Контрольные автоматы.(контрольно-измерительные машины) 3 страница
О – общий объём продукции. Информативные показатели. Они не получили широкого распространения, хотя по аналогии с предшествующими формулами их можно определить через соотношение объёмов перерабатываемой информации машинным способом (в битах) к общему объему перерабатываемой информации в той или иной информационной технологии, например подготовке управляющих программ к станкам с ЧПУ. Энергетические показатели можно представить следующей формулой расчёта W= Эм(а)/(Эм(а) + Эр) , где Эм(а) – сумма полезной работы машин (а – при автоматизации); Эр – сумма полезной ручной работы людей, участвующих в производственном, либо технологическом процессе. Хронометрические показатели проиллюстрированы показателем dt dt= tнм/ tшт. Классификация методов оценки уровня механизации и автоматизации позволяет рассмотреть способы их практического применения. В первую очередь рассматриваемые методы анализа используют для сопоставительного анализа аналогичных производств в целях определения направлений технического перевооружения или реконструкции производственных подразделений, улучшения состояния механизации и автоматизации в них до уровня образцовых. Низкое значение показателя (См) в анализируемых цехах при высоком значении (dt) может свидетельствовать о том, что значительная часть рабочих не использует механизированное (автоматизированное) оборудование на фоне того, что другая часть рабочих, использующих высокоавтоматизированное оборудование, большую часть времени занята только наблюдением за процессом. В этой связи можно констатировать, что вопросы комплексной механизации и автоматизации решены в таких цехах неправильно. Вторичная механизация и автоматизация в результате технического перевооружения и реконструкции таких цехов была ориентирована только на участки механической обработки, полностью не были затронуты слесарные участки. В результате величина См уменьшилась за счёт роста производительности труда станочников и высвобождением их численности. Выбор объектов механизации и автоматизации в данном случае был осуществлен недостаточно тщательно, что привело к относительной «размеханизации» производственного процесса с точки зрения решения социальных задач. Анализируя способы применения хронометрического показателя уровня механизации и автоматизации труда dt можно отметить, что для крупных производственных подразделений нередко требуется использование малых выборок с целью сокращения затрат времени на аналитическую работу. Решение вопроса о применении в данном случае теории малых выборок основывается на законах распределения величины dt. Исследования показали, что на отдельно взятых операциях технологических процессов, например механической обработки, законы распределения показателя близки к нормальному. Но в других случаях, например для участка, цеха, они далеки от нормального закона распределения и описываются другими законами распределения, например законом распределения Пирсона. Теория малых выборок, которая, как известно, основывается на использовании нормального закона распределения анализируемой величины, может быть использована для распределений, близких к нормальному (наличие эксцессов, ассиметрий...), лишь бы объём выборки был не чрезмерно мал. Следовательно, для выборочного анализа показателя dt на отдельных технологических операциях с указанными ограничениями приемлема общепринятая теория малых выборок с использованием критерия Стьюдента. Более сложным является решение вопроса о применении теории малых выборок при анализе крупных структурных подразделений (участка, цеха...), так как закон распределения показателя dt резко отличается от нормального. Он описывается, как правило, кривыми распределения со следующими выравнивающими частотами: , где n0=5,817; l1=6,009; l2=2,784; g1=0,584; g2=0,354. Параметры данного распределения для цеха дают U-образный тип закона распределения Пирсона. Это обстоятельство требует иного подхода к решению задачи о применении теории малых выборок Документом, в котором фиксируют значения показателя уровня механизации и автоматизации технологического процесса, является маршрутная карта. В ней предусмотрено кодирование степени механизации и автоматизации, на основании чего определяется не только технический уровень технологии, но также должен даваться ответ на решение задачи