ВЛИЯНИЕ РАЗЛИЧНЫХ ФАКТОРОВ НА РЕЗУЛЬТАТЫ ЗАКАЛКИ
(Лабораторная работа)
8.1 Цель работы
Проанализировать превращения, происходящие в стали при нагреве и различных скоростях охлаждения. Изучить технологию закалки, получить практические навыки в проведении закалки. Установить зависимость твердости закаленной стали от содержания углерода, скорости охлаждения.
8.2. Задание
8.2.1 Изучить справочные данные. Ознакомиться с устройством и работой приборов, используемых в работе.
8.2.2 Провести эксперимент и занести полученные данные в таблицу 8.1.
8.2.3 Написать отчёт.
8.3 Оборудование и материалы на рабочем месте
8.3.1 Муфельная печь.
8.3.2 Металлографический микроскоп МИМ–7.
8.3.3 Прибор Роквелла.
8.3.4 Бачки с охлаждающими жидкостями (вода, масло).
8.3.5 Клещи.
8.3.6 Образцы из углеродистой стали (0,2%С, 0,4%С, 1,2%C).
8.3.7 Шлифовальная шкурка.
8.4 План выполнения работы
8.4.1 Описать назначение и сущность процесса закалки.
8.4.2 Указать на диаграмме Fе–Fе С интервал закалочных температур.
8.4.3 Обосновать выбор температуры нагрева при закалке стали в зависимости от содержания углерода.
8.4.4 Изобразить диаграмму изотермического распада аустенита, обосновать выбор охлаждающей среды.
8.4.5 Получить образцы с указанием твердости в HRB, перевести в НВ.
8.4.6 По заданной марке стали определить содержание углерода в ней, зарисовать микроструктуру в таблицу 8.1.
8.4.7 Определить необходимую температуру нагрева по рисунке 8.1 согласно указанию таблицы 8.1.
|
|
8.4.8 Определить время нагрева и выдержки образца по графику 8.3. Результаты занести в таблицу 8.1.
8.4.9 Провести закалку образцов согласно указанию таблицы 8.1.
8.4.10 Измерить твердость на приборе Роквелла. Полученные данные занести в таблице 8.1. Значения HRC перевести в НВ, сравнить результаты закалки с исходными данными.
8.4.11 Построить графики зависимости: а) твердости от содержания углерода, б) твердости от скорости охлаждения.
8.4.12 Указать микроструктуры образцов после закалки в таблице 8.1.
Таблица 8.1 – Протокол испытаний
Номер образца | Марка стали, содер. %, С | Схема микроструктуры | Твердость до закалки | Температура нагрева. Т, °С | Время нагрева τ, мин | Охлаждающая среда, скор. охлаж. | Твердость после закалки | Микроструктура после закалки | |||
HRC | НВ | ||||||||||
HRC | НВ | ||||||||||
1 | 45 | полная | вода | ||||||||
2 | 45 | неполная | вода | ||||||||
3 | 45 | полная | масло | ||||||||
4 | 45 | полная | воздух | ||||||||
5 | У12 | неполная | вода | ||||||||
6 | У 12 | неполная | масло | ||||||||
7 | 20 | полная | вода |
|
|
8.5 Справочные данные
Термическая обработка позволяет улучшить свойства сплавов за счет изменения структуры материала. Любая термообработка состоит из операций: нагрева до определенной температуры, выдержка при этой температуре и охлаждение. Одним из видов термообработки является закалка. Она предназначена для повышения твердости, прочности и износостойкости стали за счет изменения её структуры.
Выбор температуры наг рева стали при закалке
Температура нагрева стали при закалке выбирается по диаграмме Fe–Ц в зависимости от содержания углерода и температуры критических точек: Ас (лежат на лини GS), Ас
(образуют линию PSК), А
(показывают начало выделения цементита, лежат на линии SЕ) (рисунок 8.1).
Доэвтектоидную сталь (сплав I) для закалки необходимо греть по режиму полной закалки, до аустенитного состояния:
(8.1)
При нагреве до такой температуры имеющийся в стали углерод полностью растворится в кристаллической решетке Feγ. После выдержки, обеспечивающей превращение по всей толщине, деталь охлаждают со скоростью выше критической так, чтобы кристаллическая решетка перестроилась , а углерод не успел выйти из неё. Полученный пересыщенный раствор углерода в железе Fe α называется – мартенсит (М). В результате значительного перенасыщения решетки углеродом (при медленном охлаждении в α – железе растворяется до 0,02%С) твердость её намного увеличится, следовательно, повысится, твёрдость стали. Например, твердость стали 45 до закалки HRC
12, а после закалки – HRC 56.
|
|
Кристаллическая решётка мартенсита искажается, становится тетрагональной, твердость и степень тетрагональности зависят от степени перенасыщения её углеродом.
Рисунок 8.1 – Нижняя часть диаграммы (участок стали) с указанием интервала
температур нагрева для закалки
Одним из видов брака при закалке доэвтектоидной стали является пятнистая, недостаточно высокая твёрдость. Это связано с недогревом детали. Так, если доэвтектоидную сталь нагреть по режиму неполной закалки, т.е. выше т. Aс , то в структуре этой стали будут А + Ф, которые при быстром охлаждении превращаются в М + Ф. Присутствие зерен мягкого феррита приведет к снижению твердости, структура будет неоднородной.
|
|
Для заэвтектоидных сталей (С>0,8%) лучше результаты поручают при нагреве по режиму неполной закалки, т.е.:
(8.2)
Нагретая до такой температуры сталь, претерпевает в результате закалки структурные изменения: А +Ц → М + Ц. Химическое соединение цементит имеет высокую твердость, увеличивает твердость стали. Греть заэвтектоидные стали по режиму полной закалки до аустенитного состояния нецелесообразно, т.к.:
1 – в структуре будет только мартенсит (цементит теряем);
2 – расходуется больше энергии;
3 – нагрев выше т. А вызывает роcт зерна аустенита и, как результат, повышение хрупкости стали, структурные и термические напряжения, вероятность появления макро и микротрещин. Структурные изменения в доэвтектоидной и заэвтектоидной стали, показаны на рисунке 8.2.
Рисунок 8.2 – Схема структурных превращений при закалке:
а – доэвтектоидная сталь; б – заэвтектоидная сталь.
Дата добавления: 2019-01-14; просмотров: 587; Мы поможем в написании вашей работы! |
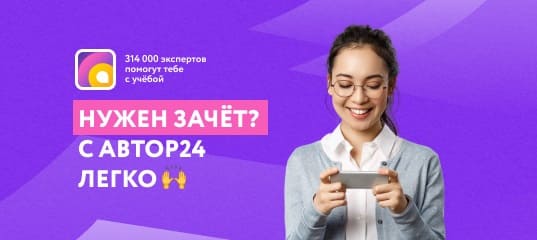
Мы поможем в написании ваших работ!