Методы обработки резьбовых поверхностей
В машиностроении наибольшее распространение получили цилиндрические с прямоугольным, треугольным и трапецеидальным профилем и конические резьбы с треугольным профилем. Для получения резьб используется следующее оборудование: специальное – резьбонарезные и резьбофрезерные станки и автоматы, гайконарезные автоматы, резьбонакатные, резьбошлифовальные и универсальное – токарные, сверлильные, токарно-револьверные и другие станки.
Основные способы формообразования резьбовых поверхностей с указанием точности и шероховатости представлены на рис. 2.35.
Нарезание резьбы
Нарезание наружной резьбы производится резцом (рис. 2.36, а) или плашкой на токарных станках различных видов, нарезание внутренней резьбы метчиком производится на всех видах токарных станков, на сверлильных станках или вручную на слесарных операциях (рис. 2.36, б). Нарезание внутренней резьбы на больших диаметрах производится на токарных станках.
Нарезание резьбы резьбонарезными голов-ками (рис. 2.37) производится на токарных или на специальных станках.
Накатывание резьбы
Накатывание резьбы осуществляется копированием профиля накатного резьбового инструмента путем пластического деформирования на заданном участке заготовки. Накатка резьбы имеет преимущества перед резьбонарезанием:
· производительность накатки больше производительности резьбонарезания;
|
|
· высокая стойкость резьбонакатного инструмента;
· повышенное качество резьбы по прочности за счет более качественной поверхности и отсутствия перерезания текстуры (рис. 2.38).
![]() |
Накатывание наружной резьбы производится на резьбонакатных станках и специальных автоматических станках двумя способами: плоскими плашками (рис. 2.39) и накатными роликами (рис. 2.40).
![]() |
Заготовки для винтов малого диаметра чаще всего изготавливают на холодно-высадочных автоматах или автоматах фасонно-продольного точения, токарно-револьверных автоматах. Накатывание резьбы накатными головками выполняется на автоматах фасонно-продольного точения (рис. 2.41).
![]() |
2.7.3. Шлифование резьбы
Обработка резьб абразивным инструментом подразделяется на абразивное резьбонарезание и шлифование резьбы.
Абразивное резьбонарезание – способ получения профиля резьбы на наружной и внутренней поверхностях шлифованием (вышлифовыванием). Данный способ чаще всего применяется для получения мелких резьб.
Шлифование резьбы производится по боковым сторонам и впадине предварительно полученных резьб резьбонарезанием, резьбонакатыванием и т.п.
Абразивное резьбонарезание и резьбошлифование можно производить [1]:
|
|
·
![]() |
однониточным шлифовальным кругом в одну сторону, т.е. при прямом ходе стола с заготовкой (рис. 2.42, а); этот способ наиболее точный, но малопроизводительный;
· однониточным шлифовальным кругом в обе стороны, т.е. при прямом и обратном ходе стола с заготовкой; такой способ более производительный, чем первый, его применяют в мелкосерийном производстве;
· врезное (рис. 2.42, в) и осциллирующее (рис. 2.42, б) шлифование многониточными шлифовальными кругами; способ применяют в крупносерийном и массовом производстве.
Применение того или иного метода определяется конструкцией изделия, требованиями точности, величиной партии изготовления, наличием оборудования. Для сравнения производительности даны несколько методов изготовления резьб (табл. 2.6).
Таблица 2.6
Сравнительная производительность различных методов
получения наружной резьбы [11]
Метод изготовления резьбы | Производительность, шт/мин |
Накатывание непрерывное Накатывание плоскими плашками Накатывание двумя роликами Нарезание самооткрывающейся резьбовой головкой Нарезание круглой плашкой Фрезерование Шлифование | 24…30 8…10 3…3,5 1,0 0,4 0,25 0,025 |
Обработка плоскостей
|
|
Обработку плоских поверхностей можно производить различными методами на различном оборудовании (рис.2.43). Лезвийным инструментом плоские поверхности получают на фрезерных, строгальных, токарных, протяжных, долбежных, многоцелевых и др.; абразивным инструментом – на шлифовальных, доводочных, полировальных. Плоские поверхности небольших габаритов получают на электроэрозионных станках.
