Контрольные автоматы.(контрольно-измерительные машины) 8 страница
|
C помощью кинематического расчета определяются линейные и угловые скорости и ускорения звеньев манипулятора.
;
. (7.3)
7.6.Динамический анализ движения манипулятора.
Манипулятор ПР – инерционная система, свойства которой определяются частотой и аплитудой колебаний при реализации заданных координатных перемещений.
Для анализа таких систем составляется уравнение движения на основе уравнения Лагранжа 2-го рода :
; (7.4)
где: ЕК и ЕП – кинетическая и потенциальная энергия системы или звена; qi – обобщенные координаты; Qi – обобщенные силы и моменты, учитывающие силы и моменты, развиваемые приводами и внешние воздействия.
Знание колебательных процессов, протекающих в системе М. дает возможность:
- оптимизировать конфигурацию М;
- обосновать скоростные и силовые характеристики приводов;
- оценить точность позиционирования в зависимости от времени выстоя в точке позиционирования.
Движение М при переносе груза в заданную точку можно разделить на три фазы: разгон, движение с постоянной скоростью и торможение. В наибольшей степени неблагоприятные факторы, связанные с упругой податливостью элементов М ПР, проявляются в фазах разгона и торможения. Однако упругие колебания , возникающие при разгоне, как правило успевают затухнуть за время движения во второй фазе. Наиболее существенное значение имеют колебания, возникающие при торможении вблизи заданной конечной точки позиционирования. Такие колебания снижают точность переноса груза в заданную позицию и быстродействие. Расчетное время выполнения рабочего движения увеличивается за счет времени выстоя , необходимого для затухания упругих колебаний.
|
|
8.ОРГАНИЗАЦИЯ ТРАНСПОРТНЫХ СВЯЗЕЙ В АТС,
8.1. Общие сведения
Функция транспортной системы заключается в обеспечении такого автоматического перемещения инструмента, деталей между элементами оборудования, при котором минимизируются простои систем обработки и достигается экономически целесообразное соотношение между стоимостью этих простоев и потерями из-за простоев самой транспортной системы при отсутствии заявок на обслуживание.
Перемещение материальных потоков бывает непрерывное и дискретное. Обеспечивают это перемещение промышленные роботы и дополнительное вспомогательное оборудование: конвейеры, транспортеры, робокары и т.п. Промышленные роботы выполняют выполняют транспортные операции, локальные , ориентирующие перемещения деталей и инструмента внутри рабочей зоны каждого станка, включая переориентацию, установку и снятие, касетирование д.р.
|
|
При выборе средств и способов транспортирования необходимо учитывать классификацию грузов и транспортных систем.
Грузы подразделяются:
- по массе;
- по способу загрузки (в таре, без тары , навалом, ориентированно);
- по форме ( валы, корпуса, диски,… .);
- по виду материала ( металл, неметалл, и т.п.);
- по свойствам материала(твердые, хрупкие, пластичные и т.п.)
В свою очередь транспортные средства подразделяются :
- по назначению (внутрицеховые и межоперационные);
- по способу перемещения груза ( в таре, без тары, навалом, ориентированно);
- по способу передвижения (периодические и непрерывные);
- по направлению движения (прямоточные и возвратные);
- по уровню расположения транспортной ветви( напольные, эстакадные, подвесные);
- по принципу работы (несущие, толкающие, тянущие);
- по схеме движения (линейные и замкнутые, ветвящиеся и неветвящиеся);
- по конструктивному исполнению (рельсовые и безрельсовые);
- по принципу маршрутослежения (механические, по датчикам с обратной связью, индуктивные, оптоэлектронные, радиоуправляемые).
При выборе Тр.С необходимо учитывать разделение их на основные и вспомогательные. Основные ТС проектируют централизованно и выпускаются серийно, а вспомогательные средства зачастую изготавливают по месту, т.к. их типоразмеры многообразны.
|
|
К основным транспортным средства относятся: конвейеры, транспортные роботы, устройства пневмо-гидротранспорта и т.п.
