Оценка технологичности конструкции
Ремонт литых боковых рам и надрессорных балок тележек грузовых вагонов. Требования, предъявляемые при подкатке под вагоны тележек
Рем. дет. тележек в основном сводятся к восст. изнош. поверхн. и заварки трещин. При рем. литых боковых рам тележек: - наплавл. направл. буксовых проемов и направление надрес. балки; - заваривают продольн. трещ. в стенках и буртиках в кронштейнах для валиков; - наплавляют фрикц. планки; - растачив. разработанные отв. для валиков подвесок до d=45 мм для постановки валокнитовой втулки или d=50 мм для постановки стальной втулки. При рем. надрес. балок: - наплавл. опорную поверхн. и отколы наружн. и внутр. буртов подпятн; - наплавляют отв. для заклепок кронштейнов в мертвой точки; - наплавляют наклонные опорные поверхности и поверхности ограничителя клина; - заваривают продольные трещины в верхнем поясе балке при сумме L≤250 мм но не переходящие на бурт подпятника. При ремонте фрикционных клиньев: - наплавляют вертикальные и наклонные при их износе не менее 2 мм но не более 8 мм.
Требования, предъявляемые при подкатке под вагоны тележек: - боковины должны иметь одинаковую базу; - местные зазоры м/у боковиной и корпусом буксы не более 1 мм; - суммарный зазор м/у направляющей боковой рамы и корпуса буксы вдоль тележки 6-13 мм, а поперек 5-11 мм; - зазор м/у скользунами в сумме должны быть не менее 6 мм и более 16 мм, кроме цистерн, хопперов дозаторов, хопперов для перевозки зерна, цемента, минеральных удобрений, катышей у которых зазор 4-12 мм; - занижение клиньев относительно надрессорной балки должно быть 4-8 мм; - подкатываемые тележки должны соответствовать типу и грузоподъемности вагона; - пятники, подпятн. и боковые скользуны должны быть смазаны графитовой смазкой.
|
|
Отсутствие зазоров между скользунами тележки и вагона по диагонали не допускается. У двухосных тележек, вход. в комплект четырехосной тележки, проверяют разницу высот от поверхн. подпятника до головок рельсов, котор. допуск. не более 12 мм.
Неисправности автосцепки. Ремонт съемных деталей автосцепки
В результате трения изнашиваются рабочие поверхности детали АУ, при этом создается условия для саморасцепа, уменьшается прочность детали, что способствует проявлению трещин и изгибов. Интенсивно изнашивается клин тягового хомута и стенка отверстий для него.
Основные износы и повреждения АУ: 1) трещины в углах окон для замка и замкодержателя; 2) трещины сверху и снизу в углах образования ударной стенки зева и боковой стенки большого зуба, а так же боковой стенкой и тяговой стороной большого зуба; 3) трещины в зоне перехода от головы к хвостовику; 4) трещины в хвостовике; 5) износы тяговых и ударных поверхностей зубьев, и ударной стенки зева; 6) износы поверхности хвостовика в местах прилегания к тяговому хомуту, в центрирующей балочки и ударной розеткой; 7) износы внутренней поверхности перемычки и торцовой поверхности хвостовика; 8) износы нижней поверхности перемычки в окно для замка; 9) изломы и износы полочки поддерживания верхней плечо предохранителя; 10) износы шипа замкодержателя.
|
|
У деталей механизма сцепления наиболее часто изнашивается в местах контакта (трения). Кроме износов не редко появляются изгибы и изломы предохранителя, излом сигнального отростка и шипа для предохранителя в замке, изгиб замкодержателя и трещины в местах перехода лапы к противовесу.
Технология ремонта АУ. АУ снимают с вагона, обмывают в моечной машине и полностью разбирают и ремонтир. в соответствии с инструкцией по рем. и обслуж. АУ.
