ЭКОНОМИЯ ВРЕМЕНИ И МАТЕРИАЛОВ
Если 6ы имелось средство сэкономить время на 10% или повысить производительность на 10%, то неприменение этого средства означало 6ы десяти процентный налог на все производство. Если рабочий получает 50 центов в час, то десяти процентная экономия на производстве может дать ему лишний заработок в 5 центов.
Почему у нас строят небоскребы? Потому что 30-этaжнoe здание требует не больше фундамента и земли, чем пятиэтажное. Следование устаревшему способу постройки стоит владельцу пятиэтажного здания годового дохода с 25 этажей. Далее: если 12 тысяч служащих сберегут каждый ежедневно по 10 шагов, то получится экономия пространства и силы в 50 миль.
Таковы соображения, положенные в основу производства на наших предприятиях; вначале они получили применение при сборке частей, a затем перешли и на другие отделы производства.
Наш автомобиль состоит приблизительно из 5 тысяч частей, включая сюда винты, гайки и тому подобное; некоторые части довольно велики, другие – не больше частей часового механизма. При постройке первых автомобилей мы собирали автомобиль прямо на земле, и рабочие приносили отдельные части по порядку на место сборки — так же как строят дома. Первое достижение в сборке состояло в том, что мы стали доставлять работу к рабочим, а не наоборот. Ныне мы следуем двум твердым правилам при всех работах — заставлять рабочего не делать никогда больше одного шага и не допускать, чтобы ему приходилось при работе наклоняться вперед или в стороны.
|
|
При этом рабочие и инструменты располагаются в порядке предстоящей работы таким образом, чтобы каждая часть во время процесса сборки проходила возможно меньший путь.
1 апреля 1913 года мы произвели наш первый опыт со сборочным путем (конвейер) — при сборке магнето.
Это был первый подвижной сборочный путь. Устроен он таким образом, что на больших цепях, прикрепленных на определенной высоте, скользит каждая отдельная часть в последовательном для сборки порядке; ни одному рабочему не приходится ничего таскать или поднимать.
Прежде, когда весь сборочный процесс находился еще в руках одного рабочего, последний был в состоянии собрать от 35 до 45 магнето в течение девятичасового рабочего дня, то есть затрачивал около 20 минут на штуку.
Когда же эта работа, в связи c установкой конвейера, была разложена на 29 различных единичных движений, время сборки одного магнето сократилось до 13 минут 10 секунд.
Дальнейшие опыты над быстротой работы довели время сборки до 5 минут.
Итак, с помощью научных методов рабочий может дать вчетверо больше работы, чем давал ранее. Сборка двигателя, которая раньше также производилась одним рабочим, распадается теперь на 48 отдельных движений, и быстрота работы увеличилась благодаря этому в 3 раза.
|
|
Не следует думать, что все это произошло так скоро и просто, как рассказывается. Для магнето мы сначала взяли скорость скольжения по цепи в 60 дюймов в минуту. Это было слишком скоро. Потом мы попробовали 18 дюймов в минуту. Это было слишком медленно. Наконец мы установили темп в 44 дюйма в минуту. Первым условием является, чтобы ни один рабочий не спешил – ему предоставлены необходимые секунды, но ни одной больше. После того как ошеломляющий успех сборки магнето побудил нас реорганизовать весь наш способ производства и ввести во всем сборочном отделе рабочие пути, приводимые в действие механическим способом, мы установили для каждой отдельной монтировочной работы соответствующий темп работы. Например, сборочный путь для шасси движется со скоростью 6 футов в минуту; путь для сборки передних осей — 148 дюймов в минуту. При сборке шасси производится 45 различных движений и устроено соответствующее число остановок. Первая рабочая группа укрепляет четыре предохранительных кожуха к остову шасси; двигатель появляется на десятой остановке и т. д. Некоторые рабочие делают только одно или два небольших движения рукой, другие — гораздо больше. Рабочий, на чьей обязанности лежит установка какой-нибудь части, не закрепляет ее - эта часть иногда закрепляется только после многих операций. Человек, который вгоняет болт, не завинчивает одновременно гайку; кто ставит гайку, не завинчивает ее накрепко. При движении № 34 новый двигатель получает бензин, предварительно будучи смазан маслом; при движении № 44 радиатор наполняется водой, а при движении № 45 готовый автомобиль выезжает на улицу.
|
|
Мы начали с того, что собирали весь автомобиль на одной фабрике. Позднее, когда мы сами стали изготовлять все отдельные части, мы устроили отделы, в каждом из которых выделывалась только одна какая-нибудь часть. Каждый отдел сам по себе – небольшая фабрика. Часть поступает туда в виде сырого материала или отлитой формы, проходит через целый ряд производственных процессов и покидает свой отдел уже как готовый фабрикат; по мере роста производства и увеличения числа отделов мы приостановили производство целых автомобилей и сделались как бы фабрикой для выделки автомобильных частей.
Это разложение всех производственных процессов на самые простые движения ведет к колоссальной экономии времени и материалов и позволяет нам пользоваться на всех работах совершенно неквалифицированной рабочей силой.
|
|
Большая часть занятых у нас рабочих не посещала школ. Они изучают свою работу в течение нескольких часов или дней. Все, что мы от них требуем, прежде чем определить их на место,- чтобы они были в состоянии дать столько работы, сколько нужно для оплаты того пространства, которое они занимают на фабрике.
