Контрольные автоматы.(контрольно-измерительные машины) 10 страница
Для повышения эффективности сборки в массовом производстве разрабатывают типовые и групповые технологические процессы, основанные на классификации сборочных единиц, характеризуемых общностью видов соединений и сопряжений.
11.2. Автоматическое сборочное оборудование.
Сборочное оборудование в зависимости от числа позиций можно разделить на два класса: однопозиционные и многопозиционные.
К однопозиционным (О) относятся сборочные станки, полуавтоматы и автоматы, на которых весь процесс сборки производится на одной позиции без перемещения базовой детали относительно рабочих органов оборудования. Однопозиционное оборудование применяется для сборки изделий с небольшим количеством деталей.
Наибольшее применение имеет многопозиционное сборочное оборудование (М), на котором сборка изделия производится одновременно на нескольких рабочих позициях; при этом собираемое изделие транспортными устройствами последовательно перемещается между рабочими позициями для выполнения процесса сборки. Классификация сборочного оборудования представлена на следующем рисунке.
Выбор соответствующего сборочного оборудования зависит от конструкции собираемого изделия, типа производства и программы выпуска изделий.
На выбор компоновки автоматического сборочного оборудования влияют габаритные размеры собираемого изделия, количество входящих в него деталей и количество сборочных операций в разработанном технологическом процессе.
|
|
|
|
|
Рис.11.1
Где:
1(а,б) – бункер-накопитель для детали «а» и «б»
2- питатель, для подачи деталей на сборочную позицию-4.
3-стол С.А.
5- автооператор для разгрузки сборочной позиции.
Многопозиционные С.А. бывают двух видов: с круглыми столами и роторные.
Многопозиционные сборочные автоматы применяют для сборки сложных изделий с достаточно большим количеством переходов.
|
|
Рис.11.2 Схема многопозиционного С.А. с круглым столом.
Поз.1.- автоматическая загрузка.
Поз.12.- автоматическая выгрузка
Поз. 2…5,7…10- рабочие позиции с бункерной загрузкой.
Пз.6 и 11-контрольные.
Цикл сборки изделия на многопозиционных сборочных автоматах производится за один оборот станка.
|
|
Роторные С.А. имеют сборочные и транспортные (питающие) роторы, которые передают собираемые изделия с одного рабочего ротора на другой.
|
|
Рис.11.3 Роторный сборочный автомат
1- питающие(транспортные роторы)
2- рабочий ротор
На роторных автоматах можно производить запрессовку, клепку, развальцовку, пайку, обжимку и др. сборочные операции.
По сравнению с другими С.А. роторные отличаются большой производительностью, но не могут, применяться для изделий сложной конструкции и крупных габаритов.
В последнее время при выполнении сборных операций, транспортировки сборочных единиц и ориентации используют сборочные промышленные работы или манипуляторы.
12. ОСОБЕННОСТИ АВТОМАТИЗАЦИИ КОНТРОЛЯ.
12.1.Назначение контроля. Виды контроля.
Важное значение при реализации безлюдной технологии отводится автоматизации контроля. Связано это с тем, что трудоемкость этой операции достаточно велика. В автоматических системах контролируется качество изделий, работоспособность инструмента, технологического и вспомогательного оборудования. В функции систем контроля входит:
|
|
- хранение информации об изготавливаемых изделиях, инструменте, оборудовании;
- проведение настройки контрольно-измерительных устройств, подналадка оборудования;
- обеспечение своевременной изоляции обнаруженного брака, сигнализации о обнаруженных отказах оборудования;
- приемочный и операционный контроль качества изделий с проверкой соответствия чертежам и техническим требованиям;
- выдача информации по результатам контроля качества изделия.
Виды контроля подразделяются в зависимости от:
- решаемой задачи : приемочный, профилактический, прогнозирующий;
- взаимодействия с обьектом контроля : активный (прямой и косвенный), пассивный (после операции или после выполнения заданной функции оборудования или оснастки);
- конструктивного решения : внутренний ( самоконтроль), внешний;
- реализации во времени : непрерывный ( в процессе изготовления или функционирования), периодический (тестовый);
- по отношению к ТП (межоперационным, операционным, послеоперационным и окончательным).
Контроль в АС может осуществляться либо с помощью контактных методов, либо бесконтактных. Контактные методы реализуются с помощью механических щупов или координатных измерительных машин. Бесконтактный контроль реализуется с помощью оптических и неоптических методов.
|
|
К оптическим методам относят:
- системы технического зрения;
- устройства со сканирующим лазерным лучем;
- фотометрические устройства и т.п.
