЖД» и органично интегрирована в единую систему инфраструктурного обеспечения деятельности компаний-перевозчиков, функционирующих в сфере железнодорожного транспорта. Такая интеграция позволяет обеспечить необходимый уровень безопасности движения поездов, сократить время нахождения грузов в пути, создать равные конкурентные условия для компаний-перевозчиков. 6. Назовите содержание основных этапов проектирования и изготовления нестандартного технологического оборудования в условиях вагоноремонтных депо. 1) Постановка задач, определение концепции (основной идеи), разработка технических требований к оборудованию на основе техпроцесса; 2) Сопоставление технико - экономических характеристик проектируемого оборудования с с имеющимися аналогами оборудования (по каталогам, патентной литературе, средствам технической информации; 3) Выбор технического решения; 4) Разработка эскизного проекта, (общий вид, кинематическая схема, основные размеры, эскизы основных узлов и деталей, способы сборки – разборки, и т.п.); 5) Разработка и необходимой нормативно – технической документации – рабочих чертежей, деталировок, техническое описание, технологические инструкции по эксплуатации, включая вопросы техники безопасности при работе, маршрутные карты техпроцесса изготовления оборудования; 6) Изготовление опытного образца оборудования, 7) Испытания, ввод в эксплуатацию установленным порядком 7. Назовите виды приводов используемых в нестандартном обор: Нестандартизированное оборудование не имеет ГОСТов, может разрабатываться непосредственно в вагонном депо. Но на него также должна быть инструкция по эксплуатации. К нестандартизированному технологическому оборудованию относятся: моечные машины; вагоноремонтные машины; оборудование для правки, сборки, разборки, сварки и наплавки деталей и узлов вагона. Типы приводов: ― электрический (пылеотсасывающая установка, перемещение тележек моечной машины, установка для правки крышек люков) ― гидравлич. (кантователь, механизм подъема уборочной машины, прессы для правки эл-тов кузова, установка для правки люков, поворотный круг) ― пневматич. (пневмоцилиндр в приспособлении для закрытия крышек люков) ― эл.-гидравлический (стенд для осмотра корпусных деталей тележки) . 8. Какие виды металлообрабатывающих станков используют в контрольных пунктах автосцепки. Фрезерный станок модели 6 П 10. - Поперечно-строгальный станок модели 7 Д 36. - Приспособление для обработки корпуса автосцепки на строгальном и фрезерном станках. - Приспособление для обработки замыкающей части замка автосцепки. - Приспособление для обработки отверстий валика подъемника в корпусе автосцепки типа Т421 ПКБЦВ. - Приспособление для обработки овального отверстия замка автосцепки. - Приспособление для обработки перемычки хвостовика автосцепки. - Приспособление для обработки торца хвостовика автосцепки. - Электропечь для нагрева хвостовика автосцепки и деталей механизма. - Пресс правки хвостовика автосцепки. - Стенд для правки деталей (предохранителя от саморасцепа и замкодержателя
|
|
|
|
|
|
|
|
Способы очистки крытых вагонов при подготовке к перевозкам и при подготовке к плановому ремонту.
Вагоны, поступающие под погрузку или в ремонт после перевозки в них людей, животных, мяса, шерсти, кожного сырья или с неизвестным ветеринарно-санитарным состоянием должны пройти специальную очистку и обработку в соответствии с требованиями санитарных правил, установленных на железнодорожном транспорте (ЦУФ -6/19). При ремонте вагонов используются следующие виды очистки:
Сухая очистка – используются специализированные вагоноуборочные машины, механические щетки, скребки, сжатый воздух, песко-дробеструйные и дробеметные установки;
Обмывка вагонов и их узлов, в том числе: водоструйная очистка без применения моющих растворов используются водопроводные сети и брандспойты;
гидродинамическая очистка с применением моющих растворов и без растворов - используются универсальные и специализированные вагономоечные машины и комплексы;
пароводоструйная очистка с применением моющих растворов и без растворов – используются промывочно – пропарочные станции различных конструкций;
Способы очистки
Механический способ - используют средства механического воздействия, а также силу струи сжатого воздуха, воды, пара, песка, дроби и т.п.
Механическая очистка может производиться ручным и механизированным методами.
