Способы выполнения неразъемных соединений пайкой
Nbsp;
Технологические процессы сборки
Общие сведения о сборке
Сборка – образование соединений составных частей изделия.
Объектом сборки в процессе сборки являются составные части изделия или изделие в целом. В зависимости от объекта сборку подразделяют на общую, объектом которой является изделие в целом, и узловую, объектом которой является составная часть изделия – узел (сборочная единица).
Стадия сборки характеризует процесс сборки по степени его законченности. По стадиям различают:
o предварительную сборку с последующей разборкой с целью определения размера компенсатора;
o промежуточную – для совместной обработки сборочной единицы (например, отверстие под вкладыш подшипника растачивается совместно после сборки корпуса и крышки подшипника);
o окончательную.
Организация производства характеризует сборку изделия или его составных частей в различных условиях организации выполнения технологического процесса. По этому признаку сборка разделяется на следующие виды:
o типовая поточная;
o групповая поточная;¨групповая непоточная;
o единичная.
Поточная сборка характеризуется тем, что при построении технологического процесса сборки длительность операций сборки согласуются в соответствии с тактом выпуска изделий. При этом рабочие места размещаются в порядке выполнения операций технологического процесса. Поточная сборка сокращает длительность производственного цикла, уменьшает межоперационные заделы деталей, повышает специализацию сборщиков и возможности механизации и автоматизации сборочных операций, что приводит к снижению трудоемкости сборки на 30…50%.
|
|
Непоточная сборка с расчленением сборочного процесса сборка каждой сборочной единицы выполняются в одно и то же время разными бригадами и многими сборщиками. Рабочие места сборщиков устанавливаются по типам применяемого оборудования и оснастки.
Подвижность объекта сборки отражает возможность перемещения изделия или его составных частей с одного рабочего места на другое.
По возможности перемещения объекта сборки сборка подразделяется на стационарную и подвижную. Стационарная сборка характеризуется тем, что весь процесс сборки и его сборочных единиц выполняется на одной сборочной позиции: на стенде, на станке, на рабочем месте и т.п. Подвижная сборка характеризуется тем, что рабочие, выполняя отдельные операции сборки, остаются на своих рабочих местах, а собираемое изделие перемешается от одного рабочего места к другому. Перемещение может быть свободным или принудительным.
Механизация и автоматизация сборки характеризует изготовление изделия или его составных частей в зависимости от степени замены ручного труда машинным. По этому признаку сборка разделяется на ручную, механизированную и автоматизированную и автоматическую.
|
|
Сборка является заключительным этапом изготовления машины. Высокое качество машины определяется не только конструкцией и применением высококачественных материалов, но и качеством выполнения сборочных операций.
Вопросы для самоконтроля
1. Что такое сборка?
2. Дать классификацию сборочных соединений.
3. Дать классификацию видов сборки.
4. Как разделяются сборочные процессы по организации выполнения работ?
5. Как разделяются сборочные процессы по методам достижения точности соединений?
Содержание сборочных операций
При реализации технологических процессов сборки выполняются следующие виды сборочных работ.
Подготовительные – приведение деталей и покупных изделий в состояние, необходимое для сборки: расконсервация, мойка, сортировка на размерные группы, укладка в тару и т.п.
Пригоночные – обеспечение сборки соединений и технических требований к ним: опиливание, зачистка, шабрение, притирка, сверление, развертывание, правка, гибка и т.п.
|
|
Собственно сборочные – взаимное ориентирование и соединение двух и более деталей с целью получения сборочной единицы: свинчивание, запрессовка, сварка, склеивание, завальцовка и т.п.
Регулировочные – достижение точности взаимного расположения деталей и сборочных единиц в изделии.
Контрольные – проверка соответствия параметрам, установленным чертежом и техническими условиями на сборку.
Демонтажные – частичная разборка изделия с целью подготовки их к упаковке и транспортированию к потребителю.
После разработки технологического процесса сборки осуществляют его нормирование. При поточной сборке в состав штучного времени включается время на транспортирование собираемого изделия, если оно не перекрывается другими элементами штучного времени. Длительность операции при этом должна быть равна или кратна такту выпуска. К основным технико-экономическим показателям сборки относятся: действительный такт выпуска, ритм работы потока, производительность сборочного рабочего места, коэффициент загрузки рабочего места или поточной линии, трудоемкость сборки, себестоимость сборки, коэффициент слесарно-сборочных работ.
В состав технологического процесса сборки включают также операции контроля и испытаний отдельных механизмов, узлов и машины в целом (точность, бесшумность, плавность движения и т.д.).
|
|
Чистота деталей и узлов – одно из условий достижения высокого качества как сборки изделий, так и их функционального назначения.