Разумеется, мы имеем также большой штат ученых-механиков, но они не строят автомобилей - это люди, занятые только опытами, изготовители инструментов и образцов. Они существуют для того, чтобы облегчать другим производство.
Не проходит недели, чтобы не появилось какого-нибудь улучшения в машинах или в процессе производства, иногда даже противоречащего принятым в стране «лучшим производственным методам».
Мы стараемся бороться со всеми видами расточения человеческой силы, времени и материала.
В области наших опытов и изысканий мы занимаемся исключительно тем, что имеет лишь непосредственное отношение к каждому заданию, более широкими исследованиями мы не занимаемся, Но и в таком виде наша задача достаточно широка. Одни из наших нововведений имеют небольшое, другие - первостепенное значение, но мы не пренебрегаем никакой - даже самой малой - возможностью улучшить производство или сократить время, необходимое для того или иного трудового процесса.
Так, однажды мы обнаружили, что если изготовлять одну часть из материала, который на 2 цента дороже прежнего, то можно понизить ее стоимость на 40%; и вот, хотя стоимость материала возросла на 2 цента, обработка настолько ускорилась, что себестоимость предмета, составлявшая при старом способе 0,2852 доллара, понизилась до 0,1663 доллара (наши издержки вычисляются обычно до десятитысячных долей доллара). Применение нового способа потребовало установки 10 добавочных машин, но так как ежедневно изготовлялось этих частей 10 тысяч штук, то общая экономия составила 1200 долларов в день.
Со времени возникновения нашего предприятия и вплоть до недавнего времени мы употребляли для выработки автомобильных рулей дерево. Это было очень убыточно, ибо дерево шло на эту работу только высшего качества. Между тем на одной из наших фирм скапливалось за год много тонн соломы. С ее помощью нам удалось получить состав, названный фордитом и состоящий из смеси соломы, резины, серы, кремния и других веществ, соответственно обработанных при известной температуре. Эта масса, получив нужную форму, после охлаждения приобретает твердость кремния.
Этот способ дешевле прежнего приблизительно на 50% и к тому же сберегает дерево.
На дорожный автомобиль идет около 15 ярдов искусственной кожи для верха, занавесок и обивки. Мы употребляем пять различных сортов этой кожи. Не могло быть и речи об употреблении естественной кожи: во-первых, она слишком дорога, во-вторых, сколько бы ни убивать животных, этим ни в малой степени не был бы покрыт наш спрос. Наш персонал с огромным трудом изобрел разновидность искусственной кожи, вполне удовлетворявшую нас; потребовалось не меньше пяти-шести лет на это изобретение, и теперь собственное производство кожи не только делает нас независимыми от рынка, но и сберегает более 12 тысяч долларов в день.
Тепловая обработка стали имеет огромное значение, ибо она позволяет, увеличивая крепость отдельных частей, уменьшать их вес. Но это очень трудная операция: предмет не должен быть ни слишком мягким - во избежание стирания, ни слишком твердым - во избежание поломки. Степень требуемой твердости зависит от назначения той или другой части. Само по себе это кажется простом, но изготовление большого количества частей, обладающих должной степенью твердости, далеко не простая вещь.
Одному молодому человеку мы поручили усовершенствовать наши методы тепловой обработки. Он вначале не имел никакого понятия о металлургии. Он действовал ощупью год или два и затем добился осязаемых результатов: он не только сократил число рабочих, но и построил закалочную машину, обеспечивающую равномерное охлаждение закаленных осей, расположенных по кругу. Таким образом, они не сгибаются и не нуждаются в позднейшей выправке.
Замена газовой печи электрической составила весьма важный прогресс. В то время как при четырех газовых печах, обслуживаемых шестью рабочими и мастером, один только отпуск 1000 шатунов требовал одного часа, две электрические печи за это же время производят закалку и отпуск 1300 шатунов, требуя только двух рабочих: одного - для загрузки, другого - для вынимания шатунов.
Это изменение способов тепловой обработки кажется маловажным, а между тем мы сберегли на нем до 36 миллионов долларов за четыре года.
Еще пример – сборка поршня.
Даже по старой системе процедура эта требовала только трех минут - казалось, она не заслуживает особого внимания. Для этого были поставлены два стола, у которых было занято 28 человек: в течение девятичасового рабочего дня они собирали всего-навсего 175 поршней - им требовалось ровно три минуты и пять секунд на штуку. Никто не наблюдал за этим, и многие поршни оказывались негодными при сборке мотора.
Весь процесс был, в общем, прост. Рабочий вытаскивал валик из поршня, смазывал его, вставлял на место шатун и валик, притягивал один винт и подтягивал другой, и дело было закончено. Наш наблюдатель подверг весь процесс точной проверке, но не был в состоянии сказать, почему на это требовалось целых три минуты. Он проверил тогда различные движения по хронометру и нашел, что при девятичасовом рабочем дне четыре часа уходило на хождение взад и вперед. Рабочие не уходили совсем, но они должны были двигаться то туда, то сюда, чтобы принести материал и отложить в сторону готовую часть. Во время всего процесса каждый рабочий делал восемь различных движений рукою. Наблюдатель предложил новый план, причем он разложил весь процесс на три действия, поставил трех человек с каждой стороны и одного надсмотрщика на конце. Вместо того чтобы производить все движения, каждый человек проделывал только треть таковых - столько, сколько можно было сделать, не двигаясь в стороны. Группа рабочих была сокращена с 28 до 14 человек. Рекордная производительность 28 человек была 175 штук в день. А теперь семь человек в течение восьмичасового рабочего дня выпускают 2600 штук.
