Смазочно-охлаждающие жидкости
При обработке резанием
При обработке материалов резанием в зоне контакта инструмента с заготовкой возникают большие температуры. Уменьшению этих температур способствует оптимизация геометрии резца и применение смазочно-охлаждающих жидкостей (СОЖ). Большинство операций механической обработки осуществляется с применением СОЖ. При резании смазочно-охлаждающие жидкости должны оказывать смазочное, охлаждающе и моющее действия.
Под смазочным действием понимают способность СОЖ образовывать на контактных поверхностях инструмента, на стружке и на обработанных поверхностях заготовки прочные пленки, полностью или частично предотвращающие соприкосновение передней поверхности со стружкой и задних поверхностей с поверхностью резания. Смазочное действие жидкостей растет с повышением проникающей способности веществ, входящих в ее состав, и активности, с которой эти вещества вступают во взаимодействие со свежеобразованными поверхностями детали, стружки и инструмента.
Охлаждающее действие СОЖ заключается в основном в отборе тепла от нагретых контактных поверхностей инструмента и поверхностей обрабатываемой детали за счет конвективного теплообмена. Теплообмен между нагретыми поверхностями и СОЖ зависит от условий испарения жидкости, теплофизических свойств контактирующих тел, смачивающих способностей СОЖ, скорости ее относительного движения.
|
|
Под моющим действием СОЖ понимают способность жидкостей удалять продукты изнашивания с поверхности резания и контактных поверхностей инструмента. Моющая способность СОЖ улучшается со снижением поверхностного натяжения жидкости.
Кроме смазочных, охлаждающих и моющих свойств, смазочно-охлаждающие жидкости должны обладать стабильностью, не иметь неприятного запаха, быть мало склонными к пенообразованию, не вызывать коррозии станка, детали и инструмента.
Все применяемые в настоящее время СОЖ можно разделить на имеющие в своей основе воду (водные жидкости) и масло (масляные жидкости). К первой группе относятся водные растворы электролитов и поверхностно-активные вещества, масляные эмульсии и присадки; эти жидкости имеют повышенные охлаждающие и пониженные смазочные свойства. Ко второй группе относятся растительные масла, минеральные масла чистые и с присадками; эти жидкости имеют пониженные охлаждающие и повышенные смазочные свойства [4].
При выборе состава СОЖ для механообработки необходимо учитывать следующее. На контактирующих поверхностях обрабатываемой заготовки и инструмента возникают высокие контактные давления. Контактное давление максимально в непосредственной близости к главной режущей кромке (до 60…70 ГПа). Такое давление препятствует доступу в активную зону смазочно-охлаждающей жидкости и эффективному охлаждению. Проблему повышения эффективности решают подачей СОЖ оптимальным способом в зону резания и обоснованным выбором рациональной рецептуры СОЖ. Основные пути улучшения охлаждающего действия СОЖ следующие [43]:
|
|
· использование в составе СОЖ жидкостей с высокой теплопроводностью, теплоемкостью и плотностью;
· применение компонентов с малой кинематической вязкостью;
· увеличение скорости потока СОЖ относительно охлаждаемых объектов;
· уменьшение гидравлического эквивалентного диаметра охлаждаемого объекта.
Первые два пункта в основном зависят от состава СОЖ, который должен удовлетворять еще и другим требованиям: предупреждения коррозии, долговечности, стабильности и т.д.
Перечисленные требования относятся к функциональным и эксплуатационным свойствам СОЖ, однако, для конкретного технологического процесса основные требования: увеличение стойкости инструмента и повышение качества обработанных деталей.
Применение при резании СОЖ уменьшает силу резания, улучшает качество обработанной поверхности и в большинстве случаев повышает стойкость инструмента.
|
|
При обработке коррозионно-стойких сталей в большинстве случаев доминирует адгезионно-усталостный износ. Для его подавления применяют СОЖ с высокими смазывающими свойствами. Из-за меньшей реакционной способности коррозионностойких сталей более высокие результаты при их обработке показывают СОЖ с высокой концентрацией противозадирных и противоизносных присадок.
Фрезерование коррозионно-стойких сталей концевыми, дисковыми, цилиндрическими фрезами целесообразно осуществлять с применением эмульсионных и полусинтетических СОЖ. Чем пластичнее сталь, тем большее влияние оказывает СОЖ на процесс фрезерования. И, наоборот, при фрезеровании малопластичных, термически упрочненных сталей (09Х16НЧБ, 40Х13) состав СОЖ незначительно влияет на стойкость инструмента. При фрезеровании вязких сталей более эффективны СОЖ с высокими смазывающими свойствами (Аквол-6).
При фрезеровании без применения СОЖ наблюдается приваривание стружки к твердосплавным зубьям с последующим отделением крупных частиц твердого сплава инструмента вместе со стружкой. Применение СОЖ препятствует этому процессу, повышая стойкость и работоспособность инструмента.
|
|
При обработке деталей из титановых сплавов усадка стружки мала и при определенных условиях происходит не усадка, а удлинение стружки. Это явление названо «отрицательной усадкой стружки», связано с низкой пластичностью материала и приводит к появлению высоких температур и контактных давлений, а, следовательно, к адгезионному износу.
Для повышения стойкости инструмента при обработке титановых сплавов необходимо уменьшать адгезионные силы, что возможно двумя путями: либо снижать температуру за счет замедления скорости резания, либо за счет применения СОЖ. При обработке титановых сплавов применяют СОЖ: ЭГТ, Аквол – 2, 6, 10М, 11, Укринол-1 и другие.
