Cистема питания дизеля воздухом
Система питания дизеля воздухом включает воздушный фильтр, охладитель воздуха и патрубки соединяющие фильтр с турбокомпрессором и далее с охладителем.
Наружный воздух поступает в воздушный фильтр непосредственно через патрубок забора воздуха.
Воздушный фильтр сухого типа (рис. 27) состоит из корпуса, двух фильтрующих элементов и крышки.
Фильтр прикреплен к кронштейнам, установленным на дизеле.
Назначение малого (внутреннего) фильтрующего элемента (может не устанавливаться) - обеспечение очистки воздуха в случае механического разрушения наружного фильтрующего элемента, поэтому его иногда называют “элемент безопасности”. (Допускается эксплуатация дизеля без внутреннего (малого) фильтрующего элемента в воздушном фильтре).
Рис. 27. Воздушный фильтр:
1 - поддон; 2 – корпус; 3 – скоба; 4 и 5 – внутренний и наружный фильтрующие элементы; 6 - прокладка; 7 – гайка-барашек; 8 - кольцо
Для нормальной работы системы питания дизеля воздухом необходимо следить за плотностью соединений, не допуская подсоса неочищенного воздуха в дизель.
Для облегчения контроля засоренности воздушного фильтра, установлен датчик между фильтром и турбокомпрессором, а на панели приборов - сигнализатор.
По мере засорения фильтра растет разрежение во впускном трубопроводе и при достижении величины 6,87 КПа срабатывает сигнализатор. При срабатывании сигнализатора следует провести обслуживание воздушного фильтра.
|
|
Для технического обслуживания фильтра необходимо ослабить хомут соединительного патрубка. Ослабить болты хомутов, крепящих фильтр к кронштейнам, сдвинуть их в стороны и снять фильтр с автомобиля.
Отвернуть гайку-барашек 7 крепления крышки, снять крышку, а затем отвернуть гайки-барашки крепления фильтрующих элементов и вынуть их из корпуса фильтра.
При наличии на картоне фильтрующего элемента пыли без копоти или сажи (элемент серый) рекомендуется продуть их сухим сжатым воздухом до полного удаления пыли.
Во избежание прорыва фильтрующего картона давление сжатого воздуха должно быть не более 0,2...0,3 МПа. Следует направлять струю воздуха под углом к поверхности, регулировать силу струи надо изменением расстояния между наконечником шланга и элементом. При наличии на картоне пыли, копоти, масла, топлива, которые не удаляются обдувом, можно промыть элемент в растворе моющего вещества ОП-7 или ОП-10 в теплой воде (40...50o С). Состав раствора: 20...25 г вещества на 1 л воды.
Вместо раствора ОП-7 или ОП-10 можно использовать раствор той же концентрации стиральных порошков "Новость", "Лотос" и др. Элемент следует промывать, погружая его на 30 мин. в указанный раствор и интенсивно вращая.
|
|
После промывки в растворе нужно прополоскать элемент в чистой воде и тщательно просушить.
Перед установкой очищенного или нового фильтрующего элемента необходимо проверить визуально его состояние, подсвечивая изнутри лампой. При наличии механических повреждений картона, отслаивания крышек и кожухов и других дефектов элемент следует заменить.
При длительной работе автомобиля в условиях повышенной запыленности и при резких изменениях условий окружающей среды сроки технического обслуживания рекомендуется определять, исходя из опыта работы в данных условиях.
При сборке воздушного фильтра нужно обратить внимание на состояние уплотнительных прокладок. Прокладки, имеющие надрывы, должны быть заменены. Качество уплотнения контролируют по наличию сплошного отпечатка на прокладке.
Если в процессе эксплуатации продолжительность работы между необходимыми техническими обслуживаньями элемента два раза подряд составит менее 2000 км пробега, наружный элемент нужно заменить. Ориентировочный срок службы элемента 40 000 км пробега.
