ВЛИЯНИЕ ТЕМПЕРАТУРЫ ОТПУСКА ЗАКАЛЕННОЙ
СТАЛИ НА ЕЁ ТВЕРДОСТЬ
Практическая работа)
9.1 Цель работы
Проанализировать превращения, происходящие в стали при нагреве до различных температур при отпуске. Приобрести навык в проведении отпуска стали. Установить зависимость твердости отпущенной стали от температуры нагрева.
9.2 Задание
9.2.1 Изучить справочные данные. Ознакомиться с устройством и работой приборов используемых в работе.
9.2.2 Провести эксперимент и занести полученные данные в таблицу 9.1.
9.2.3 Написать отчёт.
9.3 Оборудование и материалы на рабочем месте
9.3.1 Электрические муфельные печи с различной температурой нагрева (200°С, 400ºС, 600ºС), термопары.
9.3.2 Твердомер Роквелла.
9.3.3 Образцы закаленной, стали 45, У12.
9.3.4 Клещи, бачки с охлаждающей жидкостью.
9.4 План выполнения работы
9.4.1 Описать превращения, происходящие в закалённой стали при нагреве до температур отпуска.
9.4.2 Дать определение каждого вида отпуска, указать его назначение и область применения
9.4.3 Объяснить образование цветов побежалости, указать соответствие температуры нагрева и цвета.
9.4.4 Определить время нагрева и выдержки образцов для низкого, среднего и высокого отпуска по рисунку 8.3. Данные занести в таблицу 9.1.
9.4.5 Провести образцам низкий, средний и высокий отпуск, измерить твердость, полученные данные занести в таблицу 9.1.
9.4.6 По полученным результатам построить график зависимости изменения твердости от температуры отпуска.
|
|
Таблица 9.1 – Протокол испытаний
№ образец | Марка стали, % C | Твердость после закалки, НRC | Режим отпуска | Результаты отпуска | |||||
температура нагрева Т, °С | время выдер.
| цвета побежалости. | охлаждающая среда | Твердость | микроструктура | ||||
HRC | НВ | ||||||||
1 L. з. | 45
| ||||||||
2 | |||||||||
3 | |||||||||
4 5. 6. | У12
| ||||||||
5 | |||||||||
6 |
9.5 Справочные данные
Детали из стали после закалки получают высокую твердость, но обладают низкой ударной вязкостью, имеют большие внутренние напряжения. Чтобы снять внутренние напряжения, перевести структуру в более устойчивое состояние, придать ей требуемые свойства после закалки обязательно проводят отпуск.
Отпуск – это вид термической обработки, связанный с нагревом детали до температур ниже критической т. Ас , т.е. до температур, когда начинаются фазовые превращения, выдержкой при этой температуре и последующим охлаждением. Скорость охлаждения углеродной стали на структурные изменения не влияет, но при отпуске от 600ºС могут создаваться термические напряжения, поэтому детали надо охлаждать медленно, особенно, если они сложной конфигурации.
|
|
При отпуске в зависимости от температуры нагрева происходящие процессы можно разделить на три стадии.
Первая стадия происходит при нагреве до 200°С. Она связана с малой скоростью диффузии, из мартенсита выделяются – карбиды, степень тетрагональности в нем уменьшается, содержание углерода снижается до 0,25%. Такая структура называется отпущенный мартенсит (НRС 60…65).
Вторая стадия наступает при нагреве до температур 200…300°С. При этом остаточный аустенит превращается в отпущенный мартенсит, а мартенсит ещё больше обедняется углеродом.
Третья стадия (при температурах от 300…400°С) заключается в образовании из – кар бидов цементита. Выделение углерода (т.е. распад мартенсита) почти заканчивается, снимается значительная часть напряжений и искажение решетки. Получается структура троостит отпуска.
При дальнейшем повышении температуры от 400 до 700°С происходит коагуляция (объединение), сфероидизация частиц цементита. Эта структура (НRС 30) называется сорбит отпуска – смесь феррита и округлых частиц цементита. Сорбит отпуска отличается хорошим комплексом механических свойств – высоким пределом упругости при достаточной ударной вязкости и твердости. В зависимости от условий работы детали, требуемых свойств назначают определенную температуру нагрева при отпуске. Различают три вида отпуска: низкий, средний и высокий.
|
|
Низкий (инструментальный) отпуск проводят с нагревом до 150…200°С, реже до 250°С. Его назначение – понизить внутренние напряжения, сохранив высокую твердость и износостойкость. Деталь после такого вида отпуска (если она не имеет вязкой сердцевины) не выдержит значительных динамических нагрузок. Низкий отпуск применяют для режущего и измерительного инструмента из углеродистой и низколегированной стали, а также назначают деталям после поверхностной закалки, цементации, цианирования.
