Обработка сложных криволинейных поверхностей
В последние годынаметилась тенденция применения деталей со сложными криволинейными поверхностями. В первую очередь это детали для сложной формообразующей оснастки, элементы гидро- и пневмоаппаратуры, корпуса авиационной и космической техники, лопатки турбин и др. Для получения сложных трехмерных поверхностей применяют следующие основные способы: копирования эталона на металлорежущем станке, копирование эталона на электроискровом станке и задание траектории движения инструмента по математическим зависимостям на металлорежущих станках с ЧПУ.
Метод копирования эталона реализован на гидрокопировальных станках. Для повышения точности обработки эталон (копир) может изготавливаться в масштабе, например, 10:1. Метод копирования распространен в серийном и массовом производстве. Объемную деталь можно получить на электроэрозионном станке, изготовив объемный электрод по форме, соответствующей получаемой детали. Данный метод находит применение для изготовления деталей небольших габаритов. Недостаток метода – быстрый износ электрода.
С внедрением станков с ЧПУ появилась возможность обрабатывать сложные криволинейные поверхности и в мелкосерийном производстве. Для обработки применяются токарные станки и фрезерные с управлением по 2,5 и 3-м осям. Если необходимо обработать плоскую деталь (например, кулачок для токарного автомата), фрезу подводят на необходимую высоту по координате Z и фиксируют ее. Обработка производится по двум координатам (рис. 2.65). Такие станки, как ИР320ПМФ4, позволяют вести обработку по 2,5 координатам: круговая интерполяция по двум осям, а по третьей только линейное перемещение.
|
|
При обработке трехмерных криволинейных поверхностей часто применяют построчную обработку, при которой в одной плоскости выполняется движение инструмента по контуру обрабатываемой поверхности (одновременно по двум координатам). Затем производится перемещение (сдвиг) по третьей координате и снова движение по контуру (рис.2.66). Трехмерную обработку обычно выполняют концевыми фрезами. Для черновой обработки применяют концевые фрезы со сферическим торцом. После обработки на детали остаются гребешки (рис. 2.67). Чем меньше величина сдвига, тем меньше высота гребешков и тем точнее будет обработана заготовка.
![]() |

|
|
Геометрические погрешности, полученные при обработке фрезерованием, до недавнего времени убирали исключительно вручную с помощью пневматических шлифовальных машинок (рис.2.71).
Улучшение характеристик устройств ЧПУ позволяет создавать металлорежущее оборудование с новыми возможностями. Применение глобусных столов на обрабатывающих центрах с развитым программным обеспечением позволяет отслеживать перпендикулярность оси инструмента к обрабатываемой поверхности. Обработку можно вести фрезой с плоским торцом. Этим самым значительно уменьшается высота гребешков при фрезеровании трехмерной поверхности.
Применение систем CAD/CAM позволяет оптимизировать процесс обработки по критерию минимальных геометрических погрешностей.
|
|
Постоянная борьба за массу изделия, работающего в тяжелых условиях приводит к возникновению тонкостенной пространственной конструкции переменной толщины с нелинейными ребрами жесткости, наплывами и поднутрениями сложной формы.
Разработка технологии изготовления корпуса коробки передач гоночной машины Mercedes FIA/GT в системе CAD/CAM ADEM позволило получить высоту гребешков 0,01 мм и минимальный радиус сопряжений – 1 мм. При этом необходимо помнить, что коробка скоростей работает в условиях статических, динамических, ударных и вибрационных нагрузок. Поэтому конструкция корпуса коробки передач является очень сложной.
Слесарные операции
Слесарные операции подразделяются на основные и вспомогательные. Основные слесарные операции связаны с формоизменением заготовки, например, сверление отверстий (или досверливание глубоких отверстий после засверливания на станках с ЧПУ), нарезание мелких резьб, отрезка заготовки пилой вручную или вырубка зубилом окна в тонкой заготовке. На вспомогательных слесарных операциях производится доработка предыдущих операций механической обработки (например, рис. 2.71). Как основные, так и вспомогательные слесарные операции могут выполняться с применением металлорежущих станков, например, снятие заусенцев в отверстиях на сверлильном станке с помощью зенковки.
