Технология выполнения прессовых соединений
Соединения с натягом получают продольно-прессовым, поперечно-прессовым и гидропрессовым методом. В соответствии с этим они и получили название:
o продольно-прессовые;
o поперечно-прессовые;
o гидропрессовые соединения.
Сущность продольно-прессового метода сборки соединений с натягом заключается в том, что одна из сопрягаемых деталей под действием осевой силы запрессовывается в другую.
Возникающие нормальные напряжения (давления) в соединении с натягом создают силы трения, обеспечивающие передачу требуемого крутящего момента или осевой силы. Их величина определяется предварительным гарантированным натягом в соединении и качеством сопрягаемых поверхностей.
Соединения прессовой посадкой, соединения конических поверхностей, шлицевые, клеммовые и другие соединения деталей машин могут быть отнесены к напряженным.
Соединения деталей, осуществляемые запрессовкой, имеют весьма широкое распространение. Наиболее распространенными запрессовываемыми деталями являются стальные и бронзовые втулки, подшипники, разного рода муфты, пальцы, оси, штифты и т. п.
При сборке прессовых соединений посадка детали всегда производится с натягом.
Натяг может быть получен запрессовкой одной детали в другую, нагревом или охлаждением одной из сопрягаемых деталей.
![]() |
Соединение деталей прессовой посадкой в холодном состоянии заключается в том, что под действием пресса охватываемая деталь вводится в отверстие охватывающей детали (запрессовка) или, наоборот, охватывающая деталь насаживается своим отверстием на охватываемую деталь (напрессовка рисунок 8.27).
|
|
При запрессовке деталей происходит холодная пластическая деформация, величина которой зависит от величины натяга. Эта деформация, сопутствуемая наклепом, оказывает влияние на структуру и свойства металлов, способствуя повышению твердости и понижению ударной вязкости. В результате не исключается возможность поломки в отдельных случаях деталей из-за хрупкости, приобретенной ими при наклепе.
Прессовые соединения выполняют на прессах с механическим приводом, пневматических и гидравлических.
В настоящее время все большее распространение получают гидравлические и пневматические прессы, на которых не только запрессовывается деталь, но и легко контролируется усилие запрессовки. А это особенно важно при сборке ответственных конструкций. В условиях серийного и массового производств запрессовку небольших деталей осуществляют на полуавтоматах и автоматах, снабженных автоматическими устройствами для подачи и ориентации сопрягаемых деталей.
|
|
Небольшие прессы (эксцентриковые и рычажные), которые развивают усилие в 10…15 кН, применяют для запрессовки деталей относительно малых размеров.
Если запрессовка детали требует усилия до 50 кН, то используют винтовые прессы с механическим приводом.
На рисунке 8.28 изображен винтовой фрикционный пресс с механическим приводом. Электродвигатель 1 через червячную передачу 2 приводит во вращение многозаходный несамотормозящий винт 3, который скользит в червячном колесе 4 в осевом направлении. Подъем винта осуществляется с помощью противовеса 5, подвешенного на тросе 6. На винте помещена гайка 7 с тормозным барабаном, который затормаживает опускание винта с помощью ленточного тормоза 8, затягиваемого нажатием на педаль 9. При опущенной педали гайка останавливается и винт, ввинчиваясь в нее, создает прессующее усилие. Как только тормоз освободится, гайка начинает вращаться вместе с винтом, который поднимается вверх противовесом.
![]() | 1 – электродвигатель; 2 – червячная передача; 3 – многозаходный несамотормозящися винт; 4 – червячное колесо; 5 – противовес; 6 – трос; 7 – гайка; 8 – тормоз ленточный; 9 – педаль Рисунок 8.28 Схема винтового фрикционного пресса с механическим приводом |
Пневматические прессы имеют широкий диапазон усилий (от 30 до 150 кН и больше) и могут конструктивно резко отличаться друг от друга (их конструкции в значительной степени определяются условиями применения).
|
|
Для получения больших усилий, от 100 до 10000 кН, используют гидравлические прессы, у которых ползун движется под давлением масла, нагнетаемого насосом.
Автоматические станки применяют для запрессовки мелких деталей.
Перед запрессовкой надо тщательно осмотреть прессуемые детали и установить, нет ли на сопрягаемых поверхностях рисок, царапин, заусениц и других подобных дефектов, которые могли возникнуть при обработке или транспортировке деталей.
В процессе запрессовки необходимо следить за правильным направлением прессуемой детали. Наличие перекоса может вызвать заклинивание и порчу поверхностей деталей. Рекомендуется применять направляющие приспособления (рисунок 8.29).
![]() | 1 — запрессовываемая деталь; 2 — оправка; 3 — охватывающая деталь; 4 — подставка Рисунок 8.29 – Запрессовка детали 2 во втулку 3 | ![]() | 1 – запрессовываемая деталь; 2 – накладка; 3 – оправка; 4 – падающий груз; Н – высота падения груза Рисунок 8.30 – Запрессовка с помощью тарированного удара |
У охватываемой детали следует делать небольшую заходную конусность в 10…15°, а у охватывающей галтель радиусом l,5…2 мм или фаску под углом 30…45°. такая форма кромок сопрягаемых поверхностей способствует взаимному центрированию деталей и предохраняет их от местных заеданий во время запрессовки. Кроме того, снятие острых кромок предотвращает сострагивание материала (последнее особенно часто встречается при запрессовке бронзовых втулок в стальные или чугунные детали).
|
|
Перед запрессовкой необходимо поверхности деталей смазывать тонким слоем машинного масла, чтобы избежать задиров и заедания сопрягаемых деталей.
Соединение деталей с помощью тарированного удара (рисунок 8.30).
В современных конструкциях часто можно встретить запрессовываемые детали конической формы (конические направляющие, валы, на которые насаживают шестерни, штифты, соединяющие муфты и кулачки с валом, шатуны с пальцами и т. д.).
![]() |
Правильность сопряжения деталей во всех конических соединениях зависит от нескольких геометрических параметров: величин наибольшего и наименьшего диаметров конуса и угла конуса (или длины конуса). Допуски на величину угла конуса обычно выражают в виде допускаемой разности предельных отклонений большого и малого диаметров конуса.
Угол конуса, как правило, очень мал, вследствие чего при запрессовке обыкновенным ручным или механическим способом могут возникать весьма большие радиальные усилия, которые вызовут остаточную деформацию или трещины, особенно в тонких стенках запрессовываемых деталей. поэтому запрессовку последних осуществляют с помощью тарированного удара, т. е. заставляя падать с определенной высоты определенный груз.
Для обеспечения более плавного прессования применяют двойные удары: падение груза в первый раз происходит с меньшей высоты, во второй – с большей.
На рисунке 8.31 показан вариант конического соединения, где диаметральный натяг у сопрягаемых деталей создается затяжкой гайки.
Дата добавления: 2019-01-14; просмотров: 1155; Мы поможем в написании вашей работы! |
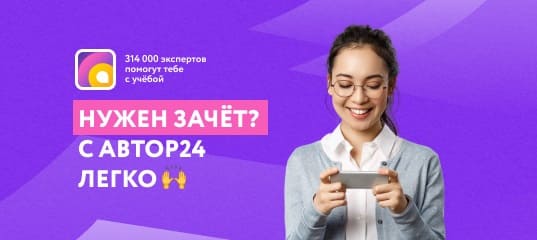
Мы поможем в написании ваших работ!