Контрольные автоматы.(контрольно-измерительные машины) 7 страница
(6.4)
или после преобразований
(6.5.)
где a - угол скоса фиксатора, который должен быть меньше угла трения и обычно равен 4°...5°, r - угол трения на скосе фиксатора, m - коэффициент трения в направляющих фиксатора.
6.7. О.М. зажимного типа.
М этого типа удерживают деталь, инструмент или связанные с ними приспособления станка в требуемом рабочем положении. Необходимую силу зажима определяют из 2-х условий:
- в затянутом стыке не должны происходить необратимые пластические деформации;
- не должно происходить открытие стыка или срыва детали под действием внешних нагрузок.
Предельное значение касательной нагрузки, когда смещение сохраняет упругий характер, может быть определено:
(6.6)
где : fy=0,12...0,15-коэффициент, равный половине коэффициента трения при трогании с места.
Суммарная сила зажима на всех поверхностях зажимного устройства получим из условия:
, (6.7)
где : Т - касательная сила от внешней нагрузки.
Зажимные устройства по конструкции подразделяются:
- механические (клиновые, винтовые, эксцентриковые, цанговые);
- магнитные (сила прижима Fy= 2....15 кг/ )
- вакуумные (Fy=1 кг/ )
- устройства с примораживанием
- устройства с приклеиванием.
|
|
7.ПРОМЫШЛЕННЫЕ РОБОТЫ В АВТОМАТИЗИРОВАННОМ ПРОИЗВОДСТВЕ.
7.1. Общие понятия о ПР.
Промышленными работами (ПР) принято считать М., выполняющие физические функции человека в производственных условиях, оснащенные системой управления.
По сравнению с другими средствами автоматизации, ПР является универсальным и наиболее эффективно применяется в гибком автоматизированном производстве, т.к. обладает свойством приспособляемости (перепрограммированию, переоснастке и переналадке) к меняющимся условиям технологической системы.
Существует три поколения промышленных роботов, характеризуемых уровнем организации системы управления(СУ).
ПР первого поколения работают по жесткой программе, составленной оператором для конкретных условий технологического процесса.
ПР второго поколения могут самостоятельно адаптироваться к изменениям внешней среды, т.е. обладают свойством самоорганизации.
ПР третьего поколения обладают свойством искусственного интеллекта.
В настоящее время массовое применение в технологических процессах нашли ПР первого положения.
ПР применяются для выполнения основных операций (сварка, сборка, покраска) и вспомогательных операций (транспортировка, установка и съем деталей и т.п.)
|
|
Возможность использования ПР в конкретных технологических процессах определяется их технологическими или эксплуатационными характеристиками:
- грузоподъемность: максимальный вес переносимого груза;
- число степеней подвижности: число линейных или угловых координат, по которым осуществляется контролируемое программное перемещение;
- количество манипуляторов с захватными устройствами (ЗУ) или количество ЗУ у манипулятора;
- быстродействие: скорость перемещения по управляемым координатам; м/с или рад/с;
- форма рабочей зоны ПР: размеры и форма пространства, внутри которого может перемещаться ЗУ с деталью. Зависит от кинематической схемы манипулятора ПР и его габаритов;
- система координат, в которой работает манипулятор ПР: зависит от кинематической схемы ПР;
- погрешность позиционирования.
7.2. Структура манипулятора ПР.
Структура манипулятора (М) ПР или его кинематическая схема определяется количеством и качеством кинематических пар( К.П. )
|
|
|
|
|
|
|
Рис.7.1 Кинематические пары ПР.
где 1-неподвижная деталь ; 2-подвижная деталь.
В свою очередь каждая из этих деталей может образовывать с другими элементами конструкции М. другие пары, создавая тем самым кинематическую схему ПР и определяя форму рабочей зоны и систему координат:
|
|
|
|
|
|
|
|

