Фармацевтические субстанции и вспомогательные вещества для инъекционных лекарственных средств, требования к чистоте, деконтаминация, депирогенизация и стерилизация.
Требования к ФС и ВВ:
· Апирогенность (2.6.8);
· Соответствие ГФ РБ, НТД, ГОСТам;
· Квалификация ХЧ (глюкоза, желатин);
Пригодность некоторых субстанций для инъекционных растворов определяют на основании дополнительных исследований согласно ГФ РБ.
Пример: бензилпенициллина калиевая соль определяется на апирогенность и токсичность. ФС используются для приготовления инъекционных растворов. Хранят в отдельном шкафу, в стерильных небольших штангласах, закрытых притертыми пробками. Штангласы перед каждым заполнением моют и стерилизуют.
Для изготовления ЛС для ПП могут быть использованы следующие ВВ:
· Консерванты (бензиловый спирт);
· Антиоксиданты (аскорбиновая кислота);
· Стабилизаторы;
· Эмульгаторы;
· Солюбилизаторы;
· Другие ВВ указанные в ЧС ГФ РБ.
Они не должны отрицательно влиять на действие ФС, вызывать токсичность или нежелательное местное раздражительное действие.
Консерванты применяются в многодозовых, а также в однодозовых ЛС в соответствии с ЧС (для ПП) ЛС для внутриполостных, внутрисердечных, внутриглазных или других инъекций, имеющих доступ к спинномозговой жидкости, а также в дозе, превышающей 15 мл не должны содержать консервантов.
Выбор стабилизатора зависит от химической природы веществ, которые можно разделить на 3 группы:
· Растворы солей слабых оснований и сильных кислот;
· Растворы солей сильных оснований и слабых кислот;
|
|
· Растворы легкоокисляющихся веществ.
ФС и ВВ подвергаются:
Деконтаминации – процесс уничтожения м/о в целях обеспечения инфекционной безопасности;
Депирогенизации – удаление пирогенов из раствора или разрушение их в растворе.Сопряжена с риском разрушения ЛВ, поэтому основной способ удаления пирогенов является – профилактический. Используются различные методы, в зависимости от свойств использующихся веществ. Например, длительное нагревание веществ при высокой температуре (180-250 С); адсорбцией или ультрафильтрацией раствора; обязательна проверка тест-дозы на пирогенность для глюкозы, желатина, бензилпенициллин калиевой соли.
Стерилизации – уничтожение м/о всех видов (патогенных и непатогенных). На производстве используются термические методы:
Стерилизация насыщенным паром под давлением. Основан на способности водяного пара вызывать набухание и коагулирование клеточного белка, что приводит к гибели вегетативной и споровой форм м/о. Проводят в 2 режимах:
При избыточном давлении 0,11 МПа и температуре 120°С
При избыточном давлении 0,2 МПа и 132°С
Воду и растворы стерилизуют в первом режиме. Время стерилизации от 8 до 15 минут в зависимости от объема. Масла стерилизуют 2 часа.
|
|
Воздушный метод стерилизации. Используется горячий воздух (160, 180, 200°С), который обеспечивает разложение белка и гибель м/о. Применяются воздушные стерилизаторы разных марок.
Метод применяется для термостабильных порошков (ZnO, NaCl, тальк, белая глина) и масел.
Водные растворы этим методом не стерилизуют т.к.:
Не обеспечивается быстрый нагрев до нужной температуры
При высокой температуре разлагаются ЛВ
Возможен разрыв флаконов
Контроль параметров эффективности термических методов стерилизации осуществляется с помощью:
КИП
Химических тестов (вещества, изменяющие свой цвет или физическое состояние при определенных параметрах стерилизации. Например, при изменении температуры реагирует бензойная кислота, сахароза)
Биологические тесты (объект из установленного материала, обсеменненый тест-м/о, которые должны погибнуть при определенных условиях стерилизации)
Производство ампул: подготовка стеклодрота, его калибровка, мойка. Выделка ампул на полуавтоматах, отжиг.
