Термическая и термохимическая операции в техпроцессе механической обработки
Термообработка предназначена для изменения каких-либо физико-механических свойств заготовки без изменения ее размеров.
Различают следующие направления термообработки:
· упрочняющая;
· разупрочняющая;
· изменяющая физические свойства;
· технологическая.
Упрочняющая термообработка повышает механические свойства обрабатываемых деталей: твердость, прочность и износостойкость. Виды упрочняющей термообработки: закалка в одной среде, закалка в двух средах, ступенчатая закалка, изотермическая закалка [19]. После проведения упрочняющей термообработки твердость заготовки может быть настолько высокой, что обработка лезвийным инструментом, даже твердосплавным может быть невозможной. В этом случае дальнейшая обработка производится либо на шлифовальном станке, либо с помощью методов электроэрозионной обработки. Необходимо учитывать, что при закалке из-за перераспределения остаточных напряжений заготовки могут значительно изменять свою форму. Величина погрешностей зависит от материала заготовки и соотношения габаритных размеров. Чем ближе форма заготовки к шаровой, тем меньше погрешность. С увеличением длины заготовки увеличивается погрешность Δ (рис. 2.91). Для исправления погрешностей после термообработки точные поверхности всегда обрабатывают (обычно шлифованием), снимая предварительно оставленный припуск. Величина припуска зависит от материала заготовки и степени закалки.
|
|
Разупрочняющая термообработка повышает пластичность, вязкость, снижает твердость, проч-ность и сопротивление де-формации. Виды разупроч-няющей термообработки: полный отжиг, неполный отжиг, нормализация, диф-фузионный отжиг [19].
Термообработка, изме-няющая физические свой-ства, например, улучшающая магнитные свойства детали.
Технологическая термообработка конструктором не задается, а вводится технологом для улучшения протекания какого-нибудь вида механообработки, например повышения качества шлифования (закаленные поверхности лучше шлифуются) или нарезания резьбы резцом.
В зависимости от требований чертежа или технологических требований термообработка может вводиться на начальных, промежуточных или на заключительных стадиях техпроцесса.
В последние годы получила распространение термообработка в вакууме. Достоинства этого метода – отсутствие окалины и меньшие искажения формы заготовки. Термообработке могут подвергаться уже готовые детали. Метод более дорогой, чем предыдущие.
Химико-термическая обработка металлических деталей применяется с целью улучшения физико-химических и механических свойств деталей – повышение жаропрочности, износостойкости за счет изменения химического состава поверхностного слоя металла, который искусственно насыщается азотом (азотирование), алюминием (алитирование), углеродом и азотом одновременно (цианирование) с последующей закалкой и некоторыми другими элементами, сюда же относят широко распространенный процесс термической обработки – насыщение низкоуглеродистой стали углеродом (цементация) с последующей закалкой [18].
|
|
Запись термической операции (закалки) в технологической документации (маршрутной карте) выглядит следующим образом:
13 1 025 5030 Термическая
1. Калить заготовку согласно чертежу
Стабилизация размеров
Изделия, полученные методом механической обработки, имеют определенный набор потребительских качеств. Эти качества нестабильны во времени. При эксплуатации, при длительном хранении на изделия воздействуют как условия их работы, так и климатические условия. В результате этого детали изделия изменяют свои характеристики: механические, физико-химические, размерные и др. Для некоторых изделий такие изменения несущественны, например, в бытовой немеханизированной мясорубке. В авиационной, космической технике нестабильность характеристик составляющих деталей приведет к отказу работоспособности изделия.
|
|
Чем большая точность изготовленных деталей, тем заметнее нестабильность их во времени.
Для точных деталей некоторые характеристики были стандартизованы. В зависимости от сохранения постоянства формы и размеров, в условиях эксплуатации, включая хранение, геометрические точности и точности взаимного расположения поверхностей детали приборов точной механики подразделяются на категории (табл. 2.11).
