Электрофизические и электрохимические
Методы обработки
Электроэрозионная обработка
Электроэрозионная (электрофизическая) обработка применяется для обработки особопрочных и труднообрабатываемых материалов и имеет 4 разновидности: электроискровую, электроимпульсную, анодно-механическую и электроконтактную.
Электроискровая обработка основана на воздействии кратковременных искровых разрядов между электродом и заготовкой, помещенной в ванне с диэлектрической жидкостью. Этот способ чаще всего применяется для прошивания отверстия (рис. 2.79), в том числе профильного. Электрод имеет профиль, соответствующий профилю отверстия (рис. 2.80). Диаметр обрабатываемых отверстий 0,25…2 мм. Погрешность изготовления электрода должна быть не более 0,01 мм.
![]() |
Шероховатость, получаемая при электроэрозионной обработке до Ra = 0,2 мкм, точность – 5…6 квалитет. Съем металла ~ 1 см3/ мин. Недостаток этого метода – большой износ электрода-инструмента.
В последние годы большое распространение получает электроискровой метод обработки поверхностей, в котором в качестве инструмента применяется проволока толщиной 0,025…1,5 мм (рис. 2.81). Для исключения быстрого износа проволока непрерывно перематывается с катушки на катушку. Метод реализован на оборудовании с ЧПУ, что позволяет выполнять обработку заготовок различного профиля. Данный метод применяется для получения деталей сложной формы, зубьев точных зубчатых колес, профилей механических передач с промежуточными телами качения.
|
|
Электроимпульсная обработка отличается от электроискровой тем, что на электроды подается последовательность импульсов. За счет этого съем металла увеличивается до 15 см3/ мин. Достигаемая точность – 9…11 квалитет, шероховатость несколько хуже.
Применение электроэрозионной обработки:
· для изготовления ковочных штампов, прессформ небольших габаритов из твердых сплавов и сталей;
· для изготовления мелких сеток, гребенок и др. в радиоэлектронной промышленности;
· для изготовления отверстий с криволинейной осью;
· для нарезания резьб в твердосплавных сплавах и закаленных сталях;
· для маркирования деталей;
· для удаления обломков сверл, метчиков в ответственных деталях;
· для получения пазов и щелей малой ширины (например, разрезка пазов у цанг после закалки);
· разрезка заготовок из вольфрама и др.;
· разрезание рабочей части твердосплавных резцов и т.п.
Кроме электроэрозионной, иногда применяются анодно-механическая и электроконтактная обработка. Точность и шероховатость при этом ниже, чем в предыдущих случаях.
Запись электроэрозионной (электроискровой) операции для обработки детали по рис. 2.82 в технологической документации произведется следующим образом:
|
|
18 1 105 382047 Электроискровая
Станок электроискровой 4532Ф3
А. Установить заготовку в приспособлении. База: 2 отв. Ø3Н9 и плоскость
1. Обработать деталь согласно эскизу
Электрод-проволока М4-1-А-80; Приспособление 7680-6073; Программа 80075-12379; Микроскоп УИМ-21; Инд. ИЧ 0,01; Стойка С- IV ; Штангенциркуль ШЦ II -150-0,05; Подставка 8026-6742-1
Электрохимическая
Электрохимическая обработка (рис. 2.83) основана на анодном растворении металла, с прокачкой электролита между заготовкой и электродом. Прокачкой электролита предупреждается осаждение металла на инструменте-катоде. Этим увеличивается срок службы электрода. Вид обработки: прошивание, точение, протягивание, разрезание, шлифование. С помощью электрохимической обработки можно обрабатывать любые металлы и их сплавы, иногда применяется для снятия заусенцев и скругления острых кромок в ответственных деталях. Электрохимическая обработка отличается от электроэрозионной активным раствором в рабочей ванне.
Процесс электрохимической обработки является саморегулируемым. За счет увеличения зазора δ (рис. 2.83), при остановке подачи электрода, уменьшается ток между электродом и заготовкой и уменьшается скорость растворения металла. Для изготовления электрода-инструмента используют латунь, медь, титан, нержавеющую сталь, которые не подвергаются коррозии в электролите. В качестве электролита применяют растворы солей NaCl, Na2SO4 и другие с различными добавками.
|
|
Плотность тока в зазоре составляет 20…100 А/см2 при напряжении 10…30 В. Величина зазора δ = 0,05…1 мм.
