Тема 6 Дефектация машин, механизмов и конструкций
Основное назначение дефектации деталей. Разделение деталей по результатам дефектации. Методы дефектации, их применение.
Методические рекомендации
Основное назначение дефектации деталей при ремонте состоит в том, чтобы оценить фактическое техническое состояние этих деталей, выявить их износы и повреждения. Для этого все детали делят на группы:
детали остова – фундаментная рама, блок цилиндров, крышка цилиндров; детали цилиндро-поршневой группы (ЦПГ) – поршень, втулка, поршневой палец, шатун, поршневые кольца; детали валовой группы – коленчатый вал, рамовые и шатунные подшипники; детали механизма газораспределения – распределительный вал, клапаны, толкатели, коромысла, пружины; детали топливной аппаратуры и дистанционно-автоматического управления (ДАУ).
По результатам дефектации выделяют детали:
· пригодные для дальнейшей эксплуатации без ремонта;
· подлежащие ремонту;
· не подлежащие ремонту и направляемые в металлолом.
Различают визуальные и инструментально-приборные методы дефектации.
Методы определения различных дефектов:
· Косвенные методы оценки технического состояния машин и механизмов;
· теплотехнические испытания;
· статистические методы;
· визуальный осмотр;
· исследования структуры металлов и сплавов;
· механические испытания;
· химический анализ проб, травление поверхности растворами кислот;
|
|
· обмер деталей;
· исследование продуктов изнашивания;
· контроль на непроницаемость;
· испытания на коррозию;
· капиллярные методы;
· испытания фильтрующимися частицами;
· магнитные методы;
· контроль вихревыми токами;
· метод электросопротивления;
· трибоэлектрический метод;
· метод теплопроводности;
· электростатический порошковый контроль;
· термоэлектрический метод;
· контроль проникающим излучением;
· акустические методы контроля;
· поляризационный метод;
· измерение деформаций датчиками;
· метод хрупких покрытий;
· радиотехнический метод.
Вопросы для самоконтроля
1. Основное назначение дефектации.
2. Какие дефекты выявляют при визуальном методе дефектации? При инструментально-приборном?
3. Какие методы неразрушающего контроля Вам известны?
4. Опишите магнитные методы контроля. Какие дефекты они позволяют обнаружить?
5. Что такое трибоэлектрический метод контроля?
6. Опишите акустические методы контроля.
Литература: [2], с. 93-129; [6], с. 23-39; [8], с. 36-42.
Тема 7 У прочнение деталей
Способы и технологии нанесения покрытий. Причины ограничения использования процессов упрочнения. Комбинированные способы. Базовые способы. Особенности поверхностного упрочнения. Основные направления повышения прочности металлов. Эпитаксия. Композиционные покрытия. Пластичное деформирование.
|
|
Плазменное напыление покрытий. Детонационное напыление. Технологические факторы и условия нанесения покрытий. Достоинства и недостатки. Материалы покрытий. Поверхностное легирование. Лазерное легирование.
Методические рекомендации
Применение процессов упрочняющей технологии позволяет повысить ресурс и надёжность продукции машиностроения, обеспечить работоспособность деталей в самых жестких условиях эксплуатации, при высоких температурах, в агрессивных средах (в морской среде), при действии динамических и контактных нагрузок
Разработаны новые способы и технологии нанесения покрытий в частности, многослойных и многокомпонентных; получили развитие методы поверхностного легирования и упрочнения лазером, электронным лучом, электрическим искровым разрядом, совершенствуются способы и процессы поверхностного и пластичного деформирования, плазменного напыления, нанесения покрытия с помощью плазмотрона.
Вопросы для самоконтроля
1. С какой целью применяется упрочнение деталей?
2. Перечислите новые способы и технологии нанесения покрытий.
|
|
3. Опишите комбинированное упрочнение, перечислите его особенности.
4. Что такое эпитаксия? Применение эпитаксии при упрочнении деталей.
5. Как производится подготовка поверхности под плазменное напыление?
6. Что такое пластическое деформирование?
Тема 8 Ремонт корпуса судна
Дефектация металлических корпусов судов. Организация и методика проведения дефектации. Дефектация в полном и частичном объеме. Условия проведения дефектации. Состав комиссии по дефектации корпусов.
Классификация дефектов корпусных конструкций. Местные остаточные деформации связей корпуса.
Типовой технологический процесс ремонта корпуса судна.
Методы подетальной замены обшивки и набора.
Методические рекомендации
Дефектация корпусов может выполняться в полном или частичном объеме.
Дефектация корпусов в частичном объеме проводится между средними ремонтами (перед промежуточными видами ремонта) и выполняется администрацией судна и владельцем флота для проверки правильности включения в ремонтную ведомость дефектов, требующих устранения. В необходимых случаях к частичной дефектации привлекается представители производственного цеха, ОТК и Регистра.
|
|
Правилами Регистра установлена следующая единая терминология в зависимости от степени и характера поражения поверхности:
а) местный износ – частичный износ, охватывающий отдельные участки поверхности связи;
б) сплошной износ – общий износ, охватывающий всю поверхность связи;
в) равномерный износ – сплошной общий износ с утонением, одинаковым по всей поверхности связи;
г) неравномерньй износ – сплошной износ с утонением, различным по всей поверхности связи;
д) язвенный износ – местный износ связи от коррозии в виде отдельных раковин (пятен, язв, точек).
К местным остаточным деформациям связей корпуса, возникающим от воздействия внешних нагрузок (соударения с судами, причалами, льдом, топляками, подводными препятствиями, падающим при погрузке грузом и т.п.), относятся вмятины, бухтины, гофрировки (ребристости) и кромочные деформации.
К прочим дефектам, которые не влияют на оценку технического состояния корпуса в процессе эксплуатации, но учитываются при дефектации для устранения при среднем ремонте, относятся цементные заделки водотечности, износ стыковых и угловых сварных швов, деформация выступающих частей корпуса, не мешающие эксплуатации судна и не влияющие на общую прочность корпуса, отдельные глубокие язвы коррозии связей и др.
Обобщенно технологический процесс ремонта корпуса можно представить в такой последовательности:
1) Наметить контур выреза в обшивке.
2) Вырезать участок обшивки не повреждая кромок набора (рис. 2.16).
3) Наметить участки набора, подлежащие правке на месте, правке со съемкой в цеховых условиях, частичной замене.
4) Вырезать участок набора, заменить или выправить.
5) Подогнать и установить детали набора, прихватить, сварить стыковые швы.
Вопросы для самоконтроля
1. В каких случаях выполняется дефектация корпуса судна?
2. Кто входит в состав комиссии по дефектации корпуса?
3. Перечислите виды дефектов корпусных конструкций.
4. Что такое вмятины, бухтины, гофрировки?
5. Как проводится подготовка корпуса к дефектации?
6. Перечислите основные операции при ремонте корпуса.
7. Как производится смена обшивки и набора подетальным методом?
Литература: [2], с. 129-138, 145-149; [6], с. 56-68; [8], с. 51-60.
Дата добавления: 2019-07-15; просмотров: 167; Мы поможем в написании вашей работы! |
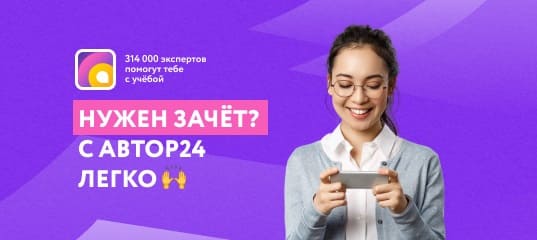
Мы поможем в написании ваших работ!