ПРИЕМКА АВТОМОБИЛЕЙ В РЕМОНТ, ИХ РАЗБОРКА, МОЙКА И ДЕФЕКТАЦИЯ ДЕТАЛЕЙ
Для наружной мойки агрегатов применяют моечные установки проходного или тупикового типа. Они отличаются от установок для наружной мойки автомобилей меньшими габаритами. Наружную мойку таких агрегатов, как двигатели автомобилей ЗИЛ-431410, ЯМЗ-238, рекомендуется проводить на установке проходного типа ОМ-4267 с подвесным транспортером или тупикового типа ОМ-837Г.
Тщательная наружная мойка автомобилей и агрегатов является одним из важнейших условий, обеспечивающих высокую производительность труда и сохранность деталей при разборке автомобилей.
РАЗБОРКА
Разборка — один из ответственных технологических процессов ремонта автомобилей. От качества ее выполнения зависит число деталей, которые могут быть использованы повторно, объем работ по восстановлению деталей, а следовательно, экономика и качество ремонта.
Разборку автомобиля начинают со снятия кузова, кабины, оперения, топливных баков, радиатора, приборов электрооборудования и топливной аппаратуры. Затем отсоединяют механизмы управления, снимают двигатель, коробку передач, передний и задний мосты и другие агрегаты и узлы.
В зависимости от годовой программы предприятия применяют непоточный или поточный методы организации разборки.
При непоточном (тупиковом) методе автомобиль (агрегат) разбирают от начала до конца на одном рабочем месте. Этот метод организации разборки применяют при сравнительно небольшой производственной программе предприятия.
|
|
Наиболее прогрессивным является поточный метод организации разборки, при котором весь объем работ по разборке автомобиля разбивается между отдельными бригадами рабочих и выполняется ими последовательно на всех ремонтируемых объектах. Промежуток времени, за который на поточной линии разбирают одно изделие, называется тактом разборки. Благодаря специализации рабочих по выполнению отдельных операций при поточной разборке повышаются качество и производительность труда. При этом методе можно шире использовать средства механизации и автоматизации работ, что очень важно, поскольку разборочные работы имеют высокую трудоемкость.
К средствам механизации и автоматизации разборочных работ относятся: подъемно-транспортные устройства, разборочные стенды, механизированный инструмент, приспособления для разборки.
Подъемно-транспортные устройства служат для подъема снимаемых при разборке составных частей автомобиля и транспортировки их на соответствующие участки производства. К ним относятся конвейеры с тележками 5 и 6 для установки агрегатов при поточном методе разборки автомобилей и агрегатов (рис. 101); подвесные конвейеры для транспортировки снятых при разборке агрегатов узлов и деталей; крановые устройства типа кран-балок, консольных кранов, монорельсов с электротельферами и т. п.
|
|
Стенды для разборки служат для установки агрегатов при их разборке. При разборке коробки передач ее устанавливают в кронштейны 2 поворотного стола / (рис. 102). Перед проведением работ положение коробки передач фиксируют стопорным устройством 4. К стендам для разборки предъявляют следующие требования: они должны быть просты по конструкции и иметь небольшие габаритные размеры; обеспечивать быстрое и надежное крепление агрегата и свободный до,-ступ ко всем его частям.
РАЗБОРКА
157
Рис. 101. Конвейер для разборки агрегатов:
/ — привод редуктора; 2 — редуктор; 3 — станина; 4 — электродвигатель; 6 и 6 — тележкн для
Установки агрегатов; 7—натяжное устройство
Механизированный инструмент — стационарные и переносные гайковерты— применяют для отвертывания гаек и болтов.
Стационарные гайковерты — это специальные стенды с приводом от электродвигателя / для отвертывания гаек с забитой или прокоррозированной резьбой (рис. 103). На стенде отвертывание гаек крепления стремянок рессоры, установленной на подставку 5, осуществляет шпиндель 3.
|
|
Переносные гайковерты делятся на электрические, пневматические и гидравлические. Наиболее широкое применение при ремонте автомобилей получили электрические и пневматические переносные инструменты. Весьма перспективными являются электрические высокочастотные гайковерты, работающие от источника тока с частотой 200 Гц и напряжением 36 В. Эти гайковерты развивают большой крутящий момент, имеют небольшие размеры и массу и безопасны в работе.
Применение механизированного инструмента повышает производительность труда при разборке резьбовых соединений в 3—5 раз.