Инструмент при электрохимической обработке изнашивается очень мало. Профильный инструмент для прошивания отверстий используется такой же, как и при эрозионной обработке.
Преимущества (по сравнению с механообработкой):
· исключение наклепа и остаточных напряжений в поверхностном слое;
· малая величина дефектного слоя, равная 0,05…0,2 мм;
· возможность обработки металлов и сплавов любой прочности;
· возможность получения малой шероховатости поверхности
Ra = 0,08…0,02 мкм;
· высокая стойкость инструмента.
Недостатки:
· необходимость принятия специальных мер для устранения коррозии узлов станка;
· низкая производительность (S = 0,2…10 мм/мин);
· вредность условий труда;
· возможность растравливания поверхностного слоя по границам зерен металла.
|
|
Для устранения растравливания в конце электрохимической обработки снижают плотность тока примерно в 10…100 раз.
Точность при электрохимической обработке достигает 7…10 квалитета. Шероховатость Ra = 1,25…0,63 мкм (при плотности тока j = 100…20 А/см2), Ra = 0,08…0,02 мкм (при j = 30…10 А/дм2). При электрохимической обработке быстрее растворяется металл микровыступов, что приводит к уменьшению микронеровностей при этом виде обработки.
Электрохимическое прошивание отверстий производится диаметром 0,75…5 мм и глубиной до 300…500 мм. Точность прошивки 0,05 мм. Непрямолинейность оси 0,1 мм на 100 мм длины. Подача 0,2…10 мм/мин.
Электрод покрыт изолятором на определенную длину (рис. 2.84). Растворение металла производится на участке А, не покрытом изолятором. На участке Б растворения металла уже не происходит.
Электроалмазное шлифование
При электроалмазном шлифовании происходит одновременное воздействие шлифования и электрического тока (рис. 2.85). Причем 90% материала удаляется за счет электрохимического растворения, а 10 % за счет срезания алмазными зернами.
Электроалмазное шлифование применяют для обработки твердых сплавов, магнитов, магнитных сплавов и других материалов. Очень эффективно при обработке хрупких материалов.
Применяют для обработки инструментов. При этом способе устраняются трещины и остаточные напряжения в поверхностном слое, что способствует повышению стойкости инструмента.
Электроалмазное шлифование позволяет в 2…3 раза увеличить производительность обработки по сравнению с алмазным шлифованием. В 8…10 раз снижается расход алмазных кругов.
При электроалмазном шлифовании используют алмазные круги на металлической связке. Плотность тока j = 50…200 А/см2 при напряжении 6…10 В. В качестве электролита используются растворы солей (обычно 2% NaNO3, 0,2% NaNO2, 2% NaF и другие компоненты). Давление Р шлифовального круга не должно быть более 4…10 кгс/см2.
Рекомендуемые режимы резания: продольная подача 1,5…5 м/мин, поперечная – 0,01…0,05 мм/дв. ход, глубина обработки до 1,5…2 мм (при 0,05 мм для обычного шлифования), скорость резания 10…25 м/с.
Точность обработки – 6...8 квалитет, шероховатость Ra=0,16…0,32 мкм.
Лазерная обработка
Лазерная технология – это обработка и сварка материалов излучением лазера [15]. Лазер – источник электромагнитного излучения видимого, инфракрасного и ультрафиолетового диапазонов (рис. 2.86). Лазерное излучение, благодаря монохроматичности и когерентности (совпадение фаз вновь возникающего и уже распространившегося в пространстве излучения), может быть сфокусировано в пятно диаметром, соизмеримым с длиной волны излучения. При этом достигается гигантская концентрация излучения, необходимая для эффективной обработки металлов. Плотность мощности достигает 108 Вт/см2 в непрерывном режиме и до 1012 Вт/см2 в импульсном режиме. Длительность импульса от 20 пс (2·10-9 с) до 20 нс (2·10-12 с) при КПД ~ 3%.
