Контрольные автоматы.(контрольно-измерительные машины) 2 страница
Во-вторых, определяют экономически целесообразные методы управления, тщательно обосновывают цель и оценочную функцию управления, выбор наиболее эффективной зависимости между измеряемыми и управляющими параметрами процесса. На этой основе устанавливают правила принятия решений по управлению и выбирают стратегию поведения руководителей производства с учётом результатов экономических исследований, направленных на выявление рациональных закономерностей системы управления. Конкретные цели управления зависят от технико-экономических, социальных и других условий. Они состоят в достижении максимальной производительности процесса, стабилизации высокого качества выпускаемой продукции, наибольшего коэффициента использования топлива, сырья и оборудования, максимального объёма реализованной продукции и снижении затрат на единицу изделия и др. В-третьих, ставится задача создания инженерных методов наиболее простого, надёжного и эффективного воплощения структуры и конструкции средств автоматизации, осуществляющих заданные функции измерения, обработки полученных результатов и управления. При разработке рациональных структур управления и технических средств их осуществления применяют теорию алгоритмов, автоматов, математическую логику и теорию релейных устройств. С помощью вычислительной техники автоматизируют многие процессы расчёта, проектирования и проверки устройств управления. Выбор оптимальных решений по сбору, передаче и обработке данных основывается на методах теории информации. При необходимости многоцелевого использования больших потоков информации применяются централизованные (интегральные) методы её обработки . Структура управления, оптимально выбранная для выполнения заданных целей, в сочетании с комплексом технических средств (измерительных, регулирующих, исполнительных, по сбору и обработке информации всех видов и т. д.), во взаимодействии с объектом управления и человеком (оператором, диспетчером, контролёром, руководителем участка) на основе рационально построенных форм и потоков информации образует автоматизированную систему управления (АСУ). В современную АСУ входят устройства для первичного формирования, автоматического извлечения и передачи, логической и математической обработки информации, устройства для представления полученных результатов человеку, выработки управляющих воздействий и исполнительные устройства. В ГПС все они группируются по функциональному, информационному и конструктивно-технологическому признакам, образуя на унифицированной элементной базе блочные наборы, из которых составляются необходимые агрегатные комплексы средств автоматизации. Технические средства А. п. (Элементы автоматизации) Для автоматического извлечения информации служат датчики (первичные преобразователи). Они представляют собой весьма разнообразные по принципам действия устройства, воспринимающие изменения контролируемых параметров технологических процессов. Современная измерительная техника может непосредственно оценивать более 300 различных физических, химических и других величин, но этого для автоматизации ряда новых областей человеческой деятельности бывает недостаточно. Экономически целесообразное расширение номенклатуры датчиков достигается унификацией чувствительных элементов. Чувствительные элементы, реагирующие на давление, силу, вес, скорость, ускорение, звук, свет, тепловое и радиоактивное излучения, применяются в датчиках для контроля загрузки оборудования и его рабочих режимов, качества обработки, учёта выпуска изделий, контроля за их перемещениями на конвейерах, запасами и расходом материалов, заготовок, инструмента и др. Выходные сигналы всех этих датчиков преобразуются в стандартные электрические или пневматические сигналы, которые передаются другими устройствами. В состав устройств для передачи информации входят преобразователи сигналов (другой термин – анализаторы).Этими устройствами связываются все периферийные источники информации (клавишные устройства, датчики) с центральной частью системы управления. Их назначение — эффективное использование каналов связи, устранение искажений сигналов и влияния возможных помех при передаче по проводным и беспроводным линиям. К устройствам для логической и математической обработки информации относятся функциональные преобразователи, изменяющие характер, форму или сочетание сигналов информации, а также устройства для переработки информации по заданным алгоритмам (в т. ч. вычислительные машины) с целью осуществления законов и режимов управления (регулирования). Вычислительные машины для связи с другими частями системы управления снабжаются устройствами ввода и вывода информации, а также запоминающими устройствами для временного хранения исходных данных, промежуточных и конечных результатов вычислений и др. Устройства для представления информации показывают человеку-оператору состояние процессов