Существует несколько способов изготовления ампул:
1. Ручное формование ампул. Для этого вручную из дрота получают капилляр, на конце которого остается кусочек трубки в виде утолщения. Эту расширенную часть разогревают на огне до полного размягчения стекла. Затем стеклодув берет форму, состоящую из двух одинаковых по ловинок, связанных между собой пружиной таким образом, что в нормальных условиях они расходятся на некоторое расстояние друг от друга. При сжимании пружины две латунные плашки точно сходятся и направляющие штифты входят в соответствующие отверстия. При этом обе плашки образуют отверстие, представляющее собой точную форму корпуса ампулы и капилляра. Размягченное стекло стеклодув кладет между отверстиями полуформочек и сжимает форму. В то же время он через капилляр вдувает воздух, отчего стеклянная масса раздувается, заполняя всю форму, и застывает, образуя требуемую ампулу. Чтобы ампулы не загрязнялись, их после изготовления запаивают. Формовые ампулы значительно удобнее, в них легко отрезаются капилляры, они имеют точный объем, корпус у них короче и поэтому удобно набирать жидкость и т.д. Однако изготовление формовых ампул дорогое и требует высокой квалификации стеклодувов.
|
|
2. Получение ампул на полуавтомате типа "Амбег" из стеклянных трубок. В настоящее время чаще всего ампулы производятся непосредственно в ампульных цехах химико-фармацевтических заводов. Ампулы производятся также на стекольных заводах и готовые ампулы закупаются фармацевтическими заводами. Дрот поступает на заводы в пучках. Его после получения калибруют через 0,25 мм. Калибровку проводят для того, чтобы получать ампулы одинакового объема, что имеет большое значение при вакуумном способе заполнения ампул. Калибровка проводится вручную или при помощи специальных приспособлений по наружному диаметру. Дрот должен иметь одинаковый наружный и внутренний диаметр по длине, на срезе должен представлять собой правильный круг. Дрот должен быть прозрачным и бесцветным без непроваренных вкраплений, кусочков стекла. Рис. 3.36. Машина для сортировки стеклянных трубок с вертикальным транспортированием.
|
|
1 - рама-основание; 2 - подвижная рама с держателем трубок; 3 — кривошипно- шатунный механизм привода подвижной рамы; 4 - параллелограмм подвижной рамы; 5 - колодки калибров; 6 - направляющие накопители; 7 - загрузочный лоток; 8 - транспортер подачи трубок. На рис. 3.36 приведено схематическое изображение машины Н.А. Филипина для сортировки стеклянных трубок с вертикальным транспортированием. На станине смонтирована вертикальная рама 2 с держателями для трубок, совершающая вертикальное движение по траектории цифры 8 от двух спаренных и разнесенных кривошипно-шатунных механизмов. На вертикальной раме-основании 1 помещаются калибры 5 и накопители трубок 6. С помощью транспортера подачи трубок 8 из загрузочного лотка 7 стеклянные трубки достигают упора и держателями трубок последова тельно переносятся на калибры. Размер калибров увеличивается снизу вверх. При совпадении диаметра трубки с размером калибра, трубка проходит через калибры и попадает в накопители 6. Трубки сортируются по максимальному диаметру с интервалом 0,25-0,3 мм при измерении в двух точках на расстоянии 700 мм. Производительность 130 кг трубок в час. На рис. 3.37 изображена машина для сортировки трубок по наружному диаметру с комбинированной системой транспортировки. >5 )
Рис 3.37. Схема машины для сортировки трубок с комбинированной системой транспорта. 1- питатель; 2 - механизм сортировки трубок по длине; 3 - механизм сортировки трубок по кривизне; 4 - механизм отбраковки трубок по диаметру; 5 — накопители. Эта машина механизмом 2 сортирует трубки по длине, механизмом 3 отбраковывает трубки с кривизной выше допустимого уровня с помощью фотоэлементов. Кривая трубка перекрывает световой луч, фотоэлемент включает электромагнит, открываются заслонки и трубка проваливается в тележку. Диаметр трубки, от большего к меньшему, измеряется роликами и системой рычажков механизма 4. Трубки одинакового диаметра собираются в накопителях 5. При достижении массы в 8 кг в любом накопителе срабатывает звуковая и световая сигнализация. Производительность 3,6-7,2 тыс. трубок в час. Откалиброванный дрот подвергают мойке в вертикальном или горизонтальном положении. Для вертикальной мойки стеклодрота широко используется установка камерного типа модели 129 М ариупольского завода технологического оборудования (рис.3.38). Стеклянные трубки на тележке в вертикальном положении завозят в камеру и закрывают герметично дверью. Включают систему автоматического управления. Камера заполняется водой с моющим средством. Вода нагревается до кипения. После кипячения вода из камеры сливается. Трубки душируются обессоленной водой и сушатся горячим профильтрованным воздухом. Производительность 100 кг трубок в час. Расход воды 40 м3/ч.