Подобные примеры можно множить без конца.
Этими успехами мы обязаны главным образом тому, что совершенно не считались с мнением, так называемых экспертов-специалистов, которые обычно являются врагами всяких нововведений и на предложение ввести какие-либо новые приемы в работе, находящиеся в прямом противоречии с прежними приемами, отвечают: «Это невозможно!»
Мы были вынуждены отпустить всех лиц, которые воображали себя экспертами, потому что никто, хорошо знающий свою работу, не будет утверждать, что знает ее досконально.
Я наотрез отказываюсь считать что-либо невозможным. Я считаю, что нет на земле человека, который был бы настолько сведущ в известной области, что мог бы с уверенностью утверждать возможность или невозможность чего-нибудь.
Нелегко освободиться от традиций. Вот почему практическим осуществлением наших новых приемов всегда руководят люди, никогда специально не занимавшиеся данным вопросом; тогда им не угрожает опасность остановиться перед тем, что другие считают «невозможным». Мы обращаемся к экспертам-техникам всякий раз, когда их помощь представляется необходимой, но ни одной операцией не руководит техник, ибо он слишком убежден, что то или иное не может быть осуществлено. На заявление: «Это невозможно!» - мы неизменно отвечаем: «Тем больше оснований попытаться».
Совершенно исключительное значение мы придаем нашим опытам по механической обработке льна и производству льняной ткани.
Мы расходуем ежедневно до 100 тысяч ярдов хлопчатобумажной ткани и до 25 тысяч ярдов шерстяной. Таким образом, даже самая малая экономия на каждом ярде ткани дала бы нам за год огромные сбережения.
Это соображение и побудило нас произвести ряд изысканий в текстильной области. Для этой цели мы построили небольшую текстильную фабрику. Прежде всего, мы установили, что хлопок отнюдь не является наилучшим материалом для наших целей и что мы пользовались им до сего времени лишь потому, что его легче всего было достать; гораздо более отвечал нашим целям лен, ибо льняное полотно значительно прочнее; известно, что прочность ткани зависит от длины волокна, а из всех волокон волокно льна отличается наибольшей длиной и прочностью.
Чтобы пользоваться своим хлопком, нам пришлось бы выращивать его на расстоянии нескольких тысяч миль от наших заводов и нести сопряженные с этим транспортные расходы; лен, наоборот, можно было выращивать поблизости от наших заводов и выстроенной нами текстильной фабрики.
Но тут мы встретились с одним существенным препятствием, которое до сего времени вообще стояло на пути развития льноводства в нашей стране.
Препятствие это состояло в тех многочисленных и устойчивых традициях, которые определяли собою процесс прядения льна.
Приемы его обработки ничем не отличались от приемов, практиковавшихся несколько тысяч лет назад; таковы они и сейчас в Ирландии, Бельгии, России - везде, где выращивается это растение; вся работа делается вручную, требует большого количества рабочих рук, а потому и представляет собою весьма невыгодное занятие; помимо того, работа эта очень кропотлива и изнурительна.
Мы поставили перед собой задачу по возможности механизировать все процессы обработки льна, ибо на наших предприятиях применение ручного груда невозможно.
Прежде всего, мы отвели под лен 600 акров земли; эта земля была вспахана механически; посев, уборка, сушка, молотьба и, наконец, очищение волокна были также произведены механически.
Следует отметить, что до нас это не удавалось никому.
Идущее на изготовление тканей волокно льна покрыто оболочкой стебля; лен никогда не жали и не косили, как хлеб, дабы не нарушить параллельности стеблей, что затруднило бы последующую обработку; далее, считали, что если лен срезать, то у корня остается ценная часть стебля; поэтому лен выдергивают руками, а когда урожай собран, выбивают семена, причем много семян теряется. Итак, уже в самом начале обработки льна две операции - уборка и отделение семян - производятся вручную.
Мы начали производить уборку с помощью жатвенной машины, ибо считали для себя более выгодным допустить некоторую потерю волокна, чем прибегнуть к ручной работе; семена мы пока оставляли на стеблях.
При ручном способе после уборки приступают к мочке льна; стебли связывают в снопы и кладут в проточную воду на несколько недель. Когда стебли в достаточной мере прогнили, снопы вынимают из воды и высушивают на солнце; прогнивший лен издает невыносимый запах, что делает эту работу весьма тяжелой и нездоровой.
Следующая операция - «трепание» льна для отделения волокна – наиболее расточительна и убыточна, ибо требует огромной затраты труда.
Мы упразднили все эти трудные и дорогие ручные операции. После уборки мы оставляем стебли на открытом воздухе в течение нескольких недель, а затем собираем их в копны, так же как сено. Вместо того чтобы сушить лен на солнце, мы пропускаем его на особом транспортере через печь; этот же транспортер подводит лен к машине, которая носит название автоматической трепалки и которая с успехом выполняет прежнюю операцию трепания от руки: она отделяет все семена и волокна, оставляя на одной стороне – тонкий лен, на другой – очесы; при этом совершенно безразлично, в каком виде стебли поступают в машину – параллельны они или нет.