Турбокомпрессор
В процессе эксплуатации специального обслуживания турбокомпрессора не требуется.
|
|
Состояние турбокомпрессора следует проверять по времени выбега ротора при остановке дизеля. Для этого после 3...5 мин работы на режиме минимальной частоты вращения холостого хода дизель выводят на режим максимальной частоты вращения, после чего выключить подачу топлива.
Вращение ротора турбокомпрессора после остановки дизеля должно прослушиваться не менее 5 с. Ровный, постоянного уровня звук с постепенным затуханием свидетельствует о нормальном состоянии турбокомпрессора.
Производить полную разборку и ремонт турбокомпрессора в условиях эксплуатации не допускается. Для промывки проточных частей и уплотнительных колец можно провести частичную разборку внешних трубопроводов турбокомпрессора.
Перед разборкой необходимо тщательно очистить наружные поверхности турбокомпрессора от грязи и пыли. Во избежании повреждения лопаток при разборке и сборке турбокомпрессора нельзя ставить средний корпус в сборе с ротором на колесо турбины компрессора. Для этой цели необходимо применять специальную подставку.
Жидкостной подогреватель
У жидкостного подогревателя применена автономная система питания топливом, не связанная с системой питания дизеля.
|
|
Для работы подогревателя применяется то же топливо, что и для дизеля. Заправка топливного бачка подогревателя рассчитана на два часа его работы.
СЦЕПЛЕНИЕ
Техническое обслуживание сцепления заключается в проверке и регулировке полного хода педали сцепления, свободного хода толкателя поршня главного цилиндра, свободного хода муфты подшипника выключения сцепления и удалении воздуха из гидравлической системы механизма управления сцеплением.
Полный ход педали сцепления "С" (рис. 28) до упора в нижний неподвижный ограничитель должен быть равен 180...185 мм. Ход измеряют по середине площадки педали по хорде дуги окружности, описываемой ею.
Рис. 28. Привод сцепления:
1 - кронштейн; 2 - педаль; 3 - оттяжная пружина; 4 - подвижный упор (регулировочный болт); 5 - эксцентриковый палец; 6 - трубка гидравлического привода; 7 - перепускной клапан; 8 - шланг подвода воздуха к усилителю; 9 - шланг гидравлического привода; 10 - пневмогидравлический усилитель; 11 - стяжной болт; 12 - вилка выключения сцепления; 14 - пружина; 15 - щит передка кабины; 16 - главный цилиндр; 17 - бачок главного цилиндра; 18 - палец; 19 - вилка толкателя; 20 - контргайка; 21 - толкатель; А - ход толкателя, соответствующий свободному ходу муфты выключения сцепления; С - полный ход педали сцепления; В - величина выступания торца толкателя из резьбового отверстия вилки
Расположенный в верхней части педали подвижный упор 4 позволяет регулировать полный ход педали изменением ее верхнего положения. После регулировки положение верхнего упора должно быть зафиксировано контргайкой.
Свободный ход толкателя поршня главного цилиндра (1...2 мм) проверяется по перемещению педали сцепления. Ход середины площадки педали должен быть в пределах 5...10 мм до того момента, когда толкатель коснется поршня главного цилиндра.
Регулировка выполняется при крайнем верхнем положении педали поворотом эксцентрикового пальца 5, соединяющего верхнюю проушину толкателя с рычагом педали сцепления.
После регулировки необходимо затянуть и зашплинтовать гайку пальца. Педаль в крайнем верхнем положении удерживается оттяжной пружиной.
Свободный ход муфты подшипника выключения сцепления (должен быть 3...4 мм) проверяется по перемещению рычага вилки выключения сцепления при снятой оттяжной пружине 14.
Перемещение "А" рычага (свободный ход), измеренное по оси соединительного пальца 18, должно быть равно 5...6 мм. Регулировка перемещения рычага осуществляется вращением толкателя 21, положение которого потом фиксируется контргайкой 20.
