Тема 16 Ремонт механизма газораспредления.
Ремонт топливной аппаратуры
Основные детали механизма газораспределения. Выкрашивание рабочих поверхностей. Допускаемая выработка рабочей поверхности. Снятие кулачковых шайб. Восстановление линейных размеров валов. Дефектация и ремонт клапанов.
Особенность дефектации, ремонта и сборки топливной аппаратуры. Сборка плунжерных пар распылителей форсунок. Дефектация. Ремонт форсунок. Опрессовка.
Методические рекомендации
Ремонт механизма газораспределения
К основным деталям механизма газораспределения относятся: распределительный вал, кулачковые шайбы, клапаны.
При эксплуатации распределительных валов выкрашиваются рабочие поверхности кулачковых шайб, искажается профиль шайб, возникают трещины на поверхностях самого вала, биение шеек относительно оси вала, происходит смятие шпоночных пазов и искривление оси вала.
Наиболее сложная операция при ремонте распределительных валов – снятие кулачковых шайб, которые, как правило, при КР дизелей меняют.
Восстановление линейных размеров валов, а также форм поверхностей осуществляют обычными способами станочной обработки на ремонтные размеры или одним из способов применяемых при ремонте коленчатых валов.
При работе дизеля изнашиваются детали клапанного комплекта.
При ремонте клапанов удаляют наклеп и выгорания на уплотнительной фаске тарелки, восстанавливают стержень клапана на номинальный размер, наращивая металл хромированием или гальваническим осталиванием, восстанавливают изношенную коническую фаску у тарелки наплавкой или напылением с последующим ее протачиванием, шлифованием и притиркой.
|
|
Клапаны притирают ручным или механизированным способом.
При СР и КР дизеля клапанные комплекты обычно заменяют новыми.
Ремонт топливной аппаратуры
Ремонт форсунок включает следующие основные технологические операции:
1) снятие нагара с распылителей форсунок и проверку качества распыливания топлива, а также давления начала впрыскивания до разборки;
2) разборку, промывку, дефектацию и ремонт деталей плунжерных пар;
3) сборку, регулировку давления начала впрыскивания и проверку качества распыливания топлива;
4) обкатку и проверку качества распыливания топлива после регулировки топливного насоса.
Замену деталей одной форсунки деталями другой не допускают.
Вопросы для самоконтроля
1. Перечислите основные дефекты механизма газораспределения.
2. Из каких сталей изготавливают впускные клапаны? Как производится их дефектация?
3. Как производят сборку плунжерных пар распылителей форсунок?
4. Перечислите основные технологические операции при ремонте форсунок.
|
|
Литература: [2], с. 44-81; [6], с. 299-314; [8], с. 94-99.
Тема 17 Сборка и центровка деталей ДВС
Типовая схема сборки ДВС. Последовательность и основные положения. Особенности сборки фундаментных рам и станин. Центровка. Методы проверки.
Требования при установке блоков цилиндров. Проверка перпендикулярности.
Последовательность запрессовки втулок. Правила запрессовки. Гидравлические испытания. Установка цилиндровых крышек.
Особенности сборки привода газораспределения.
Сборка коленчатых валов с коренными подшипниками.
Методические рекомендации
Сборка судовых ДВС в цеховых условиях осуществляется на сборочном стенде. Ее порядок определяется конструкцией дизеля, но типовая схема сборки – одна для всех ДВС.
При изучении темы следует обратить внимание на использование измерительных приборов; качество деталей и их обработку перед сборкой; требования к затяжке резьбовых соединений.
Фундаментные рамы и станины мощных дизелей при ремонте демонтируют редко. Центровка рам производится по методу реперных линий. Кроме этого, применяются также оптические методы.
При установке блоков цилиндров необходимо обеспечить перпендикулярность и пересечение осей цилиндров с осью коленчатого вала. Центровка производится методом натянутых струн.
|
|
Втулки запрессовываются после установки и закрепления блоков.
Основное условие при запрессовке втулок – обеспечение их перемещения без перекоса с помощью винтовых и гидравлических домкратов.
