Ремонт оборудования и оснастки
Капитальный ремонт сварочного оборудования и механического оборудования для сварочного производства выполняют в общезаводском ремонтном цехе. Малый, средний ремонты, а также межремонтное обслуживание и наладку оборудования осуществляют цеховые службы механика и энергетика.
Исходные данные для проектирования сборочно-
Сварочных цехов
При проектировании новых цехов исходными данными являются: чертежи сварных узлов и всех входящих (сборочных единиц, подузлов) и деталей; технические условия на изготовление и приемку изделий из составных частей; программа производства; режим работы подразделения и фонды времени.
Для проекта реконструкции, модернизации или расширения существующего сварочного цеха кроме упомянутых исходных данных необходимо иметь: ведомость имеющегося сварочного или иного оборудования; действующий технологический процесс с нормами времени и нормами расходов сварочных материалов технологического назначения; технико-экономические показатели за последний год работы; план расположения оборудования на участках цеха; чертежи здания.
Режим работы сварочных цехов одно- или двухсменный. Продолжительность рабочей смены 8,2 ч (или 41 ч в неделю). Для термических отделений или участков с печной пайкой часто применяют трехсменный режим работы (непрерывное производство, аналогичное металлургическому производству).
|
|
Действительный годовой фонд времени для рабочих мест без оборудования при односменном режиме 2070 ч., при двухсменном режиме 4140 ч (равен номинальному, без учета потерь по организационным и другим причинам).
Действительный годовой фонд времени простого сварочного оборудования (дуговых сварочных автоматов, полуавтоматов, подвесных головок, тракторов, контактных машин и т. п.) при двухсменном режиме работы 3935 ч., при односменном режиме 1967,5 ч. Для многоэлектродных сварочных машин и автоматических линий действительный годовой фонд времени при двухсменном режиме работы
3725 ч, при односменном 1862,5 ч. Термические агрегаты и печи пайки имеют действительный годовой фонд времени 5840 ч при трехсменном режиме работы.
Действительный годовой фонд времени рабочего-сварщика 1820 ч., рабочего-слесаря механосборочных работ -1840 ч., остальных рабочих 1860 ч.
Технологический процесс
Технология сборки-сварки изделия в техническом проекте документально оформляется в виде ведомости маршрутного технологического процесса, когда необходима подробная проработка технологического процесса (для массового производства).
Вариант технологического процесса и оборудования выбирают из условия наибольшей экономической эффективности от их применения с тем, чтобы технико-экономические показатели цеха (участка) к моменту ввода его в строй были более высокими по сравнению с действующими аналогами.
|
|
Нормирование технологического процесса выпол–няется с учетом производительности труда оборудования на сборочно-сварочных работах или общемашино–строительных нормативов на выполнение I погонного метра шва или других единиц работы.
Определение трудоемкости работ. Трудоемкость операции, выполняемой одним работником, равна норме штучного времени ( tm т , мин/шт.) или продолжительности операции, измеряемой в человеко-минутах или человеко-часах.
Продолжительность операции может быть сокращена, если размеры изделия позволяют вести работу одновременно нескольким рабочим, т. е. бригаде.
Трудоемкость одного изделия равна сумме продол-жительностей всех операций по изготовлению этого изделия с учетом плотности бригад по каждой операции.
В состав трудоемкости входят нормы времени на подналадку и переналадку сварочного оборудования и оснастки.
В крупносерийном и массовом производствах время на подналадку включает в себя заправку и смену электродов на контактных машинах, очистку от брызг (грата) мундштуков и сопел дуговых и газовых сварочных машин и аппаратов, смену кассет с электродной проволокой, смену токове-дущих наконечников, периодическую проверку качества сварки и корректировку режимов сварки с целью компенсации факторов (возмущений), отрицательно влияющих на качество сварных соединений.
|
|
Время на переналадку включает в себя потери времени на смену приспособлений и оснастки (электрододержателей, сварочных горелок, пистолетов и т. п.), установку новых режимов, опробывание оборудования на контрольных образцах, проверку качества сварных соединений перед запуском партии сборочно-сварочных единиц (узлов)
В единичном и мелкосерийном производствах время на подналадку и переналадку включено в подготовительно-заключительное время ( t пп ) и во время обслуживания рабочего места (t обс).
На механизированных поточных линиях массового и крупносерийного производства трудоемкость изделий определяют по расстановке рабочих на рабочих местах умножением числа рабочих, занятых на линии, на такт выпуска.
Годовая трудоемкость выпуска изделий - произведение трудоемкости единицы изделия (продукции) на годовую программу выпуска изделий плюс затраты времени на подналадку и переналадку оборудования в человеко-часах (последнее слагаемое в единичном и мелкосерийном производствах входит в t пп и t обс).
|
|
Классификация оборудования
По технологическому назначению: сборочное, для дуговой сварки (наплавки, напыления, металлизации), для контактной сварки; для газовой сварки; для дуговой и газовой резки; для пайки и склеивания; для сварки лазером; для сварки электронным лучом; механическое сварочное оборудование (для поворота сварных узлов (сборочных единиц), подъема и опускания сварщиков и т. п.); контрольное; испытательное; несварочное оборудование для комплексного процесса производства и др.
По участию в процессе производства: производственное и вспомогательное.
По принципу агрегатирования операций: одноинстру-ментное, многоинструментное, однофункциональное, многофункциональное, роторное, механизированные и автоматические линии.
По участию (размещению) в производственном потоке: отдельно стоящее; встраиваемое в автоматические линии.
По степени распространенности: серийное (универсальное, стандартное); специализированное (нестандартизированное); уникальное (именниковое).
По мобильности (в смысле способности к переналадке): переналаживаемое и непереналаживаемое).
Количество рабочих мест и оборудования определяется по каждой операции отдельно. Методика расчета зависит от форм организации производственного процесса (поточное и непоточное производство). Кроме того, выполняются расчеты по определению коэффициента загрузки (использования) оборудования, количества единиц технологической оснастки и приспособлений, определения численности работающих на участке (рабочих-сдельщиков, вспомогательных рабочих (наладчиков, электриков, слесарей-механиков рабочих РИО, транспортных рабочих, Контролеров, кладовщиков, стропальщиков, уборщиков и т. д.), ИТР, МОП, СКП, управленческого аппарата. Выполняются расчеты по определению фондов заработной платы работающих в сборочно-сварочном подразделении, капитальных затрат и амортизационных отчислений. Все расчеты выполняются в соответствии с методическими указаниями к курсовой работе по дисциплине «Организация и планирование производства».
Технические и технологические возможности различного оборудования и технологического оснащения, применяемого в сварочном производстве, изучаются в дисциплинах: источники питания для сварки, технологические основы сварки плавлением и давлением, оборудование для сварки плавлением и давлением, механизация и автоматизация сварочных процессов, роботы и гибкие автоматизированные производства, проектирование сборочно-* сварочных приспособлений и оснастки, специальные методы сварки и пайка.
Дата добавления: 2019-02-26; просмотров: 155; Мы поможем в написании вашей работы! |
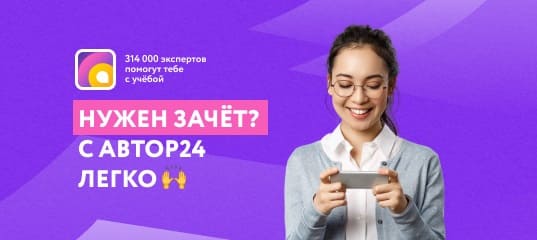
Мы поможем в написании ваших работ!