Характерные дефекты распылителей форсунок. Основные причины отказов крышек, цилиндровых втулок и поршней ДВС. Источники отказа элементов ДГ.
Наиболее чувствительный элемент форсунок – распылитель. К характерным дефектам распылителя относятся повреждение уплотнительного торца, зависание иглы, потеря плотности иглы, распрессовка сопел, а также износ сопловых отверстий по диаметру. Из указанных дефектов примерно половина приходится на повреждение уплотнительного торца. К дефектам, определяющим ресурс распылителей, относятся изнашивание и потеря герметичности запорного конуса, а также коксование отверстий распылителя и направляющей иглы. По данным зарубежных специалистов применительно в дизелям фирмы «Зульцер» примерно 75% распылителей бракуется вследствие чрезмерного изнашивания распыливающих отверстий, а 25% приходится на изнашивание запорного конуса распылителя. Основная причина отказов крышек: трещины сварных швов; пропуски газов; водотечность. Причины отказов цилиндровых втулок: натиры; наработок; наличие лаковой пленки; износ; задиры. Наибольшее количество отказов поршней связано с : прогоранием; трещины; обрыв фланцев маслопроводов.
Признаки классификации смазочных материалов по назначению, химическому
Составу. Характерные особенности масел в зависимости от химического состава.
Классификация смазочных материалов.
По назначению смазочные материалы классифицируются следующим образом:
- для снижения трения (антифрикционные свойства)
- для уменьшения скорости износа трущихся поверхностей
|
|
- для защиты трущихся и неизолированных деталей от коррозии (антикоррозионное действие)
- для очистки смазываемых поверхностей от продуктов износа, нагаров и др. загрязнений
- для постоянного теплоотвода (терморегулирующее действие)
- для уплотнения сопряжённых деталей (поршень-цилиндр, клапана-сальники и т.д.)
- для создания электрической изоляции (трансформаторы)
- как рабочее тело в гидравлических системах
Наиболее широко в судовой технике применяются антифрикционные смазочные материалы. К консервационным смазочным материалам относятся ингибированные масла, жидкие составы и пластичные смазки. Гидравлическими маслами или рабочими жидкостями в гидравлических системах различного назначения служат маловязкие масла. В качестве уплотнительных материалов используются пластичные составы. К электроизоляционным относятся трансформаторные, конденсаторные и кабельные масла и смазки. Технологические масла используются при обработке металлов резанием под давлением с целью смазки и охлаждения инструмента и обрабатываемого материала. По химическому составу смазочные масла разделяются следующим образом: Масла парафинового основания содержат нафтеновые углеводороды с длинными боковыми парафиновыми цепями. Смазочные вещества парафинового основания обладают природной стойкостью к окислению, достаточной теплостойкостью, хорошими смазочными свойствами, высокими температурами вспышки и застывания, низкой летучестью и высоким индексом вязкости. Однако, при использовании в качестве смазочного материала для ДВС, они проявляют склонность к образованию твёрдых углеродных отложений чрезвычайно плотного мелкозернистого характера. При окислении, они склонны к образованию слабых органических кислот, являющихся агрессивными по отношению к некоторым цветным сплавам. Масла смешанного основания содержат в большом количестве ароматические углеводороды. Косвенно, состав масла может быть охарактеризован значением «анилиновой точки». Стандарты устанавливают минимально допустимое значение анилиновой точки в целях ограничения в масле количества ароматических углеводородов. На практике любая нефть или смазочное масло, полученное из сырой нефти, никогда не является чисто парафиновым, нафтеновым или ароматическим продуктом, но соответствующие пропорции могут быть преимущественно парафинового или нафтенового характера. В общем, смазочные масла высокого качества получают путём переобработки парафиновой или нафтеновой нефти. Ароматическая нефть употребляется только для переработки в низкосортные и дешёвые смазочные материалы.
|
|
|
|
Роль соединительной муфты при работе многомашинных установок на ВРШ. Причины различия в частотах вращения на входном и выходном валах. Зависимости мощности и момента турбины и насоса от частоты вращения гребного винта при постоянной частоте вращения вала дизеля.
В таких ДЭУ нагрузка и частота вращения ГД, работающих через муфты и и редуктор на гребной винт, на номинальном ходовом режиме назначаются также как и для ДЭУ с прямой передачей. Дополнительные потери в муфте, регуляторе отражаются лишь на КПД установки. Однако тип и характеристика муфты существенно влияют на работу дизеля, тяговые свойства и маневренность судна при пуске, перемене хода, торможении винта, и в меньшей степени при изменении условий плавания и сопротивления движению судна. При работе ГД на винт имеются свои особенности, обусловленные характеристиками муфт. Наличие соединительной муфты в составе практически не вызывает изменения передаваемого
|
|
момента и частоты вращения. Это означает, что моменты на входном и выходном валах равны между собой, а незначительное различие в частотах вращения вызывается потерями в муфте. В дизель-редукторных установках наибольшее распространение получили механические и гидродинамические муфты, а электродинамические встречаются сравнительно редко. Все типы муфт используются как муфты сцепления. В состав гидродинамической муфты входят ротор насоса и ротор гидравлической турбины. В этом случае моменты, потребляемые насосом и развиваемые турбиной одинаковы и равны эффективному крутящему моменту дизеля.
Характерные причины отказов соплового аппарата ГТН. Режимы работы, способствующих возникновению резонансных напряжений в лопатках турбины. Основные причины повреждений подшипников качения.
На долю соплового аппарата приходится около 39% отказов. Основные причины: образование трещин; коррозионные разрушения в посадочным буртам; обрыв лопаток; усталость из-за перепадов температуры. Явление вибрационного и усталостного характера , возникающее вследствии колебаний температуры газа и пускового воздуха при частых реверсах ГД. При этом могут возникнуть и резонансные напряжения в лопастях турбин, особенно при работе ГТН на неустойчивых режимах, в результате чего возможны вырывы и выкрашивания и ,прежде всего, на выходных кромках. Основные причины отказов подшипников скольжения: износ, трещины, задиры.
Дата добавления: 2019-07-15; просмотров: 256; Мы поможем в написании вашей работы! |
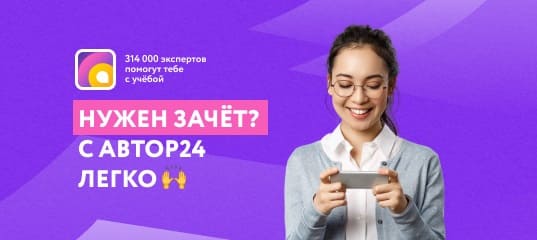
Мы поможем в написании ваших работ!