Способы выполнения неразъемных соединений сваркой
Общие сведения
Сваркой называется технологический процесс получения неразъемных соединений из металлов, сплавов и других однородных или разнородных материалов, в результате образования атомно-молекулярных связей между частицами соединяемых заготовок.
Для активации состояния поверхности с целью ослабления связей поверхностных атомов с телом и разрыва связей с атомами внешней среды требуется введение определенной энергии. Эта энергия сообщается в виде теплоты, упруго пластической деформации, а также электронного, ионного и других видов облучения.
В результате поверхностные атомы металлов и кристаллических неметаллических материалов образуют общие для соединяемых заготовок кристаллические решетки, а на поверхности пластмасс происходит объединение частей молекулярных цепей.
Свариваемость – способность материалов образовывать сварные соединения.
Свариваемость металлов определяется типом и свойством структуры, возникающей в сварном соединении при сварке.
При сварке однородных металлов и сплавов в месте соединения, как правило, образуется структура идентичная или близкая структуре заготовок. Этому случаю соответствует хорошая свариваемость материалов.
При сварке разнородных материалов в зависимости от различия их физико-химических свойств в месте соединения образуется твердый раствор с решеткой одного из материалов, либо химическое или интерметаллидное соединение с решеткой, резко отличающейся от решеток исходных материалов. В этом случае материалы относятся к категории удовлетворительно или плохо сваривающихся.
|
|
Классификация методов сварки
Способы сварки можно классифицировать либо по методу объединения поверхностей соединяемых заготовок, либо по виду применяемой энергии.
По первому признаку их можно разделить на сварку плавлением и сварку с применением давления.
При сварке плавлением происходит расплавление кромок свариваемых заготовок или присадочного материала для заполнения зазора между ними. В результате образуется общая сварочная ванна расплавленного материала. После затвердевания сварочной ванны образуется соединение в виде сварного шва.
К способам сварки плавлением относятся:
o дуговая сварка (ручная покрытым электродом, автоматическая под флюсом, газоэлектрическая и дуговой плазмой);
o электрошлаковая;
o электронно-лучевая;
o газовая;
o лазерная;
o плазменная.
Формы сварных швов, полученных плавлением показаны на рисунке 8.3.
![]() | а – стыковые; б – угловые; в – тавровый; г – внахлестку; д – с накладками Рисунок 8.3 – Формы сварных швов |
При сварке давлением заготовки соединяются путем совместной пластической деформации соединяемых поверхностей. Пластическая деформация осуществляется за счет приложения внешнего усилия, при этом материал в зоне соединения, как правило, нагревают для снижения сопротивления деформации.
|
|
В процессе деформации происходит смятие неровностей и течение материала вдоль соединяемых поверхностей. Последнее приводит к разрушению окисных пленок и частичному их удалению из зоны контакта. В результате обеспечивается плотный контакт между заготовками и условия для возникновения межатомных связей.
К способам сварки давлением относятся:
o контактная;
o газопрессовая;
o диффузионная;
o термокомпрессионная;
o ультразвуковая;
o взрывом;
o трением;
o холодная.
Впервые сварка металлов плавлением была осуществлена в России.
Русский инженер Н.Н.Бенардос в 1882 г. использовал электрическую дугу для сварки и резки металлов с использованием угольного электрода.
В 1888 г. русский инженер Н.Г.Славянов разработал способ дуговой сварки металлическим электродом.
В США в 1877 г. Томсон запатентовал способ стыковой сварки сопротивлением, основанный на нагреве поверхностей контакта между заготовками при прохождении электрического тока.
|
|
Еще через 10 лет Бенардос запатентовал устройство для точечной контактной сварки, в котором в качестве электродов были использованы угольные стержни.
Крупный вклад в развитие сварочной техники внесли разработки коллектива Института электросварки АН УССР во главе с акад. Е.О.Патоном, явившегося родоначальником автоматической дуговой сварки под флюсом. Этот способ имеет более высокую производительность и обеспечивает большую стабильность качества сварных соединений по сравнению с ручной дуговой сваркой.
В настоящее время для сварки широко применяются оптические квантовые генераторы – лазеры. Разрабатываются и совершенствуются способы сварки материалов в твердом состоянии без расплавления:
o холодной;
o диффузионной в вакууме;
o термокомпрессионной;
o взрывом и т.п.
Широкое применение сварки объясняется ее технико-экономическими преимуществами:
o снижение стоимости продукции;
o экономия металла и сокращение технологического цикла изготовления изделий по сравнению с другими способами соединения металлических частей;
o сварка позволяет получать более рациональные конструкции, используя различные профили проката;
|
|
o большой экономический эффект дает использование сварки при ремонтных работах по исправлению и восстановлению изношенных деталей, а также при исправлении брака литья;
o сварка позволяет заменить литье и кованые конструкции и детали на прокатно-сварные. В этом случае экономия металла может достигать 40…50% от массы изделия.
Электродуговая сварка
Электродуговая сварка – наиболее распространенный способ соединения металлических деталей, при котором источником тепла является электрическая дуга.