Средний отпуск при 350–500°С применяется, в основном, для рессор, пружин, для штампов. Такой отпуск обеспечивает высокий предел упругости, выносливости при достаточно высокой твердости. Твердость при среднем отпуске уменьшается процентов на 30, полученная структура – троостит отпуска с твердостью HRC 40.
|
|
Высокий (высокотемпературный) отпуск связан с нагревом до 500…650°С. При нагреве до таких температур, диффузионные процессы протекают более интенсивно, твердость снижается на 50%, полученная структура – сорбит отпуска (HRC 30). Высокий отпуск создает наилучшее соотношение прочности и вязкости стали. Назначается этот вид отпуска для деталей, подвергающихся действию высоких напряжений, динамических нагрузок (например, шатуны, шатунные болты двигателей, передние оси автомобилей и др.).
Термическую обработку, состоящую из закалки и высокого отпуска, называют улучшением. Улучшению подвергают среднеуглеродистые (0,3…0,5%C) конструкционные стали, к которым предъявляются высокие требования к пределу текучести, ударной вязкости.
Время нагрева и выдержки при любом виде отпуска зависят от нагревательного устройства, требуемой температуры нагрева, способа укладки деталей в печи. Его можно определить по графику (рисунок 8.3). Охлаждение можно вести в воде, в масле, на воздухе, так как скорость охлаждения стали, закаленной на мартенсит, влияния на степень распада мартенсита не оказывает.
9.6 Содержание отчёта
В отчёт включаются: цель работы, определение отпуска, его видов с указанием назначения и области применения, результаты испытаний (таблица 9.1), график зависимости изменения твёрдости от температуры отпуска, выводы.
9.7 Вопросы для контроля
9.7.1 Какой вид термообработки называют отпуском?
9.7.2 Какие превращения происходят в стали при различных температурах отпуска?
9.7.3 Виды отпуска, их назначение, получаемые структуры и свойства.
9.7.4 Какое влияние оказывает скорость охлаждения при отпуске?
9.7.5 От чего зависит время выдержки при отпуске?
ЦЕМЕНТАЦИЯ СТАЛИ
(Лабораторная работа)
10.1 Цель работы
Практическое изучение метода проведения цементации в твердом карбюризаторе.
10.2 Задание
10.2.1 Изучить справочные данные. Ознакомиться с устройством и работой приборов, используемых в работе.
10.2.2 Провести эксперимент и занести полученные данные в таблицу 10.1.
10.2.3 Написать отчёт.
10.3 Оборудование и материалы на рабочем месте
10.3.1 Образцы из малоуглеродистой стали после цементации.
10.3.2 Микрошлифы цементованных деталей.
10.3.3 Твердомер Т.К.
10.3.4 Металлографический микроскоп МИМ–6.
10.4 План выполнения работы
10.4.1 Описать назначение, виды и сущность процесса цементации стали.
10.4.2 Описать процесс цементации в твердом карбюризаторе (состав смеси, реакции, протекающие при цементации).
10.4.3 По готовому микрошлифу определить исходное содержание углерода в стали, рассматривая сердцевину образца, определить марку стали.
10.4.4 Рассматривая поверхностную часть шлифа, определить глубину цементации у трех образцов с выдержкой 3 ч, 5 ч, 7 ч, зарисовать схему микроструктуры образца после 7–часовой выдержки.
10.4.5 Определить твёрдость сердцевины и поверхности образцов, предназначенных для термообработки (твердость измеряют с одного и другого торца). Результаты занести в таблицу 10.1.
10.4.6 Зарисовать график термообработки после цементации.
10.4.7 Назначить режимы закалки.
10.4.8 Провести закалку в воде.
10.4.9 Зарисовать схему микроструктуры после термообработки.
10.4.10 Построить график зависимости глубины цементации от её продолжительности.
Таблица 10.1 – Протокол лабораторной работы
№ образца | Содерж. углер., марка стали | Темпер. цемен. Т, °С | Время выдер.
| Глубина цемент., мм | Твёрдость после цемент. HRB | Твёрдость после Ц+З | ||||
сердц. | поверх. | сердцевина. | поверхность | |||||||
HRC | HB | HRC | HB | |||||||
1 | ||||||||||
2 | ||||||||||
3 |
10.5 Справочные данные
Многие детали машин по условиям эксплуатации должны иметь высокую твердость поверхности при сохранении достаточной пластичности сердцевины (шестерни коробки скоростей, распредвалы, поршневые пальцы и др.). Высокая пластичность этим изделиям необходима для того, чтобы противостоять ударным, знакопеременным или изменяющимся по величине нагрузкам. Большая твердость поверхности обеспечивает её износостойкость, если детали одновременно работают в условиях поверхностного трения. Стальные изделия с твердой поверхностью и мягкой пластичной сердцевиной можно получить путем химико–термической обработки (Х.Т.О.) малоуглеродистых сталей, или поверхностной закалкой углеродистых сталей.