Наибольшее распространение при обработке плоских поверхностей в мелкосерийном производстве получили фрезерование, строгание, протягивание, шлифование.
Методы обработки, достигаемая ими точность и шероховатость обработанных поверхностей показаны на рис. 2.44.
Фрезерование
Фрезерование является в настоящее время наиболее распространенным методом обработки плоских поверхностей (рис. 2.45). Фрезерование выполняется на фрезерных станках. Фрезерные станки подразделяются на универсально-фрезерные, вертикально-фрезерные, горизонтально-фрезерные, продольно-фрезерные, карусельно-фрезерные и многоцелевые. Режущий инструмент – фреза. Для фрезерования плоскостей применяют фрезы: торцовые, цилиндрические, концевые.
|
|
Существуют следующие основные виды фрезерования: цилиндрическое (рис. 2.45, а), торцовое (рис. 2.45, ж), двустороннее (рис. 2.45, п), трехстороннее (рис. 2.45, р).
Фрезерование является прерывистым процессом. Поэтому, при конструировании инструмента и технологическими приемами при резании, решается задача обеспечения плавности работы фрезы. Наиболее производительным является торцовое фрезерование за счет жесткой схемы крепления инструмента и участия в работе большого количества режущих кромок. При обработке крупногабаритных заготовок применяют фрезерные головки (торцовые фрезы со вставными ножами) диаметром 300…700 мм.
Различают черновое, чистовое и тонкое фрезерование. Для снижения основного времени внедряют силовое и скоростное фрезерование. Силовое фрезерование применяют при черновой обработке. Скоростное фрезерование применяют для чистовой, а при очень большой скорости резания и на специальном оборудовании – для отделочной обработки. Широкое распространение получило фрезерование концевыми фрезами при изготовлении деталей сложной пространственной формы: матриц, штампов, прессформ, лопаток турбин и др. При формировании переходов в операции пользуются соответствующей терминологией (рис. 2.46). При обработке плоскостей на металлорежущих станках можно задавать различные траектории (схемы) движения инструмента.
На станках с ручным управлением применяют траектории движения инструмента типа «зигзаг» или «петля» (рис. 2.47, е и 2.47, ж). В основномприменяется движение напроход. Применение других типов траекторий оказывается затруднительным.
Внедрение станков с ЧПУ потребовало существенно изменить подход к построе-нию траекторий движения инструмента. При разра-ботке управляющих про-грамм для станков с ЧПУ можно заранее рассчитывать и применять более сложные траектории движения инструмента, оптимальные по определенным критериям: мини-мальной шероховатости, минимальных остаточных напряжениях и др. Появилась возможность рассчитывать и строить эквидистанты не только для прямых линий, но и для дуг окружностей. CAD/CAM системы позволяют рассчитывать и более сложные траектории (рис. 2.47, з).
Эквидистанта – прямая или кривая линия, равноотстоящая от контура детали (рис. 2.48). При фрезеровании по эквидистанте движется центр фрезы. Траектории движения инструмента по эквидистанте применяют для различных конструктивных элементов. В CAD/CAM системах реализуют все известные схемы фрезерования (рис. 2.47):
· эквидистанта – эквидистантная обработка от центра к границам обрабатываемого элемента;
· обратная эквидистанта – эквиди-стантная обработка от границ обрабатываемого элемента к центру. Обычно применяется для обработки плоскостей;
· петля – эквидистантная обработка по ленточной спирали с сохранением выбранного (встречное или попутное) направления фрезерования; обычно применяется для обработки уступов;
· зигзаг эквидистантный – обработка по ленточной спирали с чередованием встречного и попутного направления фрезерования; обычно применяется для обработки уступов;
· спираль – обработка элемента по спирали; если наружным контуром является окружность, то траектория является спиралью Архимеда;
· петля – обработка в параллельных плоскостях с сохранением выбранного (встречное или попутное) направления фрезерования; направление обработки может меняться;
· зигзаг – обработка в параллельных плоскостях с чередованием встречного и попутного направления фрезерования; направление обработки может меняться;
· зигзаг контурный – обработка, с чередованием встречного и попутного направления фрезерования; траектория формируется по кратчайшему расстоянию между двумя контурами.