После регулировки необходимо проверять размер "В" - величину выступания торца толкателя из резьбового отверстия вилки, который должен составлять 0...7 мм. Если размер "В" выходит за указанные пределы (допускается утопание торца толкателя на глубину не более 5 мм), то следует переставить рычаг на вилке выключения сцепления, разведя метки, имеющиеся на торце вилки и рычаге.
После этого надо повторно отрегулировать ход рычага. Метки на рычаге и вилке предназначены для их первоначальной установки. Необходимо подчеркнуть, что, помимо пробуксовки, отсутствие свободного хода ведет к сильному износу фрикционных накладок ведомого диска.
Удаление воздуха из гидравлической системы механизма управления сцеплением. Гидравлическая система механизма управления сцеплением состоит из главного цилиндра 16, исполнительного цилиндра с пневматическим усилителем 10, пневматического и гидравлического трубопроводов.
Для исключения утечки рабочей жидкости и попадания воздуха в гидравлическую систему необходимо тщательно следить за затяжкой всех резьбовых соединений системы.
В случае нарушения герметичности гидравлической системы (попадание воздуха и образование воздушных пробок) ее необходимо герметизировать и повторно прокачать.
Следует помнить, что прокачать систему будет невозможно, если отсутствует свободный ход толкателя поршня главного цилиндра, так как толкатель и поршень представляют собой запорный клапан, через который гидросистема, по мере необходимости, пополняется жидкостью, а при отсутствии свободного хода толкателя он будет постоянно закрыт.
То же самое происходит при заедании педали, если оттяжная пружина не в состоянии поднять ее в крайнее верхнее положение. Прокачку можно проводить как с наличием в системе сжатого воздуха, так и без него. Для этого нужно выполнить следующее.
1. Отвернуть пробку бачка главного цилиндра, вынуть отражатель пробки, после чего заполнить систему рабочей жидкостью до уровня не ниже 15...20 мм от верхнего края бачка. Заполнять систему рабочей жидкостью следует с применением сетчатого фильтра во избежание попадания в систему посторонних примесей.
2. Снять с перепускного клапана, расположенного в верхней части заднего корпуса ПГУ, резиновый колпачок и надеть шланг для прокачивания гидравлического привода на головку клапана. Свободный конец шланга опустить в рабочую жидкость, налитую на 1/4 ...1/3 высоты прозрачного сосуда вместимостью примерно 0,5 л. Работа ускоряется, если на конце шланга есть обратный клапан.
3. Отвернуть на 1/2...1 оборот перепускной клапан и последовательно нажимать на педаль сцепления до упора в нижний ограничитель хода педали с интервалами между нажатиями 1/2...1 с до тех пор, пока не прекратится выделение пузырьков воздуха из рабочей жидкости, поступающей по шлангу в стеклянный сосуд.
Во время прокачки системы следить за тем, чтобы уровень рабочей жидкости в бачке главного цилиндра не опускался ниже 35 мм от края. Это исключит возможность проникновения в систему воздуха и позволит пополнять магистраль рабочей жидкостью. При необходимости периодически доливать жидкость.
При нажатой до упора педали сцепления следует плотно завернуть перепускной клапан. Затем снять с головки клапана шланг и надеть резиновый колпачок.
Процесс прокачки можно несколько ускорить, если после каждого нажатия, не отпуская педаль, завернуть перепускной клапан и только после этого отпустить педаль. Обычно после третьего нажатия из перепускного клапана начинает течь жидкость без пузырьков воздуха
4. После окончания прокачки системы долить свежую рабочую жидкость в бачок главного цилиндра до указанного в п. 1 уровня, установить отражатель пробки и завернуть пробку бачка.
5. Протереть поверхность деталей гидравлического привода.
6. Проверить качество прокачки по величине полного хода толкателя поршня ПГУ, для этого надо нажать на педаль сцепления до упора ее в нижний ограничитель хода.