При обработке нержавеющих сталей тип применяемых СОЖ сущест-венно влияет на износ инструмента. Так, при фрезеровании нержавеющей стали 12Х18Н10Т торцовыми фрезами, стойкость инструмента существенно зависит от типа применяемой СОЖ (рис. 2.75). При обработке этой же стали без применения СОЖ, износ фрезы за 20 мин составил 0,55 мм [43].
Твердые сплавы по сравнению с быстрорежущими сталями обладают более высокой теплостойкостью, поэтому стойкость твердосплавных инструментов при применении СОЖ возрастает меньше быстрорежущих.
Для повышения стойкости инструмента более эффективными являются СОЖ не на масляной, а на водной основе (рис. 2.76).
При обработке резанием существуют следующие ме-тоды подвода СОЖ: полива (рис. 2.77, а), напорного охлаждения (рис. 2.77, б) и охлаждения туманом (рис. 2.77, в).
![]() |
Недостатки 1-го метода – охлаждается наружная поверхность стружки, наименее нагретая. Второй метод более эффективен – охлаждение подается в точки, наиболее приближенные к точкам с максимальной температурой. Достоинства третьего метода – очень интенсивное поглощение тепла за счет повышения мелкодисперсности, т.е. жидкость уже готова к испарению и встретившись с нагретым источником тепла быстро испаряется, поглощая при этом значительное количества тепла. Третий метод считается самым эффективным. При сверлении незаменимым является второй метод, когда подача СОЖ осуществляется через каналы в сверле. Метод полива менее эффективен.
При проектировании операций обработки резанием необходимо учитывать, в каком диапазоне скоростей будет обрабатываться заготовка. При низких скоростях резания выбирают СОЖ с большим смазывающим эффектом, при высоких – охлаждающим.
Одной из лучших СОЖ является вода, но она неприменима из-за коррозии станка, поэтому часто используются эмульсии (раствор эмульсола в воде) или мыльные жидкости. СОЖ типа сульфофрезолов – серосодержащих масел чаще используется при низких скоростях резания, для получения смазывающего эффекта. Основное их преимущество – полное отсутствие воды, а есть только легкие минеральные масла. Но это экологически грязный продукт, у некоторых людей вызывает кожные заболевания. При низких скоростях резания на смену сульфофрезолам приходят графитовые смазки, которые наносятся на резец и долго там удерживаются.
При обработке чугуна влияние СОЖ несколько меньше, чем при обработке сталей. Часто при обработке чугуна СОЖ вообще не применяется, так как СОЖ всюду разносит мелкую чугунную стружку, которая приводит к интенсивному абразивному износу станка. Для отвода стружки применяется отсос стружки.
Чистый алюминий весьма критичен к типу применяемой смазочно-охлаждающей жидкости. Термообработанные алюминиевые сплавы в определенном диапазоне скоростей обрабатывают без применения СОЖ.
Для увеличения срока службы СОЖ применяют устройства по ее очистке. Несмотря на значительную стоимость этих устройств, они быстро себя окупают.
Резание струей воды
В последние годы бурно развивается экологически чистый способ обработки резанием – резание струей воды. В качестве режущего инструмента используется струя воды высокого давления, в том числе и с абразивом. Данный способ используется для резания композиционных материалов, материалов чувствительных к воздействию тепла (алюминиевых сплавов, коррозионно-стойкой стали и титана), армированного стекла, мрамора, гранита, керамики, фарфора, природного камня, ткани, бумаги (в том числе и с покрытием пенопластом), рифленого изоляционного материала, кожи, дерева, пробки, резины, ковровых материалов.
Водоструйное резание можно успешно применять при изготовлении деталей автомобилей: панелей приборов, ковриков, дверных панелей и бамперов, для вырезания любых уплотнений и прокладок, сетчатых деталей из меди и титана. Эффективна двух- и трехмерная обработка заготовок из пластмассы и композитов, а также деталей со сложными поверхностями практически из любых материалов. Водоструйная обработка применяется для разрезания разнообразных пищевых продуктов, утилизации военной техники.
Станок легко настраивается так, что усилия резания будут ничтожны. Это дает возможность обрабатывать нежесткие конструкции. Отсутствие системы СПИД (станок – приспособление – инструмент – деталь), в ее традиционном понимании, позволяет значительно сократить затраты на достижение высокой точности обработки.
Температура в зоне формообразования не превышает 90…95°С, благодаря чему сохраняется структура материала. Рабочее давление достигает 700 Мпа. Создаются станки с еще более высоким рабочим давлением. Стойкость инструмента достигает 150 часов. Технологический процесс относится к категории экологически чистых, без выбросов токсичных паров и образования взвешенной пыли.
Оборудование легко интегрируется с другим, управляемым от компьютера. Время смены инструмента достигает 1 мин. В качестве абразива зарубежные фирмы применяют красный гранат с размерами частиц 0,2…0,3 мм, но можно использовать и литейный песок. Расход абразива до 300 г/мин.
В качестве устройств управления водоструйными комплексами применяют устройства ЧПУ типа CNC со специальным программным обеспечением. Разработаны и CAD/CAM системы для водоструйной обработки.
Скорость обработки для стали достигает 1200 мм/мин и вдвое больше для алюминиевых сплавов (рис. 2.78).
Дата добавления: 2019-02-12; просмотров: 371; Мы поможем в написании вашей работы! |
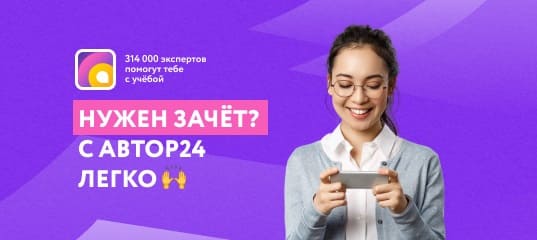
Мы поможем в написании ваших работ!