Термодинамика процесса гидрирования лигатуры Nd-Fe
Фазовая диаграмма состояния системы Nd-Fe представлена на рисунке 24.
Рисунок 24 - Фазовая диаграмма состояния системы Nd-Fe [126]
Из диаграммы видно, что при составе лигатуры 80 % неодима, железо остальное, материал будет представлен, в основном, фазами Nd2Fe17, Nd5Fe17 и эвтектикой состава 76,5 ат. % Nd, Fe – остальное. Вероятно, что, гидрированию будет сначала подвергаться обогащенная по неодиму и менее устойчивая эвтектика, а уже затем сами зерна.
Реакция гидрирования неодима при стандартных условиях экзотермическая. Энтальпия реакции ∆H составляет при 298 K -187,3 кДж/моль. Энергия Гиббса ∆G для гидрида неодима определяется по формуле:
, (28)
где R − универсальная газовая постоянная, 8,314 ;
T − абсолютная температура, K;
− давление диссоциации NdH2, Па,
определяется по формуле
. (29)
Зависимость значений энергии Гиббса ∆G от температуры показаны на рисунке 25.
Рисунок 25 − Зависимость значений энергии Гиббса ∆G процесса гидрирования лигатуры от температуры
Из рисунка следует, что процесс гидрирования теоретически вероятен до температуры 875 К. Так как реакция гидрирования экзотермична, сдвигать равновесие в сторону образования гидридов следует путем снижения температуры гидрирования.
|
|
Получение магнитных сплавов и лигатуры Nd-Fe
Исходным сырьем для получения магнитов на основе Nd-Fe-B являются сплавы, содержащие РЗМ, железо, легирующие добавки, которые получают следующими способами:
1) переплавом компонентов;
2) электролитическим методом;
3) металлотермическим печным или внепечным восстановлением;
4) фторидной технологией.
Плавку индивидуальных компонентов сплавов проводят в вакууме или инертной среде в индукционных, электродуговых печах [128,129]. В первом из методов сплав получают переплавкой исходных материалов в индукционной печи в корундовом тигле, герметично закрытом гильзой из железа. Во втором, для равномерного распределения компонентов предлагают плавку смеси материалов вести в тигле с последующим сливом сплава в изложницу. В третьем, предложен тигель для плавки магнитных сплавов, поверхность которого до 90% обогащена оксидами тяжелых РЗМ (Dy или Tb), которые при индукционной плавке частично восстанавливаются и попадают в сплав. Получение сплавов на основе Nd-Fe-B в большинстве случаев в промышленности осуществляют в инертной атмосфере индукционным способом, обеспечивающем хорошее перемешивание. РЗМ вводят после расплавления остальных компонентов в жидкий расплав. Для получения сплавов со столбчатой структурой, обладающих ярко выраженными анизотропными свойствами, используют охлаждение в массивных или в охлаждаемых кристаллизаторах. Бор вводят в расплав либо в виде чистого металла, либо в виде ферробора Fe-B с различным содержанием бора.
|
|
Методы плавки и литья являются двустадийными – первоначально получают отдельные компоненты в виде металлов или лигатур, а затем переплавляют эти полупродукты с целью получения сплавов Nd-Fe-B различного состава. Индивидуальные РЗМ получают либо методом печной металлотермии при нагревании исходной шихты, состоящей из фторидов, хлоридов или оксидов РЗМ и металла – восстановителя (чаще всего кальция или гидрида кальция), до температур 800-1200 0С [130], либо путем электролиза в основном галогенидов при температуре 800-1200 0С [64]. Для получения из этих металлов магнитных сплавов требуется их предварительная очистка от примесей, например, электрорафинированием или переплавом в вакууме в индукционных, дуговых, электронно-лучевых, плазменно-индукционных печей или других типов печей. Кроме дополнительной затраты электроэнергии данные процессы осложняются трудностью выбора конструкционных материалов для плавки и литья РЗМ из-за их чрезвычайной химической активности и значительных потерь РЗМ по причине высокого давления паров этих металлов при температурах 1300-1500 0С.
|
|
Электролитические способы производства РЗМ и магнитных сплавов основаны на электролизе либо фторидов, либо оксидов, либо смеси фторидов и хлоридов РЗМ [131]. В качестве солевой ванны служат расплавы фторидов или хлоридов щелочных и щелочноземельных металлов (Li, Ca, Ba и т.д.). Обычно в качестве катода используется железо, а анода - уголь. Процесс ведут при температурах 650-1100 0С. Основными недостатками этих способов являются малый выход по току (~ 65-70 %), значительные энерге-тические затраты и необходимость рафинирования сплавов.