При правильно отрегулированном механизме управления сцеплением и полностью прокаченной гидравлической системе ход толкателя поршня ПГУ должен быть равен 27...28 мм.
Давление воздуха в пневматической системе автомобиля должно при этом составлять не менее 0,55 МПа. При меньшем давлении сжатый воздух к ПГУ не поступает и усилие на педали сцепления резко возрастает, но работоспособность привода при этом не теряется.
Если ход толкателя меньше указанного, а система исправна и механизм управления сцеплением правильно отрегулирован, то следует продолжить прокачку, как указывалось выше, до полного удаления воздуха из системы и получения надлежащего хода толкателя.
В качестве рабочей жидкости в гидравлической системе механизма управления сцеплением используется тормозная жидкость "РОСДОТ-4" по ТУ 2451-004-36732629-99 в количестве 0,4 л. Применение других жидкостей недопустимо, так как приведет к разбуханию резиновых манжет и уплотнителей и отказу механизма управления сцеплением.
КОРОБКА ПЕРЕДАЧ
Коробка передач механическая, трехходовая, имеет девять передач для движения вперед и одну для движения назад. Коробка передач состоит из основной коробки и планетарного демультипликатора.
Управление редуктором-демультипликатором автоматическое. Схему переключения коробки передач см. рис. 15.
Для нормальной работы синхронизаторов и предупреждения преждевременного износа колец надо правильно и своевременно регулировать свободный ход педали сцепления.
Если сцепление "ведет", то переключение передач становится затруднительным. В случае включения синхронизированных передач с шумом следует немедленно выяснить причину неисправности и устранить ее.
Рис. 29. Сетчатый фильтр маслоприемника
При техническом обслуживании коробки передач следует проверить крепление коробки к картеру сцепления, а также крепление коробки отбора мощности (при ее наличии), поддерживать нормальный уровень масла в коробке передач и своевременно менять его согласно карте смазывания.
Масло надо применять только той марки, которая указана в карте смазывания. При смене масла надо очистить магнит сливной пробки и промыть сетчатый фильтр маслоприемника (рис. 29).
КАРДАННАЯ ПЕРЕДАЧА
Следует периодически проверять посадку крестовин в подшипниках и подшипников в вилках.
При значительных радиальном и торцевом зазорах в подшипниках крестовин нужно карданную передачу отремонтировать.
При ослаблении болтов, крепящих крышки подшипников, нужно их подтянуть, момент затяжки должен быть равен 14...18 Н×м.
Необходимо строго соблюдать периодичность выполнения смазочных операций и применять для карданной передачи (подшипники опоры, шлицевого соединения) смазочный материал в соответствии с требованиями карты смазывания.
Для смазывания шлицевое соединение надо разобрать, промыть шлицы скользящей вилки и внутреннюю полость шлицевой втулки и заложить в эту полость свежий смазочный материал.
При снятии карданного вала с автомобиля или при установке его на автомобиль нельзя пользоваться монтажной лопаткой или другими предметами, вставляемыми в шарнир для прокручивания карданного вала. Это приведет к повреждению торцового уплотнения и преждевременному выходу из строя карданных шарниров.
Карданная передача на заводе-изготовителе подвергается динамической балансировке. Дисбаланс устраняется приваркой балансировочных пластин, поэтому при разборке шарниров или шлицевого соединения необходимо сохранить взаимное положение деталей.
Разбирать шарнир рекомендуется только в случае неисправности его деталей в специализированной мастерской. Для разборки шарнира следует использовать специальный съемник.
ВНИМАНИЕ! Применять молоток для разборки шарнира нельзя, так как при этом нарушается соосность отверстий в вилках шарниров и резко снижается долговечность шарнира.
ЗАДНИЙ МОСТ
На автомобиль установлен задний мост с одноступенчатой гипоидной главной передачей (передаточное число 5,29).
Смазывание главной передачи и ступиц задних колес следует проводить согласно карте смазывания.