К неоптическим методам относят :
- методы, основанные на использовании свойств электрического поля: магнитопроводность, емкость, индуктивность;
- радиоционные методы (на основе радиоволн);
- ультразвуковые методы.
В машиностроении применяют два метода контроля качества изделия : активный и пассивный. Причем, при пассивном контроле автоматически производится не только отбраковка деталей, но и сортировка годных на размерные группы и брак исправимый и неисправимый.
12.2.Средства активного контроля качества.
В зависимости от назначения средства активного контроля разделяют на четыре группы:
- устройства, контролирующие детали непосредственно в процессе их обработки на станке;
- подналадчики;
- блокировочные устройства;
- устройства, контролирующие детали перед обработкой на станке.
К первой группе относятся приборы, контролирующие размеры детали, положение режущей кромки инструмента непосредственно в процессе обработки и через цепь обработной связи подающие команду на прекращение обработки при достижении заданных размеров деталей.
Подналадчики – приборы, которые через цепь обратной связи производят подналадку станка или измерительного устройства, управляющего работой станка. Подналадчики не определяют действительные размеры обрабатываемых деталей, но контролируют и поддерживают размеры обрабатываемых деталей в пределах заданного допуска.
Блокировочные устройства контролируют детали непосредственно после их обработки на станке. Если размеры деталей выходят за заданные пределы, то блокировочные устройства подают команду на прекращение обработки.
Устройства, контролирующие заготовки перед их обработкой, проверяют предельные габаритные размеры и не пропускают на станок заготовки, выходящие за допустимые размеры. Как при активном, так и при пассивном контроле могут использоваться два метода измерения: прямой и косвенный.
Прямой метод характеризуется непосредственной оценкой значения измеряемой величины или отклонений от нее по показаниям прибора. Косвенный метод характеризуется оценкой значения искомой величины или отклонений от нее по результатам измерений другой величины, связанной с искомой определенной зависимостью.
Классификацию средств активного контроля можно представить в виде следующей схемы:
12.3.Принципиальные схемы активного контроля при контактном и бесконтактном измерении.
|
|
|
Рис.12.1 Прямое измерение.
Эти схемы измерения применяются при внутреннем и наружном шлифовании колец подшипников при измерении диаметрального размера. Прямое измерение с контактом в двух точках приззмерении диаметрального размера представлена на следующем рисунке:
|

Схема с косвенным методом измерения представлена на рис.12.3:
Рис.12.3.Схема косвенного измерения.
Прямой метод измерения имеет преимущество, т.к. исключает дополнительную погрешность передачи размера от промежуточного звена к размеру обрабатываемой детали.
Измерительные приборы для косвенных измерений как правило контролируют перемещение узла станка с режущим инструментом и положение режущей кромки инструмента относительно обрабатываемой детали.
На рис. 12.4.показана схема организации бесконтактного измерения
![]() |
|
|
Рис.12.4. Схема бесконтактного измерения.
Контрольные автоматы.(контрольно-измерительные машины)
Контрольные автоматы (КА) применяют как правило для измерения и контроля деталей после их обработки. КА бывают двух видов . КА первого вида разделяют обработанные детали на две группы : годных деталей с заданными размерами и бракованных деталей. Дополнительно эти автоматы сортируют детали с браком исправимым или неисправимым. Ко второй группе относятся КА для сортировки обработанных годных деталей по размерным группам в пределах поля допуска и используются при селективной сборке.
Автоматы производят автоматический захват, ориентирование, транспортирование, измерение и сортировку обработанных деталей с помощью спец. устройств.
КА производят выходной контроль корпусных деталей, сложных штампов, зубчатых колес, червяков, кулачковых валов; управление процессом измерения – при помощи вычислительного устройства ,связанного с АСУ автоматизированного участка. Контроль детали состоит в активном ощупывании ее по записанной в памяти управляющего вычислительного устройства программе.
КА устанавливают за ОЦ в конце участка или линии.
Диагностика ТС
Задача любого процесса контроля сводится к контролю точности детали, точности работы оборудования, выявлению причин отклонений и определению методов и средств контроля , защите от аварийных ситуаций.
Технической диагностикой называется процесс определения во времени технического состояния объекта диагностики с определенной точностью в условиях ограниченной информации.
Параметрами технического состояния обьекта диагностики могут быть качественные и количественные характеристики. Их разделяют на три группы: структурные, функциональные и сопутствующие.
Структурные - характеризуют структуру машины или механизма: величины зазоров, натягов и т.п.
Функциональные – характеризуют функционирование всего оборудования: мощность, частоту вращения, продолжительность циклов и т.д.
