Технология изготовления осей и колес колесных пар вагонов
Вагонная ось - это элемент колёсной пары, на котором укрепляется колесо. Материал для изготовления осей - сталь ОсВ. Для изготовления оси используются заготовки d=210 мм или 215х215мм. Технический процесс изготовления оси включает получение черновой заготовки, термическую обработку, правку, очистку от окалины, черновую и чистовую механическую обработку, приемку и клеймение.
Осевые заготовки получают след. методами: 1) свободной ковкой на молотах (до 9 паковок в час) – процесс изготовл. Малопроизводит., больш. припуски; 2) обжатием загот. на прессах или радиально-обжимных машинах (до 15 паковок в час) – более производительный процесс, используется для серийного произв.. При ротационном обжатии 25-50 паковок в час; 3) поперечно-винтовой прокаткой на прокатных станах (автоматическая деформ. заготовки по форме оси при помощи копировального устр-ва) и радиально-ротационным методом (черновая ось зажимается в шпинделе машины, где ролики обеспечивают обжатие заготовки в соответствии с требуемыми размерами) (свыше 50 паковок в час) – получение профиля переменного сечения с минимальными припусками.
На шейке или средней части оси в горячем состоянии наносят знаки и клейма. После черновые оси термически обрабат. (нормализация или нормализация с отпуском) с последующ. процессом правки на прессах, а затем очистки в дробеструйных конвейерных камерах. Черновые оси проходят приемо-сдаточные испыт.. При этом проверяется внешн. вид, размер и проводят механ. испыт. образцов, выреза. из оси, на удар и растяж.
|
|
Технологический процесс механической обработки оси разрабатывается с учетом требований ТУ и программой выпуска. Предусматривается:1) отрезка концов оси; 2) черновая и чистовая обточка оси по всем элементам профиля; 3) нарезание резьбы, обработка торцов под планку, отверстий под крепежные болты; 4) накатка поверхностей шеек и галтелей, средней и подступичной частей; 5) шлифование шеек галтелей; 6) ультразвуковая и магнитная дефектоскопия; 7) приемка оси и консервация. При механической обработке оси осуществляется перенос клейм со средней части на один из торцов.
Требов., предъявл. к констр. колеса: 1) высокая механич. прочность (стойк. против износа); 2) миним. вес;3) возможность многокр. восстановл. профиля обода колеса.
Цельнокатаные колёса изготавл. по ГОСТу облегчённые с номин. Ø по кругу катан. 950 мм, из стали, выпл. в мартеновск. печах или друг. путем, согласов. с производит. Для пас. ваг. из стали марки 1 (углерод 0,44-0,52%), а для груз. - из стали 2 (0,55-0,65%) .
В соотв. с технич. и требованиями: 1) поверхн. колеса не должна иметь трещин, закатов и должна быть очищена от коррозии; 2) ободья колес должны быть подвергн. упрочняющей термообраб. путем прерывистой закалки и отпуска; 3) на боковой поверхн. обода с наружной стороны колеса на расстоянии 5-10 мм от кромки внутр. поверхн. должна быть маркировка (цифрами высотой 10-12 мм); 4) колёса должны быть подверж. ультразвук. и вихреток. дефектоскопии; 5) каждое колесо д/б подверж. внешн. осмотру и контролю основных размеров и предъявлено для проверки инспектору приемщику. От партии колёса из металла одной плавки одно колесо подверг. Испыт. на удар. (Смотрят прогиб колеса (дБ >=25мм) от падения с 6 м груза 1т. и провер. на трещины и твёрдость).
|
|
Колёса изготавл. следу. образом: 1) способ штамповки, с послед. раскаткой на стане и гибкой диска: а) формовка заготовки колеса формовочным штампом за 1 ход пресса усилием 70000-100000 кН; б) раскатка диска, обода, прокатка гребня на ободе на многовалковом колесопрокатном стане; в) гибка диска; 2) способ секционной штамповки – осаженная загот. с отверстием под прессом усилием 70000 кН обжимаются в трёхсекционном штампе последоват.; 3) Формовка колеса за 1 проход плунжера пресса. Преимущ.: 1) сокр. производ. цикл; 2) колёса более точные по размерам с мин. дисбалансом.