Электрическая сварочная дуга представляет собой длительный мощный электрический разряд, происходящий в газовой среде между двумя электродами или электродом и изделием.
В зависимости от среды, в которой происходит дуговой разряд, различают:
o открытую дугу, горящую на воздухе без подачи извне защитного газа или флюса;
o закрытую дугу, горящую под флюсом;
o дугу, горящую в среде защитных газов.
Сварочная дуга классифицируется по роду применяемого электрического тока. При сварке на постоянном токе различают дугу прямой и обратной полярности. При прямой полярности электрод присоединяется к отрицательному полюсу источника питания дуги (катоду), а объект сварки – к положительному (аноду). При обратной полярности электрод присоединяется к положительному полюсу источника питания дуги, а объект сварки – к отрицательному.
В практике применяют два способа дуговой сварки:
o неплавящимся электродом;
o плавящимся электродом.
Недостатком сварки при переменном токе является меньшая устойчивость горения сварочной дуги по сравнению со сваркой на постоянном токе.
По характеру механизации процесса дуговая сварка может быть:
o ручной;
o полуавтоматической;
o автоматической.
Ручной дуговой сваркой называется сварка штучными электродами, при которой подача электрода и перемещение дуги вдоль свариваемых кромок производится вручную.
Полуавтоматической называется сварка, при которой механизирована только подача электродной проволоки, а перемещение дуги осуществляется вручную.
При автоматической дуговой сварке перемещение плавящегося электрода и перемещения дуги вдоль свариваемых кромок механизированы.
Ручная дуговая сварка. Схема ручной дуговой сварки приведена на рисунке 8.4. При пропускании тока между металлическим электродом 4 и основным металлом 1 возникает дуга. Торец электрода и находящийся под ним участок основного металла расплавляются.
![]() | Рисунок 8.4 – Схема ручной дуговой сварки (стрелкой указано направление сварки) |
Дуговой разряд (пламя дуги) имеет форму, расширяющуюся к поверхности изделия, в толще которого образуется кратер дуги или сварочная ванна 3, в которую по каплям стекает расплавленный металл 6 с электрода 4. Пространство между сплавляющимся торцом электрода и поверхностью сварочной ванны заполняется раскаленной средой, состоящей из паров металла, частично ионизированного воздуха и электродного покрытия. Электрод, перемещаясь в направлении стрелки, оставляет слой напыленного металла, покрытого тонким слоем шлака 2.
Основными параметрами режима ручной дуговой сварки являются величина сварочного тока, диаметр электрода и длина дуги.
Неплавящиеся электроды изготовляют из вольфрама, электротехнического угля или графита. Графитовые электроды имеют лучшую электропроводность и более устойчивы против окисления при высоких температурах. Угольные и графитовые электроды выпускаются в виде стержней диаметром от 4 до 18 мм и длиной 250 и 700 мм и применяются только при сварке на постоянном токе. Вольфрамовые электроды применяют при сварке постоянным и переменным током.
Плавящиеся электроды в зависимости от назначения и химического состава свариваемого металла изготовляют из специальной сварочной проволоки, лент и пластин.
Электроды для ручной сварки – представляют собой проволочные стержни с нанесенными на них покрытиями. Стержень электрода изготавливается из специальной сварочной проволоки повышенного качества.
Дуговая сварка под флюсом. Из механизированных способов сварки широкое распространение нашли способы автоматической и полуавтоматической сварки закрытой дугой под флюсом. При сварке этими способами (рисунок 8.5) электрическая дуга горит между свариваемым металлом 1 и торцом электродной проволоки 2 под слоем флюса 3 и расплавляет не только электрод и основной металл, но часть флюса, окружающего дугу. Расплавленный флюс образует на поверхности расплавленного металла ванну жидкого шлака 4. Кристаллизующийся металл сварочной ванны образует по мере передвижения дуги шов 5, покрытый шлаковой коркой 6, легко удаляемой после сварки. Образующиеся при высокой температуре дуги паро- и газообразные вещества – продукты частичного испарения металла, разложение флюсов и остатки воздуха, находящиеся в слое флюса – создают вблизи дуги замкнутую газовую полость 7. Флюс защищает дугу и сварочную ванну от атмосферного влияния и обеспечивает хорошее формирование шва, отсутствует разбрызгивание металла при сварке.
![]() | Рисунок 8.5 – Схема дуговой сварки под флюсом (стрелкой указано направление сварки) |
Автоматическая дуговая сварка под флюсом позволяет:
o значительно увеличить мощность дуги до 150 кВт и более;
o повысить скорость сварки в 10... 15 раз по сравнению с ручной дуговой сваркой благодаря более полному использованию теплоты в закрытой зоне дуги и большей глубине проплавления, а также непрерывности процесса;
o улучшить качество и прочностные свойства сварных швов. Это достигается надежной защитой флюсом расплавленного металла шва, равномерностью расплавления металла в единицу времени и более медленным остыванием шва.