Специальные приспособления (съемники) и прессы с пневматическим или гид равлическим приводом применяют при разборке неподвижных прессовых соединений. Применение съемников позволяет ускорить процесс разборки и обеспе-
видл
Рис. 102. Стенд для разборки коробки передач: / — поворотный стол; 2 — кронштейн для установки коробок передач; 3 — диски, вращающиеся со
стойками; 4— стопорное устройство
$58 ПРИЕМКА АВТОМОБИЛЕЙ В РЕМОНТ, ИХ РАЗБОРКА, МОЙКА И ДЕФЕКТАЦИЯ ДЕТАЛЕЙ
|
|
Рнс. 103. Стенд для отвертывания гаек стремянок рессор:
|
|
/ — двигатель; 2 — редуктор; 3 — шпиндель; 4 — рессора; 5—подставка
Рис. 104. Съемник для выпрессовывания подшипника из коленчатого вала: / — упорная плита; 2— цанга; 3— гайка; 4— конус; 5 — гайка; б ~ ступица; 7 — рукоятка; 8 — штнфт; Я — винт
чивает сохранность деталей. При выпрессовке подшипника цангу 2 съемника вводят в его внутреннее кольцо и разжимают с помощью гайки 3 (рис. 104). При вращении рукоятки 7 гайка 5 будет вытягивать винт 9 с цангой и подшипником. При разработке съемников необходимо руководствоваться следующими техническими требованиями: они должны легко устанавливаться и сниматься с детали; иметь небольшую массу; обеспечивать сохранность детали; иметь гидравлический или пневматический привод. Гидропривод следует применять при усилии выпрессовки свыше 60'... 80 кН.
ОЧИСТКА ДЕТАЛЕЙ
Значение очистных работ при ремонте автомобилей чрезвычайно велико, так как эффективность технологических процессов мойки и очистки существенным образом влияет на производительность труда, санитарно-гигиенические условия работы на участках разборки и дефектовки, а также на всех остальных участках ремонтного производства. Качество работ по восстановлению изношенных поверхностей деталей, а также сборки автомобилей находится в прямой зависимости от полноты и качества выполнения очистных работ. Известно, что из общей трудоемкости капитального ремонта автомобилей трудоемкость очистных работ составляет примерно 5 %, например, плохая очистка блоков цилиндров двигателей и их головок от нагара и накипи приводит к снижению эффективной мощности двигателей на 5 ... 8 %, увеличению расхода топлива на 10 ... 20 %, снижению межремонтного ресурса сборочных единиц (агрегатов) до 30 %. Производительность ремонтных работ на автомобилях и их деталях без очистных работ снижается до 15 ...20%.
Загрязнения на поверхностях автомобиля и его составных частей возникают в процессе эксплуатации, а также ремонта. Классификация загрязнений дана на рис. 105.
ОЧИСТКА ДЕТАЛЕЙ
159
Накипь характерна для жидкостной охлаждающей системы двигателей. Она ухудшает теплообменные процессы, нарушает нормальную работу двигателя. Источником образования накипи является вода, содержащая соли магния и кальция. Накипь образуется на стенках водяных рубашек блока и головки блока, на внутренних поверхностях трубок радиаторов, трубопроводов и др.
В охлаждающей системе двигателя механические частицы в виде глины, песка, продукты коррозии и органические вещества могут образовывать илистые отложения. Технологические загрязнения могут быть в виде пыли, стружки, зерен абразива, остатков притирочных паст, окалины.
Очистку деталей проводят перед разборкой, дефектацией, механической обработкой, нанесением покрытий (электрохимических, химических, лакокрасочных), подготовкой к сборке и при сборке. Для условий авторемонтного производства выделяют три уровня очистки, отличающейся массой остаточных загрязнений: макроочистка, микроочистка и активационная очистка. Макроочистка — процесс удаления с поверхности наиболее крупных частиц, мешающих разборке, дефектации и механической обработке. Микроочистка — процесс удаления загрязнений (масло, остатки эмульсии, соли моющих растворов, пыль) с микронеровностей поверхности. Этот процесс проводят перед финишными операциями сборки и нанесением лакокрасочных покрытий. Активационная очистка — процесс травления металла и очистка поверхности от остатков поверхностно-активных частиц, защитных пленок и посторонних веществ. Ее выполняют при подготовке поверхностей деталей к электролитическому покрытию (например, хромирование, железнение, цинкование и др.).
При ремонте автомобилей следует добиваться абсолютной чистоты поверхностей деталей, только если это вызвано технологической необходимостью. Процессы очистки достаточно трудоемки. Допускается определенная остаточная загрязненность.
Для контроля остаточной загрязненности поверхностей применяют различные методы: весовой, протирания, люминесцентный, смачивания водой. При весо-
Загрязнения
эксплуатационные
технологические
дорожная грязь — _ масляно-грязевые
_ производственная пыль
остатки перевозимых грузов (цемент, ааралы$Г
лакокрасочные покрытии —
асазальтосмолис - тые отложения
стружка, абразивный материал
окалина, шлаки
смазочный материал —
продукты коррозии
лаковые отложение
_ притирочные пасты и остатки эмульсий
Накипь
нагар
продукты изнашива ния при обкатке
Рис. 105. Классификация загрязнений
Дата добавления: 2019-01-14; просмотров: 1483; Мы поможем в написании вашей работы! |
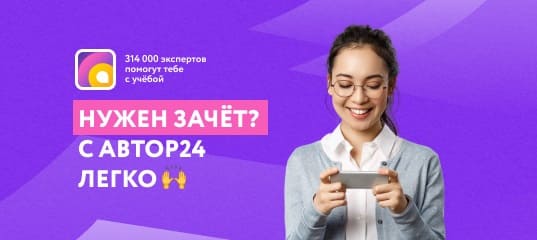
Мы поможем в написании ваших работ!