Эта машина, управляемая двумя рабочими, за восемь часов может вытрепать столько льна, сколько треплют от руки 10 человек за 12 часов.
Сам процесс тканья льняного полотна производится специальными машинами, купленными нами в Европе. В эти машины нами уже внесен ряд усовершенствований, и нет сомнения, что в скором времени мы добьемся того, что лен будет поступать в машины с одного конца, а с другого будет выходить готовое и окрашенное льняное полотно.
Таким образом, все операции, начиная с сушки льна и кончая окрашиванием готового полотна, будут представлять собою один непрерывный механический процесс.
Мы считаем эти свои опыты важнейшими из всех, производимых нами. Они могут послужить толчком к созданию новой отрасли промышленности и стать одним из подсобных промыслов земледельца; место автоматических трепалок, веретен и ткацких станков - в деревне, вблизи льняных плантации.
Большую ценность имеют побочные продукты льна: масло, пакля и др. Наши химики производят в настоящее время опыты по выделению из льна целлюлозных составных частей. Эти части после соответственной обработки могут быть применены в качестве лака для верха автомобилей, а в твердом виде – для фабрикации ручек, электрических приборов и т. п.
Мы пытаемся также наладить по способу непрерывности производственного процесса и выработку необходимых нам шерстяных тканей. Пока мы произвели незначительные изменения в машинах, но уже сейчас можно сказать, что мы в скором времени сможем добиться при изготовлении нашего сукна приблизительно 30% экономии, что составляет несколько миллионов долларов в год.
Возьмем, далее, процесс производства стекла. Стекольное производство насчитывает много веков, и в нем также существуют свои традиции, главная из которых состоит в выработке того глиняного сосуда, в котором смесь переплавляется в стекло. Глина месится голыми ногами рабочих, а горшок делается руками. Мы долго следовали этой традиции и лишь кое-какие ручные операции заменили машинными.
Но нам казалось, что можно производить оконное и зеркальное стекло непрерывной широкой лентой и совершенно не пользоваться при том ручной работой.
Все эксперты по части стекольной промышленности заявляли, что это уже испробовано и оказалось невозможным. Тогда мы поручили эту задачу людям, никогда ранее не занимавшимся стекольным производством. Они начали производить опыты и встретились со всеми затруднениями, о которых им говорили, и еще с целым рядом других, непредусмотренных, но в конце концов они добились своего.
Два наших завода производят ныне 14 с половиной миллионов квадратных футов стекла, и хотя мы не смогли расширить наши заводы в такой мере, чтобы удовлетворить наши потребности, на вырабатываемом нами стекле мы сберегаем 3 миллиона долларов в год.
Говорилось, что серый чугун не будет выливаться по нашему ценному методу; налицо имелся даже целый ряд неудачных опытов. Несмотря на это, мы делаем это сейчас. Тот человек, которому это наконец удалось, или ничего не знал о прежних опытах или не обратил на них внимания. Равным образом нам доказывали, что совершенно невозможно выливать горячий металл из плавильных печей прямо в формы. Обыкновенно металл течет сначала по лоткам, отстаивается там и перед выливанием в форму растапливается еще раз. Но на нашей фабрике мы теперь научились выливать металл прямо из круглых плавильных печей.
Разумеется, эти новые приемы также дают нам большую экономию.
В общем, мы руководствуемся тем взглядом, что мы должны находить наилучшие способы для выработки производимых нами предметов и что на каждый процесс производства мы должны смотреть лишь с точки зрения опыта.
Если мы достигли успехов, которые кажутся нам замечательными по сравнению с тем, что было раньше, то мы все же считаем их лишь одной из ступеней в улучшении нашего производства. По переменам, уже происшедшим, мы предвидим дальнейшие, гораздо более замечательные; но нет и не может быть ни одной операции, о которой мы могли бы сказать, что выполняем ее в совершенстве.
ИСПОЛЬЗОВАНИЕ ОТБРОСОВ
Наш отдел по использованию отбросов производства поставлен на широкую ногу и дает нам более 20 миллионов долларов в год.
Но по мере того как этот отдел разрастался, становясь все более важным и выгодным, мы начали задумываться: «Не слишком ли много у нас отбросов? Не уделяем ли мы слишком много внимания их использованию, вместо того чтобы позаботиться об устранении самой возможности отбросов?»
С этой новой точки зрения мы приступили к обследованию всех наших предприятий, и результатом этого обследования явилось то, что мы в настоящее время сберегаем 80 миллионов фунтов стали в год; раньше эта сталь представляла собою отбросы, которые шли в переработку и требовали большой затраты труда. Этот труд стоил ежегодно более 3 миллионов долларов, что при нашей заработной плате равно труду 2 тысяч рабочих.
Это сбережение было достигнуто такими простыми средствами, что следует только удивляться, как мы не додумались до этого раньше.
Вот несколько примеров.