Рис. 3.39. Поточная линия для горизонтальной мойки трубок.1 - лоток загрузки; 2 — ванна для кипячения трубок; 3 — ванна для промывания пучков трубок турбулентным потоком; 4 - привод гребных винтов; 5 - ванна для струйной промывки пучков трубок; 6 - устройство для перемещения сопла струйной промывки; 7 — туннель для сушки трубок; 8 - лоток выгрузки; 9 - транспортная система шагающего движения для перемещения пучков трубок в линии; 10 - захваты для пучков трубок; 11 — пневмоцилиндры вертикального перемещения транспортной системы; 12 - пневмоцилиндры продольного перемещения транспортной системы; 13 - привод конвейера туннеля для сушки трубки. Поточная линия для мойки стеклодрота в горизонтальном положении состоит из загрузочного стола 1; ванны для кипячения трубок 2; ванны для турбулентной промывки трубок 3 горячей водой с помощью гребных винтов с диффузорами 4, расположенными с торцов трубок; ванны для струйной промывки пучков 5, перемещающимися с двух сторон соплами 6. После промывки стеклянные трубки сушатся горячим профильтро ванным воздухом в туннеле 7 и перемещаются на лоток выгрузки 8. Над ваннами укреплена транспортная система 9-13, обеспечивающая перемещение по линии из ванны в ванну стеклянных трубок в пучках. В настоящее время для мойки дрота используется ультразвук, который позволяет значительно повысить качество мойки и увеличить производительность труда на мойке. Горизонтальная ванна укреплена в основании 13. В днище ванны на резиновых прокладках вмонтированы 4 магнитострикционных преобразователя ПМП 2,5. К ним подводится переменный ток высокой частоты от генератора. В ванне смонтирована кинематическая система для обеспечения движения трубок по внутренней поверхности ванны, заполненной водой. Кинематическая система работает следующим образом. Стеклянные трубки, помещенные в питатель 5,6 по одной при помощи звездочек 1,2, шестерней 7, роликов 11, ведущего вала 3 и ведомых валов 4,10, цепного транспортера 9 перемещаются в зону действия излучателей ультразвука. Зазор между трубками и излучателями регулируется направляющими 8. После ультразвуковой мойки трубки поднимаются по ванне вверх, попадают под действие душирующего устройства 14, который промывает трубки горячей профильтрованной водой с температурой 60-70 С. Вымытые трубки собираются в приемник 12. Производительность 100-110 кг дрота в час. Вымытые стеклянные трубки сушатся в вертикальном положении в сушильном шкафу. Из подготовленных трубок изготавливаются ампулы на полуавтомате типа "Амбег".
На рис. 3.41 изображена схема основного процесса получения ампул на роторном стеклоформующем автомате. Рис. 3.41. Схема работы полуавтомата "Амбег".