Металлические опилки, мельчайшие кусочки стружки остатки обтирочных материалов, абразивный порошок, попадая в отверстия или каналы деталей, могут впоследствии, при работе машины, попадать со смазкой в подшипники или зазоры других подвижных соединений и вызывать их интенсивный износ и задиры.
Для предотвращения этого детали и узлы в процессе сборки проходят специальные операции – очистки и мойки. Эти операции достаточно трудоемкие, и на их выполнение расходуется до 10% времени, затрачиваемого на изготовление деталей.
Очистка узлов и деталей от слоя антикоррозионной смазки, следов краски на поверхностях и других твердых загрязнений может быть осуществлена механическим путем, при помощи приводных и ручных щеток, с последующей мойкой и обдувкой сжатым воздухом.
Для мойки деталей используются различные способы:
o химический (мойка с окунанием и струйная мойка с применением органических растворителей);
o электрохимический (в спокойном или принудительно возбуждаемом электролите):
o ультразвуковой.
В серийном и массовом производствах используются специальные моечные машины (однокамерные, двухкамерные и трехкамерные), в которых процесс мойки деталей и узлов осуществляется в закрытом пространстве без участия рабочего.
Большую роль в обеспечении чистоты деталей и узлов на сборке играет обдувка их сжатым воздухом, которую целесообразно производить перед каждой сборочной операцией.
Пригонка деталей при сборке обычно осуществляется в условиях единичного и мелкосерийного производств. Пригоночные работы при сборке выполняются с помощью механизированных универсальных и специализированных инструментов с электрическим, пневматическим и, реже, гидравлическим приводом.
Процесс пригонки может включать в себя следующие технологические операции:
o опиливание и зачистку;
o притирку;
o полирование;
o шабрение;
o сверление;
o развертывание;
o торцевание и шарошение;
o гибку.
Опиливание и зачистка производится вручную или с использованием механических инструментов. После опиливания поверхность зачищают напильниками, надфилями, абразивными кругами, головками и брусками.
Для механизации работ по опиливанию и зачистке целесообразно использовать верстачные или передвижные установки с гибким валом, приводящие в движение специальные напильники или абразивные головки.
Притирку при сборке применяют в тех случаях, когда необходимо получить точный размер деталей за счет снятия очень малого припуска или для достижения плотного прилегания поверхностей, обеспечивающего гидравлическую непроницаемость соединения. Точность размеров, достигаемых при притирке до 0,1 мкм. В качестве примера можно привести притирку плунжерных пар гидронасосов.
Существует два способа притирки деталей:
o одной детали по другой (притирка клапанов, пробок и др.);
o каждой из деталей по притиру (детали топливной аппаратуры, крышки, торцы, фланцы и буртики в плотных сопряжениях).
Полирование применяют при сборке для достижения меньшей шероховатости поверхностей, подвергавшихся опиливанию или зачистке.
Для полирования применяют механизированные шлифовальные или быстроходные сверлильные машинки. При большом объеме полировальных работ применяют ручные полировальные машины с эластичным кругом, работающим торцовой поверхностью.
Шабрение плоских поверхностей (плоскости разъема, направляющие) или цилиндрических поверхностей (вкладыши подшипников, втулки и др.) при сборке производят для обеспечения плотности прилегания и увеличения контурной площади контакта. Шабрение при сборке осуществляют шаберами вручную.
Сверление при сборке применяют:
1. когда требуемая точность совмещения отверстий достигается проще всего путем обработки двух или более деталей в сборе;
2. если место сверления труднодоступно для обработки на станке, а отверстие небольшого диаметра и может быть просверлено с помощью механизированного инструмента:
3. когда сверление не было предусмотрено при механической обработке (например, для постановки пробок, при обнаружении пористости в литых деталях: станине, картере, блоке, различных корпусах и т.д.), если это допускается техническими требованиями.
Сверление в сборочных цехах производится: на сверлильных станках, электрическими и пневматическими сверлильными головками.
Развертывание применяется при сборке для получения требуемой посадки в соединении или для обеспечения соосности отверстий монтируемых деталей.
Для механизации процесса развертывания применяют электрические или пневматические сверлильные машинки с дополнительными редукторами, понижающими частоту вращения шпинделя до 30... 50 об/мин.
Гибочные работы при сборке машин выполняют главным образом в связи с пригонкой различных трубопроводов, а также для стопорения соединения деталей (шплинты и т.д.).
Медные и латунные трубки малого диаметра (до 8 мм) при больших радиусах закругления (более 10...12 диаметров), обычно гнут вручную в холодном состоянии. Трубопроводы с диаметром 8… 14 мм изгибают с надетой на место сгиба стальной пружиной. При больших диаметрах такая пружина вставляется внутрь трубы. Трубы диаметром более 20 мм гнут после наполнения их песком или расплавленной канифолью. Это делается, чтобы сохранить поперечное сечение трубы и предотвратить ее от появления микротрещин.