Гидравлические испытания полости охлаждения проводят при давлении 0,4...0,6 МПа. Пропуски воды через уплотнения не допускаются.
Сборка привода газораспределения производится после укладки распределительного вала. Требования к укладке вала и пригонке его подшипников такие же, как и для коренных подшипников коленчатого вала. Приводы распределительного вала выполняются шестеренными и цепными.
Под сборкой коленчатых валов дизелей с коренными подшипниками понимают комплекс технологических операций, связанных с обеспечением и проверкой заданной точности взаимного расположения этих деталей. В специальной и технической литературе такой комплекс работ часто называют укладкой коленчатых валов в подшипники.
Основная задача технологической операции укладки коленчатого вала в коренные подшипники независимо от того, каким методом обеспечивают заданную точность сборки, сводится к удовлетворению следующих технических требований:
|
|
плотного прилегания наружной поверхности вкладышей подшипников к постелям фундаментной рамы и заданного по рабочей документации натяга; возможно более полного (не менее 70%) контакта между рабочими
поверхностями шеек коленчатого вала и вкладышей подшипников; прямолинейности оси коленчатого вала, уложенного в коренные подшипники; оптимального монтажного зазора между шейками вала и вкладышами коренных и шатунных подшипников.
Вопросы для самоконтроля
1. Опишите порядок сборки судовых ДВС.
2. Опишите метод центровки блоков цилиндров.
3. Как производится запрессовка цилиндровых втулок?
4. Перечислите основные технические требования при укладке коленчатого вала в коренные подшипники.
5. Как контролируют качество прилегания наружной поверхности вкладышей подшипников к постелям фундаментной рамы и коренных шеек коленчатых валов к антифрикционному покрытию вкладышей?
Литература: [2], с. 231-236; [6], с. 389-409; [8], с. 99-105.
Тема 18 Ремонт валопровода
Износы, повреждения и дефектация валопроводов. Разборка валопровода. Способы снятия гребного винта. Снятие гребного вала, дейдвудных втулок. Ремонт деталей валопровода (валы, дейдвудные устройства, подшипики).
Методические рекомендации
В процессе эксплуатации судна валопровод и его отдельные детали подвергаются износу и различным повреждениям: неравномерное истирание, наработки, задиры трущихся поверхностей, трещины, прогибы и поломки валов, деформация соединительных болтов, кавитационный и коррозионный износы.
Причины возникающих дефектов валопровода: неточность при монтаже, неправильная центровка, изгиб корпуса судна, посадка на мель, неправильная нагрузка, постановка неотбалансированного винта и т.д.
Разбирают валопровод на плаву с дифферентованием судна, выморозкой в зимний период, в доке, на слипе и в кессоне. Начинают разборку валопровода с отсоединения коротыша, затем снимают крышки опорных подшипников и разбирают упорные подшипники. После этого раздвигают промежуточные валы с помощью стропов и талей.
Гребной вал вынимается после снятия движителя, затем выпрессовывают дейдвудные втулки и вкладыш подшипника гребного вала (кронштейна).
Вопросы для самоконтроля
1. Как производят дефектацию валопровода?
2. Опишите разборку валопровода.
3. Как восстанавливают изношенные шейки вала и шпоночные гнезда?
4. В чем заключается ремонт дейдвудной втулки? Подшипников?
Литература: [2], с. 125-127; [6], с. 18-23; [8], с. 105-108.
Дата добавления: 2019-07-15; просмотров: 528; Мы поможем в написании вашей работы! |
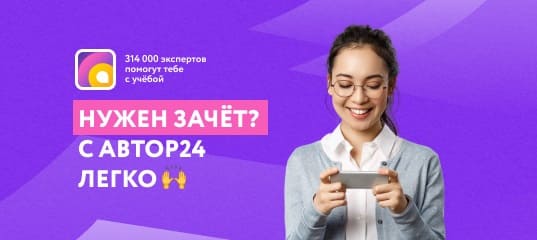
Мы поможем в написании ваших работ!