Автоматическую сварку под флюсом выполняют автоматическими сварочными автоматами или сварочными тракторами, перемещающимися по изделию.
Дуговая сварка в среде защитных газов. Особенность дуговой сварки в защитном газе состоит в том, что зона сварки и сварочная дуга защищаются защитным газом от вредного воздействия атмосферного воздуха. В качестве защитных газов могут применяться инертные (аргон, гелий) и активные газы (водород, окись углерода, азот).
Дуговая сварка в среде защитных газов имеет ряд технико-экономических преимуществ, к которым относится: простота процесса сварки, обеспечивающая высокую производительность и высокое качество сварных швов при соединении алюминиевых, магниевых, медных сплавов, нержавеющих и жаропрочных сталей и сплавов, а также разнородных металлов и сплавов; отсутствие необходимости применения флюсов, а следовательно, очистки швов от шлаковой корки, а также трудностей, связанных с изготовлением флюсов и электродов.
![]() |
При сварке неплавящимся электродом (рисунок 8.6,а) дуга горит между вольфрамовым электродом 3 и свариваемым изделием 1. В зону пламени 5 подается присадочная проволока 2, изготовленная из материала, близкого по химическому составу к основному металлу. Присадочная проволока и основной металл образуют сварочную ванну 6. Сварка осуществляется специальной горелкой, в которой укреплен неплавящийся электрод 3. По каналу горелки в зону дуги подается защитный газ 4.
Неплавящиеся электроды по роду материала бывают вольфрамовые и угольные. Вольфрамовые электроды в виде прутков диаметром 0,8 ...8 мм применяют при сварке в среде инертных газов, не взаимодействующих с металлом шва (аргон, гелий и их смеси), а также в среде азота, с которым вольфрам не взаимодействует даже при очень высоких температурах. Для сварки в углекислом газе вольфрамовые электроды непригодны, так как вольфрам в среде углекислого газа интенсивно окисляется и электрод сгорает.
Угольные электроды нашли применение при сварке меди и ее сплавов в среде азота на постоянном токе прямой полярности и при сварке углеродистых сталей в среде углекислого газа. При сварке других металлов и сплавов эти электроды не нашли применения из-за существенных недостатков: «блуждания» дуги и низких механических свойств сварных соединений.
Сварка плавящимся электродом в защитных газах (рисунок 8.6, б) состоит в следующем. Дуга горит между изделием и электродной проволокой 8 диаметром 0,6...3 мм, непрерывно подаваемой в дугу через наконечник горелки 7. Электродная проволока, расплавляясь при сварке, служит присадочным металлом. Защитный газ 4 через специальный канал наконечника горелки подается в пламя дуги 5. Дуга расплавляет проволоку и кромки изделия и образуется общая сварочная ванна. По мере перемещения дуги сварочная ванна затвердевает, образуя сварной шов, соединяющий кромки изделия.
Контактная сварка
Контактной называется сварка давлением, при которой нагрев; производится теплом, выделяемым при прохождении электрического тока через находящиеся в контакте соединяемые части.
Процесс контактной сварки заключается в сближении свариваемых заготовок до расстояния, при котором начинают действовать силы межатомного сцепления. Для облегчения этого сближения; свариваемые заготовки нагревают до пластического состояния или оплавления. Нагрев заготовок в машинах контактной сварки осуществляется электрическим током, проходящим через сварочный контакт и части заготовок, прилегающих к сварочному контакту (рисунок 8.7).
Свариваемые заготовки 1 зажимают в электродах 2, к которым подводится ток. Затем при помощи механизма сжатия заготовки сдавливают с усилием Р и пропускают сварочный ток. При этом происходит нагрев металла заготовок. Количество выделяющегося тепла определяется известным законом Джоуля – Ленца.
Особенностью контактной сварки является применение кратковременных (доли секунды) импульсов сварочного тока большой силы (иногда до 100 000 А) при напряжении 0,3... 10 В. Для периодического включения и выключения сварочного тока предусмотрены специальные прерыватели тока (механические, электромагнитные, электронные),
Механизмы давления обеспечивают закрепление, создание усилий сжатия и перемещения свариваемых изделий.
По форме свариваемого соединения, определяющей тип сварочной машины, различают:
o точечную;
o шовную;
o стыковую;
o конденсаторную сварки.
![]() |
Точечная сварка: вид контактной сварки, при которой соединение элементов происходит на участках, ограниченных площадью торцов электродов, подводящих ток и передающих усилие сжатия. Соединение может происходить одновременно в одной, двух или нескольких точках, положение которых определяется размещением электродов точечной машины.
Для получения точечной сварки (рисунок 8.7) очищенные от загрязнений детали 1 помещают между электродами 2 и зажимают. После создания плотного контакта между деталями включается сварочный ток, который доводит металл между электродами до плавления, а прилегающую к ядру зону – до пластического состояния. После кристаллизации расплавленного ядра ток выключается и давление снимается. Для улучшения структуры сварной точки в некоторых случаях давление перед выключением увеличивают (проковка точки). Величина давления составляет 20... 120 МПа.