Таблица 2.11
Параметры точности в зависимости от категории
Категории деталей | Постоянство размеров детали в заданных условиях, % | Точность отклонения формы и взаимного расположения поверхностей, мм |
1 2 3 | ≥ 0, 0050 0,0002 – 0,0005 ≤ 0,0002 | ≥ 0,05 0,005 – 0,05 ≤0,005 |
В общем виде потребительские качества Q являются функцией многих параметров:
Q = f (М, СЗ, К, Т, Д, В, ТП, Др),
где М – материал детали, СЗ – способ получения заготовки, К – климатические условия, Т – температура в зоне работы детали или изделия, Д – давление, В – вибрации, ТП – особенности построения технологического процесса изготовления детали, Др – другие, например ионизирующее или световое излучение.
|
|
Для получения постоянства параметров заданной точности применяются различные способы их достижения. Наиболее действенным
является способ многократной термической обработки. В зависимости
от требуемой точности в технологический процесс механической обработки неоднократно вводятся операции термической обработки.
Разработаны типовые технологические процессы как для заготовок из деформируемых материалов (табл. 2.12), так и для заготовок, полученных литьем.
Для заготовок, полученных литьем, добавляется дополнительная термическая обработка, следующая сразу за литейной. Критерием при определении категории точности является удельная толщина стенки детали ΔS (ГОСТ 17535-77): ΔS = Sсп / Lmax, где Sсп - среднеприведен- ная площадь поперечного сечения детали в мм2, определяемая как отношение объема детали V в мм3 к периметру P поверхности детали в
Таблица 2.12
Типовые технологические процессы для высокоточных деталей из деформируемых сплавов в зависимости от категории деталей
После-дователь-ность операций |
Категория деталей
| |||
1 | 2 | 3 | ||
1 | Получение заготовки | |||
2 | Предварительная механическая обработка с оставлением припуска до 2,0 мм на сторону | |||
3 | Термическая обработка по режиму 1 | |||
4 | Механическая обработка с оставлением припуска до 0,5 мм на сторону для наиболее точных размеров | |||
5 | Отделочная операция | Термическая обработка по режиму2 | ||
6 | Окончательная механическая обработка резанием |
Отделочная операция
| ||
7 | – | Окончательная механическая обработка резанием | ||
8 | – | – | Термическая обработка по режиму 3 | |
плоскости расположения главных поверхностей детали в мм; Lmax – наибольший габаритный размер детали, определяемый в плоскости расположения главных поверхностей детали в мм.
Для оценки размерной стабильности материалов используют следующие характеристики:
· условный предел прочности – напряжение, которое вызывает (при кратковременном нагружении) остаточную деформацию 0,005% при растяжении или 0,001% при изгибе;
· условный предел релаксации (ползучести) – напряжение, вызывающее остаточную деформацию 0,001% в условиях релаксационных испытаний в интервале 500 – 3000 ч.
Для наиболее распространенных деформируемых материалов: стали 45, стали 12Х18Н10Т, алюминиевого сплава Д16 характеристики размерной стабильности даны в табл. 2.13.
Таблица 2.13
Сравнительные характеристики размерной стабильности
Марка стали или сплава |
Наименование и режимы термической обработки | Характеристика размерной стабильности материалов | |
Условный предел упругости при 20–25°С, Н/ мм2 (кгс/ мм2) | Условный предел релаксации при изгибе (95–105°С), Н/ мм2 (кгс/ мм2) | ||
Сталь 45 ГОСТ 1051–73 | Закалка с +840°С в воде, отпуск при +510°С | 559,2 (50,0) | 392,4 – 422,0 (35,0-40,0) |
12Х18Н10Т ГОСТ 5632–72 | Закалка с +1070°С в воде, деформация 50%, стабилизирующий отжиг при +350°С в течение 10 ч | 637,7 (65,0) | 147,2 – 174,6 (15,0-18,0) |
Д16 ГОСТ 21488–76 | Закалка с +500°С в воде, старение при +190°С в течение 18 ч | 294,3 (30,0) | 39,2 – 49,1 (4,0-5,0) |
Промывочные операции
Промывочные операции проводят в следующих случаях: после окончательной механической обработки, перед определенными видами сварки, перед нанесением покрытий и др. Промывку проводят в различных средах, зависящих от материала заготовки, метода обработки, способа последующего покрытия, способа консервации и т.д. Некоторые способы консервации требуют строго определенного способа промывки. Для наиболее часто применяемых способов промывки разрабатываются типовые технологические процессы (ТТП) промывки.