Стальные трубы диаметром до 10 мм гнут без нагрева и без наполнителя, трубы больших размеров гнут в горячем состоянии.
Вопросы для самоконтроля
1. Назовите виды сборочных работ.
2. Содержание подготовительных работ.
3. Способы мойки деталей перед сборкой.
4. В каких случаях применяются пригоночные работы. Способы пригонки.
5. В каких случаях применяется сверление при сборке. Применяемое оборудование.
6. Гибочные работы при сборке машин. Применяемое оборудование.
Оборудование сборочных цехов
Оборудование сборочных цехов можно разделить на две группы:
o технологическое;
o вспомогательное.
Технологическое оборудование предназначено для выполнения технологических операций по осуществлению соединений, регулировке и контролю в процессе общей и узловой сборки.
Вспомогательное оборудование предназначено для выполнения вспомогательных операций: консервации и расконсервации, промывки, обезжиривания, транспортирования, складирования, подъема и т.п.
К технологическому оборудованию при сборке неподвижных разъемных соединений относят одно- и многошпиндельные установки для выполнения резьбовых соединений.
Сборку неподвижных неразъемных соединений осуществляют запрессовкой на прессах, а также путем термического воздействия (нагревом или охлаждением) на одну или обе сопрягаемые детали.
При сборке с нагревом охватывающей детали применяют электропечи, индукционные печи, для нагрева мелких деталей – масляные ванны и другие нагревательные устройства.
Сборка с охлаждением охватываемой детали выполняется на специальном оборудовании, в которых в качестве хладоагента используется сжиженный газ (кислород, азот), твердая углекислота и т.п. Прочность соединений, полученных с охлаждением охватываемой детали выше в 2…2,5 раза, чем при запрессовке.
К вспомогательному оборудованию относятся подъемно-транспортные средства, установочное оборудование и т.п. Транспортные средства предназначены главным образом для перемещения объектов сборки: рольганги и транспортеры. Перемещение объектов сборки в вертикальном направлении осуществляется подъемниками: талями, полиспастами, консольные поворотные краны, специальные подъемники, манипуляторы, роботы.
Вопросы для самоконтроля
1. Назовите виды технологического оборудования сборочных цехов.
2. Назовите виды вспомогательного оборудования сборочных цехов.
Методы выполнения соединений
Классификация соединений
Соединения классифицируются по ряду признаков:
o сохранение целостности при разборке;
o возможность относительного перемещения;
o форма сопрягаемых поверхностей;
o метод образования сборочного соединения.
Разъемным называется соединение, разборка которого происходит без нарушения целостности составных частей изделия.
Соединение, при разборке которого нарушается целостность составных частей изделия, называется неразъемным.
В подвижном соединении имеется возможность относительного перемещения составных частей изделия.
Соединение, в котором отсутствует такая возможность, называется неподвижным. При неподвижном соединении сопряженные детали или узлы сохраняют неизменное взаимное положение, достигнутое при сборке.
Метод образования соединения при сборке определяется конструкцией соединяющей детали (клин, штифт, шпонка и т. д.) или процессом образования соединения (сварка, пайка, клепка и т.д.).
По форме сопряженных поверхностей соединения разделяются на:
o плоские;
o цилиндрические;
o конические;
o сферические;
o винтовые;
o профильные;
o комбинированные.
Метод образования соединения характеризует конструктивные и технологические особенности образования соединения при сборке составных частей изделия.
Рисунок 8.1 – Виды соединений
Наиболее распространенными способами осуществления неразъемных соединений являются:
o пайка;
o сварка;
o склеивание;
o клепка;
o развальцовка;
o пластическим деформированием материала деталей.
Вопросы для самоконтроля
1. По каким признакам сборочное соединение относят к определенному виду?
2. Назовите виды соединений по признаку целостности при разборке.
3. Назовите виды соединений по признаку возможности относительного взаимного перемещения.
4. Назовите виды соединений по форме сопрягаемых поверхностей.
5. Перечислите методы выполнения соединений.
Способы выполнения неразъемных соединений пайкой
Пайка – процесс получения неразъемного соединения материалов при нагреве соединяемых материалов ниже температуры их плавления, путем смачивания, растекания и заполнения зазора расплавленным припоем..
Пайкой можно соединять детали из углеродистых и легированных сталей, серого и ковкого чугуна, медные, алюминиевые и т. д., а также и разнородные детали: стальные с чугунными, стальные с алюминиевыми, чугунные с медными и т. п.
В зависимости от температуры плавления различают припои высокотемпературные (твердые) и низкотемпературные (мягкие).