Точечную сварку применяют для изготовления изделий из малоуглеродистых, углеродистых конструкционных и нержавеющих сталей, алюминия и его сплавов, химически активных и тугоплавких металлов при толщине свариваемых деталей от 0,001 до 10 мм.
Шовная контактная сварка – вид контактной сварки, при которой соединение элементов выполняется внахлестку вращающимися дисковыми электродами в виде непрерывного или прерывистого шва (рисунок 8.8).
![]() |
Шовная сварка может быть двухсторонней или односторонней.
Подготовленные полосы 1 пропускают между вращающимися роликами-электродами 2, через которые проходит электрический ток. Электроды обеспечивают необходимое усилие сжатия полос Р. В результате образуется прочный герметичный шов.
Шовную контактную сварку применяют для получения герметичных сварных швов металлов и таких же сплавов, как и при точечной сварке.
Стыковая сварка (рисунок 8.9) может быть выполнена оплавлением и сопротивлением.
При стыковой сварке сопротивлением нагрев металла выполняется без оплавления соединяемых торцов.
![]() |
Торцы деталей тщательно обрабатывают, детали сводят до соприкосновения и включают ток. После нагрева металла в месте контакта до пластического состояния давление сжатия повышают. Время протекания сварочного тока определяется косвенно через величину осадки. Величина осадки зависит от теплофизических свойств металла, конфигурации стыка и размеров детали.
Стыковая сварка сопротивлением может быть применена для сварки углеродистых, легированных сталей и цветных металлов главным образом для деталей простых сечений (круга, квадрата, кольцевого сечения).
Стыковая сварка оплавлением – вид контактной сварки, при которой нагрев металла сопровождается оплавлением соединяемых торцов. Детали сближают до соприкосновения, когда ток уже включен. В результате на торцах в местах контакта возникают дуговые разряды и происходит оплавление вначале мест контакта, а затем всего стыка. Прилегающий к стыку металл нагревается до пластического состояния и происходит его осадка. Давление, создаваемое при осадке, составляет 15... 50 МПа. В процессе осадки с торцов выдавливается жидкий металл и вместе с ним удаляются окислы и загрязнения. В результате удается получать более стабильные по качеству стыковые швы.
При стыковой сварке оплавлением свариваются те же металлы и сплавы, что и при точечной сварке. Можно сваривать разнородные металлы и сплавы с сечениями разных размеров и сложным профилем.
Конденсаторная сварка. Сущность этого прогрессивного способа сварки заключается в том, что кратковременные сварочные операции проводят благодаря энергии, накопленной в электрических конденсаторах. К первичной обмотке трансформатора (рисунок 8.10) подключают колебательный контур, состоящий из выпрямителя В, конденсатора К и прерывателя П.
![]() |
Электрическая энергия предварительно накапливается на пластинах конденсатора К и затем разряжается, нагревая свариваемые металлы 1. Мощный импульс энергий производит мгновенное плавление металла в месте стыка. Кратковременность импульса (тысячные доли секунды) создает возможность сварки деталей с различными сечениями.
Преимуществом конденсаторной сварки является значительная экономия электрической энергии. Конденсаторной сваркой можно сварить различные металлы и сочетания: вольфрам – никель, молибден – никель, алюминий – медь и т. д. Диапазон толщин свариваемых металлов находится в пределах от нескольких микронов до нескольких миллиметров.
Холодная сварка металлов
Холодная сварка представляет собой сварку давлением при значительной пластической деформации без внешнего нагрева соединяемых металлов.
Впервые холодную сварку металлических изделий успешно осуществил советский ученый К. К. Хренов. Он показал, что важнейшим условием холодной сварки является абсолютно чистая металлическая поверхность в месте контакта. Этого можно добиться, если соединяемые металлы подвергнуть значительной пластической деформации в течение сотых долей секунды. В течение этого времени приконтактный объем металла выдавливается в виде грата, а первоначально контактировавшие загрязненные и окисленные поверхности полностью удаляются. Происходит сближение чистых кристаллитов глубинных зон металла, на которых мгновенно создается стабильная металлическая связь и образуется единая кристаллическая структура.
![]() |
Холодной сваркой могут быть выполнены соединения встык и внахлестку.
Листы 1 толщиной 0,2 ... 15 мм сваривают внахлестку посредством вдавливания в толщу металла с одной или двух сторон пуансонов 2 (рисунок 8.11). Требуемая для сварки пластическая деформация обеспечивается усилием сжатия Р, величина удельного давления выбирается в зависимости от состава и толщины свариваемого металла и составляет 150... 1000 МПа, при этом деформация в месте сварки достигает 50...80%. Соединение выполняют в виде отдельных точек или непрерывного шва. Непрерывное герметичное соединение по контуру может быть получено в результате деформации одновременно по всей длине или в результате прокатывания роликами.