Промывочная операция для стальной детали, имеющей по техпроцессу доводочную операцию, запишется следующим образом:
18 1 100 0127 Промывочная
1. Промыть по ТТП 01279–00002, опер. 001
Промежуток времени между операциями 095 Доводочная и
100 Промывочная не более 4 ч
или
для детали, имеющей центральное отверстие по 7 квалитету точности с полированным посадочным местом:
19 1 085 0127 Промывочная
1. Обдуть деталь струей сжатого воздуха до полного избавления от стружки и пыли. Струя сжатого воздуха не должна быть направлена на людей
2. Протереть отверстие детали салфеткой, смоченной смесью нефраса с хладоном, при помощи шомпола
Ерш цеховой; шомпол; бязь отбеленная 400х400 ГОСТ 11680–76
3. Просушить деталь струей сжатого воздуха
4. Установить в отверстия бумажные заглушки, чтобы ни пыль, ни влага не попадали вовнутрь
Бумага оберточная серая Паранайская ГОСТ 8873–75; Лента ПВХ ГОСТ 16214–70
Покрытия
Покрытие – это слой одного материала или несколько слоев различных материалов, нанесенных на поверхность детали и адгезионно связанных с ним, для придания поверхностному слою свойств, отличных от свойств основного металла. Такими свойствами могут быть: антикоррозийные, износоустойчивые, декоративные, магнитные, электроизоляционные и др. В качестве материалов покрытий применяются оксиды, металлы, соли металлов, пластмассы, краски, лаки. Покрытия наносятся на металлы, керамику, пластмассы, стекло от нескольких десятых долей микрометра до единиц миллиметров.
Постоянно возрастающие потребности народного хозяйства в покрытиях различного назначения и разнообразие номенклатуры металлизируемой продукции обусловили появление широкого класса установок, предназначенных для решения конкретных производственных задач – металлизации рулонных и полосовых материалов, нанесение защитных, износостойких, декоративных покрытий на металлические и неметаллические материалы, изготовления различных пленочных элементов изделий электронной техники.
Общие требования к покрытиям
К покрытиям предъявляются следующие требования:
· сплошность;
· равномерность:
· непроницаемость;
· высокая сцепляемость с основным металлом;
· твердость;
· износостойкость;
· коэффициент теплового расширения должен быть равен или близок коэффициенту теплового расширения основного металла.
В зависимости от конкретных требований к покрытию усиливается значение отдельных параметров.
Классификация покрытий
Все многообразие методов нанесения покрытий можно свести к 10 методам:
1. Диффузионное нанесение покрытий.
2. Наплавка.
3. Напыление.
4. Оплавление.
5. Осаждение из газовой или паровой фазы.
6. Осаждение из растворов.
7. Плакирование.
8. Погружение.
9. Припекание.
10. Электрохимическое нанесение покрытий.
Под диффузионным нанесением покрытий понимается химикотермическая обработка заготовок в газовых атмосферах, жидких средах (расплавах солей) и засыпках.
Под наплавкой понимаются методы, при которых за счет тепла внешнего источника на некоторую глубину расплавляется поверхность обрабатываемого материала, а также наносимый материал, после чего происходит их контакт и взаимодействие с образованием связи. Источниками тепла при этом могут быть пламя, электрическая дуга, плазменный шнур, искровой разряд. В отличие от плазменного напыления при плазменной наплавке изделие находится под током, а рабочий поток создается двумя дугами – дугой плазмотрона и дугой, переходящей на изделие. В связи с этим различают следующие виды наплавки: газопламенная наплавка, плазменная наплавка, плазменно-дуговая наплавка, электродуговая наплавка, электроискровая наплавка (легирование), электрошлаковая наплавка.
Под напылением понимаются методы, при которых наносимый материал расплавляется в специальном аппарате, распыляется и транспортируется к заготовке струей газа. За счет высокой кинетической энергии летящих частиц (например, за счет взрыва) производится сцепление материала покрытия с поверхностью заготовки.
В качестве материала для напыления применяются порошковые материалы, выпускаемые отечественной промышленностью:
Al2O3, TiО2, Cr2O3, B4C, WB, TiC, ZrC, TiN, NbC, ZrN, HfN и металлические порошки: W, Fe, Mo, Ni, Al, Cu.
В последние годы в России и за рубежом получают распространение композиционные порошки типа металл-металл, карбид-металл,
керамика-металл, керамика-керамика, Ni-Al, Ti-Ni и др.