К вспомогательным транспортным средствам относят ориентаторы, толкатели, подъемники, поворотно-координатные столы, производственную тару и т.п.
8.2. Определение потребного количества ТС.
Количество ТС каждого типа определяют, исходя из машиноемкости Тм.е. транспортных операций:
(8.1.)
Вторая зависимость – в таре.
где: Q- грузопоток , Т
Тц - средняя длительность одного рейса или одного цикла работы ТС, мин
q П - средняя транспортная партия (количество грузов, привезенных за один рейс), Т
Z Т - грузопоток, ед. тары
Z ТП. – величина транспортной партии, ед. тары
, (8.2.)
где ZTi - грузопоток, ед. тары, по определенной группе изделий
Qi- грузопоток по определенной группе, Т
С i- средняя грузовместимость тары, Т
Время движения Тр.С с грузом определяют исходя из длины транспортного пути и скорости перемещения, которая не должна превышать 80 м/мин для напольного транспорта и 50 м/мин для подвесного транспорта.
|
|
Для непоточного производства время движения транспортного средства, может быть вычислено по средней длине транспортного пути.
Количество Тр.С определяется:
(8.3.)
где Кс=1,2…1,6 - коэффициент спроса, учитывающий неравномерность поступления требований по обслуживанию в единицу времени
Кз =0,7…0,8 - коэффициент загрузки транспортного средства
Фо- эффективный годовой фонд времени работы принятого типа оборудования
n- число грузопотоков, обслуживаемых данным типом транспорта.
Общее количество единиц тары одного наименования определяется:
где 1,15- коэффициент, учитывающий тару, находящуюся в ремонте и на транспортной системе;
количество единиц тары, находящейся на цеховых складах
количество тары на рабочих местах
количество единиц тары для хранения межоперационных и складских заделов на участках.
8.3. Определение времени на транспортное обслуживание.
Независимо от вида транспортного устройства, общим и одним из основных видов расчетов является расчет времени обслуживания:
(8.4.)
Тз- время загрузки транспортного устройства
ТТ- время транспортирования
Тв- время выгрузки
Как правило
Следовательно, основным резервом повышения производительности транспортного устройства является уменьшение Тт. Наиболее актуально это для транспортных систем с значительным путем транспортировки – конвейры, транспортеры.
(8.5)
время разгона
время движения с установившейся скоростью
время торможения до достижения пониженной скорости
время движения со скоростью
до полной остановки.
зависят от динамических параметров транспортного механизма.
Для перевода транспортного модуля в режим торможения используют путевые датчики, которые устанавливаются на расстоянии ТД от элементов обслуживаемого технологического
оборудования.
|
Рис. 8.1.Схема транспортного пути
SП – путь, проходимый Тр.С с изменением скорости от VП до 0.
S П = (8.6)
путь, проходимый при торможении.
Тогда путь с установившейся скоростью
определяется:
S- расстояние, которое проходит транспортное устройство при выполнении одноадресной операции
перемещение при разгоне
1) Для случая S1>SP+SТ.Д.
(8.7)
Для случая (2)- и случая (3)-
выполняются аналогичные расчеты.
Для любой многоадресной транспортной операции :
TT=d1(TT)1+ d2(TT)2+d3(TT)3 ,
Где слагаемые – доли транспортных операций 1,2 и 3 вида в общем числе транспортных операций.
Для конкретной номенклатуры деталей с известным маршрутом обработки, когда известно частности появления всех необходимых i-х одноадресных операций, время транспортирования определяется:
(8.8)
где R- общее количество транспортных операций
Для транспортной операции j-го вида (j=1,…,3) средний пробег при выполнении одноадресных операций j-го вида определим:
(8.9)
Sij - пробег при выполнении i-ой операции j-го вида
Aj - количество транспортных операций j-го вида
Тогда время обслуживания определим:
(8.10)
8.4. Организация потока материалов в ГПС.