Раньше изготовляли кожухи для двигателей из готовых стальных листов, обрезанных точно по длине и ширине кожуха. Сталь эта обходилась нам в 0,0335 доллара за фунт. Теперь мы покупаем листы длиною в 150 дюймов по цене 0,028 доллара, сокращаем длину до 109 дюймов и за одну операцию нарезаем пять кожухов; остаток листа идет на изготовление другой части. Это дает экономию в 4 миллиона фунтов стали в год, что составляет около полумиллиона долларов.
Стойка переднего стекла имеет несколько неправильную форму. Мы ее вырезали раньше из прямоугольных стальных листов 18 × 32,5 дюйма. Из листа получалось шесть стоек и некоторое количество обрезков. Теперь, употребляя листы 152 × 32,5 дюйма, срезанные под углом в 7 градусов, мы получаем шесть стоек из листа, как и раньше, но при этом у нас остается еще 10 мелких кусков. Отсюда - ежегодное сбережение полутора миллионов фунтов стали.
Крестообразную подставку для масляных резервуаров мы раньше штамповали из стали, с большим количеством отбросов, по себестоимости в 0,0635 доллара. Мы вырезаем теперь отдельно обе половинки креста, что почти не дает лома, и свариваем их: штука обходится нам в 0,048 доллара.
Бронзовая трубка в рулевом механизме раньше имела в поперечине 0,128 дюйма (3,25 мм). Мы убедились, что она вполне может выполнить свое назначение, будучи наполовину тоньше. Мы сберегаем 130 тысяч фунтов бронзы в год, то есть более 30 тысяч долларов. Опорой прожектора служит крест размерами 7,5 × 3,5 дюйма; мы нарезали 14 таких крестов из листа 6,5 × 35 дюймов. Уменьшив размеры до 7,5 × 31/8 дюйма, мы получили возможность вырезать то же количество, что и раньше, из листа в 57/8 ×35 дюймов; это сберегает нам более 100 тысяч фунтов стали в год.
Раньше мы вырезали шкив вентилятора из нового листа. Теперь мы делаем его из обрезков, сберегая около 300 тысяч фунтов стали в год. Слегка видоизменяя мелкие латунные части, мы ежегодно сберегаем больше миллиона фунтов латуни. На 19 частях, нарезаемых из полос или труб, переменив инструменты, изменив размеры, мы сберегаем более миллиона фунтов стали в год. Мы получали, например, 18 частей из полосы длиною в 143 дюйма, но убедились, что можем получать то же число частей из полосы длиною в 1409/32 дюйма, выгадывая, таким образом, более 2 дюймов на каждой. Для многочисленных мелких предметов мы заменили горячую прокатку холодной, что на 16 мелких единицах дает 300 тысяч долларов экономии в год. Эти примеры были нами введены во всех цехах.
Мы считаем, что обрезки - вещь, которой можно избежать, а к переплавке следует прибегать лишь в крайнем случае.
Так, например, старые стальные железнодорожные рельсы мы считали ломом, подлежащим переплавке. В настоящее время мы прокатываем их через вал таким образом, что головка и подошва отделяются друг от друга и получаются превосходные стальные полосы, которые можно применить для самых различных целей.
Мы надеемся развить применение этой идеи и для многих других случаев, ибо количество стали, которую мы рассматриваем как лом, составляет и сейчас не менее 1000 тонн в день. Мы продавали ее на сторону, а затем сами же приобретали под видом стали, неся расходы по перевозке в оба конца.
Теперь мы установили на одном из наших заводов электрические печи и оборудовали прокатную, чтобы самим переплавлять свой стальной лом и избежать транспортных расходов.
Если мы не можем совершенно избежать отбросов – есть и неизбежные,– то мы можем по крайней мере сберечь человеческий труд, затрачиваемый на хранение и перевозку.
Использование отбросов развернулось на наших предприятиях в настоящую промышленность; в ней заняты преимущественно рабочие, которые по слабости здоровья не могут работать в других цехах.
Здесь переплавляются отбросы меди, бронзы, свинца, алюминия, баббита, стали, железа; песок, употребляющийся при формовке металлического литья, также используется, ибо представляет собою известную ценность, а главным образом, для того, чтобы сберечь издержки на его переноску и перевозку.
Используются также все отбросы масел, и то, что непригодно для смазки машин, идет на топливо.
Найден способ разбавлять цианистое соединение, употребляемое при тепловой обработке металлов, что уменьшает расходы наполовину. В наших лабораториях изобретен особый состав для наклейки холщовой оболочки на шкивы, уменьшающей скольжение ремней и соответственную потерю энергии. Утилизируются отбросы кирпича, а также шлак из печей. В нашем фотографическом отделении извлекаются серебряные соли из растворов проявителя. Экономия составляет около 10 тысяч долларов в год.
У нас в мастерских имелось большое количество бумажных и тряпичных отбросов, а в мастерской, где изготовляются автомобильные кузова, много отбросов твердого дерева; мы предполагали превращать все эти отбросы в бумагу, но нам сказали, что из твердого дерева нельзя делать бумагу.
Мы, однако, установили мельницу для переработки древесной массы, и в настоящее время наша бумажная фабрика поглощает в день 20 тонн отбросов и вырабатывает 14 тонн обыкновенного картона и 8 тонн особого водонепроницаемого картона по способу, изобретенному в наших лабораториях. Этот картон так крепок, что десятидюймовый лист его выдерживает вес нашего автомобиля; часть картона идет на обивку кузова, другая - на ящики, в которых перевозятся автомобильные части, чем сильно сокращается расход дерева.