Высокотемпературные припои имеют температуру плавления выше 500°С и предел прочности 60…500 МПа. Эти припои представляют собой сплавы на основе серебра, меди, никеля, хрома, титана и др. металлов. Твердые припои разделяются на легкоплавкие с температурой плавления до 875оС и тугоплавкие с температурой плавления выше 875оС.
Низкотемпературные припои имеют температуру плавления ниже 400°С и предел прочности до 70 МПа (оловянно-свинцовые, висмутовые, кадмиевые и др.).
Этапами ТП пайки являются:
o подготовка поверхностей соединяемых деталей;
o покрытие флюсом;
o лужение;
o пайка.
Подготовка поверхностей деталей сводится к удалению загрязнений, ржавчины, окалины и жировых пленок.
Покрытие флюсом подготовленных поверхностей производят непосредственно перед лужением или пайкой. Флюсы защищают основной металл и припой от окисления, растворяют или восстанавливают окисные пленки, улучшают смачиваемость поверхностей, способствуют растеканию припоев. Флюсы применяют в твердом, жидком или газообразном видах (порошки, пасты, растворы газов). Роль флюса может выполнять вакуум или специальные газовые смеси.
Сам процесс пайки сводится к прогреву места соединения после нанесения припоя до его расплавления, сжатия соединяемых деталей для фиксирования их взаимного расположения до полного затвердевания припоя.
Для пайки деталей из алюминиевых сплавов, имеющих очень прочные окисные пленки, затрудняющие пайку, применяются специальные ультразвуковые паяльники. На расплавленный припой воздействуют ультразвуковые колебания от рабочего стержня паяльника, вибрирующего с частотой 20…25 кГц. Под действием этих вибраций частицы окислов разрушаются, и припой входит в контакт с чистой основой сплава соединяемых деталей. Облуженные алюминиевые детали могут затем паяться обычным паяльником.
При пайке применяют различные формы соединения:
o внахлестку;
o стыковые;
o соединения в ус (рисунок 8.2 ).
![]() | а – соединения внахлестку; б – соединения встык и в скос; в – соприкасающиеся соединения; г – соединения в угол; д – соединения в тавр; е – комбинированные соединения Рисунок 8.2 – формы соединений при пайке |
Основные параметры конструктивных элементов паяного соединения:
o толщина;
o ширина;
o длина капиллярного участка шва.
Зазор между соединяемыми деталями должен быть малым, чтобы обеспечит затекание припоя в зазор под действием капиллярных сил.
Введение в зазор между соединяемыми деталями припоя паяльником является малопроизводительным методом пайки. Для повышения производительности труда применяют специальные печи. В этом случае предварительно очищенные соединяемые детали собирают таким образом, чтобы у места соединения можно было поместить припой в виде проволочного контура. Собранный узел помещают в электрическую печь, где он нагревается до температуры плавления припоя, но не выше температуры плавления материала собираемых деталей. Расплавленный припой благодаря хорошему смачиванию им поверхностей собираемых деталей и вследствие явления капиллярности проникает в соединительный шов и образует сплав, обладающий после затвердения прочностью более высокой, чем прочность припоя.
Высокую производительность и хорошее качество дает пайка погружением в ванну. ванну загружают расплавленным припоем и окунают в нее собранный узел, покрытый в месте спая флюсом, а по остальной поверхности – защитным покрытием (графитом). После определенной выдержки в ванне (5…20 мин.) узел вынимают и дают стечь избытку припоя.
При пайке твердым припоем применяют соляные ванны из смеси расплавленного хлористого калия и хлористого бария. Подвергаемые пайке узлы с прокладками припоя окунают в ванну. Расплавленная соль растворяет окислы, способствует смачиванию расплавляющимся припоем мест соединений и после пайки защищает узел от окисления на воздухе.
Вопросы для самоконтроля
1. Поясните сущность процесса пайки и лужения. Детали из каких материалов можно соединять пайкой.
2. Виды припоев в зависимости от температуры плавления. Их свойства и состав.
3. Технология подготовки поверхностей под пайку.
4. Флюсы. Их назначение. Виды флюсов.
5. Технология пайки.
6. Особенности пайки алюминиевых сплавов.
7. формы соединений при пайке.
8. Оборудование для пайки.
Дата добавления: 2019-01-14; просмотров: 728; Мы поможем в написании вашей работы! |
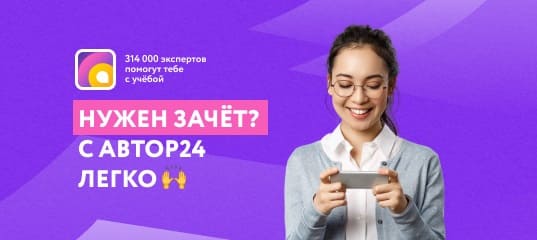
Мы поможем в написании ваших работ!