К механическому способу относятся;гидродинамическая очистка вагонов и их частей водой под давлением (5—15 МПа)
с помощью брандспойтов или мониторных (гидромониторных) универсальных и специализированных вагономоечных машин и комплексов.
Пароводоструйную очистку поверхности выполняют струей пара температурой 90-100°С под давлением 0,5-2,0 МПа с помощью специальных установок.
виброабразивная очистка – производится путем погружения деталей в жидкую среду в специальных установках, которым придаются
колебательные движения. Очистка происходит под влиянием вибрации. шлифование и полирование –поверхности крупных деталей очищают абразивными кругами на шлифовальных станках или механизированным переносным инструментом и пневматическими зубилами. Метод используется при подготовке поверхности детали, например под гальванические или лакокрасочные антикоррозионные покрытия.
Назначение и устройство индукционного нагревателя, используемого в процессе демонтажа букс с подшипниками на горячей посадке.
В процессе монтажа и демонтажа букс с подшипниками на горячей посадке используется индукционный нагреватель для нагрева лабиринтных колец и внутренних колец подшипников.
Универсальный индукционный нагреватель УН-2[1] применяется для снятия внутренних колец подшипников и лабиринтных колец, установленных в горячем состоянии. Нагреватель, разработанный ПКБ ЦТ МПС, имеет катушку из 98 витков провода ПСД сечением 8,6 мм2.
Индукционный нагреватель применяется с переходными кольцами, изготовленными по конфигурации снимаемого кольца. Переходные кольца служат для заполнения воздушных зазоров между полюсами магнитопровода и концами нагреваемой детали. Они изготовляются разомкнутыми, бесшарнирными из стали марки СтЗ. Толщина кольца выбирается из расчета, чтобы его площадь диаметрального сечения была равна примерно 75% торцовой площади магнитопровода.
На кольце наносится маркировка, для какого лабиринтного кольца по наружному диаметру D и подшипника с наружным диаметром Dнар оно предназначено, например D = 298 мм для подшипника с DHap = 280 мм, или с указанием обозначения подшипника.
Индукционный нагреватель может применяться без переходных колец при наличии суммарного воздушного зазора в магнитной цепи не более 1 мм.
После установки переходных колец, нагреватель вручную устанавливают на снимаемые детали.
Для работы нагреватель подключают к электросети напряжением 220 В. Ток включают кнопкой на ручке.
Под действием магнитного потока переходные кольца будут притягиваться и прижиматься к торцу снимаемой детали и удерживаться в таком положении до съема последней.
Переменный магнитный поток индуктирует в теле нагреваемой детали электрический ток большой силы и вызывает быстрый ее нагрев, незначительно нагревая шейку оси.
Момент ослабления кольца определяется легким покачиванием прибора вокруг шейки или подступичной части оси. Ослабшее кольцо снимается силой магнитного притяжения вместе с прибором и переходными кольцами.
Снятое кольцо и переходные кольца удаляются из прибора выталкивателем после отключения электрического тока.
До полного ослабления и снятия кольца нельзя прерывать питание прибора током, так как это затруднит съемку кольца и может сделать ее невозможной.
При использовании описанного выше индукционного нагревателя рабочий должен непрерывно находиться возле надетого на предподступичную часть колесной пары нагревателя, внимательно наблюдая за процессом нагрева лабиринтного кольца. После того как рабочий решит, что кольцо нагрелось до температуры, при которой оно может быть снято с предподступичной части, он вручную старается сдернуть лабиринтное кольцо вместе с нагревателем, поворачивая его вокруг оси колесной пары. Очень важно не пропустить момент, когда лабиринтное кольцо ослабнет на оси, поэтому рабочий старается чаще повертывать и тянуть на себя нагреваемое кольцо.
Дата добавления: 2018-02-15; просмотров: 1148; Мы поможем в написании вашей работы! |
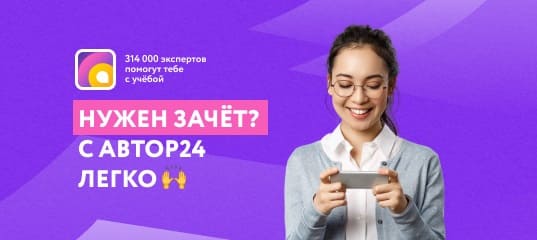
Мы поможем в написании ваших работ!