1 — отверстие патрона верхних шпинделей; 2 — продольная подача дрота; 3 — оттяжные горелки; 4 - патрон нижних шпинделей; 5 - отрезная горелка; 6 - лоток; 7 - торцовый копир. Он работает следующим образом. Стеклянная трубка вставляется через патрон верхнего шпинделя 1 до упора 2, затем поднимается по копиру 7 патрон нижнего шпинделя 4, опирающийся на ролик и захватывает конец трубки. Включается горелка 3. В это время дрот вращается вокруг сво ей оси и размягчается. Горелка тухнет и нижний патрон опускается, растя гивая дрот, получается шейка ампулы. Затем дрот подходит к другой горелке 5, которая имеет острое пламя и перерезает трубку. Вследствие поверхностного натяжения стекла, перерезанные концы трубки заплавляются. Одновременно получается донышко новой ампулы и герметизируется готовая ампула, которая выпадает из патрона на лоток 6. Далее цикл по вторяется. Этот полуавтомат носит название карусельного, так как патроны шпинделей движутся по кругу, непрерывно попадая под горелки. Такой полуавтомат позволяет получить до 5-8 тыс. ампул в смену. Получение ампул при помощи полуавтомата типа "Амбег" является высокопроизводительным, однако велик и процент боя и расхода стеклян ных трубок. Ампулы получаются не соосными, неодинаковыми, так как толщина дрота различна, поэтому пламя неодинаково расплавляет дрот. Для увеличения производительности автоматов, часто используют способ получения двойных ампул .
Рис. 3.42. Схема получения двойных ампул. 1 - верхние патроны шпинделей; 2 - упорный столик; 3 - оттяжные горелки; 4 - патроны нижних шпинделей; 5 - отрезные горелки; 6 - тор цовый копир перемещения нижних шпинделей; 7 - горелка дополнитель ного подогрева; 8 - заготовка двойных ампул. Полуавтомат для получения сразу двух ампул работает так же по схеме основного процесса получения ампул. Стеклянные трубки вводится через патроны верхних шпинделей 1 до упорного столика 2 так, чтобы длины нагреваемой части трубки хватила на заготовку двойной ампулы 8. Трубка захватывается патронами нижних шпинделей 4, приводится во вращательное движение и разогревается на оттяжных горелках 3. При растяжке нагретого участка трубки получается капилляр для двух ампул. Затем горелкой 5 отрезают спаренную заготовку с одновременным формованием донышек у отрезанной заготовки и у последующей ампулы. Во избежание втягивания дна угерметично запаянной двойной ампулы заготовка во время формования дополнительно нагревается горелкой 7. Далее заготовки направляют в приставку для разрезки ампул и набора их в кассеты. Недостатком способа является разрежение внутри двойной ампулы, при резке которых стеклянная пыль засасывается в ампулу, что дополнительно загрязняет ее внутреннюю поверхность.
3. Выделка ампул непосредственно из стеклянной массы. Исходя из преимуществ формовых ампул (одинаковая геометрия), возможно формование ампул непосредственно из стекломассы выдуванием, как это делается при изготовлении бутылок, банок и т.д. В этом случае производство ампул станет мало стадийным процессом, поддающемся автоматизации. Если производство ампул будет осуществляться выдуванием из стекломассы, можно изменить форму ампулы. Цилиндрическая ампула с соотношением диаметра и высоты 1:4 неэкономична, При изготовлении сферических ампул того же объема может быть достигнута экономия в массе ампулы около 25 %. При производстве 1 млрд, ампул экономия достигает 1000 тон стекломассы. Сферическая форма наиболее пригодна для выдувания ампулы со стенками однородной толщины. По-видимому, наиболее удобной может быть форма с грушевидным удлинением вверху и уплощенным донышком для удобства работы при заполнении шприца. Стебель ампулы наверху может иметь утолщение, что придаст ему прочность и облегчит запайку. Переход на изготовление ампулы непосредственно выдуванием из стекло массы приведет к замене многостадийного процесса одностадийным, ликвидации ненужных перевозок дрота и снижению стоимости ампулы. Важной является проблема изыскания материала, способного заменить хрупкое стекло. В настоящее время возрастает доля емкостей для стерильных лекарственных форм, изготовленных экструзией и выдуванием в соответствующие формы из полиэтилена низкого, среднего и высокого давления, из полипропилена, поливинилхлорида, полиметилметакрилата и других полимерных материалов. Отрезка капилляров.