В зависимости от интенсивности излучения лазера можно как расплавлять частицы металла, так и испарять их. Это свойство используется в мощных лазерах для резки, сверления, закалки и сварки различных материалов без возникновения в них механических напряжений, неизбежных при обычной обработке. Обрабатываются заготовки из материалов любой твердости, металлов, алмазов, рубинов. Например, прошивка алмазных фильер занимает несколько минут, против 4…10 ч при механической обработке.
Прошивка применяется для получения отверстий диаметром от нескольких микрометров до десятков миллиметров и глубиной до 15 мм в первую очередь в сверхтвердых, сверхпрочных и хрупких материалах с производительностью до 300 отверстий в минуту (для мелких отверстий).
Лазерная сварка позволяет получить высококачественные соединения деталей из коррозионностойкой стали, никеля, молибдена, а также сваривать высокотеплопроводные металлы, такие как серебро, медь и другие. Скорость сварки достигает нескольких метров в минуту, причем сварной шов не уступает по прочности свариваемому металлу. Подвергшаяся тепловому воздействию зона имеет очень маленькие размеры, что в отдельных случаях имеет решающее значение. Лазерная сварка в отдельных случаях заменяет сварку электронным лучом, невозможной при остаточной намагниченности ферромагнитных сталей из-за отклонения электронного луча. Лазерная сварка заменяет и электроконтактную при сварке материалов с резко различающимися физическими свойствами (в первую очередь электрическим сопротивлением).
С помощью лазерного излучения выполняется и поверхностная термообработка (упрочнение) некоторых деталей, работающих на износ, например, шестерен, распределительных валов и т.д.
Аморфизация поверхности (остекловывание) – одна из разновидностей лазерной обработки – заключается в получении поверхностного слоя металла (на глубине нескольких микрометров) с хаотичным расположением атомов относительно друг друга. Аморфизация получается при быстром (до 105…106 °С/с) охлаждении, когда атомы не успевают перегруппироваться в кристаллическую фазу и застывают при сохранении беспорядочного расположения атомов. Аморфизация поверхности повышает прочность материала, увеличивает коррозионную стойкость материала, устраняет поры, трещины, уменьшает шероховатость поверхности.
Широкое применение находят лазеры для раскроя и профильной резки различных материалов: дерева, фанеры, пластиков, бумаги, текстильных материалов, металлов, стекла, керамики. Скорость резки последних двух материалов до 10 м/мин при толщине материала 1…5 мм. Для увеличения производительности в процесс вводят активные или инертные газы (газолазерная резка). При мощности излучателя в несколько сотен ватт можно осуществлять резку листового материала значительной толщины. При отсутствии газа мощность лазера необходимо увеличить на порядок.
На основе лазерной техники создаются автоматизированные лазерные технологические комплексы, которые можно объединить с другими видами обработки: штамповкой, механообработкой и т.п.
Недостатки лазерной технологии: необходимость в поглощающем покрытии на заготовках, повышенные требования по технике безо-
пасности от излучения, аэрозолей, шума и т.д.
Основные технологические операции лазерной обработки:
· поверхностная термообработка;
· лазерное легирование [40];
· образование поверхностных термических напряжений (лазерное скрайбирование);
· локальный переплав;
· сварка металлических и неметаллических материалов;
· резка материалов;
· размерная обработка материалов.
Электронно-лучевая обработка
Основным видом электронно-лучевой обработки являются процессы, связанные с выделением теплоты в зоне взаимодействия потока электронов с заготовкой [2]. Электронный луч получается в вакууме с помощью электронной пушки и фокусируется магнитными линзами
(рис. 2.87). Рабочее напряжение между катодом и анодом 30…150 кВ.
Электронно-лучевая обработка распространена в микроэлектронике.
Основные технологические операции электронно-лучевой обработки:
· плавление (локальный переплав, плавка в вакууме, сварка);
· испарение (испарение в вакууме, размерная электронно-лучевая обработка, резка заготовок из полупроводниковых материалов и ферритов, прошивание в них отверстий);
· термообработка без изменения агрегатного состояния вещества.
Погрешность размеров при размерной обработке не превышает ±5 мкм, шерохо-ватость Ra = 1,25 мкм. Прошивкой получают до 500 отверстий на круге диаметром 30 мм, при толщине круга 1…3 мм.