При деповском ремонте подвергаются обязательному магнитному дефектоскопированию: - хвостовик корпуса АУ; - тяговый хомут; - клин тягового хомута; - маятни-ковые подвески центрирующего прибора; - стяжной болт ПА. Стяжной болт после ремонта сваркой дополнительно испытывается на растяжение под нагрузкой 100 кН
|
|
Весь процесс ремонт можно разделить: 1) очистку и обмывку деталей и узлов; 2) разборку АУ; 3) осмотр и проверку деталей; 4) определение объема ремонта; 5) правку изогнутых деталей; 6) устранение износов и повреждений электросваркой и наплавкой; 7) механическая обработка наплавляемых поверхностей; 8) сборку, проверку и комплектовку узлов; 9) клеймения и окраску.
Перед ремонтом для проверки степени износа используют шаблоны (проходные и непроходные). Изогнутые детали механизма сцепления подвергают вправке после подогрева (820-900 °С), в основном вручную. Восстановление наплавкой разрешается только детали имеющие износы не выше обусловленных правилами ремонта.
При восстановлении деталей, механизма сцепления, сваркой разрешается: 1) наплавка изношенной замыкающей поверхности замка; 2) наплавка задней кромки овального отверстия замка для валика подъемника, изношенных мест нижней части замка; 3) наплавка или приварка нового шипа для предохранителя, обломанного отростка замка; 4) наплавка изношенных поверхностей замкодержателя, заварка не более одной трещины замкодержателя; 5) наплавка изношенных поверхностей и отверстий предохранителя, подъемника замка, валика подъемника.
|
|
Заварка трещин в хвостовике корпуса АС при глубине и не боле 5мм допускается при условии, что после разделки трещин поперечное сечение стенок хвостовика не уменьшится более чем на 25мм. Наплавка перемычки хвостовика со стороны прилегания тягового клина из торца разрешается при условии, что толщина её перед наплавкой не менее 40 мм.
3. Неисправности колесных пар вагонов
При взаимодействии пути и подвижного состава возникают контактные напряжения в точках соприкосновения колес с рельсами. В результате этих напряжений при движении колес по рельсам происходит естественный износ трущихся поверхностей, а также их упругие и пластические деформации и усталостные разрушения.
Износ поверхности катания колеса является следствием естественного, нормального изнашивания и истирания тормозными колодками. В обычных условиях возникает равномерный прокат. Характерные признаки неравномерности проката — местный наплыв на наружную грань, сужение фаски, смятие фаски, местное уширение дорожки качения. При несимметричной насадке колес на ось, значительной разнице диаметров колес, - перекосах рамы тележки или неправильной установке колесной пары в тележке, а также под воздействием центробежной силы при длительном следовании вагона по участкам пути с крутыми кривыми у колесной пары колеса изнашиваются по-разному.
При этом появляются тонкий гребень, вертикальный подрез гребня и остроконечный накат. В последнем случае износ гребня сопровождается активной пластической деформацией металла от основания к вершине гребня из-за высокого контактного давления в месте взаимодействия его с головкой рельса.
К дефектам поверхности катания относят ползуны (плоские места), которые появляются в результате скольжения (юза) колеса по рельсу при заклинивании колесных пар вследствие действия неисправных тормозных устройств вагона, неправильного управления тормозами с локомотива или при контакте со съемным башмаком на сортировочной горке.
Характерными дефектами поверхности катания являются выщербины — выкрошившиеся участки, иногда с наличием трещин или расслоений, идущих з глубину металла.
Внутренние дефекты металлургического происхождения приводят к местному уширению обода колеса — раздавливанию его в зоне фаски или к поверхностному отколу у наружной грани.
Трещины и изломы в ободе, диске и ступице колеса являются следствием дефектов металлургического и прокатного производства — неудовлетворительной термообработки, неметаллических включений и расслоений металла, неровностей от прокатки, а также возникают от действия ударных сил.
Износы осей в условиях нормальной работы являются естественными износами. Но и при этом при подшипниках скольжения образуются сверхдопустимые конусность и овальность шейки, а неправильная подгонка подшипников приводит к неравномерному износу галтелей и маломерности буртов.