Для регулировки конических подшипников ступиц колес нужно затянуть гайку крепления подшипников, проворачивая ступицу в обоих направлениях для предотвращения перекоса роликов (момент затяжки составляет 60...80 Н·м). Ступица после затяжки не должна вращаться, осевой люфт не допускается.
Затем отвернуть гайку приблизительно на 45o, установить замочную шайбу, совместив штифт гайки с ближайшим отверстием в замочной шайбе, установить уплотнение, если оно имеется и затянуть контргайку (момент затяжки равен 250...300 Н·м). При такой регулировки ступица должна свободно вращаться и осевой зазор должен находиться в пределах 0,125...0,25 мм.
Необходимо периодически промывать воздушные каналы сапуна, при их засорении возможно повышение давления в картере заднего моста, что может привести к течи масла.
В гипоидном мосту масло наливают через заливное отверстие на правой боковой стенке картера главной передачи, закрываемое пробкой, до появления течи масла из открытого контрольного отверстия в задней крышке картера моста.
Сливают отработанное масло после предварительного прогрева агрегата через сливное отверстие. Заливное отверстие при этом должно быть открыто.
ВНИМАНИЕ!. При замене смазочного материала или его доливке пробку контрольного отверстия, расположенную справа по ходу автомобиля, нельзя путать с опорным болтом, расположенным слева, во избежание падения маслоуловителя, установленного но опорном болте, в картер моста.
РАМА АВТОМОБИЛЯ
В передней части рамы установлены буфер и два сцепных устройства для буксирования автомобиля.
В отверстии задней поперечины рамы тягово-сцепное устройство с резиновым буфером, обеспечивающим двустороннюю амортизацию, и крюком с защелкой для соединения со сцепной петлей прицепа. Устройство используется для буксирования прицепа.
Недопустима работа автомобиля с прицепами, у которых диаметр прутка, образующего сцепную петлю прицепа, более 43,9 мм.
Нарушение этого требования может привести к поломке крюка из-за потери подвижности в сочленении.
Износ крюка не должен быть более 5 мм, при большем износе замените крюк. Детали тягово-сцепного устройства не должны иметь повреждений. Ось защелки должна быть зашплинтована, а болт крепления оси собачки затянут.
После сцепки с прицепом, защелка должна быть зашплинтована штатным шплинтом или стальной проволокой диаметром не менее 5 мм, с последующей фиксацией ее в осевом направлении (при отгибании проволоки допускается только одноразовое ее применение).
Крюк при вращении его руками должен вращаться с небольшим усилием. Осевое перемещение должно быть не более 0,5 мм.
Запрещается сверлить, прорезать, а также ослаблять какими-либо другими способами горизонтальные полки лонжеронов рамы.
ПЕРЕДНИЙ МОСТ
Передний мост неразрезной, с кулаками вильчатого типа. Цилиндрические шкворни снабжены двумя лысками под клин, расположенными под углом 90о, что позволяет поворачивать шкворень при одностороннем его износе.
Углы поворота устанавливают с помощью упорных болтов рычагов поворотных кулаков, которые упираются в бобышки на балке моста.
Для регулировки осевого зазора между поворотным кулаком и проушиной балки имеются регулировочные прокладки. Зазор считается правильно отрегулированным, если в него нельзя установить прокладку толщиной 0,25 мм.
При увеличении зазора в конических подшипниках ступиц колес более 0,25 мм необходимо произвести их регулировку, для этого нужно затянуть гайку крепления подшипников, проворачивая ступицу в обоих направлениях для предотвращения перекоса роликов (момент затяжки составляет 60...80 Н·м).
Ступица после затяжки не должна вращаться, осевой люфт не допускается. Затем отвернуть гайку приблизительно на 45o, установить замочное кольцо, замочную шайбу, совместив штифт гайки с ближайшим отверстием в замочной шайбе, затянуть контргайку (момент затяжки равен 250...300 Н·м) и отогнуть замочную шайбу на одну из граней гайки.