Различают следующие виды напыления:
· газотермическое напыление, газотермическое нанесение покрытий, имеющее подвиды: газопламенное напыление, газопламенное нанесение покрытий, пламенное напыление, детонационное напыление, детонационное нанесение покрытий, плазменное нанесение покрытий, плазменное напыление;
· нанесение покрытий взрывающимися проволочками, электрораспыление взрывающимися проволочками;
· плазмохимическое напыление покрытий;
· распыление расплавов.
Под оплавлением понимаются методы, при которых на покрываемую поверхность сухим или мокрым способом наносится материал покрытия, который затем расплавляют внешним источником тепла. Наибольшее распространение получили следующие виды оплавления: газопламенное оплавление, индукционная наплавка, высокочастотное оплавление, индукционное оплавление, лазерное оплавление, напайка, плазменное оплавление, радиационное оплавление, электронно-лучевое оплавление.
Под осаждением покрытий из газовой или паровой фазы понимается вся совокупность методов формирования покрытий из газов или паров, реализуемых как при атмосферном давлении, так и в вакууме, с протеканием химических реакций или без таковых. Наиболее известные из этих методов:
· ионная имплантация, ионное легирование;
· физическое осаждение из паровой фазы, вакуумное испарение имеют следующие подвиды – ионное распыление, катодное распыление, магнетронное распыление, индукционное испарение, лазерное испарение и распыление, электронно-лучевое испарение и распыление;
· химическое осаждение из парогазовой фазы, которое имеет подвиды: газофазное осаждение, реактивное испарение и распыление, индукционное реактивное испарение, ионно-плазменное реактивное испарение и распыление, плазменное реактивное испарение и распыление.
Под осаждением покрытий из растворов понимаются методы, основанные на химических реакциях покрываемых материалов или заготовок с водными растворами солей или других соединений, причем реакции протекают без применения электрического тока. Так наносят металлические покрытия, например никелевые, неметаллические, например, кислород, фосфор, комбинированные, например покрытия типа Ni-P. Различают следующие виды осаждения из растворов: жидкостное химическое нанесение покрытий, осаждение из жидкой фазы, химическое нанесение покрытий.
Под плакированием понимается соединение двух или более твердых материалов воедино за счет механических воздействий: взрыва, прокатки, экструзии.
Под нанесением покрытий погружением понимается образование на покрываемом материале или заготовке металлического или неметаллического слоя при погружении в расплав металла или неметалла, например, стекла, но не солей. Например, проводят так называемую горячую металлизацию или остекловывание.
Под припеканием понимают образование связи между наносимым и покрываемым материалом за счет процессов, протекающих обычно при твердофазном спекании в порошковой металлургии. При этом наносимый материал может быть в порошкообразном, пастообразном или твердом консолидированном состоянии.
Под электрохимическим нанесением покрытий понимаются все методы, реализуемые в водных растворах или суспензиях с приложением электрического тока, т.е. гальванические и электрофоретические методы формирования слоев, включая композиционные. Наибольшее распространение получили следующие виды электрохимических покрытий:
· гальваническое нанесение покрытий, электролитическое нанесение покрытий;
· оксидирование, анодирование;
· получение композиционных электролитических покрытий;
· электрофоретическое нанесение покрытий.
Кроме перечисленных методов нанесения покрытий довольно часто в промышленности применяются комбинированные методы. Например, при изготовлении металлической посуды для консервирования используют двойное покрытие: сначала металлическое, затем лаковое.
Требования к поверхности основного материала
Для нанесения устойчивого покрытия, с хорошей адгезионной связью с основным материалом, необходимо перед нанесением покрытия выполнить ряд требований. Шероховатость поверхности должна быть:
· под защитные покрытия Rz ≤ 40 мкм;
· под защитно-декоративные покрытия Ra ≤ 2,5 мкм;
· под специальные покрытия Rz ≤ 40 мкм;
· под электроизоляционные анодно-окисные Ra ≤ 1,25 мкм.
На поверхности заготовки не допускаются неоднородности проката, окалина, заусенцы, поры, раковины, трещины. Поверхность заготовки после механической обработки должна быть без видимых слоев смазки или эмульсии, заусенцев и продуктов коррозии. Острые кромки и углы заготовок должны быть скруглены радиусом не менее 0,3 мм. Поверхность шлифованных и полированных деталей должна быть без видимых вмятин, рисок, заусенцев и прижогов. Поверхность литых и кованых заготовок должна быть без раковин, шлаковых включений, трещин. Швы на сварных деталях должны быть зачищены и непрерывны. Указанные требования выполняются на операциях механической обработки. Другие требования перед механообработкой согласовываются со специалистами (технологами) по покрытиям.
