Измерение отклонений от формы цилиндрических поверхностей
Форма цилиндрических поверхно-стей характеризуется цилиндричностью, круглостью и профилем продольного сечения (рис. 2.99).
Отклонение от цилиндричности – наибольшее расстояние Δ от точки реальной поверхности 2 до прилегающего цилиндра (рис. 2.99, а).
Отклонение от круглости – наибольшее расстояние Δ1 от точки реального профиля 2 до прилегающей окружности 1 (рис. 2.99, б).
Отклонение от профиля продольного сечения – наибольшее расстояние от точек реального профиля до соответствующей стороны прилегающего профиля (рис. 2.99, в).
Прилегающий профиль продольного сечения цилиндрической поверхности – две параллельные прямые, соприкасающиеся с реальным профилем и расположенные вне материала так, что наибольшее отклонение точек образующей реального профиля от соответствующей стороны прилегающего профиля имеет минимальное значение.
Частным случаем отклонения от круглости является овальность (рис. 2.99, г).
К частным видам отклонения от профиля продольного сечения относятся конусообразность (рис. 2.99, е), бочкообразность (рис. 2.99, ж), седлообразность (рис. 2.99, з).
В некоторых случаях для оценки отклонений формы цилиндрических поверхностей в осевом направлении можно применять отклонение от прямолинейности оси – наименьшее значение диаметра, внутри которого располагается реальная ось поверхности вращения в пределах нормируемого участка. Примером такого типа отклонений формы является изогнутость (рис. 2.99, и).
|
|
Отклонения от формы цилиндрических поверхностей измеряют на специальных приборах – кругломерах, а также с помощью универсальных средств линейных измерений и приспособлений.
![]() |
Овальность определяют по наибольшей разности диаметров в двух взаимно перпендикулярных направлениях (рис. 2.100, а). Овальность равна полуразности показаний прибора. Овальность отверстий находят аналогично с помощью нутромеров.
Огранку с нечетным числом граней измеряют при установке вала в призме или кольце трехконтактным методом, при котором две точки профиля изделия соприкасаются с опорой, а одна точка – с наконечником прибора. Значение огранки определяют как наибольшую разность показаний индикатора (рис. 2.100, б, в).
Конусообразность определяют по диаметрам изделия, измеренным по краям продольного сечения, а бочкообразность и седлообразность – по краям и в середине.
Изогнутость измеряют при вращении детали на двух опорах под наконечником индикатора (рис. 2.100, г). Значение изогнутости равно полуразности наибольшего и наименьшего показаний индикатора. Для измерения отклонений от цилиндричности используют разнообразные приспособления с индикаторами.
|
|
По наибольшему допускаемому значению отклонения формы – допуску формы, цилиндрические поверхности, так же как и плоские, делятся на 16 степеней точности. Измерительные средства выбирают в зависимости от степени точности. Например, вал с номинальным значением диаметра 100 мм и поверхностью 4-й степени точности должен иметь допуск формы не более 4 мкм. Для измерений может быть использован оптиметр ОВО-1 с ценой деления 0,001 мм или индикаторная головка с ценой деления 0,001 мм с установкой вала в центрах.
Кругломеры, предназначенные для измерения отклонения от круглости, основаны на принципе образцового вращения измерительного наконечника относительно изделия, или наоборот. При измерении происходит непрерывное ощупывание цилиндрической поверхности по окружности. После одного оборота диска на бумаге записывается круглограмма проверяемого поперечного сечения изделия (рис. 2.101). Для определения круглости на круглограмму наносится прилегающая окружность 1, касающаяся выступов точек записанного профиля 2. Отклонение от круглости равно наибольшему расстоянию по радиусу от круглограммы до прилегающей окружности. На рис. 2.101 наибольшее расстояние АВ равно 6 делениям шкалы, а отклонение от круглости поверхности при цене деления 0,001 мм (увеличение 2000Х) равно 6 мкм.
|
|
Измерение твердости
Для измерения твердости предложено много методов. Основными являются методы вдавливания наконечников в материал под действием статических нагрузок: Бринелля, Роквелла, Виккерса.