С резки капилляров начинается технологический процесс ампулирования. Ампулы обычно хранят запаянными, чтобы внутрь их не попадала грязь при транспортировке и хранении. Перед мойкой кончики капилляров ампул отрезают. Это может производиться различными методами. Наиболее простой способ - ручная отрезка капилляров .
Она осуществляется на приспособлении, состоящем из алундового и карборундового трехгранного бруска и упора, к которому прикладываются донышки ампул для того, чтобы капилляры отрезались одинаковой длины. Приспособление это устанавливают в наклонное положение так, чтобы донышки ампул во время нанесения царапины были немного приподняты. Для того, чтобы стеклянная пыль и пыль от брусочков не распространя лась в воздухе, с рабочего места отсасывают воздух, кроме того, брусочки автоматически смачивают водой. Второй способ отрезки капилляров — механический, с помощью дискового ножа . Ампура
Рис. Дисковый нож для отрезки капилляров ампул.
Устройство дискового ножа следующее. Стальной диск укрепляется на валу электродвигателя (2,5 тыс. оборотов в минуту) и закрывается кожухом Ампулы кладут на упор, находящийся в щели, образуемой неподвижной частью кожуха. При вращении диска наносится черточка и затем кончик ампулы отламывается механическим ударом. Более производительны полуавтоматы для резки капилляров. Они могут быть разнообразной конструкции.
Рис. 3.46. Приставка к стеклоформующему автомату для резки ампул.
1 - станина; 2 - вход ампул в приставку; 3 - дисковый нож; 4 - рычаг поджима ампул к ножу; 5 - горелка термоудара для отлома надрезанной части капилляра; 6 - горелка для оплавления капилляра; 7 - транспортный орган; 8 -неподвижная линейка с ячейками для ампул; 9 - бункер для сбо ра обрезанных и оплавленных капилляров ампул. 229 Принцип работы приставки к стеклоформующему автомату типа "Амбег" для резки ампул (рис 3.46) состоит в следующем. Ампулы из лотка автомата типа "Амбег" с помощью транспортных линеек приставки попадают в питатель. Коромыслом с масляным демпфером ампулы плавно подводятся к дисковому ножу. Для нанесения кругового надреза ампула приводится во вращательное движение роликом. Откол части капилляра осуществляется термоударом первой горелки. Далее на второй горелке кончик капилляра ампулы оплавляется и попадают в бункер для сбора ампул. Чтобы устранить остаточные напряжения или уменьшить их до практически допустимой величины, ампулы подвергают процессу отжига, т.е. особой тепловой обработке, которая состоит из следующих стадий: 1. Нагрев ампулы до температуры 560-580 °С или 600 С; 2. Выдержка при этой температуре до исчезновения остаточных на пряжений (7-10 мин); 3. Медленное охлаждение, чтобы при этом не возникли новые напряжения (30 минут — до 200 °С) и более быстрое охлаждение до комнатной температуры. Температура отжига должна быть на 20-30 °С меньше той, при которой происходит деформация ампул. Температуру отжига определяют 3 методами: 1. Оптический: суть состоит в том, что если в ампуле имеются внутренние напряжения, то поляризованный луч света, проходя сквозь испытуемое стекло окрашивается в желтый или другой цвет. Образец стекла помещают в небольшую электрическую печь и наблюдают с помощью полярископа за исчезновением цветов при повышении температуры. 2. Механический: определяют температуру деформации ампулы и затем высчитывают температуру отжига. 3. Расчетный метод: температура отжига определяется теоретически по составу стекла. В ампулах, имеющих небольшую толщину стенок 0,2-0,3 мм, остаточные напряжения невелики и такие ампулы отжигу не подвергаются. Отжиг проводится в специальных печах разнообразной конструкции с газовым или электрическим нагревом. t