Более экономичным, чем вышерассмотренные, является прямой металлотермический способ получения магнитных сплавов, в котором отсутствуют дорогостоящие стадии получения и рафинирования РЗМ. Металлотермическому восстановлению подвергают оксиды и концентраты оксидов, смеси галогенидов и оксидов, хлориды, фториды РЗМ [105]. Переходные и легирующие элементы (Fe, Co и др.) вводят в шихту для металлотермического восстановления в виде металлического порошка, ферробора, оксида. В качестве восстановителя соединений РЗМ, переходных металлов и бора используют металлический кальций, магний или их смеси, гидрид кальция или смесь гидрида кальция и металлического кальция, щелочные металлы – литий, натрий [106].
|
|
Большинство из этих процессов являются печными, т.е. тепла, выделяющегося при протекании реакций восстановления соединений РЗМ и переходных металлов недостаточно для расплавления всех продуктов реакции и формирования слитков сплавов лигатур, поэтому восстановление проводят при нагревании шихты до температур 800-1300 0С. Для снижения температуры плавления и увеличения жидкотекучести шлаков в шихту предлагается вводить хлорид кальция, а для увеличения масштаба плавки – прессовать шихту.
В ряде работ после восстановительной плавки проводят для удаления α-Fe и повышения содержания магнитной фазы РЗ2-Fe14-B гомо-генизирующий отжиг сплава путем выдержки в течение 5-24 ч при температурах 750-1300 0С, а после чего медленное со скоростью 0,3-5 0С/мин охлаждение от 600 0С до комнатной температуры. Гомогенизирующий отжиг проводят в среде инертного газа, или в восстановительной водородной среде. Вследствие совмещения процессов восстановления и диффузионного получения основной магнитной фазы эти процессы называют восстановительно-диффузионными. Термичность шихты можно увеличить введением переходных металлов (Fe, Co) в виде оксидов, хлоридов, что позволяет проводить процессы внепечным способом [128,129].
Фториды и хлориды РЗМ получают осаждением их из растворов плавиковой или соляной кислотой с последующей сушкой и прокалкой осадков. Эти процессы не позволяют полностью удалить из продуктов влагу и, вследствие этого, на операциях восстановления выход РЗМ в слиток не превышает 80-85 % [128].
Недостатками рассмотренных выше методов прямого металлотермического получения сплавов являются:
- недостаточность тепла реакции для формирования слитков сплавов и необходимость подогрева системы в печи при использовании переходных и РЗ металлов в виде оксидов;
- высокая гигроскопичность и трудность получения безводных соединений при использовании хлоридов металлов;
- наличие остаточной влаги и гидроксильной группы при использовании фторидов, полученных по “мокрой” схеме;
- трудности переработки шлаков из-за их сложного состава при применении соединений РЗМ и переходных металлов в виде оксидов, хлоридов, фторидов совместно.
В Северской государственной технологической академии совместно с Сибирским химическим комбинатом разработана принципиально новая, экологически безопасная, малоотходная фторидная технология получения магнитных материалов на основе РЗМ, включающая получение фторидов РЗ и переходных металлов с использованием элементного фтора; внепечное кальцитермическое восстановление этих фторидов для получения сплавов для изготовления высокоэнергетических постоянных магнитов, а так же переработку образующихся по этой технологии различных отходов [132].