Микротвердость измеряют при небольших размерах изделия (у тонких металлических лент и покрытий, фольги, проволоки, поверхностных слоев металла, мелких изделий и т.д.), прижимая к поверхности изделия алмазные наконечники различной формы.
Нормирование
Техническое нормирование устанавливает технически обоснованную норму расхода производственных ресурсов – рабочего времени, энергии, сырья, материалов, инструментов и т. д. (ГОСТ 3.1109 – 82).
Норма времени – регламентированное время выполнения некоторого объема работ в определенных производственных условиях одним или несколькими исполнителями соответствующей квалификации.
В машиностроении за единицу объема работ, на который устанавливается норма времени, принимают операцию.
Под нормой выработки Нв понимают регламентированный объем работы, которая должна быть выполнена в единицу времени в определенных организационно-технических условиях одним или несколькими исполнителями соответствующей квалификации: Нв = Т/t, где Т – время, на которое рассчитывают норму выработки (час, смена, месяц); t – норма времени (tшт или tшт. к ).
|
|
Имеются три метода установления норм времени [22]: на основе изучения затрат рабочего времени наблюдением; по нормативам; сравнением и расчетом по типовым нормам. При первом методе норму времени устанавливают путем изучения затрат времени непосредственно в производственных условиях на рабочем месте. При втором методе производят расчет длительности операции, используя нормативы длительности выполнения отдельных элементов работы (операции). При третьем методе нормирование операции осуществляется приближенно с использованием типовых норм. Первые два метода нормирования чаще применяют в серийном и массовом производствах, третий – в единичном и мелкосерийном.
При изучении затрат рабочего времени используют следующие методы: фотографию рабочего времени, хронометраж и фотохронометраж.
Фотография рабочего времени заключается в изучении затрат времени путем наблюдения и их замеров по видам на протяжении одной или нескольких смен. При этом методе главное внимание уделяют выявлению потерь рабочего времени, времени обслуживания рабочего места и времени, необходимого на отдых.
С помощью хронометража изучают затраты времени на выполнение циклически повторяющихся ручных и машинно-ручных элементов операции. Хронометраж применяют для проектирования рационального состава и структуры операции, установления их нормальной продолжительности и разработки на этой основе нормативов, которые используют при расчете технически обоснованных норм времени. Хронометраж применяют также при изучении передовых методов работы с целью их распространения.
Фотохронометраж является комбинированным методом изучения затрат рабочего времени путем наблюдения, при котором фиксируются одновременно все затраты рабочего времени в течение смены.
Штучное время есть интервал времени, равный отношению цикла технологической операции к числу одновременно изготовляемых или ремонтируемых изделий либо равный календарному времени сборочной операции.
Различают подготовительно-заключительное время, основное время, вспомогательное время, оперативное время, время обслуживания рабочего места и время на личные потребности.
Подготовительно-заключительное время – интервал времени, затрачиваемый на подготовку исполнителя и средств технологического оснащения к выполнению технологической операции и приведению в порядок после окончания смены.
Основное время – часть штучного времени, затрачиваемая на изменение и последующее определение состояния предметов труда.
Вспомогательное время – часть штучного времени, затрачиваемая на выполнение приемов, необходимых для обеспечения изменений и последующего определения состояния предметов труда.
Время обслуживания рабочего места – часть штучного времени, затрачиваемая исполнителем на поддержание средств технологического оснащения в работоспособном состоянии и уход за ними и рабочим местом.
Время на личные потребности – часть штучного времени, затрачиваемая человеком на личные потребности и, при утомительных работах, на дополнительный отдых.
Штучное время Tшт для неавтоматизированного производства состоит из элементов:
Tшт = Tо + Tв + Tт + Tорг + Tп,
где Tо – основное (технологическое) время; Tв – вспомогательное время; Tт – время технического обслуживания рабочего места; Tорг – время организационного обслуживания рабочего места; Tп – время перерывов.
Основное время Tо затрачивается на непосредственное изменение размеров, формы, физико-механических свойств или внешнего вида обрабатываемой заготовки (станочная, слесарная доводочная и другая обработка) или на соединение деталей при сборочных операциях. При обработке на станках основное время определяют расчетным методом по формуле:
Tо = lрi/ Sм,
где lр – расчетная длина обработки, мм (длина хода инструмента в направлении подачи); i – число рабочих ходов инструмента; Sм – минутная подача инструмента, мм/мин.