Рис. 3.47. Печь для отжига ампул с газовыми горелками
1 - корпус; 2 - камера нагрева; 3 - камера выдержки; 4 - камера охлаждения; 5 - стол загрузки; 6 - стол выгрузки; 7 - газовые горелки; 8 - кон вейер; 9 - кассета с ампулами. Печь для отжига ампул с газовыми горелками (рис. 3.47) представляет собой тоннель, внутри которого движется транспортер с регулируемой скоростью. В начале и конце печи имеются столы загрузки и выгрузки ампул. Ампулы для отжига (примерно по 500 штук) загружаются в металлические контейнеры капиллярами вверх, ставятся на цепной конвейер и перемещаются в тоннеле. Тоннель (печь) разделена на три камеры (нагрева, выдержки и охлаждения), в которых выдерживается температурный режим отжига, указанный выше. Газовые горелки установлены на верхнем своде печи и под полом из чугунных плит. Зажигание горелок осуществляется электроискровым способом. Температура контролируется с помощью термопар. Электрическая схема печи содержит ряд блокировок, обеспечивающих безопасность эксплуатации. Газовые печи для отжига Мариупольского завода марки 398-Р-К и 418Р-К имеет производительность 24000 - 28800 ампул в час Электрическая печь представляет собой трубу, с внешней стороны которой расположены электрические нагреватели таким образом, чтобы в средней части печи была зона наивысшей температуры, в которой остаточные напряжения должны сниматься достаточно быстро. Однако температура этой зоны не должна превышать температуру деформации. В начале и конце печи нагревателей ставятся меньше, чем в центре. Печь закрывается изолирующим материалом. Ампулы, подлежащие отжигу, помещаются в металлические контейнеры и движутся по металлическому транспортеру. С одной стороны беспрерывно загружаются, а с другой стороны печи - разгружаются. После отжига ампулы набираются в кассеты для последующей мойки. Для того чтобы механизировать процесс заполнения кассет ампулами, П.И. Резепиным сконструирован автомат, схема которого приведена на рис. 3.48. Автомат помещает в кассету мелкоемкие ампулы по 1 и 2 мл следующим образом. В верхней части автомата расположен подвижный бункер (питатель), в котором находятся ампулы, подлежащие набору в кассету. Ниже бункера укреплена поворотная линейка с ячейками для ампул. Число ячеек соответствует наибольшему количеству отверстий в диамет ральном ряду диска, зафиксированном на подвижном столике автомата. В процессе работы автомата по заданной программе специальные шторки перекрывают справа и слева одновременно требуемое количество ячеек линейки. Тем самым определяется нужное количество ампул для соответствующего ряда отверстий в кассете. При перемещении бункера вдоль линейки ампулы заполняют ячейки, затем, линейка, поворачиваясь, переносит ампулы к кассете капиллярами вниз, ампулы сбрасываются в отверстия кассеты. Линейка возвращается в исходное положение. Столик перемещается на один ряд и цикл повторяется сначала. После заполнения всех рядов кассету снимают и ставят на ее место пустую.
Рис. 3.48. Полуавтомат для набора ампул в кассеты.
1— станина автомата; 2— подвижный бункер; 3— поворотная линейка ячейками для ампул; 4 — подвижный столик; 5 —- кассета для ампул. Кассеты, заполненные ампулами, передаются на мойку, сушку и наполнение 2.
Дата добавления: 2019-07-15; просмотров: 752; Мы поможем в написании вашей работы! |
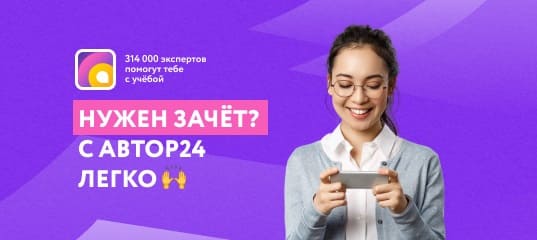
Мы поможем в написании ваших работ!