При такой регулировки ступица должна свободно вращаться и осевой зазор должен находиться в пределах 0,125...0,25 мм.
ПОДВЕСКА АВТОМОБИЛЯ
Техническое обслуживание подвески заключается в смазывании рессорных пальцев, проверке крепления рессор и амортизаторов. Проверке состояния резиновых втулок и буферов.
Стремянки надо затягивать в такой последовательности: сначала равномерно затянуть обе передние (по ходу автомобиля) гайки, а затем обе задние.
Следует также проверять затяжку гаек стремянок крепления ушков передних и задних рессор, затяжку проводить до сжатия пружинных шайб. После полного сжатия пружинных шайб дальнейшая их подтяжка не рекомендуется.
При сквозном износе накладки скользящего конца коренного листа рессоры нужно снять накладку и в дальнейшем эксплуатировать автомобиль без нее.
Сухари скользящего конца передних и задних рессор выполнены симметричными. Если сухарь в зоне контакта с накладкой коренного листа изношен более чем на половину толщины стенки, его надо заменить.
КОЛЕСА И ШИНЫ
На автомобиле установлены дисковые колеса размером 10,00-20, с разрезными бортовыми кольцами.
Шины колес камерные с радиальным кордом имеют размер 280R508.
После каждого снятия и установки колес необходимо проверять затяжку гаек крепления колес через каждые 100...150 км. Если в ходе проверки ослабления затяжки не наблюдается, то последующие проверки производите в сроки планового технического обслуживания (момент затяжки - 400...500 Н·м).
Давление воздуха в шинах с радиальным кордом должно быть для передних колес 0,6 МПа, для задних 0,74 МПа. При проверке давления шины должны быть холодные.
В процессе эксплуатации автомобиля из-за неравномерного изнашивания шин нарушается заводская балансировка колес в сборе с шинами. Поэтому рекомендуется через 15...16 тыс. км пробега проверять дисбаланс колес и устранять его с помощью балансировочных грузов.
ВНИМАНИЕ! Не стойте вплотную к автомобилю при снятии запасного колеса во избежании травмирования ног. Колесо падает вертикально вниз.
Снимать запасное колесо с колесодержателя, показанного на рис. 30 рекомендуется в такой последовательности:
отвернуть гайки крепления колеса к кронштейну;
нажать монтажной лопаткой или другим инструментом на собачку храповика 4 лебедки 2 после чего колесо на тросе опустится на землю.
При установке запасного колеса надо:
- установить пластину 5 с тросом на диск колеса и, вращая ключом гайку 3 лебедки, подтянуть тросом колесо к кронштейну;
- затянуть колесо гайками к кронштейну.
Рис. 30. Установка запасного колеса на автомобиле:
1 - лебедка; 2 - храповик; 3 - гайка; 4 - собачка храповика; 5 - пластина крепления запасного колеса
Рис. 31. Схема перестановки колес
В случае необходимости при неравномерном износе шин следует произвести перестановку колес по схеме приведенной на рис. 31.
Накачивание шин
Для накачивания шин используется шланг и наконечник к нему из комплекта инструмента и принадлежностей. Штуцер шланга навинчивается на клапан отбора воздуха, расположенный справа сзади под кабиной на корпусе влагомаслоотделителя, в другой конец шланга вворачивают наконечник и подсоединяют к вентилю шины.
Верхний предел давления при этом (0,65...0,8 МПа) будет определяться срабатыванием регулятора давления.
ВНИМАНИЕ! Если воздух не поступает в шину, то следует понизить давление в тормозной системе до давления, соответствующего включению регулятора, так как во время работы компрессора в разгрузочном режиме отбор воздуха через этот клапан невозможен.
Понизить давление можно нажав несколько раз на педаль тормоза или открыв любой кран слива конденсата из воздушных баллонов.
Кроме того для накачивания шин и других целей отбор воздуха можно производить от любого клапана контрольного вывода, находящегося под давлением.
