Из Инструкции по ремонту и обслуживанию автосцепного устройства подвижного состава железных дорог
(утверждена МПС России 16 сентября 1997 г. № ЦВ-ВНИИЖТ-494)
2.8.3. Разница между высотами осей автосцепок по обоим концам вагона, тепловоза или электровоза (одной секции), вагона электро- или дизель-поезда при выпуске из капитального ремонта должна быть не более 15 мм, а при выпуске из других видов ремонта должна быть не более 20 мм (для грузового вагона — не более 25 мм).
2.8.4. Положение автосцепки относительно горизонтали определяют по разности между значениями ее высоты от головок рельсов до литейного шва, измеренной в двух местах: по линии зацепления и у входа хвостовика в ударную розетку. Отклонение автосцепки вниз (провисание) допускается у вагонов и локомотивов he более чем на 10 мм, а отклонение вверх — не более чем на 3 мм.
У вагонов моторвагонного подвижного состава провисание допускается не более чем на 3 мм, а отклонение вверх — не более чем на 5 мм.
141
Таблица 2.2.
Подвижной состав | Высота оси автосцепки над головками рельсов, мм, при выпуске из ремонта | |
капитального | вагонов из деповского; тепловозов, электровозов и вагонов электро- и дизель-поездов из текущих ТР-2, ТР-3, паровозов из подъемочного | |
Грузовые вагоны | 1080—1020 | 1080—1000 |
Пассажирские вагоны на тележках: | ||
КВЗ-5, КВЗ-ЦНИИ | 1080—1030 | 1080—1020 |
остальных типов | 1080—1020 | 1080—1010 |
Рефрижераторные вагоны | 1080—1030 | 1080—1020 |
Электровозы | 1080—1000 | 1080—990 |
Тепловозы, паровозы, тендеры, дизель-поезда серий Д1, ДР1 | 1080—1020 | 1080—1010 |
Вагоны электропоездов серий Сд, Ср,С. | 1167—1097 | 1167—1090 |
Вагоны электропоездов остальных серий: | ||
промежуточные | 1160—1090 | 1160—1080 |
головные | 1070—1000 | 1070—990 |
Примечание: у паровозов и тендеров с полным запасом воды и топлива при выпуске из ремонта высота автосцепки допускается не менее 990 мм.
|
|
2.8.5. При центрирующем приборе с маятниковым подвешиванием
зазор между верхней плоскостью хвостовика и потолком ударной розет
ки на расстоянии 15—20 мм от наружной ее кромки должен быть не
мене 25 мм и не более 40 мм, а между этой же плоскостью хвостовика
и верхней кромкой окна в концевой балке — не менее 20 мм.
При центрирующем приборе с подпружиненной опорой для хвостовика автосцепки указанный зазор не контролируется.
2.8.6. Автосцепка должна свободно перемещаться из среднего положения в крайнее от усилия, приложенного человеком и возвращаться обратно под действием собственного веса. Проверку этого требования выполняют, когда аппарат плотно прилегает дном корпуса к задним упорам и через упорную плиту к передним упорам.
2.8.7. Длина цепи расцепного привода должна быть отрегулирована. Рукоятка расцепного рычага должна укладываться на полочку фик-
|
|
142
сирующего кронштейна так, чтобы нижняя часть замка не выступала наружу от вертикальной стенки зева.
Перед регулированием длины цепи предварительно проверяют длину короткого плеча рычага от оси стержня от центра отверстия, которая должна составлять 190+10 мм.
3. Наружный осмотр.
3.2. При наружном осмотре необходимо проверить:
а) действие механизма автосцепки;
б) износ тяговых и ударных поверхностей большого и малого зубь
ев, ширину зева корпуса, состояние рабочих поверхностей замка;
в) состояние корпуса автосцепки, тягового хомута и других деталей
автосцепного устройства (наличие в них трещин и изгибов);
г) состояние расцепного привода и крепление валика подъемника
автосцепки;
д) крепление клина тягового хомута;
е) прилегание поглощающего аппарата к упорной плите и задним
упорным угольникам (упору);
ж) зазор между хвостовиком автосцепки и потолком ударной ро
зетки;
з) зазор между хвостовиком автосцепки и верхней кромкой окна в
концевой балке;
и) высоту продольной оси автосцепки пассажирских вагонов от головок рельсов;
к) положение продольной оси автосцепки относительно горизонтали;
|
|
л) состояние валика, болтов, пружин и креплений паровозной розетки.
В случае выявления неисправности действия механизма автосцепки, а также при единой технической ревизии пассажирских вагонов механизм автосцепки разбирают, карманы корпуса осматривают, при необходимости очищают, неисправные детали заменяют исправными и после сборки проверяют действие механизма в установленном порядке.