производства и фиксируют его важнейшие параметры. Такими устройствами служат сигнальные табло, мнемонические схемы с наглядными символами на щитах или пультах управления, вторичные стрелочные и цифровые показывающие и регистрирующие приборы, электроннолучевые трубки, алфавитные и цифровые печатные машинки. Устройства выработки управляющих воздействий преобразуют слабые сигналы информации в более мощные энергетические импульсы требуемой формы, необходимые для приведения в действие исполнительных устройств защиты, регулирования или управления. Исполнительные устройства состоят из пусковой аппаратуры, исполнительных гидравлических, пневматических или электрических механизмов (сервомоторов) и регулирующих органов, воздействующих непосредственно на автоматизируемый процесс. Важно, чтобы их работа не вызывала излишних потерь энергии и снижения кпд процесса. Реализованная идея построения приборов для контроля, регулирования и управления в виде агрегатов, состоящих из самостоятельных блоков, выполняющих определённые функции, позволила путём различных сочетаний этих блоков получить широкую номенклатуру устройств для решения многообразных задач одними и теми же средствами. Унификация входных и выходных сигналов обеспечивает сочетание блоков с различными функциями и их взаимозаменяемость. В состав А.п. входят пневматические, гидравлические и электрические приборы и устройства. Наибольшей универсальностью отличаются электрические устройства, предназначенные для получения, передачи и воспроизведения информации. Применение универсальной системы элементов промышленной пневмоавтоматики позволило свести разработку пневматических приборов в основном к сборке их из стандартных узлов и деталей с небольшим количеством соединений Приводы -важнй элемент автоматизации. Приводы: - пневмо; - гидро; - электро (шаговые, серво и т.д.) Заключение: Комплексная А. п. требует высокого уровня научной организации труда с широким применением разнообразных вспомогательных технических средств на рабочих местах производственного и управленческого персонала. Комплексная А. п. на основе сплошной механизации, научной организации труда, широкого применения прогрессивной технологии и вычислительной техники — основное направление технического прогресса в современном машиностроении. Автоматизируются складские и транспортные операции, входной контроль, резка и раскрой материалов, рабочие и вспомогательные операции на станках (установка и фиксация заготовки, подвод и замена инструментов, перемещение на позициях обработки и отвод готовых деталей, подналадка станков). Осуществляются автоматическое регулирование режимов обработки и активный контроль изделий на станках. Создаются станки-автоматы, в том числе с программным управлением, автоматические линейные и роторные многооперационные агрегаты, жёсткие и гибкие автоматические поточные линии с гидравлическими, пневматическими, электрическими или комбинированными системами управления. Автоматизация сборочных процессов — одна из наиболее сложных и актуальных проблем машиностроения. Она не только даёт большой экономический эффект, но и способствует значительному повышению надёжности изготовляемых машин, аппаратов и приборов, т. к. в этом случае процесс сборки не зависит от квалификации сборщика. Однако автоматизация сборки требует высокой степени взаимозаменяемости деталей и узлов, при условии, что особенности технологии автоматизированной сборки учитываются уже в процессе конструирования изделий, проектирования машин, аппаратов и приборов. В наибольшей степени условиям автоматизации отвечают модульные и блочные конструкции, печатный монтаж электрических схем, широкое применение неразъёмных соединений на основе запрессовки, холодной сварки и склеивания, а также замены болтовых и винтовых соединений технологически прогрессивными и более удобными в эксплуатации разъёмными соединениями. Качество собранных узлов и изделий в целом непрерывно контролируется в ходе автоматической сборки. В машиностроении, как и в других отраслях, А. п. охватывает не только технологию, но и технико-экономическую деятельность предприятия: планирование, материально-техническое снабжение, подготовку производства, учёт и оперативное управление Так, в сфере оперативного управления автоматизируются учёт и обработка документов для составления календарного плана, сменного задания, контроля за сохранением уровня нормативных запасов деталей, материалов, инструмента и т. д. Автоматизируется также составление оптимальных квартальных, годовых и перспективных планов производства с учётом всех технико-экономических показателей Цели автоматизации -Повышение эффективности производственного процесса. -Повышение безопасности. -Повышение экологичности. -Повышение экономичности. Задачи автоматизации: -Улучшение качества регулирования -Повышение коэффициента готовности оборудования -Улучшение эргономики труда операторов процесса -Обеспечение достоверности информации о материальных компонентах, применяемых в производстве (в т.