Сопутствующие – вибрации, шумы, изменение тока, температуру.
В условиях АП первые два вида затруднены , т.к. требуют полного или частичного разбора. Наиболее удобны для диагностирования косвенные параметры: износ инструмента можно определить по вибрации, шуму, изменению тока в электроприводе и т.д.
Задача диагностики состоит в установлении зависимости параметра технического состояния оборудования и контролируемых параметров.
Контроль состояния инструмента проводится с целью фиксации его износа и поломки, а при ударных нагрузках – выкрашивания режущих кромок. Алгоритмы контроля состояния реж. инстр. Определяются выбором места контроля в процессе обработки ( в ходе резания, в перерывах, до или после обработк) и методов контроля (прямых или косвенных).
Прямые методы контроля связаны с непосредственным измерением геометрических параметров ин-та. Прямые измерения осуществляют либо в рабочей зоне станка, либо в специальной позиции инструментального магазина. На станках с ЧПУ измерения осуществляются с помощью индикаторов контакта (ИК), служащих так же для привязки ин-та к системе координат станка. Для косвенного инструментального контроля наиболее часто применяют: контроль различных составляющих сил резания и контроль по параметрам виброакустической эмиссии. Измерение и обработка результатов измерения осуществляется в процессе резания. Первый метод связан с повышением сил резания при износе ин-та. Второй – измерение упругих волн в твердых телах, подвергнутых пластической деформации или излому. Измерение проводится пьезоэлектрическими датчиками.
Косвенный метод контроля ин-та заключается также в определении фактического времени работы ин-та и сравнении его с расчетным.
Используются различные датчики:
- измеряющие ток в якоре двигателя главного привода;
- тензодатчики на подшипниках шпинделя для измерения составляющих сил резания;
- пьезодатчики для измерения статических и динамических нагрузок ( в основном на револьверных головках);
- датчики , определяющие деформацию шпинделя;
- пьезоэлектрические высокочастотные акселерометры непосредственно на шпинделе станка;
В условиях комплексной автоматизации производства целесообразно создание автоматизированных систем диагностирования, в том числе с использованием модульных принципов построения.
13.АВТОМАТИЗАЦИЯ СРЕДСТВИНСТРУМЕНТАЛЬНОГО ОБЕСПЕЧЕНИЯ ПРОИЗВОДСТВЕННЫХПРОЦЕССОВ.
Наиболее значительные потери времени при механической обработке в условиях АП связаны с транспортированием, установкой, закреплением, съемом и наладкой инструмента и приспособлений.
Инструментальная оснастка АП состоит не только из режущего и вспомогательного инструментов, но и из приборов настройки режущего инструмента и инструментальных головок вне станка, систем автоматической смены инструментов, подналадки режущего инструмента, диагностики и контроля состояния инструмента и оборудования. Для обеспечения заданной точности при обработке широкой номенклатуры сложных и дорогих деталей без спец.приспособлений режущий инструмент должен обладать:
- высокой режущей способностью и надежностью с использованием наиболее совершенных инструментальных материалов;
- повышенной точностью за счет изготовления инструментов по спец.ужесточенным стандартам;
- универсальностью, позволяющей обрабатывать сложные детали за один автоматический цикл;
- высокой жесткостью и виброустойчивостью;
- быстросменностью;
- возможностью автоматической настройки и поднастройки.
Материал реж. части инструмента АП должен обеспечивать стабильность реж. свойств: повышенную общую и особенно размерную стойкость; прочность и надежность ин-та. Указанные требования реализуются следующими путями:
- применение дорогих, но высококачественных инстр.сталей (Р18, Р18Ф2, Р18К5, Р10К5Ф5 и т.д.);
- обеспечение мелкозернистой и однородной карбидной структурой стали (за счет включения ванадия и многократной проковки);
- применение твердых сплавов с повышенной износостойкостью (с высоким содержанием Ti и низким Со);
- применение износостойких покрытий (карбохромирование, нитрация, плазменное напыление и др.)
Дата добавления: 2019-02-12; просмотров: 690; Мы поможем в написании вашей работы! |
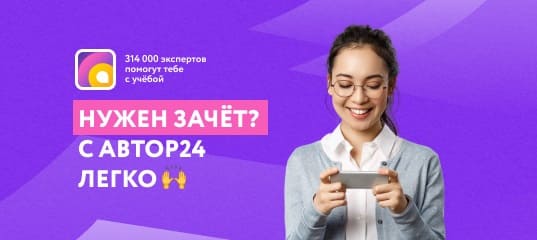
Мы поможем в написании ваших работ!