3.3. Пе разрешается выпускать подвижной состав в эксплуатацию
при наличии хотя бы одной из следующих неисправностей:
а) автосцепка не отвечает требованиям проверки комбинированным
шаблоном 940р;
б) детали автосцепного устройства с трещинами;
в) разница между высотами автосцепок по обоим концам вагона
более 23 мм, провисание автосцепки подвижного состава более 10 мм;
высота оси автосцепки пассажирских вагонов от головок рельсов бо-
143
лее 1080 мм и менее 1010 мм у вагонов на тележках КВЗ-5, КВЗ-ЦНИИ и менее 1000 мм на тележках остальных типов;
г) цепь расцепного привода длиной более или менее допустимой;
цепь с незаваренными звеньями или надрывами в них;
д) зазор между хвостовиком автосцепки и потолком ударной розет
ки менее 25 мм; зазор между хвостовиком и верхней кромкой окна в
концевой балке менее 20 мм (при жесткой опоре хвостовика);
|
|
е) замок автосцепки, отстоящий от наружной вертикальной кромки
малого зуба более чем на 8 мм или менее чем на 1 мм; лапа замкодер-
жателя, отстоящая от кромки замка менее чем на 16 мм (у замкодержа-
телей, не имеющих скоса — менее чем на 5 мм);
ж) валик подъемника заедает при вращении или закреплен нетипо
вым способом;
з) толщина перемычки хвостовика автосцепки, устанавливаемой
вместо неисправной на вагон, выпускаемый из текущего отцепочного
ремонта, менее 48 мм;
и) поглощающий аппарат не прилегает плотно через упорную плиту к передним упорам (для аппарата 73ZW допускается наличие суммарного зазора между передним упором и упорной плитой или корпусом аппарата и задним упором до 5 мм);
к) упорные угольники, передние и задние упоры с ослабленными заклепками;
л) планка, поддерживающая тяговый хомут, толщиной менее 14 мм, либо укрепленная болтами диаметром менее 22 мм, либо без контргаек и шплинтов на болтах (допускается крепление поддерживающей планки болтами диаметром 20 мм, но в количестве 10 шт.);
м) нетиповое крепление клина (валика) тягового хомута;
н) неправильно поставленные маятниковые подвески центрирующего прибора (широкими головками вниз);
о) ограничительный кронштейн автосцепки с трещиной в любом месте, износом горизонтальной полки или изгибом более 5 мм;
п) отсутствие предохранительного крюка у паровозной автосцепки; валик розетки, закрепленный нетиповым способом; ослабшие болты розетки; болты без шплинтов или со шплинтами, не проходящими через прорези корончатых гаек.
3.4. Порядок проверки автосцепки комбинированным шаблоном 940р:
а) проверка исправности действия предохранителя замка. Прикладывают шаблон и одновременно нажимают рукой на замок, пробуя втолкнуть его в карман корпуса автосцепки. Уход замка полностью в карман корпуса указывает на неправильное действие предохранителя
144
замка. Если предохранитель действует правильно (верхнее его плечо упирается в противовес замкодержателя путем нажатия на лапу ребром комбинированного шаблона), то замок должен уходить от кромки малого зуба автосцепки не менее чем на 7 мм и не более чем на 18 мм (измеряют в верхней части замка);
б) проверка действия механизма на удержание замка в расцеплен
ном положении. Шаблон прикладывают, затем поворотом до отказа
валика подъемка уводят замок внутрь полости кармана и освобождают
валик, продолжая удерживать шаблон в зеве автосцепки. Если замок
опускается обратно вниз, значит механизм неисправен;
в) выявление возможности преждевременного включения предо
хранителя замка при сцеплении автосцепок. Шаблон устанавливают
так, чтобы его откидная скоба стороной с вырезом 35 мм нажимала на
лапу замкодержателя, а лист шаблона касался большого зуба. Авто
сцепка считается годной, если при нажатии на замок он беспрепятст
венно уходит в карман на весь свой ход;
г) проверка толщины замыкающей части замка. Прикладывают
шаблон. Если шаблон одновременно прилегает к боковым сторонам
малого зуба и замка, значит замок негоден (тонок);
д) проверка ширины зева автосцепки (без замка). Шаблон прикла
дывают одним концом к углу малого зуба, а другим подводят к носу
большого зуба. Если шаблон проходит мимо носка большого зуба в
зев, то корпус автосцепки негоден. Проверка производится по всей
высоте носка большого зуба;
е) проверка износа малого зуба. Прикладывают шаблон. Если шаб
лон соприкасался с боковой стенкой малого зуба, то автосцепка негод
на. Проверку выполняют на расстоянии 80 мм вверх и вниз от про
дольной оси корпуса;
ж) проверка износа тяговой поверхности большого зуба и ударной
поверхности зева. Шаблон устанавливают. Если шаблон входит в зев,
то автосцепка негодна. Проверку выполняют в средней части большо
го зуба по высоте на 80 мм вверх и вниз от середины (проверка боль
шого зуба против окна для лапы замкодержателя не производится).
Дата добавления: 2019-07-17; просмотров: 562; Мы поможем в написании вашей работы! |
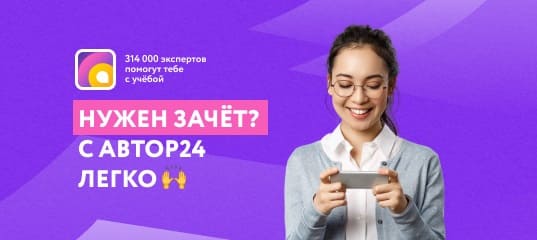
Мы поможем в написании ваших работ!