Основные её достоинства:
· универсальность газообразного фтора как фторирующего агента, заключающаяся в возможности применения его для переработки практически любого вида сырья: оксидов, металлов, концентратов и отходов, содержащих РЗЭ;
· высокая интенсивность процесса;
· уникальность физико-химических свойств фторидов, получающихся по этой технологии, что позволяет в большинстве случаев работать с ними в атмосферных условиях;
· возможность легирования магнитных сплавов в процессе внепечного восстановления любыми компонентами;
· возможность использования большого научного и производственного опытов, накопленных в атомной промышленности;
· экологические достоинства, основанные на коротких, малоотходных схемах, связанных с отсутствием в основном жидких отходов и с возможностью регенерации фтора.
Исходное сырьё (оксиды, концентраты, отходы производства и т. д.) подаётся в реактор на фторирование. Отходящие газы на этой стадии улавливаются на оксидах и возвращаются на повторное фторирование. Далее готовится шихта смешиванием полученных фторидов с восстановителями (Са, Mg, Al) и компонентами сплава (Fe, B, Co и др.), которая отправляется на внепечное металлотермическое восстановление. Полученные слитки идут на получение магнитов, а шлак перерабатывается. Выделенные из него фтор и ценные компоненты направляют на повторное использование.
Получение высоконеодимого сплава Nd-Fe с содержанием неодима (75-80) % мас. проводилось по фторидной технологии на ХМЗ СХК, представленной на рисунке 7. Тепла химической реакции достаточно для получения компактного слитка:
NdF3 + nFeF3 + 1,5(n+1)Ca → NdFen + 1,5(n+1)CaF2 , (30)
NdF3 + nFeF3 + gB + mFe + 1,5(n+1)Ca → NdFe(n+m)Bg + 1,5(n+1)CaF2. (31)
Было проведено три серии ВП по 8-10 операций в каждой с 4 кг загрузкой по металлу и использованием фторидов одинакового качества (a = 94-98 %). Средний выход сплава в слиток составил 93,7; 94,0 и 97,3 %, в тиглях с засыпкой из фторида кальция толщиной 10 мм по схемам, представленным на рисунке 26. Во всех экспериментах давление в реакторе не превышало 0,1 МПа. Особенностью этих операций было то, что сразу же после проведения процесса после оседания и расслаивания системы на сплав и шлак верхняя часть футеровки осыпалась, изолируя при этом верхнюю часть шлака. Это обеспечивало получение сплава с выходом не ниже 94 %, а в случае, представленном на рисунке 27 - 97,3 %. Поэтому во всех последующих операциях конструкция металлоприёмника тигля была принята цилиндрической. На рисунке 26 изображены тигли из силицированного графита и Ст.3 с засыпной футеровкой, в которых проводились опытные и производственные операции получения магнитных сплавов. В этих опытах отрабатывались условия подготовки тигля к восстановлению, а также варьировались толщина и материал футеровки, обеспечивающие получение высококачественного материала с высоким выходом в слиток. В качестве материала футеровки использовались CaF2 марки ч.д.а., плавиковый шпат, используемый для получения элементного фтора, MgO и другие материалы. Подробно подготовка тигля к работе, а также характеристики материалов, используемых для футеровки, описаны в работе [80]. Для получения сплава 80 % Nd – 20 % Fe массой 4 кг использовались фториды железа и неодима со степенью фторирования 94-96 % и 97-98 %, соответственно. Начальное избыточное давление аргона в реакторе поддерживалось на уровне 0,01 МПа, а конечное не превышало во всех операциях 0,08-0,11 МПа. Полученные данные сведены в таблицу 6.
Рисунок 26 – Схемы тиглей с засыпной футеровкой
1 – воронка; 2 – стакан с крышкой из Ст. 3; 3 – СГТ; 4 – футеровка; 5 – шихта; 6 – тигель из Ст. 3; 7 – реактор.