Качество холодной сварки зависит от подготовки свариваемых поверхностей. Последние должны быть тщательно очищены ог окисных пленок и загрязнений. Окисные пленки некоторых легко окисляемых на воздухе металлов при достаточно больших удельных давлениях разрушаются и вытесняются из зоны сварки.
Холодная сварка применяется главным образом для соединения пластичных металлов, в первую очередь, алюминиевых и медных сплавов в однородных или разнородных сочетаниях.
Для холодной сварки внахлестку могут быть использованы любые прессы, а для сварки встык – специальные машины и установки.
Ультразвуковая сварка
Ультразвуковая сварка является одним из новых способов соединения материалов и представляет собой сварку давлением при воздействии ультразвуковых колебаний.
Ультразвуковым методом можно выполнить точечную, шовную, стыковую сварку деталей. Возможно образование прямых и криволинейных швов и сваривание сечений различной формы.
Основной узел машины для выполнения точечных соединений с помощью ультразвука – магнитострикционный преобразователь 1 (рисунок 8.12). Его обмотка питается током высокой частоты от ультразвукового генератора 2. Магнитострикционный преобразователь, охлаждаемый водой, преобразует энергию тока высокой частоты в механические колебания, которые передаются волноводу 3. На конце волновода имеется рабочий наконечник 4.
![]() |
При ультразвуковой сварке соединяемые детали 5 помещают между рабочим наконечником и механизмом нажатия 6, к которому прикладывается усилие Р, необходимое для сварки. Усилие создается гидравлической, пневматической или механической системой. Сварка происходит при включенном преобразователе. Высокочастотные упругие колебания передаются через волновод на рабочий наконечник в виде горизонтальных механических перемещений, которые подвергают поверхности соединяемых деталей колебательному сдвигу с ультразвуковой частотой 15...75 кГц и амплитудой перемещения, равной 20...80 мкм. В результате действия поперечных сдвиговых колебаний происходит деформация микрообъемов, дробление хрупких окисных пленок на трущихся поверхностях и образование общих кристаллов, прочно соединяющих свариваемые детали. В зоне сварки наблюдается повышение температуры благодаря деформации и трению на контактных поверхностях.
Усилия сжатия при сварке небольшие (98...2450 Н) и вызывают незначительную деформацию поверхности в месте соединения (вмятина не превышает 5... 10%). Длительность процесса сварки зависит от свариваемого металла и его толщины. Для малых толщин она исчисляется долями секунды.
Ультразвуком можно сваривать почти все металлы и сплавы. Лучше всего свариваются пластичные металлы – алюминий, медь. С помощью ультразвука легко соединяются тугоплавкие и активные металлы – молибден, цирконий и его сплавы, титан, ниобий, тантал, некоторые марки нержавеющих сталей. Важным достоинством ультразвуковой сварки является возможность соединять тонкие листы и фольгу с деталями большой толщины, а также разнородные металлы.
При помощи ультразвуковой сварки можно соединять неметаллические материалы, например различные пластмассы, керамику, органическое стекло и полимерные материалы. Возможна также сварка неметаллических материалов с металлами.
Наряду с преимуществами ультразвуковая сварка имеет ряд недостатков: затруднительность сварки металлов толщиной более 2...2,5 мм.
Сварка взрывом
Сварка взрывом представляет собой процесс сварки, при котором соединение осуществляется в результате вызванного взрывом соударения быстро движущихся частей.
![]() |
При сварке взрывом (рисунок 8.13) соединяемые поверхности двух деталей, в частности пластин 1 и 2 располагают под некоторым углом друг к другу. На всю поверхность пластины 2 укладывают заряд 3 взрывчатого вещества слоем одинаковой толщины. Заряд взрывают при помощи детонатора 4, находящегося над вершиной угла. В качестве взрывчатого вещества используют гранулированные аммониты и гранулиты, имеющие плотность около 103 кг/м3 и скорость детонации 3000 ...4000 м/с.
В результате взрыва заряда и образования фронта ударной волны пластина 2 движется по направлению к другой, (неподвижной) пластине 1 со скоростью 1,5... 3 км/с. При таком движении метаемой пластины 2 в каждый момент времени происходит последовательное соударение поверхностей свариваемых пластин под углом а. Вершина угла, образованного пластинами, перемещается вдоль соединяемых поверхностей по направлению фронта ударной волны. В местах соударения происходит совместное деформирование поверхностных слоев свариваемых металлов. Деформирование имеет характер вязкого течения, в результате поверхности сближаются до расстояния действия межатомных сил, происходит схватывание по всей площади соединения и образование металлических связей.
Продолжительность процесса сварки не превышает нескольких микросекунд. Этого времени недостаточно для протекания диффузионных процессов, поэтому при сварке взрывом отсутствует зона, состоящая из промежуточных структур и химических соединений свариваемых металлов. Эта особенность процесса позволяет сваривать разнородные металлы, которые при сварке плавлением образуют хрупкие интерметаллические соединения, делающие швы не пригодными к эксплуатации.