Механическая запрессовка (распрессовка) колесных пар вагонов
|
|
Запрессовка:1) подготовительная; 2) формирование посадки; 3) контроль размеров.
1) Подготовительная -подборка колес: а) по кругу катания ∆d=1мм - для новых, ∆d=5мм - для старогодных; б) по толщ. обода <=5 мм; в) по велич. натяга 0,1-0,25 мм.
Подборка натяга осуществляется: 1. селективным способом - подбор колеса по фактическим размерам посадочных мест. Для этого необходимо большой запас обработанных элементов; 2. пригонкой колеса к оси. Используется система вала и система отверстия. Система отверстия- диаметр оси подгоняется к диаметру отверстия. (Минусы: уменьшается диаметр подступичной части и уменьшается срок службы оси). Система вала- отверстие ступицы колеса подгоняется к готовому диаметру подступичной части оси. Этот способ более выгоден и широко применяется. (Плюсы:сохраняется максимальный диаметр подступичной части оси; повышается надежность колёсной пары; увеличивается срок службы оси).
При системе вала подобранные колёса обрабатываются на карусельных станках. При окончательной приточке по шаблону контролируется правильность скругления кромок отверстия ступицы радиусом 4-5 мм
2) Формирование посадки производится с записью процесса запрессовки соединений. Индикаторная диаграмма снимается самопишущим манометром. На шейке одевают алюминиевые стаканы (защищают ступицы колёса от забоин и являются направляющими при надевании колес на ось).
|
|
Посадочные поверхности ступиц и оси обезжиривают, насухо протирают и покрывают тонким слоем растительного масла. Расположение колёс относительно центра оси проверяют по шаблону.
При формировании: 1) должен быть заходной конус на наружном конце подступичной части оси с разностью диаметров не более 1 мм на длине 7-15 мм; 2) необходимо обеспечить совпадение геометрических осей сопрягаемых элементов и оборудования, т.е. не допустить перекоса; 3) при наличии конусности и овальности сопрягаемых деталей запрещается использовать обратную конусность и овальность максимального диаметра оси с минимальным диаметром отверстия; 4) если при запрессовке отмечаются отклонения от нормы соединения бракуются по: -форме диаграммы; -линии сопряжения; -величине конечных элементов; 5) не допускается более 2 раз перепрессовывать колёса на один и тот же конец оси без дополнительной механической обработки.
3) контроль размеров и качества запрессовки. Качество запрессовки определяется по индикаторной диаграмме. Диаграмма запрессовки показывает величину давления, возрастания или снижения его при сборке соединения. Годные и забракованные диаграммы запрессовки колеса после формирования, оформления и приемки КП хранятся в течение 20 лет.
Распрессовка выполн-ся на гидравл-ких прессах с исп-нием приспособлений исключающих изгибы шеек, повреждение их торцов и деформацию резьбы. Распр-ют 2 колеса (с проверки магнитным дефектоскопом подступичных частей оси). Колёсную пару со сдвигом ступиц колеса распр-ют с последующим исп-нием годных эл-тов.
Дата добавления: 2019-07-15; просмотров: 4864; Мы поможем в написании вашей работы! |
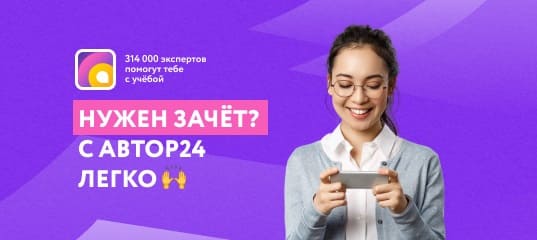
Мы поможем в написании ваших работ!