Контроль качества сварных соединений
для предупреждения и обнаружения дефектов сварных соединений, существует предварительный, промежуточный и окончательный методы контроля. При выполнении контактной сварки особое значение имеет предварительный и окончательный контроль.
Предварительный контроль предусматривает контроль: состояния исходных материалов, подготовка и сварка сопрягаемых поверхностей (плотность их прилегания, зачистка, величина переходного контактного сопротивления и т.д.); основных параметров сварки (величины тока, продолжительности импульса тока и т.д.).
Окончательный контроль предусматривает: наружный осмотр швов и изделий, механические испытания сварных соединений, испытание соединений и изделий на плотность (выполненных шовной сваркой), микро- и макроструктурные испытания, просвечивание швов рентгеновскими лучами, а также ультразвуковой контроль.
Внешний осмотр позволяет выявить поверхностные дефекты с лицевой стороны сварного шва: (выплески, непровары, подрезы, наплывы, перегрев, припаи, пористость), наличие коробления изделия в целом. Сварные изделия, требующие плотных швов (баки, резервуары, выполненные шовной сваркой) подвергают после сборки керосиновой пробе, гидро- и пневмоиспытаниям по методике, описанной выше.
Механическим испытаниям подвергают образцы-свидетели, сваренные в тех же условиях и из того же металла, что и само изделие.
Или, в особых случаях, вырезанные из самого изделия. Эти образцы испытывают на статическое растяжение, изгиб, отрыв и на повторно статическое растяжение. Особо ответственные сварные изделия подвергают выборочно механическим испытаниям целиком.
|
|
Металлографический анализ сварных соединений позволяет выявлять внутренние поры, раковины, микротрещины, перегрев. Его проводят на макро- и микрошлифах, вырезанных из образцов, предназначенных для механических испытаний.
Наиболее объективным является контроль качества соединений с помощью рентгеновских лучей. метод позволяет выявить дефекты внутри шва без его разрушения.
Вопросы для самоконтроля
1. Сущность соединения деталей сваркой.
2. Свариваемость металлов. Сущность.
3. Классификация методов сварки?
4. Виды сварных соединений и швов.
5. Чем объясняется широкое применение сварки в промышленности?
6. Электродуговая сварка. Физическая сущность. Разновидности.
7. Технология и область применения ручной дуговой сварки.
8. Дуговая сварка под флюсом. Сущность. Область применения.
9. Дуговая сварка в среде защитных газов. Сущность. Область применения. Разновидности.
10. Сущность и область применения точечной контактной сварки.
|
|
11. Сущность и область применения шовной контактной сварки.
12. Стыковая сварка сопротивлением. сущность и область применения.
13. Конденсаторная сварка. Сущность и область применения.
14. Холодная сварка металлов. Сущность и область применения.
15. Ультразвуковая сварка. Сущность и область применения.
16. Сварка взрывом. Сущность и область применения.
17. Диффузионная сварка. Сущность и область применения.
18. сварка трением. сущность и область применения.
19. Электронно-лучевая сварка. сущность и область применения.
20. Сварка пластмасс. Методы сварки пластмасс. Технология сварки.
21. Контроль качества сварных соединений.
22. Сущность и область применения холодной сварки?
Технология выполнения неразъемных клеевых соединений
Склеиванием можно соединять детали из различных материалов (металла, пластмассы, фибры, эбонита, древесины и др.), причем две склеиваемые, детали могут быть как из одного и того же материала, так и из разных материалов. Соединения, полученные этим способом, обладают достаточной прочностью, герметичностью, водо- и маслостойкостью, высокой стойкостью к вибрационным и ударным нагрузкам. Кроме того, использование способа склеивания упрощает технологию ремонта и сборки машин.
|
|
Для склеивания деталей чаще всего применяют карбинольный клей с катализатором и наполнителем. В качестве катализатора используют 2…3%-ную перекись бензола; порошкообразными наполнителями могут являться цемент, гипс, окись цинка и др.
Перед склеиванием деталей поверхности, подлежащие склеиванию, должны быть хорошо очищены, обезжирены и просушены. Если соединяемые детали имеют поверхности высокой чистоты, то рекомендуется абразивной шкуркой или напильником увеличить шероховатость этих поверхностей и тщательно протереть их ацетоном.
Клей наносят стеклянной палочкой равномерным слоем на склеиваемые поверхности, которые затем соединяют, проверяют взаимное положение собранных элементов контрольными инструментами или приспособлениями. В зафиксированном состоянии соединение сушат.
Соединения, собранные на клее, обеспечивают достаточную прочность.
Конструктивно клеевые швы аналогичны сварным швам. На рисунке 8.20 показаны примеры выполнения клеевых соединений.
Наиболее распространенным способом соединения пластмасс между собой и с металлом является склеивание.
![]() |
Соответствующие поверхности обязательно следует сделать шероховатыми и очистить от загрязнений, в особенности от жира.
|
|
При склеивании металлических деталей с пластмассовыми используют клеи БФ-2 и БФ-4 и карбинольный клей, а при склеивании слоистых пластиков — смоляные клеи ВИАМ-53 и др., не требующие высокой температуры.
Детали склеивают клеями БФ-2 и БФ-4 при температуре 140…150°, давлении 0,5…1 МПа и времени выдержки 30…60 мин.; карбинольным клеем – при температуре 20…45°, давлении 0,02…0,5 МПа (в зависимости от толщины склеиваемых деталей) и времени выдержки 12—24 часа.
Клеевое соединение деталей из пластмасс прочнее и экономичнее соединения на заклепках.
Вопросы для самоконтроля
1. Сущность соединения деталей склеиванием.
2. Подготовка поверхностей под склеивание.
3. Формы клеевых соединений
4. Технология склеивания.
Дата добавления: 2019-01-14; просмотров: 187; Мы поможем в написании вашей работы! |
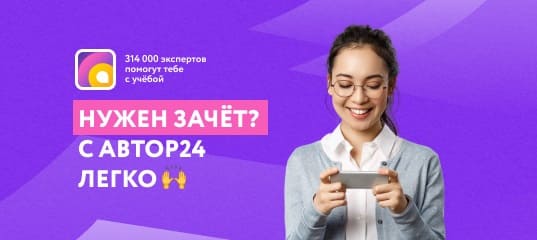
Мы поможем в написании ваших работ!