Рисунок 27 – Схема тигля с засыпной футеровкой
Таблица 6 – Результаты опытных операций получения сплава 80 % Nd – 20 % Fe в тиглях с засыпной футеровкой
№ опыта | aВП,% | Результаты химического анализа, % | aВ, % | Материал и толщина слоя футеровки, мм | |||
Nd | Pr | Fe | РЗF3 | FeF3 | |||
1 | 90,9 | 76,0 | 1,5 | 21,8 | 88,1 | 99,2 | 0 |
2 | 92,6 | 76,8 | 0,6 | 22,0 | 89,6 | 101,9 | CaF2/5 |
3 | 91,1 | 76,2 | 1,3 | 22,1 | 88,3 | 101,6 | MgO/5 |
4 | 96,8 | 79,5 | 0,5 | 20,5 | 97,0 | 99,3 | CaF2/10 |
5 | 98,5 | 79,4 | 0,4 | 20,2 | 98,3 | 99,5 | CaF2/12-15 |
6 | 98,4 | 79,2 | 0,6 | 20,2 | 98,2 | 99,4 | Шпат/12-15 |
7 | 98,5 | 79,3 | 0,5 | 20,1 | 98,3 | 99,3 | Шпат/12-15 |
8 | 90,8 | 75,0 | 2,0 | 22,0 | 87,4 | 99,8 | CaO/5 |
9 | 92,0 | 77,0 | 0,5 | 21,5 | 89,1 | 98,9 | CaCl2/10 |
10 | 93,8 | 77,2 | 1,7 | 21,2 | 92,5 | 99,4 | AlF3/10 |
11 | 92,8 | 78,1 | 0,2 | 21,1 | 90,8 | 99,3 | Al2O3/10 |
Примечания – 1. В опытах 8-11 загрузка шихты проводилась непосредственно на дно тигля с коническим металлоприёмником. 2. Содержание углерода и кремния во всех сплавах, полученных в опытах 2-7, не превышало 0,01 %. 3. Толщина слоя футеровки d в опытах 2-7 была одинаковой как на дне, так и на боковой поверхности тигля. 4. Шпат, используемый для футеровки в опытах 6 и 7, был предварительно прокален при температуре 800-900 °С. |
Из данных, представленных в таблице 6, следует, что с помощью 10 мм слоя футеровки дна тигля удается увеличить выход сплава в слиток на 2-4 % за счет снижения теплопотерь, но не удается устранить "привары" сплава к тиглю, а так же другие вышеперечисленные недостатки для СГТ.
С нанесением же и увеличением толщины футеровки, как дна, так и боковой поверхности тигля до 12-15 мм эти недостатки устраняются при росте выхода сплава в слиток и степени восстановления РЗМ. Так, если футеровка тигля отсутствует, то выход сплава в слиток составляет всего 90,9%, а если футеровка существует, и ее толщина соответственно увеличивается, то увеличивается и выход сплава в слиток. Причем, если толщина футеровки достигает 10-15 мм, то степень восстановления соеди-нений РЗМ практически совпадают со степенью фторирования соединений РЗМ и химический состав получаемых сплавов близок к заданному. Результаты исследований также свидетельствуют о том, что показатели ВП, полученные в футерованных тиглях из СГ и Ст.3 практически одинаковы. Поэтому, в производственных условиях можно для получения сплавов использовать и те, и другие тигли. Преимуществом металлических тиглей является их меньшая на 3-4 кг масса, объем и, как следствие, возможность увеличение масштаба плавки на 0,5-1,0 кг, а так же возможность их многократного использования.