Применение CAD/CAM систем в подготовке производства значительно расширяет технологические возможности фрезерования.
Запись в технологической документации фрезерной операции для обработки рычага (рис. 2.49) производится следующим образом:
11 1 030 362031 Фрезерная
Фрезерный станок точности "В"
А. Установить деталь в тисках
База: 2 стороны и плоскость
1. Фрезеровать заготовку в размеры по эскизу (рис 2.49)
Фреза концевая Ø10 2220-6078; Штангенциркуль
ШЩ I – 125 – 0,1; Штангенциркуль ШЩ II – 150 – 0,05
Строгание
Строгание (рис. 2.50) находит большое применение в мелкосерийном и единичном производстве благодаря тому, что для работы на строгальных станках не требуется сложных инструментов и приспособлений, как для работы на фрезерных станках.
Этот метод малопроизводителен, так как обработка выполняется однолезвийным инструментом, а наличие вспомогательных ходов увеличивает время обработки. Заготовки небольших габаритов обрабатываются на поперечно-строгальных станках. Крупногабаритные заготовки обрабатываются на продольно-строгальных и фрезерно-строгальных станках. Точность и шероховатость поверхности будет зависеть от геометрии инструмента и условий резания, точно так же, как и при точении.
Плоское шлифование
Шлифование плоскостей производится на плоскошлифовальных станках с прямоугольным или круглым столом (рис. 2.51).
Плоское шлифование выполняют периферией или торцом шлифовального круга. При шлифовании периферией круга меньше сила резания и меньше нагрев заготовки, чем при шлифовании торцом круга.
При шлифовании торцом круга поперечные колебания шпинделя шлифовального круга в меньшей мере влияют на рельеф обрабатываемой поверхности в связи с чем при этом способе получают более высокую точность и низкую шероховатость [39].
Заготовки закрепляются с помощью приспособлений: электромагнитных столов, плит и магнитных блоков, призм и угольников. Миниатюрные заготовки устанавливаются на электромагнитном столе между стальными пластинами и засыпаются магнитным порошком.
В последние годы наметилась тенденция в ряде случаев заменять фрезерование глубинным шлифованием, по производительности приближающимся к фрезерованию.
В технологической документации шлифовальная операция обработки рычага (рис. 2.52) запишется следующим образом:
12 2 060 344032 Плоскошлифовальная
Плоскошлифовальный станок точности "В"
А. Установить деталь на магнитном столе между стальными пластинами
База: 2 стороны и плоскость
1. Шлифовать заготовку в размеры по эскизу (рис 2.52)
Круг шлиф. ПП200х13х32 91 А40 СМ26 К8 35 м/с; Микр. 0…25;
Инд. МИГ ц.д. 0,001; Штангенрейсмас (стойка)
Дата добавления: 2019-02-12; просмотров: 1677; Мы поможем в написании вашей работы! |
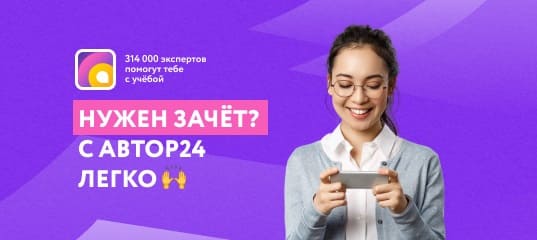
Мы поможем в написании ваших работ!