Методы сборки, применяемые в вагоностроении и вагонорем. производстве
Сборка – наиболее ответственная и продолжительная стадия изготовления и ремонта вагонов. В зависимости от способа базирования различают следующие методы сборки: 1. по разметке – взаимное расположение деталей определяется разметкой по чертежу или временным закреплением зажимными устройствами. Сборка ведется без специальных приспособлений; 2. по сборочным отверстиям. Взаимное расположение собираемых деталей определяется положением имеющихся на них сборочных отверстий. Детали совмещают друг с другом и вставляют в сборочные отверстия фиксаторы; 3. в приспособлении – путем совмещений базовой поверхности приспособлений и базовых деталей. Применяют кондукторы, стенды и т. д.
По степени взаимодействия деталей и узлов различают следующие методы сборки:
1. Метод полной взаимозаменяемости. Производится без подбора и подгонки деталей и обеспечивает рациональную сборку. Используется в массовом и крупносерийном производстве. Этот метод обеспечивает: а) удешевление и упрощение сборочных операций, но удорожание механической обработки; б) простоту нормирования операции, упрочнения организации планирования производства, возможность перевода сборки на поток. Облегчение и удешевление всего процесса ремонта.
2. Метод неполной взаимозаменяемости. Некоторый процент собранных узлов может иметь допуск замыкающего звена больше допустимого. Процент брака не велик, а экономический эффект от снижения себестоимости окупает издержки из-за брака.
|
|
3.Метод подбора деталей. Осуществляется селективной сборкой (попарной или групповой). Наиболее экономичен при сборке малозвеневых узлов и деталей высокой точности.
4. Метод применения компенсаторов (метод регулирования). Требуемое значение допуска достигается регулированием размера 1-ой из деталей компенсатора (прокладка, кольцо, втулка). Позволяет получать и поддерживать в эксплуатации высокую точность независимо от количества звеньев, но увеличивает число изготавливаемых деталей. Недостаток – увеличение номенклатуры изготавливаемых деталей.
5. Метод индивидуальной подгонки. Требуемая точность достигается изменением размеров 1-ой из деталей слесарной или механической обработкой. Метод требует высокой квалификации исполнителей, но обеспечивает высокую точность при сборке многозвенных узлов. Вызывает: а) увеличение трудоемкости сборочных операций; б) увеличение продолжительности сборки; в) нарушение ритмичности производства (не поддается нормированию); г) загрязнение собираемых узлов стружкой или абразивом. Достоинство – высокая точность при сборке многозвенных узлов.
|
|
По формам организации работ:
1. стационарная сборка. Выполняется на 1 рабочем месте, обслуживаемом бригадой;
2. подвижная сборка. Каждая позиция сборки специализируется на выполнении определенных операций;
3. поточная сборка. Работа идет непрерывно, а готов. продукц. выходит периодич. через такт линии. Может осущ. как при подвижном, неподв. объекте или комбинировано;
4. поточная подвижная сборка. Производится на транспортных средствах различного вида (конвейер, рольганга, на рельсовых путях, на карусельных столах и т. д.);
5. поточная неподвижная сборка. Выполняется на неподвижных сборочных стендах в порядке последовательности сборочных операций. Специализированные бригады не перемещаются, выполняя только свою операцию за промежуток времени равный τ. При конвейерной сборке полное время процесса складывается из времени непосредственной сборки и времени на передвижение изделия по позициям.
Виды износов, причины их возникновений. Кривые износов
Изнашивание – постепенное разрушение деталей или их покрытие при трении или других видах контактов с внешней средой сопровождается изменением размеров или свойств (твердости, пластичности, структурыи т.д.). Износ – результат процесса изнашивания проявляется в виде отделения материалов или в виде остаточной деформации.
|
|
Различают следующие виды изнашивания: а) Механическое – в результате воздейств. твердых частиц на трущиеся поверхности. Виды механич. изнашив.: 1) абразив-ное; 2) гидро- и газоабразивное; 3) усталостное; 4) кавитационное; 5) эрозионное.