ч. с помощью управления каталогом) -Хранение информации о ходе технологического процесса и аварийных ситуациях В связи с различностью подходов различают автоматизацию следующих технологических процессов: Автоматизация непрерывных технологических процессов (Process Automation) Автоматизация дискретных технологических процессов (Factory Automation) Автоматизация гибридных технологических процессов (Hybrid Automation) 2.4. Экспертная оценка эффективности АПП. Техническое перевооружение и реконструкция производства предусматривает комплексную механизацию и автоматизацию. Комплексность (лат. complexus – 1. связь, сочетание, построение; 2. охватывание, обнимание, объятие), в том числе и механизации и автоматизации, – одна из характеристик структуры рассматриваемого объекта или явления. Комплексность есть ни что иное, как выражение доли участия некоторых или всех компонентов в реализации всей системой, т.е. всеми компонентами какого-либо явления, например автоматизации. Комплексность есть явление структурно-иерархическое, своеобразно проявляющееся на разных ступенях развития объекта рассмотрения. Применительно к производственным процессам прежде всего можно отметить комплексное усовершенствование оборудования и других средств технологического оснащения на отдельных операциях. В данном случае имеется относительно низкая, как бы первичная, ступень комплексности, где объектом (подсистемой) является технологическая операция, а её первичными компонентами орудия труда или средства технологического оснащения, используемые для выполнения технологических и вспомогательных переходов. Второй, более высокий, уровень комплексности – это построение следующего по сложности структурного образования – технологического процесса. Объектами третьей ступени комплексности могут приниматься уже не отдельные технологические процессы, а их системы, объединенные единой производственной задачей в пределах производственного участка или отделения какого-либо цеха. Четвёртой ступенью комплексности можно считать производственные процессы в пределах цеха. Пятой – комплексную механизацию и автоматизацию в рамках технологически однородной группы цехов: механических, сборочных, ремонтных, инструментальных и т.д. Шестая ступень – комплексная механизация и автоматизация предприятия в целом. Седьмая ступень относится к ассоциации, союзу или другому объединению предприятий на региональном или отраслевом уровнях. Из приведенной схемы следует, что в реализации данной системой какого-либо явления система может или вообще не участвовать, либо её участие может иметь две разновидности: единичную или комплексную (более одного) занятости компонентов. По своей природе комплексность может быть либо частичной, либо полной. Это означает, что в реализации рассматриваемого явления, например автоматизации, в первом случае участвуют не все компоненты системы, а во втором – все компоненты без исключения. Такой подход, вскрывая системные основы комплексной механизации и автоматизации, тем не менее не раскрывает смыслового содержания собственно процессов механизации и автоматизации. Эти процессы, являясь, в первую очередь, способами замены ручного труда машинным, предполагают замену орудий труда на особый вид средств технологического оснащения, называемых машинами. Изучая процессы механизации, можно отметить, что использование в трудовом процессе машины как средства механизации обеспечивает замену части или всех энергозатрат человека, необходимых для формообразования предмета труда или для перемещений. Таким образом, механизация позволяет частично или полностью устранять энергозатраты человека, необходимые для производства продукции. Вот почему механизация процесса должна рассматриваться как применение энергии неживой природы в технологическом или другом производственном процессе, полностью управляемом людьми. Она осуществляется в целях сокращения трудовых затрат, повышения качества продукции и улучшения условий труда рабочих. В отличие от механизации, процесс автоматизации производства предполагает внедрение машин, существенным отличием которых является самоуправление. Поскольку управление основывается на информационном обмене, то особенности процесса автоматизации следует рассматривать в первую очередь с учётом замены информационно-управляющей функции труда человека работой машин. Следовательно, определяя категорию «автоматизация», следует иметь в виду, что новым и особенным моментом в этом случае является применение энергии неживой природы для выполнения и управления процессами без непосредственного участия людей. Цель таких действий – также сокращение трудозатрат, улучшение условий труда и производства, повышение объёма выпуска и качества продукции. Фиксируя какой-либо процесс как сумму элементарных действий, можно определить состояние его механизации или автоматизации исходя из представлений теории