Сварка взрывом применяется при изготовлении листового биметалла, при плакировании поверхностей конструкционных сталей металлами и сплавами с особыми физическими и химическими свойствами, а также при сварке заготовок и некоторых деталей из разнородных металлов.
Перспективным является применение сварки взрывом для соединения армированных металлов, получения из порошков монолитных металлов и сплавов, а также сочетание сварки взрывом со штамповкой, прессованием, ковкой.
Диффузионная сварка
Способ диффузионной сварки был предложен в 1953 году советским ученым Н. Ф. Казаковым.
Диффузионная сварка – процесс сварки давлением, осуществляемый благодаря взаимной диффузии атомов контактирующих поверхностей при относительно длительном воздействии температуры и при незначительной пластической деформации.
![]() |
Свариваемые детали 1 (рисунок 8.14) помещают в охлаждаемую камеру 2 и вакуумными насосами создают разрежение в камере. Обычно сварку проводят в вакууме при остаточном давлении среды Па. После создания требуемого разрежения в камере производится нагрев свариваемых деталей с помощью индуктора 3 от генератора токов высокой частоты 6. По достижении требуемой температуры и равномерного ее распределения по сечению свариваемых деталей к ним прикладывается сжимающее усилие. Шток 4 гидро- или пневмоцилиндра вводится в камеру через вакуумное уплотнение или сильфон 5. Температура и давление в контакте поддерживаются постоянными в течение всего времени сварки.
Температура сварки составляет 0,7...0,9 от температуры плавления менее тугоплавкого металла или сплава, входящего в соединение. Величина давления в зоне контакта зависит от свойств металла, температуры сварки и других факторов и может изменяться от 3 до 100 МПа. Значение давления в контакте примерно равно пределу текучести свариваемых металлов при температуре сварки.
Совместное действие температуры и давления приводит к облегчению деформации микронеровностей, увеличению площади истинного контакта и возникновению металлических сил связи.
Время выдержки (сварки) при заданной температуре и давлении необходимо для обеспечения плотного контакта и прохождения диффузии атомов через поверхность соединения. Время сварки зависит от свойств свариваемых материалов, температуры и составляет от нескольких минут до десятков минут. Диффузионные процессы, развиваясь во времени, способствуют ликвидации первоначальной границы раздела, образованию диффузионной зоны и прочного сварного соединения.
Охлаждение свариваемых деталей до температуры 100...300°С производится в камере с приложенным давлением.
Способы подготовки и обработки поверхностей свариваемых деталей оказывают большое влияние на прочность соединений при диффузионной сварке. Удаление поверхностных окисных пленок и различного рода загрязнений производится механической обработкой и обезжириванием органическими: растворителями, а предупреждение их образования в процессе сварки достигается использованием вакуума. В качестве защитной среды могут использоваться инертные газы.
Сварку производят в специальных сварочных установках.
К достоинствам диффузионной сварки следует отнести высокое качество сварных соединений и возможность получать соединения разнородных металлов, сплавов и неметаллических материалов. С помощью диффузионной сварки получены соединения таких пар металлов, сплавов и неметаллических материалов, выполнить которые другими методами сварки или невозможно, или очень, трудно. Например, сварены: титан с нержавеющей сталью, алюминием, платиной, медью; алюминий со сталью, вольфрам с ниобием; молибден, ниобий со сталями. Этот метод позволяет сваривать фольгу никеля, алюминия, платины и др. различной толщины с массивными деталями. Получены соединения различных металлов: с неметаллическими материалами – керамикой, кварцем, стеклом,, графитом, ситаллом, сапфиром и др.
Сварка металлов трением
Сварка трением представляет собой процесс сварки давлением,, при котором нагрев осуществляется трением, вызываемым вращением одной из свариваемых деталей (рисунок 8.15,а) или обоих (рисунок 8.15,б), сжимаемых усилием Р.
![]() |
Механизм образования соединения при сварке трением условно' можно разделить на две стадии – нагрева и проковки (сварки).
На поверхностях деталей, прижатых усилием Р, возникают силы трения. В начале процесс протекает при незначительных температурах 100...120° С и характеризуется сухим или граничным трением поверхностей свариваемых деталей. При этом происходит смятие и срез микровыступов, разрушение окисных пленок и их удаление из стыка. Работа, затраченная на преодоление этих сил, превращается в теплоту, которая выделяется на поверхностях трения и вызывает интенсивный нагрев деталей до состояния повышенной пластичности. Происходит макропластическая деформация поверхностных слоев металлов и вытеснение их из зоны сварки в радиальном направлении. В зону контакта вступают чистые поверхности металла, между которыми возникают металлические связи.
Объем поверхностного слоя нагреваемого металла настолько незначителен, что весь цикл его нагрева составляет от нескольких секунд до одной минуты.
Основными технологическими параметрами этой стадии процесса являются:
o скорость вращения;
o величина давления;
o время нагрева.