|
|
Запись слесарной операции в технологической документации производится следующим образом:
19 1 030 0108 Слесарная
1. Снять заусенцы после фрезерования
Шабер 2850-0002, СТП 608.935-84; надфиль плоский 80, № 2
или
19 1 070 0108 Слесарная
А. Уложить заготовку на слесарный верстак с технологическими упорами. Заготовку поднимать и опускать при помощи кран-балки
1. Снять заусенцы после фрезеровки, острые кромки притупить фаской 0,3х45°
2. Зенковать 6 отверстий Ø3Н14 изнутри радиусом 5±0,3 за 3 перехода по чертежу
Заточку радиусной зенковки предъявить ОТК перед обработкой детали
Напильник 2820-0012; Лупа ЛТ1-4х
Зенковки: угол 60° - 2353-6057; угол 90° - 2353-6057-01; радиусная – 2355-6030; шаблон радиусный, набор № 1; ручная пневматическая головка УСМ 12-В-3000; зенковка радиусная 2355-6031
Отделочные операции
К методам отделочной обработки относятся тонкое точение, алмазное выглаживание, абразивные методы отделочной обработки (тонкое шлифование, хонингование, суперфиниширование, доводка, притирка, полирование), обработка давлением.
Каждый из перечисленных методов обладает своими достоинствами и недостатками. При получении особо точных поверхностей необходимо учитывать многие параметры, влияющие на точность обработки. На отделочных операциях получают 6…4 квалитет точности и шероховатость поверхности Rа = 1,25…0,02 мкм.
При обработке ювенильных (сверхгладких и сверхчистых) поверхностей с субмикронной точностью применяются методы нанотехнологии, базирующейся на принципиально новых физико-химических процессах размерной обработки, обеспечивающих параметр шероховатости, измеряемый в тысячных долях микрометра.
В НИИ технологии машиностроения (НИИТМ, г. Москва) разработаны физико-химические основы нанотехнологии, позволяющие управлять параметрами поверхности за счет работы выхода электрона и тем самым создавать сверхгладкие, сверхточные поверхности деталей.
Хонингование
Хонингование – абразивная обработка внутренних цилиндрических поверхностей. Для обработки применяют специальный инструмент – хонинговальную головку (рис. 2.72, а). Для оснащения головок применяют абразивные, алмазные бруски, а также бруски из эльбора. В процессе работы инструмент совершает вращательное и возвратно-поступательное движения (рис. 2.72, б).
В процессе хонингования происходит повышение точности размеров, снижение погрешности неточности формы, уменьшение шероховатости поверхности, повышается несущая способность обработанной поверхности.
Припуск под хонингование может колебаться от сотых до десятых долей миллиметра. Минимальный припуск применяется в случае, если необходимо изменить только шероховатость поверхности. Особенность хонингования – получение на обработанной поверхности благоприятного микрорельефа для удержания смазки, что способствует снижению износа трущихся пар. Поэтому хонингование часто применяют для обработки гидравлических цилиндров, подшипников скольжения.
Хонингование применяется после тонкого точения, шлифования и других чистовых операций механической обработки.
Суперфиниширование
Суперфиниширование – отделочная обработка различных поверх-ностей деталей, в том числе цилиндрических, абразивными брусками (рис. 2.73). В результате суперфиниширования шероховатость поверхности снижается до Ra = 0,1…0,012 мкм, увеличивается относительная опорная длина профиля поверхности с 20 до 90% [35].
Существенного изменения размеров и макрогеометрии поверхности не наблюдается. Обработка производится мелкозернистыми брусками зернистостью от 3 до М14 с добавлением смазочного вещества (смесь керосина с маслом и др.) при небольшой скорости (до 2,5 м/с) и с весьма малыми давлениями инструмента на поверхность заготовки (0,1…0,3 Мпа – для заготовок из стали; 0,1…0,2 Мпа – для заготовок из чугуна; 0,05…0,1 Мпа – для заготовок из цветных металлов). Толщина снимаемого слоя 0,03…0,005 мм.
Доводка
Доводка – абразивная обработка, при которой инструмент и заготовка одновременно совершают относительные движения или при неподвижности одного из них другой совершает сложное движение. Доводку совершают микропорошками из алмазов, эльбора и других абразивов с целью получения поверхностей прецизионных деталей с высокими требованиями к точности геометрической формы, взаимному расположению поверхностей, минимальной шероховатости.