При ручном подводе инструмента расчетная длина обработки lр представляет собой сумму собственно длины обработки l, размера врезания (недобега) инструмента lв и размера схода (перебега) инструмента lсх:
lр = l + lв + lсх.
Схема определения расчетной длины обработки для продольного точения, сверления, фрезерования показана на рис. 2.102.
При обработке резанием на станках с ЧПУ следует учитывать путь подхода lп инструмента к заготовке для облегчения работы инструмента (рис. 2.102, б, в). Расчетная длина lр при этом увеличится:
lр = l + lп + lв + lсх.
Значения lп , lв , lсх определяют по нормативным таблицам или расчетным путем.
Вспомогательное время Tв – время, затрачиваемое на различные действия, обеспечивающие выполнение элементов работы, которые относятся к основному времени, например на установку и снятие заготовки или собираемого узла, на пуск и останов станка, на переключение режимов обработки в процессе выполнения операции, на измерение заготовок или контроль качества сборки.
В расчетах учитывается та часть вспомогательного времени, которая не перекрывается машинным временем. Вспомогательное время рассчитывается по эмпирическим формулам, в соответствии с действующими на данном предприятии нормативами, или на основе проводимого хронометража.
Часть штучного времени, равную сумме основного Tо и вспомогательного времени Tв, называют оперативным временем Tоп:
Tоп = Tо + Tв.
Оперативное время затрачивается на выполнение каждой операции и представляет собой основную часть технической нормы.
Время обслуживания рабочего места Tоб включает затраты времени на уход за рабочим местом в течение смены (смазка и чистка механизмов, раскладка и уборка инструмента в начале и в конце смены, уборка рабочего места).
Время обслуживания рабочего места устанавливают на основании нормативов и во многих случаях определяют в процентах (до 4…8%) к оперативному времени.
Штучное время рассчитывают по формуле:
Tш = Tоп (1 + α + β + γ),
где α, β, γ – коэффициенты, характеризующие, соответственно, время технического обслуживания, время организационного обслуживания и время на отдых и личные надобности.
В серийном производстве при расчете норм времени на партию заготовок необходимо учитывать подготовительно-заключительное время.
Подготовительно-заключительное время Tп-з затрачивается рабочим перед началом обработки партии заготовок и после окончания задания. К подготовительной работе относятся: получение задания, ознакомление с работой, наладка оборудования, в том числе установка инструмента, специального приспособления; к заключительной работе относятся: сдача выполненной работы, снятие специального приспособления и режущего инструмента, приведение в порядок оборудования и т.д. Подготовительно-заключительное время зависит от сложности задания, в частности от сложности налаживания оборудования, и не зависит от размера партии.
В единичном производстве подготовительно-заключительное время включается в штучное время.
В серийном производстве норму времени на обработку партии заготовок или сборку партии сборочных единиц рассчитывают по формуле:
Tп = Tшn + Tп-з,
где n – размер партии.
Штучное время и подготовительно-заключительное время на выполнение операции над одной деталью образуют норму штучно-калькуляционного времени:
Tш-к = Tш + (Tп-з/n).
На основе норм времени определяют расценки выполняемых операций, рассчитывают необходимое количество оборудования для выполнения программы, осуществляют планирование производственного процесса.
Применение CAD/CAM-систем для технологической подготовки производства значительно упрощает нормирование технологического процесса: при создании модели детали становятся известными все размеры l, а другие составляющие расчетной длины lр (lп , lв , lсх) заложены в данной системе. Определение составляющих нормы времени производится автоматически.
Дата добавления: 2019-02-12; просмотров: 776; Мы поможем в написании вашей работы! |
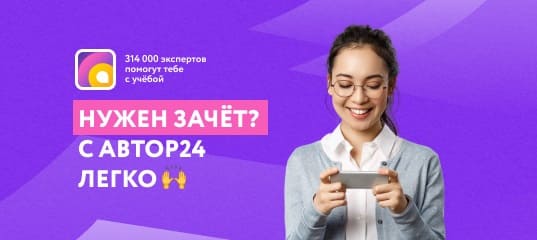
Мы поможем в написании ваших работ!