Достоинства электронно-лучевой обработки:
· возможность за счет фокусировки луча плавно менять в широких пределах удельную энергию в зоне нагрева;
· большая мощность (от десятков ватт до единиц мегаватт);
· простота пространственного управления луча;
· наличие вакуума, как рабочей среды;
· возможность получения малоразмерной (прецизионной) зоны воздействия электронного луча на обрабатываемый материал.
Недостатки электронно-лучевой технологии:
· необходимость обеспечения высокого вакуума;
· сложность изготовления и эксплуатации электронно-лучевого оборудования.
Плазменная обработка
Плазменная обработка находит широкое применение в промышленности вследствие своей технологичности процесса обработки заготовок.
Плазменная обработка – это обработка материалов низкотемпературной (до 2·104 °К) плазмой, генерируемой дуговыми или низкочастотными плазмотронами (рис. 2.88).
При плазменной обработке изменяется форма, размеры, структура обрабатываемого материала или состояние его поверхностного слоя. Применяются следующие виды технологических процессов плазменной обработки:
· резка металлов;
· плазменный нагрев;
· плавка металла;
· сварка;
· наплавка;
· напыление.
Плазменная дуга хорошо режет коррозионно-стойкие и хромоникелевые стали, медь, алюминий и другие металлы и сплавы, не поддающиеся кислородной резке. Высокая производительность плазменной резки позволяет применять ее в поточных непрерывных производственных процессах.
Свойство плазменной дуги глубоко проникать в металл используется для сварки металлов. Благоприятная форма образовавшейся ванны позволяет сваривать достаточно толстый материал (до 10…15 мм) без специальной разделки кромок. Сварка плазменной дугой отличается высокой производительностью и благодаря стабильности горения дуги хорошим качеством. Маломощная плазменная дуга удобна для сварки тонких листов (0,05 мм).
Плазменная обработка часто применяется для восстановления (до 3-х мм) изношенных деталей транспортных средств, например, коленчатых и распределительных валов автомобилей.
Плазменные покрытия отличаются пониженной теплопроводностью и хорошо противостоят термическим ударам.
Ультразвуковая обработка
В основе метода лежит использование упругих механических колебаний в диапазоне 16·103…108 Гц для придания энергии мельчайшим
частицам абразивного порошка, находящегося в суспензии, которые и производят ударные воздействия на поверхность заготовки (рис. 2.89). Смещение инструмента за период ~ 60 мкм.
Область применения ультразвуковой обработки (табл. 2.10):
· размерная обработка хрупких материалов;
· размерная обработка закаленных и жаропрочных сталей;
· придание колебательного движения рабочим органам технологических машин.
Ультразвуковые колебания (УЗК), наложенные на металлорежущий инструмент, интенсифицируют процесс резания. При этом ускоряется процесс резания и улучшается качество обработанной поверхности (рис. 2.90).
Таблица 2.10
Характеристики ультразвуковой размерной обработки отверстий в некоторых конструкционных материалах
Обрабатываемый материал | Экономичес-кая точность обработки, мкм | Шероховатость обработанной поверхности, мкм | Относительный износ инструмента, % |
Стекло, кварц, ситалл | 20…100 | 5…1,25 | 0,5…1 |
Германий, кремний, ферриты | 30…100 | 1,25…0,63 | 1…2 |
Керамика ЦМ332 | 50…100 | 2,5…0,63 | 2…10 |
Твердые сплавы | 20…50 | 2,5…0,32 | 40…400 |
Закаленная сталь HRC 50…60 | 30…100 | 2,5…0,32 | 120…200 |
Жаропрочные стали | 80…100 | 2,5…0,63 | 150…200 |
Дата добавления: 2019-02-12; просмотров: 949; Мы поможем в написании вашей работы! |
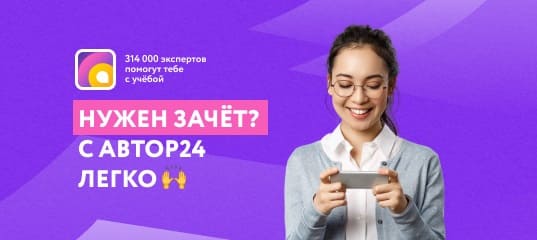
Мы поможем в написании ваших работ!