1) Абразивное – это результат механических воздействий твердых тел или частиц, оказывающих режущее или царапающее действие при относительном перемещении. Наибольшее распространен среди сопряжений. Интенсивность линейного изнашивания стали: dh/dt=C*p*V/H, где С – к-т пропорциональности; Р – нагрузка, Н; V – скорость скольжения, м/сек; Н – твердость металла; dh/dt – скорость изнашивания, мкм/час.
2) Гидро- и газоабразивное – в результате воздействия твердых частиц, увлекаемых потоком жидкости или газа. 3) Усталостное – изменение пов-ти трения в рез-те повторного деформирования материала, приводящего в возникновению трещин и отделению частиц. Возник. под действ. знакопеременных нагрузок. При этом происх. постепенное расшатывание кристаллической решетки металла и затем внезапное разрушение детали.
4) Кавитационное – происх. в условиях гидродинамической кавитации (нарушение сплошности в жидкости). 5) Эрозионное – в рез-те воздейств. потока жидкости или газа.
|
|
б) Молекулярно-механическое – в результ. одновременного механич. воздействия, и воздействия молекулярных и атомных сил (схватывание с последующим разрушением). Схватывание возник. в отсутствии смазки при V<1 м/сек и Руд> предела текуч. матер. Пластические деформ. сопровожд. схватыванием. Больше подвержены мягкие стали.
в ) Коррозионно-механическое – происходит при трении металла, вступившего в химическое воздействие со средой. Характеризуется образованием пленки окислов, химических соединений с последующим их разрушением, т.е. происходит в результате окислительного изнашивания и изнашивании при фретинг-коррозии.
Мероприятия по снижению износа вагонных деталей заключаются в необходимости использования возможности увеличения сопротивляемости поверхности повторным деформированием. С целью уменьш. интенсивности изнашивания необходимо: 1) снижать давление на поверхность трения и обеспечивать равномерное распределение нагрузки в зоне контакта; 2) предотвращение попадания в зону трения пыли и абразива; 3) применять самосмазывающийся материал и смазки с противозадирными свойствами; 4) рационально использ. материал в парах трения и выбирать методы их упрочнения.
Кривые износа.
Тэ – период нормальной эксплуатации; То – период обкатки или приработки; h пр – предел, за который неизбежно появляется неисправность сопряжения; dh/dt – темп износа. За момент времени Тэ износ вновь возрастает, т.к. с увеличением зазоров напряжения усиливается действие ударных нагрузок. Угол наклона кривой износа альфа характеризует интенсивность изнашивания зависит от: 1) условий работы; 2) удельного давления; 3) характер нагрузки; 4) скорости скольжения; 5) свойства материалов; 6) условий смазки; 7) условий сопряжения; 8) характера контакта; 9) обработки сопряженных поверхностей
10. Основы современ. методов восстановл. деталей. Оценка целесообр. Восст
Восст. изнош. дет. произв. до первонач. разм. или до рем. разм. (пригоночные, категорийн.). Если восст. деталь нельзя обраб. под рем. размер, то прибег. к постановке доп. деталей, или наращ. сваркой или гальваниз.. Выбор способа рем. зависит от: 1) конструктивн. особен. восст. детали; 2) технич. возможн. рем. предпр.; 3) экономич. эффективн..
Детали целесообр. восстанавл. способом, при котор. обеспечивается её надёжность работы до очередного ремонта, а стоимость ремонта будет ниже стоимости новой детали.
где себестоимость соответств. восстановления и изготовления дет;
средняя продолжительность службы восстанавливаемой и новой детали.
Основы методов восстановления: Сварка – процесс получ. неразъёмн. соедин. Ме изделий местным оплавлением или пластинчатым деформированием.В вагоностроении и при рем. ваг. наиб. распростр. получили 2 способа сварки – электродуговая и газовая.
