Технологические параметры точности отработки
В процессе изготовления детали на каждой последующей операции технологического процесса происходит уточнение показателей качества заготовки. Любая операция технологического процесса выполняется с определенной точностью, зависящей от многих факторов, как систематических, так и случайных.
На точность полученной на станке детали оказывают влияние параметры, связанные с неточностью получения заготовки, неточностью оборудования, оснастки, температура, возникающая при резании, износ оборудования и оснастки – технологические параметры. При разработке управляющих программ для станков с ЧПУ необходимо учитывать и геометрические параметры точности.
В общем случае погрешности обработки разделяют на теоретические и погрешности, возникающие из-за неточности работы станка.
Теоретические погрешности – погрешности, возникающие из-за заранее допущенной неточности проектирования инструмента или примененного метода обработки, использующего более упрощенную (более технологичную) схему обработки.
Погрешности обработки формируются на различных этапах технологического процесса обработки заготовки. Чем выше требования к детали, тем сложнее технологический процесс. Для получения детали заданного качества в одном технологическом процессе может быть применено несколько различных методов обработки. Каждый метод имеет свои достоинства и недостатки и имеет свои показатели качества.
|
|
При переходе от операции к операции технологического процесса производится уточнение обрабатываемой заготовки. Но, с другой стороны, каждая операция вносит свои погрешности, присущие примененному виду обработки. В общем виде суммарная погрешность определяется следующим образом:
=
,
где Δy – погрешность, вызываемая упругими отжатиями элементов технологической системы, вследствие нестабильности сил резания; Δн –
погрешность настройки станка; Δи – погрешность, вызываемая размерным износом инструмента; Δт – погрешность, вызываемая тепловыми деформациями технологической системы; ΣΔф – суммарная погрешность формы обрабатываемой поверхности в результате геометрических погрешностей станка и деформаций заготовки при ее закреплении из-за неравномерных упругих отжатий технологической системы в различных сечениях заготовки; П – попадание посторонних частиц при установке детали, приспособления или инструмента; σ – перераспределение напряжений в заготовке при механической обработке; Н – другие погрешности, связанные, например, с настройкой станка. В связи с тем, что в большинстве случаев составляющие П, σ, Н достаточно малы, общепринятой является функциональная зависимость, предложенная В.С. Корсаковым [25]:
|
|
=
.
При определении величины упругих перемещений Δ y оперируют понятием упругой системы СПИД (станок – приспособление – инструмент – деталь). Под действием сил резания происходит перемещение звеньев упругой системы, и фактический размер обрабатываемой детали будет отличаться от настроечного. Значения перемещений элементов системы СПИД зависят от жесткости упругой системы и действующих сил резания. Станки с ЧПУ отличаются повышенной жесткостью, поэтому наибольшие погрешности в системе СПИД будут зависеть от других составляющих. Например, при обработке длинных валов наибольший прирост суммарной величины Δy даст составляющая «деталь», при расточке глубоких отверстий наибольшей составляющей будет «инструмент».
Величину Δy определяют в том сечении, в котором эта величина является наибольшей.
Погрешность настройки станка Δн состоит из погрешностей настройки инструмента и приспособления. Величина погрешности, связанной с размерным износом инструмента Δи, зависит от пары режущий материал – обрабатываемый материал, метода обработки и условий обработки. Характеристикой интенсивности размерного изнашивания является относительный износ (uo) – это размерный износ (мкм), отнесенный к 1000 м пути резания: uo =1000u/l. Зная интенсивность изнашивания конкретного режущего материала при обработке конкретного материала заготовки, можно прогнозировать время изменения коррекции на инструмент и время его замены.
|
|
Температурные деформации технологической системы Δт связаны с нагревом системы СПИД в результате выделения тепла в зоне резания, из-за трения в различных узлах станка, а также поступления теплоты от внешних источников. Температура в зоне резания достигает 800…1000 °С, поэтому это основной источник теплоты. Теплота поступает из зоны плоскости сдвига, от трения по передней поверхности и от трения по задней поверхности резца. При скоростях резания более 100 – 150 м/мин (оптимальных для твердого сплава) основное тепло из зоны резания отводится стружкой. При этом уменьшается доля теплоты, передающаяся в инструмент и изделие.
Основным средством снижения температуры в зоне резания является охлаждение. При этом возрастают требования к охлаждающей жидкости и ее очистке. Многие зарубежные фирмы применяют специальное оборудование для оптимальной очистки охлаждающей жидкости. В современном оборудовании охлаждающая жидкость поступает в зону резания под большим (10 – 20 атмосфер) давлением.
|
|
Задачей проектировщика технологического процесса является минимизация суммарной составляющей δ.
Каждый режущий инструмент при резании вносит свои погрешности. Так при токарной обработке основными причинами возникающих погрешностей обработки могут быть упругие и температурные деформации резца, износ инструмента. При черновой и получистовой обработке основные погрешности возникают за счет упругих деформаций системы СПИД. При чистовой обработке основные погрешности – это температурные деформации и износ инструмента. Если инструмент работает в зоне наростообразования, то можно ожидать погрешностей из-за неудовлетворительной шероховатости.
При сверлении возникают следующие погрешности: увод сверла от заданной оси, разбивка отверстия по диаметру, неудовлетворительная шероховатость поверхности обработанного отверстия, смещение оси отверстия от базовой поверхности. Увод сверла возникает из-за продольного изгиба сверла, неплотной посадки конуса сверла в шпинделе станка, непараллельности оси шпинделя направляющим станка, неперпендикулярности поверхности детали к направлению подачи сверла. Основные причины разбивки отверстия: несоосность осей хвостовика и рабочей части сверла, смещение оси заборного конуса относительно хвостовика, неравенство режущих кромок при заточке, биение оси шпинделя станка.
При обработке отверстий резцами основные погрешности возникают за счет изгиба державок под действием сил резания, размерного износа и температурных деформаций.
При фрезеровании концевыми фрезами наиболее частой погрешностью является отклонение оси фрезы Δ под действием сил резания (рис. 2.92). Для уменьшения данной погрешности выполняют еще один проход фрезы с толщиной срезаемого слоя 0,5…0,2 мм.
Погрешность технологической оснастки в значительной мере зависит от погреш-ностей компонентов приспособления (УСП). Исследования [21] показывают, что один из самых важных компонентов УСП – координатная плита, с течением времени теряет свои эксплуатационные показатели. Это связано с несовершен-ством технологии изготовления координатных плит.
В течение их длительной эксплу-атации происходит релаксация напряжений и плита изгибается выпуклостью в сторону сетки Т-образных пазов (рис. 2.93). Выпуклость может составлять 0,3…1,4 мм. До установки приспособления на координатную плиту ее необходимо проверить на точность.
Полученная в результате технологического процесса деталь должна полностью соответствовать чертежу. Для выявления несоответствия изготовленной детали чертежу выполняют контрольные операции.
Контрольные операции назначают как после выполнения всех операций технологического процесса, так и после выполнения отдельных операций. Для контроля используют технические средства измерений.
Дата добавления: 2019-02-12; просмотров: 288; Мы поможем в написании вашей работы! |
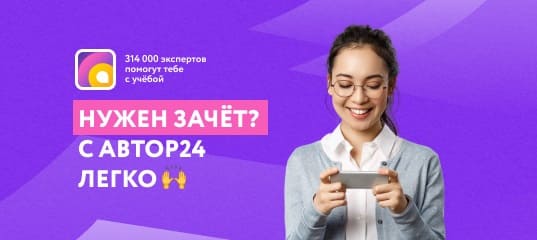
Мы поможем в написании ваших работ!