|
|
|
|
|
|
|
|
|
|
|
|
|
|
|
|
|

|
|
|
В зависимости от конкретной решаемой задачи конструкция М ПР может иметь от 1 до 5 кинематических пар.
Каждая пара , как правило, имеет индивидуальный привод:
- пневматический
- гидравлический
- электрический ( шаговые двигатели).
7.3. Условия функционирования ПР и их расчет.
При проектировании ПР и использовании их в конкретных технологических процессах выполняется ряд расчетов с целью определения жесткостных характеристик ПР и динамических характеристик. При жескостных расчетах определяют упругие перемещения в системе, в динамических расчетах определяют частоту и амплитуду колебаний в системе.
Эти параметры в конечном итоге влияют на точность позиционирования и на скорость перемещения по управляемым координатам.
В общем случае ПР кроме механической системы М имеет систему управления для обеспечении автоматической работы по заданной программе, систему ввода программы, систему информации для обеспечения прямой и обратной связи с высшей средой. Таким образом, условие функционирования ПР в технологической системе можно предоставить в виде некоторого системного окружения:
Рис.7.4.Системное окружение ПР
7.4. Некоторые особенности использования ПР в технологических процессах.
|
|
|
|
|
Рис. 7.5. Размерные связи ТС.
где: - система координат, связанная с зоной загрузки-выгрузки ПР;
- система координат, связанная с ПР;
-
система координат, связанная с базами детали; - система координат, связанная со станком;
- система координат, связанная с рабочим приспособлением станка; R1,R2,…,R4 – вектора, определяющие относительное положение соответствующих систем.
В общем виде положение относительно
определяют вектор
и поворот
относительно
.В численном виде это выглядит как:
=
, (7.1)
где : X , Y , Z – координаты вершины в
; а11, а12,…,а33 – направляющие косинусы, получаемые на основе анализа углов Эйлера.
Справедлива и следующая запись:
, (7.2)
где: и
- поворот осей
относительно соответствующих осей
.
При создании роботизированного станочного модуля необходимо с максимальной точностью закоординировать соответствующие системы координат ( в
и
в
). В значительной степени это обеспечивается точностью режима обучения ПР , которая может реализоваться двумя способами.
Первый способ используется для ПР , работающих по жесткой программе, В ручном режиме работы манипулятор с деталью в захватном механизме ориентируется относительно загрузочно-выгрузочного приспособления (спутник, призмы, тиски и т.д.) таким образом, чтобы не было зазоров между базовыми поверхностями детали и приспособления, При достижении такого положения, оно фиксируется соответствующими упорами на кинематических парах и электро-магнитными контактами соответствующих степеней подвижности М. ПР. Далее в ручном режиме деталь переводится М в рабочую зону станка и ориентируется аналогичным образов относительно технологических баз приспособления станка, Производится настройка соответствующих парных упоров и эл.-маг. контактов.
Второй способ используется для ПР с обратной связью. Процедура та же , но вместо механических упоров и КЭМ , положение управляемых координат фиксируется датчиками обратной связи СУ. Это дает возможность использовать не две , а больше точек позиционирования по каждой координате.(Обслуживать не один, а несколько станков одним ПР).
7.5.Кинематический анализ ПР.
Реальное положение детали в ТС деталь-станок-робот-накопитель в любой момент времени определяется реализацией кинематических свойств манипулятора, составленного кинематическими парами.
Положение кинематической структуры или цепи в пространстве определяется с помощью обобщенных координат – qi( i=1,…,n), характеризующих относительное перемещение в кинематических парах.
При анализе кинематики М. решаются следующие задачи:
1.Прямая задача о положении М. При решении этой задачи рассчитывают положение захватного устройства, а так же звеньев М. по заданным относительным перемещениям qi(i=1,…,n) в кинематических парах.
2.Обратная задача о положении М. С помощью этой задачи определяют обобщенные координаты qi(i=1,…,n) манипулятора по заданному в опорной системе координат положению рабочего органа или некоторого звена М.
Или графически:
Прямая задача:
Заданы qi(i=1,…,n)
Определяем
Обратная задача:
|
|





|
|



Дата добавления: 2019-02-12; просмотров: 130; Мы поможем в написании вашей работы! |
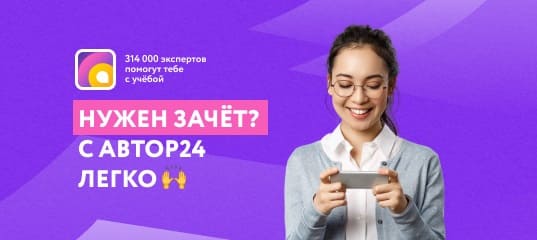
Мы поможем в написании ваших работ!