РУЛЕВОЕ УПРАВЛЕНИЕ
Автомобиль оборудован рулевым управлением с гидравлическим усилителем, объединенным в один агрегат с рулевым механизмом.
Проверять угловой свободный ход рулевого колеса необходимо при работе двигателя на режиме холостого хода, покачивая рулевое колесо до начала поворота управляемых колес.
Угловой свободный ход рулевого колеса при работе двигателя не должен превышать 25o. Свободный ход следует проверять, предварительно установив прямо передние колеса.
Если свободный ход рулевого колеса больше допустимого, нужно проверить состояние рулевых тяг и их шарниров, регулировку механизма рулевого управления, зазоры в шарнирах карданного вала, затяжку клиньев крепления карданного вала, а также затяжку гайки упорных подшипников в рулевом механизме. При нарушении регулировки механизма рулевого управления или тяг узел надо отремонтировать.
При наличии увеличенных зазоров в карданных сочленениях (окружной зазор более 2о) надо заменить или отремонтировать карданный вал. Убедившись в удовлетворительном состоянии перечисленных узлов, следует проверить затяжку гайки упорных подшипников рулевого механизма.
Для проверки рулевого механизма надо отсоединить продольную тягу рулевого управления и измерить пружинным динамометром, прикрепленным к ободу рулевого колеса, усилие в трех положениях.
Первое - рулевое колесо повернуто более чем на 2 оборота от среднего положения, усилие на ободе рулевого колеса должно быть в пределах 5,5...13,5 Н.
Второе - рулевое колесо повернуто на 3/4...1 оборот от среднего положения, усилие не должно превышать 23 Н.
Третье - рулевое колесо проходит среднее положение, усилие на ободе рулевого колеса должно быть на 8,0...12,5 Н больше усилия, измеренного при втором положении, но не должно превышать 28 Н.
Если усилия не соответствуют указанным, то нужно отрегулировать рулевой механизм.
Регулировку надо начинать с установки усилия на ободе рулевого колеса в третьем положении вращением регулировочного винта вала сошки, так как это не требует разборки рулевого механизма. При вращении винта по часовой стрелке усилие будет увеличиваться, а при вращении против часовой стрелки - уменьшаться.
Несоответствие усилий на ободе колеса во втором положении вызывается повреждением деталей узла шариковой гайки, а в первом - той же причиной, а также неправильным предварительным натягом упорных шариковых подшипников. Для регулировки усилия в первом положении нужно частично разобрать рулевой механизм для затяжки гайки упорных подшипников.
Разбирать рулевой механизм следует только в случае необходимости в специализированной мастерской в условиях полной чистоты.
Осевое перемещение рулевого колеса недопустимо. При наличии осевого перемещения рулевого колеса надо подтянуть гайку крепления подшипников колонки, навернутую на нижний конец вала, предварительно разогнув усики стопорной шайбы. После регулировки один из усиков загнуть в паз гайки. Момент вращения вала рулевого управления, отсоединенного от карданного вала, должен быть равен 0,3...0,8 Н×м.
Чрезмерная затяжка гайки с последующим ее отворачиванием для получения заданного момента вращения вала недопустима, так как может вызвать повреждение подшипника.
При эксплуатации автомобиля необходимо регулярно, в сроки, указанные в карте смазывания, проверять уровень масла в бачке насоса. Во время проверки уровня масла передние колеса автомобиля должны быть установлены прямо. Перед снятием с бачка крышку надо тщательно очистить от грязи и обмыть бензином.
Для системы с рулевым усилителем нужно употреблять только чистое, отфильтрованное масло, указанное в карте смазывания. В бачке насоса установлен бумажный фильтр, смену которого необходимо производить через каждые 40 тыс. км пробега. В этом случае масло доливают до верхней риски на бачке.