Существует несколько вариантов компоновок ГПС, влияющих на организацию транспортного потока.
Произвольная , при которой несколько станков произвольно располагают по площади прямоугольника:
Функциональная – при которой станки (токарные, фрезерные, расточные и др.) располагают по функциональному признаку так, чтобы заготовки последовательно проходили с начала до конца ГПС.
Модульная- при которой аналогичные операции параллельно выполняются одинаковыми гибкими производственными модулями Такая компоновка обладает некоторыми свойствами резервирования:
Групповая, при которой каждая группа станков предназначена для обработки определенной номенклатуры заготовок. Эта компоновка является развитием принципа групповой технологии и обеспечивает наивысшую производительность на операциях механообработки:
Решение о принятии той или иной компоновки должно быть оптимизировано. В качестве критерия оптимизации согласно теории массового обслуживания могут быть выбраны штучное время и коэффициент обслуживания оборудования: .
Ступенчатая с группами оборудования для предварительной обработки (1), основной обработки (2), окончательной обработки (3):
Транспортные операции в выше представленных компоновках выполняют конвейеры и транспортеры.
Варианты компоновок на основеиспользования двух многоцелевых станков:
|

Здесь : 1 – многоцелевые станки; а) – с многопозиционными устройствами автоматической смены спутников, в) – с линейным потоком заготовок, с) – с кольцевым потоком заготовок; 2 – участок загрузки – выгрузки.
9.АГРЕГАТНО – МОДУЛЬНЫЕ АТС.
9.1. Общие сведения
В последнее время при разработке новой техники получил широкое распространение модульный принцип. Он заключается в построении механических, аппаратных и программных частей из более мелких унифицированных частей – модулей, которые позволяют реализовывать различные компановки из некоторого их набора. Система таких модулей обычно строится по иерархическому принципу.
В машиностроении различают модули технологические и конструкционные.
Технологические – технологическая структурная единица компановки или наименьший состав блоков компановки АС , необходимых для выполнения операций формообразования. Конструкционный модуль является единицей унификации оборудования . Это функционально и конструктивно независимая единица, которую можно использовать индивидуально и в различных комбинациях с другими модулями.
Термин « технологический модуль» понимается как структурный элемент АТС, который может включать станок, загрузочно-разгрузочное устройство, контрольно-измерительные приборы и т.д.
Унификация – это наиболее эффективный метод стандартизации , заключающийся в рациональном сокращении числа обьектов одинакового функционального назначения с целью повысить производительность инженерно- конструкторского труда , экономическую эффективность и обеспечить взаимозаменяемость.
С применением агрегатно-модульного принципа создаются следующие возможности:
- сокращение цикла разработка-изготовление-внедрение оборудования, т.к. при его создании используются готовые унифицированные модули;
- расширение области применения оборудования;
- снижение стоимости разработки –изготовлении- внедрении оборудования, скомпанованного из серийно выпускаемых модулей. Частным случаем модуля является агрегат. Он представляет собой унифицированную сборочную единицу определенного функционального назначения, Примером агрегатного построения являются агрегатные станки. Схема такого станка с фрезерной
|
|
|
где: 1 – центральная станина; 2 и 3 – боковые станины; 4 – стол поворотный; 5 – гидравлический силовой стол; 6 – подставка; 7 – вертикальный электромеханический стол; 8 –привод; 9 – многошпиндельная коробка; 10 – фрезерная головка.
Дата добавления: 2019-02-12; просмотров: 263; Мы поможем в написании вашей работы! |
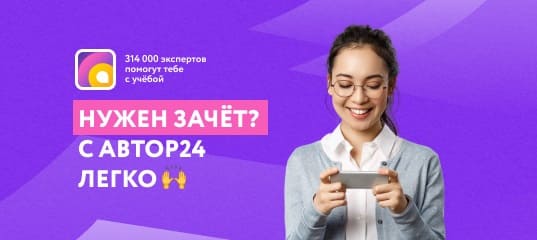
Мы поможем в написании ваших работ!