По достижении требуемой температуры относительное движение деталей практически мгновенно прекращается, при этом прекращается и тепловыделение. Процесс образования сварного соединения завершают проковкой, т. е. к нагретым, но уже неподвижным деталям прикладывают сжимающее усилие. Величину давления при проковке прикладывают в 2...2,5 раза больше по сравнению с давлением при вращении. Процесс проковки длится несколько секунд. После проковки происходит естественное охлаждение.
Сварка трением обладает рядом преимуществ:
o высокой производительностью;
o малым потреблением энергии и мощности;
o высоким качеством сварных соединений;
o стабильностью качества.
При сварке трением не предъявляется высоких требований к чистоте свариваемых поверхностей и точности их обработки, особенно при сварке однородных материалов. На поверхности трения недопустима лишь окалина. Ее присутствие может привести к образованию некачественного соединения. Этим сварка трением выгодно отличается от контактной.
Одним из важнейших преимуществ сварки трением является возможность получения прочных соединений не только однородных, но и большого числа сочетаний разнородных металлов и сплавов, теплофизические свойства которых резко различны, например, меди со сталью, алюминия и некоторых его сплавов со сталями, алюминия с титаном и т. п.
Сварку трением применяют при изготовлении составного режущего инструмента, различных валов (рис. 5.16,а), сварноштампованных деталей, биметаллических трубчатых переходников (см. рис. 5.16,6) и др.
Применение сварки трением ограничивается формой и размерами сечения свариваемых деталей. При вращательном движении сварка трением позволяет получить соединение, когда одна из деталей представляет собой тело вращения (стержень или трубу).
Электронно-лучевая сварка
Электронно-лучевая сварка относится к сварке плавлением, при которой для нагрева соединяемых частей используется энергия электронного луча.
![]() |
Схема процесса сварки электронным лучом в вакууме представлена на рисунке 8.16. Электронный луч с большой плотностью энергии создается в специальном приборе – электронной пушке. Пушка имеет катод 1, который питается от высоковольтного источника 2 постоянного тока и может нагреваться до высоких температур. Катод размещен внутри прикатодного электрода 3. В результате нагрева катода до высоких температур (порядка 2500° С) его электроны приобретают скорость (15000...20000 км/ч), достаточную, чтобы покинуть металл – возникает эмиссия электронов. На некотором расстоянии l от катода расположен ускоряющий электрод (анод) 4 с отверстием. Прикатодный и ускоряющий электроды благодаря своей форме фокусируют электроны в пучок с диаметром, равным диаметру отверстия в аноде. Положительный потенциал ускоряющего электрода может достигать нескольких десятков тысяч вольт, поэтому электроны на пути к аноду приобретают значительную скорость и энергию. Для увеличения плотности энергии в пучке электроны фокусируются магнитным полем в специальной магнитной линзе 5. Сфокусированные в плотный пучок летящие электроны ударяются с большой скоростью о малую площадку свариваемых металлов 7. Вследствие торможения кинетическая энергия электронов превращается в теплоту, нагревая металл до температуры плавления.
Для установки электронного луча и перемещения его по линии сварки используется магнитная отклоняющая система 6.
Чтобы обеспечить свободное движение электронов от катода к аноду и предотвратить возможность возникновения дугового разряда между электродами, процесс сварки ведут в вакууме. При этом заметно уменьшается содержание вредных примесей в металле шва и повышается его качество. Вакуум в камере Па создается насосной системой установки.
Электронный луч – наиболее эффективный источник нагрева металла при сварке. Плотность энергии в луче достигает 5…108 Вт/см2, что примерно на два порядка выше плотности энергии в электрической дуге. При хорошей фокусировке и достаточной мощности электронный луч обеспечивает получение узкой и глубокой зоны проплавления, что является одним из основных преимуществ электронно-лучевой сварки. Это делает его перспективным для сварки металлов больших трещин (200...500 мм).
Сварка электронным лучом осуществляется в специальных установках для электронно-лучевой сварки (ЭЛУ).
Электронно-лучевая сварка находит применение для соединения как малогабаритных изделий микроэлектроники, так и крупногабаритных изделий длиной и диаметром в несколько метров.
Сварка пластмасс
Неразъемные соединения из пластмасс получают сваркой и склеиванием. Образование неразъемного соединения является результатом взаимной диффузии молекул полимера в контактирующих поверхностях или химической реакции присоединения.
Термореактивные пластмассы обычными методами не свариваются. Их соединяют механическим способом либо склеиванием.
Термопластичные пластмассы (полистирол, полиамид, полиакрилат, поликарбонат и др.) способны многократно подвергаться нагреву, не теряя исходных свойств после охлаждения. Эта группа пластмасс способна к переработке и сварке.
Все применяемые в настоящее время методы сварки связаны с нагревом в месте контакта и приложения давления. По использованию источников нагрева методы сварки пластмасс можно разбить на две группы.
Одна группа объединяет методы сварки, в которых использована теплота посторонних источников теплоты: газовыми теплоносителями, нагревательными элементами.
В другой группе объединены методы, в которых теплота генерируется внутри пластмассы в процессе преобразования различных видов энергии – токов высокой частоты, ультразвуковых колебаний, трения, инфракрасного излучения и химических реакций.