При смене масла нужно выполнить следующее:
отсоединить продольную рулевую тягу;
повернуть рулевое колесо влево до упора;
снять крышку бачка, отвернув гайку-барашек;
открыть сливное отверстие, вывернув пробку с магнитом из картера рулевого механизма. Сливать масло до тех пор, пока не прекратится течь масла из сливного отверстия;
удалить из бачка насоса остаток масла и бумажный фильтр;
залить в бачок через воронку с двойной сеткой 1 л свежего масла и слить его через сливное отверстие, поворачивая рулевое колесо от упора до упора;
промыть в бензине снятые детали и продуть их сухим сжатым воздухом;
завернуть пробку с магнитом в сливное отверстие картера рулевого механизма;
установить новый элемент и зафиксировать его прижимной планкой (рис. 32);
![]() | Рис. 32. Приспособление для прокачки гидравлического рулевого усилителя: 1 - прижимная планка; 2 - бумажный фильтрующий элемент; 3 - уплотнитель фильтра |
при повернутом до упора влево рулевом колесе залить свежее масло в бачок насоса до рисок и, вращая рулевое колесо от упора до упора, доливать масло до тех пор, пока в систему не будет залито не менее 2,5 л;
пустить двигатель и при его работе на режиме холостого хода вращать рулевое колесо от упора до упора, удерживая его кратковременно в крайних положениях в течение 2...3 с с усилием примерно 100 Н, и доливать по мере необходимости масло до верхней риски.
Заливка масла и удаление воздуха из системы считаются законченными, когда прекращается выход воздуха в виде пузырьков через масло в бачке насоса;
остановить двигатель и снять с бумажного фильтра прижимную планку;
установить крышку бачка с уплотнительной прокладкой, резиновое кольцо, шайбу и затянуть крышку гайкой-барашком. Гайку-барашек следует затягивать только от руки. При течи масла из-под крышки бачка проверить правильность установки прокладки крышки и в случае повреждения сменить ее;
присоединить продольную рулевую тягу.
Привод рулевого управления состоит из продольной и поперечной рулевых тяг. Шаровые шарниры рулевых тяг регулируемые, закрыты резиновыми чехлами. Эксплуатация автомобиля с разорванными чехлами не разрешается.
При регулировке шарнира пробку надо затянуть до упора, а затем отпустить до первого возможного положения для шплинтовки (но не менее 1/8 оборота) и зашплинтовать.
Для смазывания шарнира нужно вывернуть из наконечника тяги пробку, ввернуть на ее место масленку и смазать шарнир до выдавливания свежей смазки из-под чехла.
Если в процессе пополнения смазочного материала чехол его не пропускает, то для предотвращения повреждения чехла, смазывание следует прекратить после заполнения смазочным материалом полости чехла, которое определяется возрастанием упругости последнего. После смазывания нужно установить пробки на место.
Следует помнить, что полное устранение зазоров шарниров не допускается, так как это может привести к поломке шарового пальца или тяги. Момент качания и вращения шарового пальца должен быть не более 50,0 Н×м.
Поперечная тяга имеет на концах правую и левую резьбу для навинчивания головок с шаровыми шарнирами. С помощью головок можно изменять длину тяги и, следовательно, регулировать схождение передних колес. Шарниры поперечной тяги смазываются через каждые 4000 км пробега автомобиля, а при движении по грязным дорогам чаще.
ТОРМОЗНАЯ СИСТЕМА
Дата добавления: 2021-07-19; просмотров: 89; Мы поможем в написании вашей работы! |
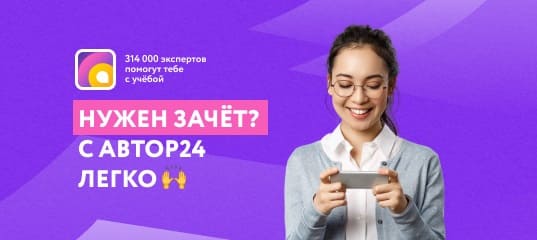
Мы поможем в написании ваших работ!