об оптимизации технологического процесса по уровню его автоматизации. Для кодирования состояния механизации и автоматизации технологических операций в маршрутных картах технологических процессов предлагается воспользоваться двоичным алфавитом, который широко распространен в технической кибернетике. Основываясь на определении механизации и автоматизации как способах использования в технологическом процессе энергии и информации, замены энергетической и информационно-управляющей функций труда человека работой машин , можно выполнить следующую классификацию технологических операций и средств технологического оснащения в целях кодирования технологических процессов по состоянию их механизации и автоматизации. Пусть Е – обозначает энергетическую, И – информационно-управляющую функции выполнения технологической операции или процесса. Эти аббревиатуры могут дополняться индексом (м), если заданная функция выполняется машиной, и (ч) – человеком. Обозначив наличие средств технологического оснащения, в том числе и технологического оборудования аббревиатурой Т, можно на основе формул теории сочетаний для множеств {Им; Ем; Т; Ир; Ер} определить 32 теоретически возможных способа выполнения технологических операций по изготовлению продукции. Система показателей экспертной оценки уровня М и А ПП позволяет : - оценивать состояние автоматизации производства и вскрывать резервы для повышения производительности труда; - сравнивать уровни автоматизации родственных отраслей и производств; - планировать уровни автоматизации ПП и, тем самым определять направления дальнейшего совершенствования производства. 3. ТЕХНОЛОГИЧЕСКИЕ АСПЕКТЫ АВТОМАТИЗАЦИИ ПРОИЗВОДСТВЕННЫХ ПРОЦЕССОВ. 3.1.Классификация деталей автоматизированного производства. Для эффективного использования уже спроектированных средств автоматизации и для более эффективного их проектирования в системе САПР, построения базы данных – необходима их систематизация на основе классификации деталей , относительно легко ориентируемых и по-этому обрабатываемых в автоматизированном производстве Т.к. основное назначение средств автоматизации – манипулирование деталью, то мы должны оценить, насколько способствует геометрическая форма , габаритные параметры , вес, твердость, шероховатость поверхности реализации необходимых степеней свободы для придания детали заданного ориентированного в рабочей зоне станка положения. Ниже предлагается в качестве примера вариант классификации деталей ,основанный на оценке некоторых геометрических свойств деталей массового производства и их относительных параметров и типовые примеры автоматизации их манипулирования. 1. Шар . Деталь обладает ярко-выраженным свойством симметрии., не требует дополнительной ориентации. Для перемещения и транспортировки деталей такого типа используют широко самотечные устройства: лотки-скаты . Лоток - скат 2. Шар со скосом Лоток – склиз. Шар со скосом или отверстием . Могут использоваться также самотечные устройства, использующие однако другое свойство – скольжение. Условие работы таких лотков-склизов это: - коэффициент трения 3.Вал гладкий Для перемещения таких деталей широко используются как самотечные, так и полусамотечные ( приводные) средства автоматизации . На схеме представлен роликовый лоток. В такой конструкции ролики могут снабжаться приводом , например если лоток расположен горизонтально. 4. Ролик 5. Втулка Лоток - склиз Лоток- скат 6. Шайба , кольцо Геометрическая особенность таких деталей (небольшой размер L) используется на-пример в вибробункерах, для поштучной выдачи деталей из межоперационного задела . Благодаря наличию угла и вибродвижению второй и послудующие слои деталей сваливаются , а нижний слой ( за счет вибродвижения) благополучно поднимается по спиральному желобу вверх к выходному отверстию. 7, Вал ступенчатый L>D Детали такой формы с успехом могут перемещаться по наклонным профильным лоткам-скатам. 8. Стакан Емкость-накопи-тель L D В данном примере детали находятся в накопительной емкости не ориентировано ( навалом). Для ориентации и поштучной выдачи деталей используется устройство –элеватор.Здесь имеет место гибкий тяговый элемент с ориентирующими и захватными элементами стержневого типа., которые захватывают за внутреннюю полость ориентированные определенным образом детали и перемещают их. 9. Шайба со скосом, кольцо со скосом. По сравнению с простой шайбой или кольцом здесь имеет место дополнительный конструктивный признак. По-этому для полной ориентации необходимо дополнительное движение или действие, которое может быть реализовано в переориентирующих лотках. 