При выборе метода сварки необходимо учитывать толщину материала, свойства пластмассы, тип конструкции.
Сварка газовыми теплоносителями – наиболее распространенный и простой метод. Кромки свариваемых деталей нагревают горячими газами (воздухом, аргоном, азотом и др.) либо продуктами сгорания горючего газа, выходящего из сопла специального сварочного пистолета. Сварка может проводиться с применением присадочного материала или без него. Свариваемые поверхности деталей и присадочный пруток нагревают до вязкотекучего состояния струей газа и немного прижимают свариваемые детали.
Прочность соединений при сварке в значительной степени зависит от типа соединения и состояния поверхности свариваемого материала.
При сварке тонкого материала применяются стыковые и нахлесточные соединения. Поверхность кромок должна быть тщательно очищена и обезжирена. Рекомендуется удалять глянцевые поверхности, так как прочность сварных соединений значительно уменьшается. Глянец снимают наждачной бумагой или шабером.
Сварка нагретым инструментом является наиболее универсальным методом и имеет несколько разновидностей в зависимости от применяемой оснастки.
Схема контактно-тепловой сварки представлена на рисунке 8.17. Соединяемые детали 1 нагреваются от соприкосновения с инструментом – роликами 2 и сжимаются под действием незначительного усилия Р.
Инструмент в виде роликов и лент применяют для сварки швов значительной протяженности. Для сварки коротких и фасонных швов используют нагреватели типа паяльников, электроутюгов. Этим методом можно сваривать фторопласт, полиэтилен, полистирол и другие пластмассы.
![]() | Рисунок 8.18 – Сварка токами высокой частоты |
Сварка токами высокой частоты (т. в. ч.) основана на преобразовании электрической энергии в тепловую непосредственно внутри материала (рисунок 8.18). Различают точечную, роликовую и прессовую сварку т.в.ч.
Детали 1 из пластмассы помещают в переменное электрическое поле высокой частоты, которое создается между электродами – роликами 2. Под действием т. в. ч. пластмассы равномерно по толщине нагреваются до температуры вязкотекучего состояния. Давление Р, приложенное к электродам, создает тесный контакт между свариваемыми поверхностями.
Токами высокой частоты можно сваривать такие материалы, как поливинилхлорид, толщиной до 5 мм. Такие пластмассы, как фторопласт, полиэтилен, полистирол и некоторые другие непосредственно токами высокой частоты не свариваются.
Сварка трением пластмасс осуществляется по тому же принципу, что и сварка металлов. Сварку трением применяют для деталей, имеющих форму тел вращения из твердых термопластмасс.
Сварка ультразвуком основана па нагреве контактирующих поверхностей при превращении энергии ультразвуковых колебаний в тепловую.
Сущность процесса ультразвуковой сварки пластмасс и устройства машин для сварки те же, что и при сварке металлов. При сварке пластмасс механические перемещения конца волновода перпендикулярны к свариваемым поверхностям и происходят в одном направлении с прилагаемым давлением. Разогрев материалов происходит только на контактирующих поверхностях, что исключает возможность перегрева.
Ультразвуком можно сваривать все термопласты, отвержденпые пластики и разнородные пластмассы толщиной до 10 мм.
Сварка полимеров с помощью инфракрасного (ИК) излучения основана на явлении превращения лучистой энергии в тепловую внутри материала. В качестве источников ИК-излучения используют кварцевые излучатели, силитовые стержни и никельхромовые сплавы.
![]() |
Схема сварки внахлестку с помощью инфракрасного излучения показана на рисунке 8.19. Для сварки листы 1 укладывают на эластичную подложку 2, изготовленную из материала, поглощающего ИК-лучи (поролон, микропористая резина, прорезиненная ткань черного цвета). Прижимное устройство 3 фиксирует материал в натянутом состоянии и ограничивает зону нагрева. Нагрев осуществляют от источника ИК-лучей 4. Упругость подложек, плотно прижатых к листам, обеспечивает необходимое давление их друг па друга, обеспечивая сварку.
Инфракрасным излучением можно сваривать все пленки, переходящие при нагреве в вязкотекучее состояние. Толщина свариваемых материалов составляет 1,5...2 мм. Сварка ИК-излучением дает возможность сваривать многолистовые пакеты.
Относительная прочность сварных соединений при испытании на расслаивание в среднем составляет 75...85%.
Дата добавления: 2019-01-14; просмотров: 966; Мы поможем в написании вашей работы! |
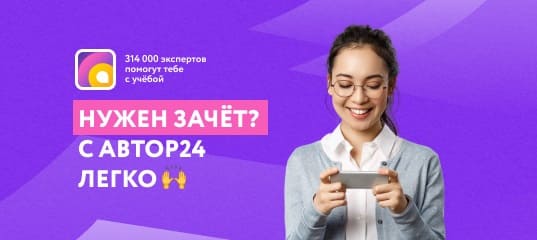
Мы поможем в написании ваших работ!