Доменные печи дают 500 тонн шлака в день; из них 225 тонн идут на изготовление цемента, а остальное дробится и употребляется на мощение дорог.
Цементный завод дает нам около 2 тысяч бочек цемента в год.
Особо следует отметить деятельность нашего ремонтного отделения. Здесь ведется список всех машин, имеющихся на наших предприятиях, с точным указанием рода и размера требующихся для них орудий. В любой момент мы можем получить здесь точное указание, что сделать из испорченного инструмента. Обычно его можно переработать в такой же инструмент меньшего размера, но всегда согласно основному чертежу.
Перед переделкой все инструменты сортируются; используются даже ручки поломанных инструментов; из ручки лопаты отлично можно сделать несколько ручек для отверток или ручки для ножниц.
Кирки, лопаты, заступы, ломы, щетки - все идет в переделку, поскольку это представляется выгодным.
В день используется около 500 галлонов старой краски, которая идет для грубых работ.
Каждый промышленник обязан делать все от него зависящее для экономного расходования материалов, как с целью понижения цен на фабрикаты, так и для сбережения материалов, добывание и доставка которых ложатся все более тяжелым бременем на промышленность, а следовательно, и на покупателя.
О СТАНДАРТАХ
За последнее время много говорят о стандартизации производства, об установлении единого образца - стандарта - для каждой отдельной отрасли промышленности страны; так, мыслят полную стандартизацию производства автомобилей, одежды, мебели и пр.
При установлении образцов-стандартов нужна чрезвычайная осмотрительность, ибо легче установить неправильный стандарт, чем правильный.
Предположим, например, что какая-нибудь комиссия или правительственная организация, обследуя разные отрасли промышленности с целью установления, сколько изготавливается сортов одного и того же предмета, устранила модели, признанные излишними, и определила образцы, которые следует считать стандартными. Выгадал ли покупатель от такого отбора? Ни в какой степени!
Никакая посторонняя организация не может обладать достаточными познаниями для установления стандартов, ибо знания эти тесно связаны с ходом самого производственного процесса в каждом предприятии и не могут быть приобретены людьми, приходящими со стороны.
Но даже, если бы такая комиссия и обладала достаточными познаниями для установления стандартов, – эти стандарты, хотя бы они имели следствием некоторую экономию, затормозили бы общее развитие промышленности; дело в том, что промышленники считали бы достаточным производить по установленным образцам, вместо того чтобы сообразоваться с подлинными потребностями покупателей, и людская изобретательность не поощрялась бы, а тормозилась.
Некоторые, общие для всей страны, стандарты, разумеется, необходимы. Дюйм всегда должен быть дюймом. Когда мы покупаем по весу или по длине, мы должны знать, что именно мы покупаем. Обувь определенного номера должна быть во всей стране одного размера. Кварта должна быть квартой, фунт - фунтом. В этом отношении стандартизация удобна и необходима.
То же самое относится к квалификации - установлению определенного качества предмета. Определенный сорт цемента должен быть всегда одинаковым, чтобы покупателям не пришлось каждый раз проверять его. Выражение «чистая шерсть», так же как и «чистый шелк», должно точно соответствовать действительному качеству товара.
Мелкий розничный покупатель, не располагающий способами точной проверки, должен иметь возможность полагаться на существующие печатные описания каждого предмета.
Здесь стандартизация - установление раз и навсегда определенных образцов,- повторяю, необходима и предотвращает злостную конкуренцию, при которой плохой и хороший товар продаются под одной маркой.
Но совершенно иначе обстоит дело со стилем предметов, то есть с их формой, которая существует совершенно независимо от качества материалов, из которых они сделаны.
Люди, незнакомые с производством, любят представлять себе стандартизованный мир, где все живут в одинаковых домах, носят одинаковую одежду, питаются одинаковой пищей и чуть ли не одинаково мыслят и действуют. Но такой мир был бы тюрьмой, и он невозможен, пока люди еще продолжают мыслить.
Вопрос о том, до какой степени указанные предметы могут быть сведены к нескольким типам, должен разрешаться не государством в целом, а каждой отдельной промышленной единицей.
Против разнообразия моделей по большей части возражают в том смысле, что разнообразие несовместимо с экономным производством. Здесь на лицо определенное заблуждение - ведь если предприятия специализируются каждое на выработке одной определенной модели-стандарта, то этим достигается уже и экономия и разнообразие вместе, так что нет необходимости распространять такой образец на все промышленные предприятия, на всю страну.
Стандартизация в истинном смысле этого слова есть сочетание лучших качеств изделия с наилучшими способами его производства; стандартизировать изделие и способ его производства – значит выбрать из многих возможностей одну, наилучшую, и применить ее.
Каков же наилучший способ производства? Это сочетание всех хороших способов, изобретенных до сих пор.
Но устанавливать, что сегодняшний стандарт будет стандартом и завтра, – значит превышать свои силы и свои права, ибо ничто не может помешать промышленному предприятию изобрести завтра еще более совершенное и отвечающее спросу изделие. Только поверхностные люди могут воображать, что стандарт есть какая-то стальная форма, в которую можно заключить все человеческие усилия и придать им единый облик на все времена.