10.Болт с головкой L > D Профильный лоток 11. Призма, короб. 12 . Брус Транспортер 13. Пластина Н Воздух под давлением Данное устройство называется пневмолоток. Используя классификацию деталей , анализируя наличие и относительное расположение осей вращения , осей и плоскостей симметрии, можно также систиматезировать и унифицировать средства манипулирования, использующие эти геометрические особенности деталей. Это повысит эффективность их разработки и внедрения. 2.2Особенности конструирования обьектов производства в условиях АПП. При конструировании изделия необходими помимо его потребительских качеств учитывать следующие обстоятельства: - конструкция изделия должна обеспечивать технологичность при изготовлении ( изготовление с минимальными затратами ресурсов); - конструкция изделия должна обеспечивать возможность использования при его изготовлении современных средств автоматизации. Что означает последний тезис? Большинство средств автоматизации при контакте с деталью для ориентации, транспортировки, фиксации, захвата действуют наощупь, т.е. их действие основывается на выявлении геометрических характеристик детали, ее конструктивных особенностей. Таким образом использование готового или проектирование нового устройства автоматизации будет основано на анализе обьектов производства по геометрических признакам или параметров ( по их наличию и относительной величине).И это необходимо учитывать при проектировании обьектов производства. Симметрия – одна из многих геометрических характеристик детали. В некоторых случаях симметря деталей способствует автоматизации, а в других – делает ее затруднительной. На пример, для организации транспортировки деталей типа тел вращения (валы, втулки, кольца) используется свойство симметрии – наличие оси вращения, Детали такого типа перемещают с помощью простейших устройств – лотков с помощью качения (а). а) На рис. б) ориентация цилиндрической детали с вертикальной осью симметрии относительно заданной системы координат облегчена, т.к. вместо 6 степеней свободы для позиционирования используется только 5 (а x , by , cz , . Поворот вокруг z не фиксируется. x y б) Однако если у детали имеются скрытые геометрические характеристики, которые необходимо фиксировать для реализации технологического процесса, например для нарезания резьбы в отверстии, то используются все 6 степеней свободы (рис.с). z x c) Сьориентировать такую деталь вокруг оси Z сложно,т.к. она явно симметрична и дополнительные внешние ориентирующие признаки не выявляются . В таких случаях в конструкцию изделия, если позволяют потребительские свойства , вносятся искусственные черты ассиметрии : В данном случае наличие дополнительного ориентирующего признака- лыски, легко обнаружить механическим путем. Взаимное сцепление деталей – одно из нежелательных явлений , вызванное конструктивными особенностями деталей. Наиболее часто это встречается при загрузке деталей в накопитель навалом. При этом возникает сцепление деталей и затрудняется их поштучная подача. Типичный пример – пружина. б) а) На рис.а) сцепление возможно за счет наличия проушин у пружины и за счет большого расстояния между витками пружины. На рис.б) эти конструктивные недостатки уменьшены. Как правило сцепление происходит у деталей , имеющих отверстия и выступы, функционально не связанные друг с другом, но размерно сопрягаемые . Соотношение размеров этих элементов у деталей должно исключать возможность сцепления с помощью внесения конструктивных изменений. На рис.а) наличие у детали выступа и отверстия приводит к сцеплению соседних деталий в случае их скопления в неориентированном виде. На рис.б) и рис.в) сцепление устранено путем конструктивных изменений. а) б) в) На последующем рисунке сцепление деталей типа разрезного кольца также устранено с помощью конструктивных изменений: Особенности конструкции изделия, обеспечивающего подачу самотеком. Для транспортировки деталей применяют устройства иногда очень простой конструкции, использующие самотечный принцип перемещения деталей под действием сил тяжести или вибрации, когда толкающее усилие передается от детали к детали . Детали как бы подталкивают друг друга. Это используется в устройствах лоткового типа в частности для плоских деталей со стабильно заданной ориентацией. Однако если детали слишком тонкие или имеют на торцевых кромках скосы, это может вызвать наползание деталей друг на друга и образование затора ,затрудняя подачу (рис.