Доводочные операции (рис. 2.74) могут выполняться вручную или с применением соответствующего оборудования. Перед доводкой детали должны быть размагничены, очищены от заусенцев и посторонних частиц; на доводимых поверхностях не допускаются трещины, сколы и глубокие риски, превышающие половину величины припуска на доводку. Минимальные отклонения от геометрической формы и взаимного расположения поверхностей деталей должны быть обеспечены обработкой базовых поверхностей на предшествующей операции. Исходная погрешность формы поверхности не должна превышать половины припуска на доводку. Для достижения высокой производительности доводки необходимо на предшествующей операции обработать поверхности с параметром шероховатости Rа в пределах 1,25 – 0,5 мкм и обеспечить требования по точности формы и взаимного расположения поверхностей. Технологический процесс доводки деталей, в зависимости от точности и качества, выполняют за одну или несколько последовательных операций: предварительная доводка, окончательная доводка, отделка. На предварительной доводке происходит исправление исходной неточности формы со снятием основного припуска. На окончательной доводке и отделке достигаются требуемые параметры качества. Величину общего припуска под доводку назначают в пределах от 0,02 до 0,05 мм.
На окончательную доводку и отделку оставляют припуск 0,005–0,03 мм. На предварительной доводке необходимо обеспечить шероховатость Ra = 0,63 – 0,32 мкм, на окончательной – Ra = 0,16 – 0,08 мкм, на отделочной операции – Ra = 0,04 – 0,02 мкм.
Доводочное оборудование необходимо выбирать в зависимости от типа и размеров доводимой поверхности, габаритных размеров детали и предъявляемых к доводимой поверхности требований по точности и шероховатости. Доводку наружных цилиндрических поверхностей, отверстий, плоских поверхностей осуществляют на профилированном оборудовании. Доводка сфер чаще всего производится на универсальных станках (токарных и сверлильных) или на специальных станках, созданных для обработки детали только одной конструкции.
Для осуществления процесса доводки применяется инструмент – при-тир. Для предварительной обработки чаще всего используют чугунные притиры из износостойкого мелкозернистого перлитного чугуна, для окончательной – медь, латунь, бронза, для отделки – неметаллические материалы: пластмассы, дерево, специальные смолы, ткани (табл. 2.8).
Притиры по форме классифицируют на
· плоские – для доводки плоских и наружных поверхностей;
· цилиндрические и конические для доводки внутренних поверхностей тел вращения;
· специальные и фасонные – для доводки асимметричных и фасонных поверхностей.
Параметры шероховатости рабочей поверхности доводочного инструмента должны быть соизмеримы с параметрами шероховатости по-
Таблица 2.8
Материал доводочного инструмента
Материал детали | Обработка | ||
Предвари-тельная | Чистовая (Окончательная) | Отделка | |
Твердые сплавы | Чугун СЧ10, СЧ15, СЧ20 | Чугун СЧ20 Латунь Л63 | Текстолит |
Закаленные хромистые стали и сплавы Металлокерамика | Чугун СЧ20 Сталь Ст3 Латунь Л63 Бронза БрКМц 3-1 | Медь М1 Текстолит Винипласт | |
Стали незакаленные и нержавеющие Титановые сплавы |
Чугун СЧ10, СЧ15, СЧ20 Латунь Л63
| Чугун СЧ20 Алюминиевый сплав Амг6 | Текстолит Липа Батист, фланель, замша |
Медь Латунь Бронза Алюминиевые сплавы | Чугун СЧ20 Стекло Бук | Текстолит Липа, бук Смола Батист, фланель, замша |
верхности достигаемыми при доводке на данной операции. Величина отклонения геометрической формы должна быть не более 1/3 величины допуска на размер доводимой поверхности.
При работе на доводочный инструмент подаются доводочные средства. Доводочные средства применяют в виде паст, суспензий, аэрозолей и микропорошков, шаржированных в притир:
· суспензии рекомендуются на предварительных доводочных операциях и при больших размерах притиров для получения параметра шероховатости Ra = 0,32 – 0,08 мкм;
· пасты рекомендуются для достижения параметра шероховатости Ra = 0,04 – 0,02 мкм при небольших размерах притира;
· доводка шаржированным в поверхность притира микропорошком рекомендуется на окончательных доводочных операциях для достижения высокой плоскостности поверхности до 0,0003 мм и минимального параметра шероховатости поверхности Ra = 0,02 – 0,01 мкм;
· аэрозоли применяются взамен паст и суспензий при больших размерах притиров.