Для футеровки тиглей можно применять плавиковый шпат марок ФФ-95 и ФФ-92 (ГОСТ 7618-83). Последний является значительно более дешевым материалом, однако требует предварительной подготовки – прокалки при температуре 850-900 °С, поскольку по данным сертификата он имеет следующий состав: CaF2 – 93-96 %, SiO2 – 1,4 %, CaCO3 – 1,6-3,0 %, S < 0,2 %, P< 0,06 %, H2O < 1,0 % мас. Сушка и прокалка шпата необходимы для снижения содержания S, P, удаления влаги и разложения карбоната по реакции
СaCO3 = CaO + CO2 . (32)
В качестве материала можно использовать и шлак от ВП после его измельчения до крупности 0,1-0,2 мм и прокалки до 500-600°С. В отличие от плавикового шпата шлак даже после прокалки необходимо хранить в герметичной таре, ибо наличие в шлаке до 10-15 % СаО будет приводить к его увлажнению на воздухе за счет взаимодействия его с влагой атмосферы. Возможно также использование и других материалов для создания футеровки (оксидов алюминия, кальция, бария, стронция и т.д.). Однако, в этих случаях могут появиться проблемы при переработке шлаков с целью извлечения фтора. Необходимо отметить, что в сплавах, полученных в тиглях с футеровкой, уровень загрязнения Si и C значительно ниже (£ 0,01 %), "прихватов" ни боковой, ни нижней поверхностью слитка к тиглю не происходит, нет проблем и с извлечением слитка из тигля. Шлак и слиток при опрокидывании тигля легко из него извлекаются. При 12-15 мм толщине футеровки в процессе проведения плавки только 5-6 мм ее спекается и частично проплавляется, превращаясь в монолит, а остальная же часть остается в виде порошка и ее можно использовать в футеровке повторно. В тиглях с футеровкой увеличивается в 2-3 раза время отвода теплоты перегрева и кристаллизации продуктов ВП по сравнению с тиглями без нее, и это позволяет значительно увеличить выход сплава в слиток. При такой конструкции сроки эксплуатации тиглей как металлических, так и СГ становятся практически неограниченными, так как на них не действуют термоудары, и они непосредственно не взаимодействуют с расплавами шлака и металла.
Таким образом, на основании проведённых исследований было установлено, что в тиглях (СГ и Ст.3) с засыпной футеровкой из CaF2 возможно получение высоконеодимового сплава Nd-Fe с выходом не менее 98-99% мас.
Полученный таким образом в виде слитка высоконеодимовый сплав представляет собой очень прочный материал, трудно поддающийся механическому измельчению. Её состав − 80% неодима, оставшиеся 20% − железо. Плотность сплава составляет 7,18 – 7,20 г/см3.
Из-за наличия в технологических процессах различных факторов, влияющих на состав и качество получаемых сплавов, таких как нестабильность состава исходных фторидов, колебания атмосферной влажности, ошибки технологического персонала в процессе получения магнитных сплавов и т.д., неизбежно образуются некондиционные слитки сплавов, в частности, например, с низким содержанием РЗМ. Исправить химический состав возможно, не нарушая технологический процесс, например, отправив его на индукционный переплав, что экономически не выгодно, а также на стадии измельчения сплава, путем введения необходимых легирующих добавок. Такой метод получил название “твердофазное легирование”. Идеальным вариантом было бы введение легирующих добавок на стадии помола в виде порошков, однако это не представляется возможным, т.к. механически высоконеодимовый сплав Nd(80%) - Fe(20 %) измельчить затруднительно. Даже, если бы это и получилось, работы с этим порошком из-за их высокой химической активности не возможна.
Из этого затруднительного положения есть выход и он предлагается в данной работе: использовать вместо гипотетического порошка Nd-Fe порошок его соединения с водородом. В результате могут быть решены одновременно две проблемы:
первая – эти гидриды как и гидриды сплава Nd2Fe14B должны легко измельчаться; и вторая — порошки гидридов должны быть менее активны в атмосферных условиях, чем мелкоизмельчённые порошки этого сплава.
Таким образом, использование метода твёрдофазного легирования позволит исключить дорогостоящую операцию переплава некондиционных слитков, а также, при необходимости, позволяет скорректировать состав серийных магнитных сплавов.
Дата добавления: 2020-01-07; просмотров: 491; Мы поможем в написании вашей работы! |
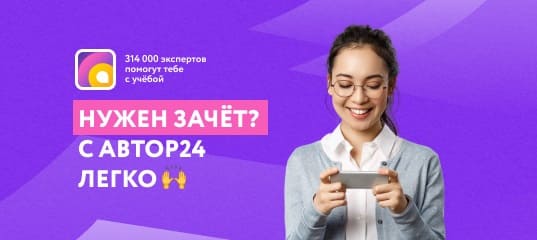
Мы поможем в написании ваших работ!