а). Для устранения этого увеличивают толщину детали. а) Может также возникнуть заклинивание деталей , если соприкасающиеся кромки не перпендикулярны направлению подачи (рис.б). Стабильность процессов обработки и манипулирования (ориентации). Деталь, поступающая на автоматизированную операцию после предшествующей обработки , имеет конструктивные параметры с отклонениями , вызванными многими независимыми случайными факторами .Таким образом параметр, по которому осуществляется ориентация, закрепление, установка или просто сопряжение детали с автоматическим приспособлением имеет поле рассеяния, имеющее форму нормального распределения: N 68,3% 99,7% Х X N – частость (плотность вероятности). В свою очередь процесс автоматического действия предполагает конструктивный размер устройства с полем допуска (размер пропускных скоб или пазов, величина расхода подвижных губок и т.д.) Соотношение между полем рассеяния размера детали и полем допуска автоматического процесса определяет стабильность, а иногда и саму возможность процесса манипулирования. Возможно четыре относительных положения этих полей. Q Q d) Q Q НГ ВГ Х НГ ВГ Х На представленных (а,в.с и d ) рисунках кривая распределения характеризует поле рассеяния размера конструктивного элемента детали . сопрягаемого с автоматическим приспособлением. Q – поле допуска приспособления с нижней границе –НГ и верхней границей – ВГ. Только в одном случае- с поле Q полностью перекрывает интервал , что означает 100% годность деталей для обслуживания автоматическим приспособлением. Заштрихованные части на рис.а,в и с определяю количество деталей, для которых применение данного конкретного автоматического приспособления невозможно. Т.е. процесс манипулирования будет нестабильным , будут отказы.
|
|
|
|
|
|
|
|
ЭЛЕМЕНТЫ АВТОМАТИЗАЦИИ.
4.1 Классификация элементов автоматизации.
Компоненты автоматизации можно условно разделить на четыре класса:
1. Датчики
2. Анализаторы
3. Исполнительные механизмы
4. Приводы
|
| ||||||||||
| ||||||||||
![]() | ||||||||||
![]() |
|
Рис.4.1.Элементы АП
В данной схеме оператор – человек, а не ПР, так как промышленный робот является частью автоматизированной системы и включает сам указанные компоненты всех четырех классов.
Датчики собирают информацию об обрабатывающем оборудовании, обрабатываемой детали и о человеке – операторе. Анализаторы регистрируют и оценивают информацию, воспринятую датчиками. После этого устанавливается очередность действия, которую реализуют исполнительные устройства.
Примером действия исполнительного механизма может служить толкатель или штанга (шибер), сталкивающие детали с конвейера – чисто физическое действие. Другой пример – замыкание электрической цепи.
Приводы, как и исполнительные механизмы, воздействуют на процессы в соответствии с командами от анализаторов. Различие между приводами и исполнительными механизмами заключается в том что, исполнительные механизмы используются для выполнения законченных дискретных коротко ходовых движений (региональные перемещения относительно рабочей зоны оборудования), обычно линейных. Приводы реализуют более продолжительные (глобальные) движения, по большей части вращательные. Исполнительные механизмы могут включать и выключать приводы. (Золотник и гидроцилиндр).
Датчики.
Служат для получения необходимой информации о параметрах ТП .
Различают датчики перемещения, положения, скорости, ускорения и т.п. По способу получения информации д. подразделяются на дискретные, фазовые и амплитудные. По способу преобразования информации - контактные и бесконтактные (емкостные, фотоэлектрические, индуктивные и т.д.). По конструкции д.подразделяются на линейные и роторные. Роторные – кинематически связаны с валом двигателя и осуществляют косвенное измерение величины перемещения рабочего органа станка. Линейные д. располагают на неподвижной части ТО и производят прямое измерение линейных перемещений рабочего органа.
Дата добавления: 2019-02-12; просмотров: 115; Мы поможем в написании вашей работы! |
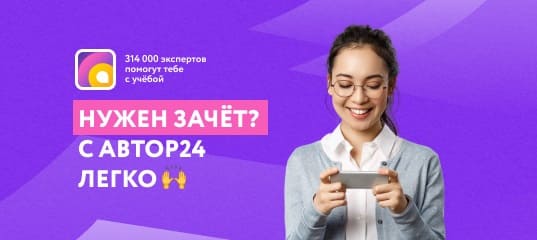
Мы поможем в написании ваших работ!