Количество доводочного средства, подаваемого в зону доводки, строго дозируется. Малое количество может вызвать разрыв абразивного слоя и непосредственный контакт поверхности детали и инструмента, что резко ухудшит качество обработки. Чрезмерное количество резко снижает производительность процесса. Доводочное средство представляет собой пасту из абразивного материала (табл. 2.9) и наполнителей: масел растительных и минеральных, сложных эфиров, поверхностно-активных веществ (ПАВ), специальных добавок и наполнителей (парафин, воск пчелиный, дибутилфталат).
Жидкие компоненты паст и суспензий выполняют следующие функции:
· равномерно распределяют абразивные зерна в зазоре между обрабатываемой поверхностью и притиром;
· оказывают смазочное действие и облегчают процесс притирки;
· действуют как охлаждающие жидкости, снижают температуру и деформацию детали;
· удаляют изношенные зерна абразива и частицы металла.
В качестве моющих жидкостей после доводки водорастворимыми пастами применяют однопроцентный раствор тринатрийфосфата, спирт, чистую холодную и горячую воду; после доводки жировыми пастами на органической основе применяют очищенный керосин, бензин, ацетон, моющие средства, содержащие поверхностно-активные вещества.
![]() |
Для измерения доведенных поверхностей применяется специальное оборудование. Толщина плоских деталей и диаметр наружных поверхностей измеряется индикатором 1ИГП или скобой рычажной типа СР с ценой деления 0,001 мм, диаметр внутренних поверхностей – нутромером с ценой деления 0,002 мм. Шероховатость доведенных поверхностей измеряется по ГОСТ 19300–86 интерферометром МИИ-10 (до Ra = 0,16 мкм), профилометром модели 283 (до Ra = 0,025 мкм), профилографом модели 252 (до Rz = 0,10 – 0,032 мкм). Отклонение от круглости измеряют на кругломерах моделей 289 и 290. Отклонение от плоскостности измеряют методом интерференции с помощью стеклянных пластин по ГОСТ 2923–75 или ТУ3-3.2123–88.
Пример записи доводочной операции в технологической документации (доводка производится на токарном станке):
19 1 095 395 Доводочная
Станок токарный точности «В»
А. Установить инструмент в расточенной цанге
1. Зачистить конус угол 60°±1°, выдерживая шероховатость поверхности Ra ≤ 0,8 мкм
2. Довести предварительно конус угол 60°±1° в отверстии, не нарушая размеров, выполненных по чертежу
Зенковки 2353-6059; 2353-6059-01; паста эльборовая МНО Л М40; притир 2854-6414
3. Довести конус (угол 60°±1°) окончательно по чертежу
Микроскоп МБС2-16; подсветка 7875-6018
Паста эльборовая МНО Л М10 ОСТ 92 036-2-70; угломер ц. д. 5'.
Инструмент предъявить ОТК для контроля угла 60°±1°
Детали и притир в процессе доводки и перед контролем периодически (каждые 10÷15 мин) промывать с помощью кисти или салфетки, смоченных в хладоно-нефрасовой смеси
До окончания доводки всей партии, обработанные детали уложить в металлическую тару с крышкой и чистой промывочной смесью
Полирование
Полирование предназначено для уменьшения параметров шероховато-сти поверхности без устранения отклонений размеров и формы деталей. При окончательном полировании достигается (при малых давлениях резания 0,03…0,2 Мпа) параметр шероховатости Ra = 0,1…0,008 мкм. Абразивными инструментами являются эластичные круги (войлок, фетр, ткань, кожа, капрон и т.п.), покрытые полировальными пастами, шлифовальные шкурки и свободные абразивы (обработка мелких заготовок в барабанах и виброконтейнерах). В качестве абразивных материалов применяют электрокорунд, карбиды кремния, бора, окись хрома, железа, алюминия, пасты ГОИ, алмазные и эльборовые шкурки и др. Процесс полирования производят на больших скоростях (до 50 м/с).
Применяют химическое и электрохимическое полирование.
Дата добавления: 2019-02-12; просмотров: 813; Мы поможем в написании вашей работы! |
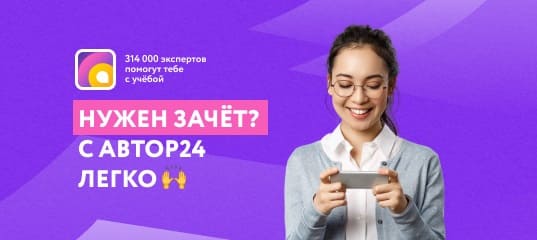
Мы поможем в написании ваших работ!