4.Неисправности и ремонт подшипников вагонов
Возникновению неисправностей роликовых подшипников могут способствовать многие факторы: конструктивные недостатки и плохое качество подшипников, неправильный монтаж букс, низкое качество, недостаточное или избыточное количество смазки, попадание в буксу посторонних включений, неправильная сборка тележек, сверхдопустимые продольные и осевые нагрузки, динамические удары. Основными повреждениями, которые приводят к чрезмерному нагреву букс, а затем к полному разрушению подшипников, являются разрывы внутреннего кольца и сколы его бортов, ослабление посадки внутренних колец,изломы сепараторов, ослабление торцового крепления. Разрывы внутренних колец и сколы (отколы) их бортов происходят в холодном состоянии и в значительной степени зависят от наличия в кольцах больших внутренних напряжений, возникших при изготовлении. В основном это происходит с кольцами, изготовленными из стали объемной закалки, например, марки ШХ15СГ. Эта сталь обладает большой хрупкостью и чувствительна к различным поверхностным концентраторам напряжений. Риски от токарной обработки, микроожоги при шлифовании, контактно-усталостное выкрашивание приводят к возникновению и развитию трещин, чему способствуют остаточные напряжения после закалки и отпуска. Кольца из стали ШХ4 регламентированной прокаливаемости изламываются значительно реже. К трещинам и разрывам внутренних колец могут привести электроожоги, перекосы роликов, сколы торцов роликов, вызывающие эти перекосы. Электроожоги происходят из-за неправильного заземления электрического провода при выполнении сварочных работ на вагоне, а также вследствие прохождения через буксы обратного тока от системы электроотопления вагонов при питании их от стационарных установок напряжением 3000 В в парке отстоя. Разрывы колец вызывают заклинивание роликов подшипника. К этому же приводят попадание осколков борта на дорожку качения и недостаточный радиальный зазор, допущенный при монтаже, который еще больше уменьшается при рабочем нагреве. Ослабление (проворачивание) внутреннего кольца происходит в результате неправильного подбора посадочного натяга. Если между кольцом и шейкой оказывается масляная прослойка, то какой-то промежуток времени кольцо работает аналогично подшипнику скольжения. Когда же создаются условия трения без смазки детали подшипника, и шейка оси быстро нагреваются и повреждаются. Они покрываются окалиной, оплавляются латунью сепаратора. Вследствие этого появляются задиры, возникают трещины и сколы.
Усталостные разрушения сепараторов и изломы из-за нарушений технологии изготовления и монтажа происходят обычно в период действия наибольших вертикальных динамических нагрузок (зимнее и весеннее время года) и в первые месяцы эксплуатации. Установлено, что концентраторы напряжений образуются в виде хвостов горячих трещин в углах окон сепаратора.
При изломе сепаратора его кусочки откалываются и оплавляются, ролики начинают проскальзывать по дорожке качения. Появляются ползуны на образующей роликов и задиры на их торцах. Возникают задиры на дорожке качения и бортах колец. Такое же явление имеет место при недостаточности осевого зазора. При разборке эксплуатируемых подшипников обнаруживаются дефекты на дорожках качения колец, и образующей роликов:
- усталостные раковины из-за достижения предела выносливости металла;
- коррозионные раковины и предшествующие им поверхностная и точечная коррозия в результате попадания в смазку воды и длительного отстоя вагонов в парке ожидания;
- шелушение (рябина) вследствие проскальзывания роликов по дорожкам качения;
- электроожоги в виде небольших точек-кратеров в результате кратковременного прохождения электрического тока через подшипник или в виде рифления, если прохождение тока является длительным;
- вмятины из-за попадания в подшипник твердых включений;
- различные забоины и задиры вследствие небрежности монтажа и демонтажа.
На посадочных поверхностях наружных и внутренних колец и закрепительных втулок обнаруживается коррозия (фретинг-процесс), как результат микроперемещений в условиях знакопеременного радиального нагружения.
На торцах роликов и бортах колец — задиры типа «елочки», обусловленные воздействием осевых сил при отсутствии масляной пленки на трущихся поверхностях. Трещины и изломы упорных колец — от неравномерных деформаций при их креплении торцовой гайкой.