При нанесении покрытий необходимо учитывать их толщину, поэтому при назначении операционных размеров вводится коррекция на толщину покрытия.
Обозначение покрытий в технической документации
Порядок обозначения покрытий регламентируется ГОСТ 9.306–85.
В строке, обозначающей покрытие, все его элементы записываются в следующей последовательности:
1. Обозначение способа обработки основного материала (при необходимости).
2. Обозначение способа получения покрытия.
3. Обозначение материала покрытия.
4. Толщина покрытия.
5. Обозначение электролита, из которого требуется получить покрытие (при необходимости).
6. Обозначение функциональных или декоративных свойств покрытия (при необходимости).
7. Обозначение дополнительной обработки (при необходимости).
Обозначение способа получения и материала покрытия следует писать с прописной буквы, остальных со строчных. Все составляющие отделяют друг от друга точками. Толщину покрытия £ 1 микрометр в обозначении не указывают. Покрытия, используемые в качестве технологических (например, медное), допускаются в обозначении не указывать. Например:
Ан.Окс.прм ,
где Ан. – способ получения покрытия – анодный; Окс. – материал
покрытия окисная пленка; толщина покрытия £ 1мкм (так как нет данных о толщине покрытия); прм – дополнительная обработка промасливание.
Лакокрасочные покрытия
Лакокрасочные покрытия предназначены для защиты деталей от коррозии и придания товарного внешнего вида. Эти покрытия применяются при температуре не более 200°С и не должны подвергаться значительным механическим воздействиям.
Лакокрасочные материалы подразделяются на 8 групп:
· атмосферостойкие;
· стойкие внутри помещений;
· специальные;
· термостойкие;
· стойкие к различным (определенным) средам;
· электроизоляционные;
· грунтовые;
· шпатлевки.
Для повышения устойчивости против коррозии детали предварительно грунтуются. Перед окраской детали из алюминия обычно анодируются, а детали из стали, латуни оксидируются для улучшения сцепления краски с металлом.
Лаки и краски можно наносить в один или два слоя; грунт также наносят в один или два слоя. После окраски детали сушат. Время сушки 2…6 часов зависит от состава лакокрасочного покрытия и температуры сушки.
В машиностроении применяются краски и эмали черного, серебристого, голубого, желтого, защитного, белого и других цветов. Они могут быть матовыми, полуглянцевыми, глянцевыми.
Толщина лакокрасочных покрытий составляет 0,2…1,6 мкм.
Покрытия деталей машин
В машиностроении все чаще прибегают к покрытиям деталей машин. При этом преследуются различные цели, но в основе – это изменение поверхностных свойств деталей при неизменной сердцевине. Кроме изменения физических свойств – износоустойчивости, улучшения антикоррозийных свойств и др., в последние годы особое внимание уделяется товарному виду изделия, его декоративным свойствам.
Повышению конкурентоспособности способствует придание поверхностному слою деталей обычной конструкционной стали особых свойств, присущих только высоколегированным сталям или сверхтвердым и сверхпрочным металлам. Например, покрытие хромом толщиной всего 18 мкм повышает износоустойчивость обычной стали в 3 раза, сравнимой с износоустойчивостью закаленной стали У10.
Многие высокие технологии в своем составе используют однослойные и многослойные покрытия. Благодаря успехам в нанесении покрытий создаются элементы компьютерной техники: жесткие диски (винчестеры), дискеты, материнские платы и др.
Дата добавления: 2019-02-12; просмотров: 1827; Мы поможем в написании вашей работы! |
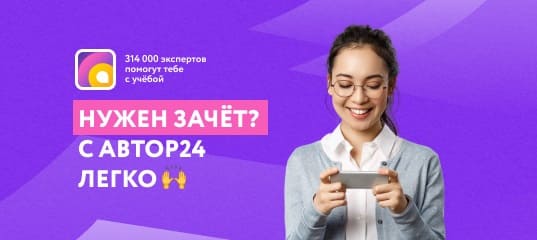
Мы поможем в написании ваших работ!