Следовательно, стандарт, с нашей точки зрения, есть такой образец, который сегодня лучше всех других, а завтра будет еще более улучшен.
Мы считаем, что ни один завод не является достаточно большим, чтобы производить два рода продуктов. Несколько лет назад мы приобрели завод Линкольнской автомобильной компании. Наша «Модель Т», общеизвестный «форд», является нашей главной специальностью, и мы сделали ее ходовым товаром – нашим стандартом. Но у нас не было ни малейшего намерения делать ходовым товаром модель Линкольнской компании.
Хотя эти обе модели принадлежат теперь одной фирме, но изготавливаются на разных заводах и служат разным целям.
Между тем как «Модель Т» дешева и доступна буквально всем, линкольнская модель по карману лишь очень немногим; она не представляет собою предмет роскоши, но в то же время и не является предметом общего пользования.
А между тем оба типа автомобилей стандартизированы в том смысле, как мы говорили выше.
Заработок одного человека позволяет ему приобрести один тип изделия, другому - более дорогой.
При таком понимании стандартизация не станет угрозой промышленному развитию и усовершенствованию техники, как в том случае, если бы установление стандартов производства исходило сверху, от правительственной власти.
Лично мы придаем разумной стандартизации весьма важное значение и проводим ее не только в отношении наших изделий - автомобилей - в целом, но и в отношении мельчайших частей, из которых они состоят, а также и машин, на которых эти части изготавливаются. Именно этому обязаны мы своими успехами и ростом нашего предприятия.
Для экономизации производства необходимо, чтобы одноименные части были взаимозаменимы. Наши автомобили не делаются в одном определенном месте, мы изготовляем лишь автомобильные части, а сборка автомобилей происходит там, где они должны быть проданы.
Такая система по необходимости влечет за собою исключительную точность производства, ибо если части не будут пригнаны совершенно точно друг к другу, то окончательная сборка просто не удастся.
Поэтому-то мы стремимся к абсолютной точности в производстве, точности, доходящей в иных случаях до одной десятитысячной доли дюйма.
В обычных условиях нельзя достигнуть такой точности, и нужна она лишь в исключительных случаях, а для большинства работ мы довольствуемся точностью до одной тысячной дюйма.
Чтобы добиться этой точности, мы обратились к единственному человеку в мире, сделавшему достижение предельной точности основным предметом своей деятельности, и привлекли его в свое предприятие; человек этот – Карл Иогансен, работавший в качестве старшего мастера в арсеналах шведского правительства, прославился тем, что изобрел такое сочетание составных элементов, употребляющихся при производстве ружейных частей, что оно позволяло получать из небольшого их количества большое число калибров (размеров). Первый набор был им сделан в 1897 году.
В настоящее время измерительные инструменты Иогансена считаются самыми точными в мире.
Мы приобрели право выделки измерительных приборов Иогансена для Америки, а сам Иогансен вошел в наше предприятие и продолжает свои исследования.
Приборы Иогансена - прямоугольные части из инструментальной стали, закаленной, выверенной и отшлифованной. Их поверхности совершенно плоски и параллельны. Это является замечательным механическим достижением, ибо всеми признано, что добиться такой совершенной параллельности двух стальных поверхностей - исключительно трудная задача. Профессор И. Хьельслей, декан математического факультета Копенгагенского университета, заявляет, что поверхности этих приборов представляют собою наибольшее приближение к предельной плоскости, когда-либо выполненное человеческой рукой. Эти поверхности обладают необычайными свойствами: если их потереть о ладонь и приложить одну к другой, они слипаются с силой, равной 33 атмосферам.
Ученые предлагают различные объяснения этого явления: атмосферное давление, молекулярное притяжение и наличие чрезвычайно тонкой жидкой пленки на соприкасающихся поверхностях. Возможно, что все эти три действия совмещаются. Две поверхности, потертые о кожу и затем прижатые друг к другу посредством скольжения, могут противостоять тяге в 210 фунтов. Это доказывает, что не атмосферное давление вызывает подобное сцепление.
В некоторых наборах эти измерительные инструменты отличаются один от другого на одну десятитысячную дюйма, в других - на одну стотысячную. Одна десятитысячная дюйма - это наивысший предел точности, применяемой в нашем производстве, но он кажется низким по сравнению с инструментами Иогансена. Рекорд, однако, достигнут одним прибором, в котором разница доведена до одной миллионной дюйма. Его чувствительность такова, что на него влияет температура тела оператора на расстоянии нескольких шагов. Этот прибор - единственный в мире. Хотя нам принадлежит монополия на эти приборы, мы, с тех пор как приобрели права для Америки, работаем над усовершенствованием методов их производства, чтобы тем самым увеличить их производство и понизить цены; это сделает доступными иогансеновские приборы для каждой механической мастерской и для каждого инструментального мастера. Все это лишний раз доказывает, что высокое качество и массовое производство вовсе не исключают друг друга.
По мере того как разрасталось наше предприятие, перед нами встал вопрос о стандартизации всего нашего оборудования. На наших заводах в Америке имеется несколько десятков тысяч машин; к тому же мы время от времени оборудуем новые фабрики в различных частях света. Поэтому мы, естественно, должны всегда иметь в своем распоряжении запасные части этих машин; любой производственный процесс на нашей фабрике в Испании должен выполняться точно так же, как в Америке, ибо мы не можем пренебрегать накопленным нами опытом. Рабочий, стоящий у сборочного конвейера в Детройте, должен быть в состоянии немедленно встать у такого же конвейера в любом другом городе.