1) Ручная дугов. сварка – при устран. в дет. трещин и изломов небольш. разм., или при сварке дет. сложн. формы. 2)Ручн. дугов. плавка – при восст. изнош. поверх. дет. небольш. разм., гладких и резьбов. отверстий d<25 мм. 3)Автоматич. и полуавтоматич. сварка под слоем флюса – при автом. св-ке механизир. подача и перемещ. электрода вдоль свар. шва. 4) Напл. и сварка в среде защ. газов – защ. среда – CO2, N2, аргон, водяной пар, смеси газов. 5)Вибродугов. напл. – имеет < нагрев дет и < деформ.. Электрод вибрир. с част. 35-100 колеб. в сек и амплитудой 1,5-2 мм. Восст. нагруж. поверхн. шеек валов, втулок, шпонок и шлицев. соед.. 6)Автомат. и полуавт. сварка и напл. порошк. проволокой – способств. получ. роста кач. наплавл. Ме и уменьш. трудоёмк.. 7)Контактная сварка (стыковая, роликовая и рельефная) – за счет тепла при прохожд. тока в месте контакта свариваем. дет.. 8)Плазменная сварка и напл. – источник теплов. энергии – струя плазмы. Свар. швы получаются с высок. мех. свойств. и износостойк.. 9) Газовая (кислор.-ацетиленовая) св. – произв. с пом. горелки. Преимущ.: простота оборуд. и инструм.; независ. от источн. Эл. энерг.. Недост.: малая производит.; больш. деформ. изделия. 10)Газопрес. сварка – примен. для соедин. дет. в стыках на газопрес. станках. 11)Сварка трением – использ. для изготовл. и восстановл. валиков ТРП.
Гальванич. наращив. – это электролитический способ. В вагонорем. произв. использ.: А) Хромирование – слой хрома нанес. гальванич. способом облад. высок. антикоррозийностью, низк. коэф. трения, большой тверд. и эластичн.. Недост.: - большая стоим. процесса; - невозм. нанесен. толстых слоёв; - малая производит. процесса. Б) Железнение – в кач. анода – Fe, катода – деталь. Преимущ.: - повал. наращив. большие слои; - производит. в 8 раз больше чем при хромиров.. Недост.: - сравнит. малое сцепление с основными Me; - малая твёрд. слоя. В) Никелирование – примен. в защитно-декоративных целях. Г) Меднение – для нанес. многосл. защ. декоративн. покрыт. типа медь-никель-хром, а также для наращив. толщ. детали. Д) Цинкование – использ. как антикор. покр..
Покрытие полимерным мат-ом. Полимерный материал использ.:- для защ. деталей от кор., повышения их износостойк.; - замен быстроизнашив. Металлич. деталей.
Электроискровая обраб.. Метод основан на использовании электрической эрозии. Используется для: - для снятия Ме с дет из закалённых стали или из твёрд. сталей; - для получ. различн. отверстий; - для упрочн. Ме поверхностей дет гранитом, хромом и т.д..
Пластическая деформ.. Применяется для – восст. размеров и форм изнош. детали, упрочн. поверхн. деталей. Виды пластич. деформ.:1) Осадка – поперечн. сеч. дет. увеличив. за счет высоты; 2) Раздача – восстановл. норм. размеров полых деталей, за счет увелич. их внутр. разм.; 3) Обжатие – получ. внутр. размеров за счет уменьш. наружн.; 4) Правка – использ. для восст. формы дет. В вагоностр. примен.: а) статическим способом в холод сост. и с подогревом под прессом; б) наклёпом с помощью пневмо-молотка.
Дата добавления: 2019-07-15; просмотров: 360; Мы поможем в написании вашей работы! |
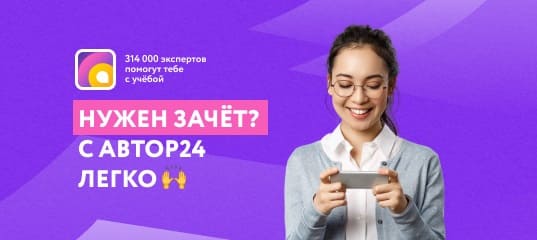
Мы поможем в написании ваших работ!