На вагоноремонтных предприятиях производится текущий ремонт роликовых подшипников, который заключается в разборке, осмотре и браковке деталей, исправлении небольших дефектов, сборке и парной комплектовке подшипников с заменой отдельных деталей.
Установлены два вида текущего ремонта подшипников — без переборки роликов и с переборкой. Детали с незначительными дефектами, например ролики и кольца с мелкими рисками, наминами, вмятинами и небольшой коррозией, не бракуют.
При ремонте рабочую поверхность роликов шлифуют, зачищают торцы от задиров и заусенцев и кольца от коррозии, запиливают острые углы в месте примыкания перемычки к телу сепаратора, восстанавливают чеканку сепаратора, зачищают борта у наружных колец и закрепительные втулки.
Сепараторы подшипников подвергают химической очистке (осветлению) для определения трещин визуально или с помощью люминесцентной дефектоскопии.
Химическую очистку с предварительным обезжириванием и промывкой в горячей и холодной воде выполняют в водном растворе смеси ортофосфорной, уксусной и азотной кислот с небольшим добавлением соляной кислоты.
Оценка технологичности конструкции
При конструировании необходимо обеспечить выполнение эксплуатационные требований и рациональность, экономичность изготовления и последующих ремонтов.
Технологичность вагона- степень приближения конструкции к требованиям изготовления (чем меньше трудоёмкость и себестоимость изготовления, тем более технологична конструкция). Для улучшения технологичности вагона необходимо: выбирать наиболее стационарную компоновку; рационально расчленять его сборочные единицы; уменьшать общее количество деталей; максимально использовать стандартные и унифицированные узлы, детали; учитывать показатели технологичности.
а) коэффициент конструкционной стандартизации и модификации
где кол-во стандартных деталей в изделии;
кол-во унифицированных деталей;
общее кол-во деталей.
б) коэффициент использования материала
где масса деталей (или сумма);
масса заготовки (или сумма).
в) коэффициент конструкционной преемственности
где кол-во заимствованных деталей;
общее кол-во деталей без стандартизованных
г)коэф-нт точности
где кол-во деталей обрабат. с высокой точностью
Технологичность конструкции вагона определяется совокупностью кинематических, конструктивных и технологических решений, осуществляемых в процессе проектирования вагона на основе технико-экономического анализа. Различают: производственную и эксплуатационную технологичность продукции.
Производственная технологичность обеспечивает сокращением затрат средств и времени на конструкционную и технологичную подготовку производства и изготовления изделия.
Эксплуатационная технологичность - сокращением затрат, средств и времени на техническое обслуживание и ремонт изделия.
Основные показатели технологичности:
а) абсолютный техникоэкономич. показатель - трудоёмкость изготовления изделия
б) уровень технологичности конструкции по трудоёмкости изготовления
где трудоёмкость изготовлении;
базовый показатель трудоёмкости.
в) уровень технологичности конструкции по технологической себестоимости
где технологич. себестоимость изделия;
базовый показатель технологич. себест.
г) технологическая себестоимость изделия
где стоимость материалов, заработная плата и цеховые расходы
Технологичная конструкция с точки зрения сборки обеспечивает: – параллельную и независимую сборку; – контроль и испытание отдельных сборочных единиц; – обеспечение сборки без пригонки с полной взаимозаменяемостью; – простоту сборки и доступность к местам монтажа и возможность применения высокопроизводит. Методов сборки.
Дата добавления: 2019-07-15; просмотров: 368; Мы поможем в написании вашей работы! |
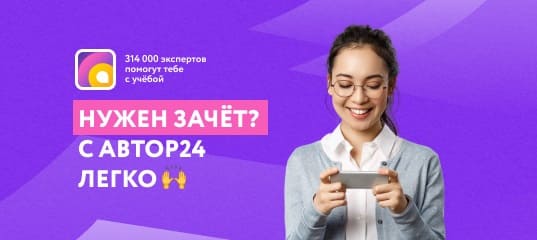
Мы поможем в написании ваших работ!