Около 90% нашего оборудования стандартизировано.
Стандартные машины подразделяются на 250 различных групп, каждая из которых подразделяется на типы и виды; общее число видов исчисляется тысячами.
В группах, носящих название токарных станков, прессов, пил, сверл и так далее, заключаются сотни различных видов, каждый из которых отличается и своей формой, и размерами.
И вот, несмотря на то что мы выпускаем в настоящее время 8 тысяч автомобилей в день, у нас вложено меньше капитала в оборудование, чем когда наша продукция равнялась 3 тысячам автомобилей в день.
Это объясняется исключительно стандартизацией.
Это стандартизированное оборудование - результат двадцатилетней работы. Ныне эта система развилась до такой степени, что наши машины не труднее приобрести, чем какой-нибудь обиходный предмет. То же относится к инструментам, употребляемым для производства машин. Все зубчатки, ключи, оси, рычаги, педали и другие части машин стандартизированы; комбинируя различным образом эти части, одинаковые по форме и размерам, мы имеем возможность строить машины для самых специальных целей.
Такое упрощение вопроса оборудования является основой нашей производственной программы.
Эта система проведена на всех наших предприятиях и заводах не только в отношении оборудования, но и в отношении приемов работы в мастерских. Все конвейеры, употребляемые в наших различных цехах, а также цепи, входящие в их состав, тщательно стандартизированы. Равным образом стандартизированы всевозможные материалы. Например, чертежи всегда имеют один и тот же формат и разные данные всегда указаны на том же месте листа, чтобы не терять времени на их разыскивание.
Серия книг, носящих название «Стандарты фордовских машин», содержит все нужные сведения и дает полную историю наших опытов, вплоть до мельчайших подробностей.
Книги эти, содействуя обучению новых работников, сберегли нам тысячи долларов, но главная их ценность заключается в том, что с их помощью нам удается поддерживать полную однородность производственных процессов на всех наших предприятиях.
Выгоды от стандартизации машин, инструментов и всех материалов весьма многочисленны. Машины изготовляются так же легко, как любые скобяные товары. При постройке стандартных машин и машин специального назначения достигается огромная экономия, и, если выработанный тип машины оказывается неудовлетворительным, главным ее частям можно дать другое назначение; тем самым оборудование наших заводов чрезвычайно упрощается.
Равным образом упрощается и облегчается поддержание в порядке машин и их ремонт; ежегодная экономия от такой организации производства чрезвычайно велика.
Единственный недостаток такой организации состоит в том, что при изменении стандарта приходится нести значительные расходы; но обычно эти издержки вполне окупаются теми усовершенствованиями, которые приносит с собою каждая перемена и которые идут на пользу потребителю наших автомобилей.
Мы многие годы стремились к тому, чтобы выработать наилучший тип автомобиля, и изготовляли каждую отдельную часть, исходя из следующих моментов: 1) крепость и легкость, 2) экономность производства, 3) внешний вид.
В 1925 году мы произвели некоторые изменения в нашем автомобиле, но мотора мы не трогали, ибо мотор - это сердце автомобиля; всего было сделано 88 изменений - больших и малых. Ни одно из них не делалось наобум, и новые типы автомобилей были подвергнуты испытаниям во всех частях страны в течение многих месяцев.
Когда мы решили произвести изменения, мы выработали точную программу их выполнения.
Мы назначили определенный срок, начиная с которого должны были вводиться изменения; плановое отделение нашего предприятия должно было высчитать точно наличие сырых материалов, необходимых для прежнего производства, чтобы, исчерпав весь материал, оно могло остановиться. Тем временем инженеры выполнили сотни чертежей для изготовления новых матриц и машин.
Таким образом, нам удалось провести необходимые изменения, почти не прерывая работу заводов; мы реорганизовали один отдел за другим, и лишь было произведено последнее изменение - новое производство пошло полным ходом.
Мы приведем несколько цифр, которые покажут, что значит произвести в изготовлении продукта 88 изменений.
Мы установили 4759 новых штампов и матриц и 4243 заново собранных машин. Рабочая сила обошлась нам в 5 682 387 долларов, а материалы - в 1 395 596 долларов. Установка новых печей для эмалирования на 13 наших заводах стоила 371 тысячу долларов и новое оборудование в 29 других отделениях - около 145 650 долларов.
В итоге эти изменения обошлись нам в более 8 миллионов долларов, не считая времени, потерянного для производства.
ТРАКТОР
Дата добавления: 2020-01-07; просмотров: 318; Мы поможем в написании вашей работы! |
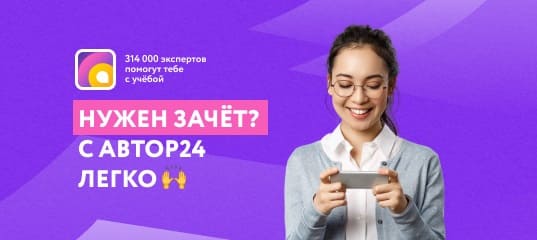
Мы поможем в написании ваших работ!