множеств следующим образом : Рис.10. Диаграмма Эйлера – Венна для определения состояния механизации и автоматизации технологического процесса (оценка трудозатрат) (Р – ручной; М – механизированный; А – автоматический; мр – механизированно-ручной; ар (амр) – автоматизированно-ручной (полуавтоматический); ам – автоматизированный; ма (амр) – механизированно-автоматический) Важнейшей характеристикой любого производственного процесса, кроме затрат энергии и объёмов перерабатываемой информации, является время. Затраты времени –важнейшая исходная величина для определения не только объёма выпуска продукции, но и характеристик производственной мощности объекта технического перевооружения или реконструкции. Трудозатраты, составляющие штучного времени, содержание составных частей штучного времени по состоянию их механизации и автоматизации предопределяют также величину уровня механизации и автоматизации технологических процессов. В зависимости от хронометрического показателя уровня механизации и автоматизации оценивающего значимость и меру влияния механизации и автоматизации на технологический процесс, можно выделить различные категории их состояния. dt = tмн / tшт (tмн – машинное не перекрытое ручным время выполнения технологической операции или процесса; tшт – штучное время выполнения той же технологической операции или технологического процесса). Такая аттестация рабочих мест, участков, цехов при анализе и выборе объектов технического перевооружения на стадиях разработки проектов позволяет целенаправленно вести работы на повышение уровня механизации и автоматизации производственных процессов и в конечном счёте обеспечивать на этой основе рост производительности, так как многократно доказана тесная взаимосвязь показателя уровня механизации и автоматизации с показателями производительности труда. Кроме сказанного, показатели уровня механизации и автоматизации используются в паспортизации предприятий, цехов, для аттестации рабочих мест, в компоновочных расчётах групп многостаночного обслуживания, в расчётах запасов технологической оснастки и т.д. На предприятиях используют систему показателей уровня механизации и автоматизации, в которой каждая оценка имеет свою строгую целевую направленность и служит не только для сопоставительного анализа, но и позволяет решать другие конкретные проектно-технологические задачи. Показатели уровня механизации и автоматизации можно распределить на два больших класса: структурные и функциональные. Простые формулы расчётов можно проиллюстрировать следующими примерами. Кадровые показатели. В этом классе широко распространен расчёт - степени охвата рабочих механизированным трудом: См= Рм/(Рм+Рмр+Рр ) , где Рм – число рабочих механизированного труда; Рмр– число рабочих механизированно-ручного труда; Рр – число рабочих ручного труда. Этот показатель характеризует в первую очередь состояние механизации и автоматизации труда рабочих для решения социальных задач совершенствования производства. - уровня механизированного труда в общих трудозатратах: , - уровня механизации и автоматизации производственных процессов: - процент возрастания производительности труда за счет его М или А : , где индекс 1 соответствует показателям, полученным до проведения мероприятий по механизации или автоматизации , индекс 2 – после. Ра – число рабочих , выполняющих работу с использованием средств автоматизации; Р – общее число рабочих на обследуемом участке производства; К – коэффициент М или А , выражающий отношение времени механизированного или автоматизированного труда к общим затратам времени на данном рабочем месте; П – коэффициент производительности оборудования, характеризующий отношение трудоемкости изготовления детали на универсальном оборудовании с наименьшей производительностью, принятом за базу, к трудоемкости изготовления этой детали на автоматизированном оборудовании; М – коэффициент обслуживания, зависящий от количества единиц оборудования, обслуживаемого одним рабочим ( при многостаночном обсл. М>1 . По-машинные показатели уровня механизации и автоматизации характеризует показатель Кавт= Савт/ Собщ, где Кавт – коэффициент (уровень) автоматизации; Савт – число станков автоматического действия; Собщ – общее число станков. Кроме такого способа оценки состояния (распространенности) механизации и автоматизации широко используются различные классификационные системы оценки состояния механизации и автоматизации самих станков: от станков с ручным приводом до полностью автоматических. Продукционные методы оценки состояния механизации и автоматизации получили преимущественное распространение для анализа погрузочно-разгрузочных, транспортных и складских работ, например, расчёт У = Ом/О, где Ом – объём продукции переработанной механизированным способом;
Дата добавления: 2019-02-12; просмотров: 148; Мы поможем в написании вашей работы! |
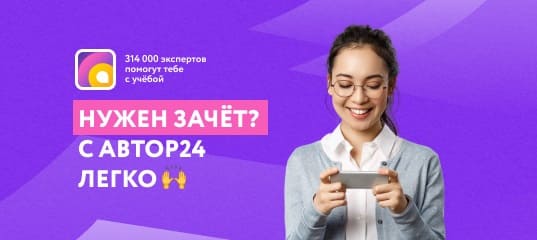
Мы поможем в написании ваших работ!