Химико–термической обработкой называется операция поверхностного насыщения стальных деталей неметаллами (например, углеродом, азотом, кремнием) или металлами (алюминием, хромом) путем их диффузии в атомарном состоянии из окружающей среды. Для осуществления химико–термической обработки детали помещают в жидкую, твердую или газообразную среду (карбюризатор), нагревают до заданной температуры и выдерживают определенное время. При этом протекают следующие три процесса:
– выделение из среды карбюризатора диффундирующего элемента в атомарном состоянии;
– поглощение (адсорбция) поверхностью детали активных атомов;
– проникновение элемента (растворение) в кристаллическую решетку железа.
Основные виды химико–термической обработки: цементация; азотирование; цианирование, диффузионная металлизация.
Цементация – процесс насыщения поверхности детали углеродом. Цементации подвергают углеродистые и низколегированные стали с содержанием углерода 0,1…0,3%. Цементация проводится в твердом или газовом карбюризаторе. В качестве твердой среды используется карбюризатор состава: 70…75% древесного угля, 20…25% углекислого бария ВаСO или Na
CO
и до 3% углекислого кальция CaСО
.
На цементацию детали поступают после механической обработки с припуском на шлифование 50–100 мкм. Детали, подвергаемые цементации, укладывают в ящик рядами на расстоянии 10–20 мм друг от друга и от стенок. После этого ящик помещают в печь, нагревают до аустенитного состояния (910°…930°С), так как – железо активно растворяет в себе атомарный углерод. При нагреве происходят следующие реакции:
– кислород взаимодействует с углеродом карбюризатора и образует окись углерода:
2С + О = 2СО;
– при контакте со сталью окись углерода разлагается на углекислоту CO и атомарный углерод:
2СО СО
+ С атом;
– атомарный углерод диффундирует в поверхность, растворяясь в – железе.
BaCO (Na
CO
) вводится в состав карбюризатора для активизации процесса образования атомарного углерода, обогащая атмосферу в цементационном ящике окисью углерода:
ВаСO
+ С ВаО + 2CO
Углекислый кальций добавляется для предотвращения спекания карбюризатора.
Скорость цементации зависит от температуры нагрева и составляет 0,12…0,17 мм/ч при 920°С. Следовательно, чтобы получить глубину цементации 1 мм необходимо выдержать деталь в карбюризаторе при заданной температуре 6…7 часов. Практически цементацию осуществляют на глубину 0,5…1,8 мм.
На ремонтных предприятиях для цементации может быть использована паста следующего состава: сажа или древесный уголь, углекислый натрий, желтая кровяная соль и декстрин. Из этих компонентов приготавливается водяная смесь сметанообразного состояния. Пасту наносят на детали толщиной 4 мм. После высыхания нанесенного слоя детали укладывают в ящик и выдерживают в течение часа при температуре цементации. Глубина цементации достигает 0,6…0,8 мм.
Поверхности, которые не должны подвергаться цементации, покрываются обмазкой, состоящей из 70% однохлористой меди, 30% свинцового сурика, замешанных на канифольном лаке.
Газовая цементация осуществляется в природном газе (СН ), пропанобутановых смесях и других газах, содержащих углерод. Газовая цементация, по сравнению с твердой, имеет ряд преимуществ: сокращается длительность процесса на I5–20%, обеспечивается механизация процесса. Закалку деталей можно проводить непосредственно из печи. Прогрессивной является газовая цементация в агрегатах непрерывного действия, в которых нагрев осуществляется токами высокой частоты (ТВЧ).
Структура цементованного слоя изменяется в зависимости от степени науглероживания. Практически стремятся увеличить содержание углерода до 0,8%, в результате в поверхностном слое получаем структуру – перлит.
Рисунок 10.1 – Схема микроструктуры цементованного слоя
Длительная выдержка при повышенной температуре цементации, необходимая для получения толстого слоя, может привести к более высокому содержанию углерода на поверхности. Это вызывает появление грубой сетки цементита, которая не только ухудшает механические свойства цементованного изделия, но и способствует образованию микротрещин при закалке стали. Если цементитная сетка незначительна, она рассосется при закалке. Для устранения грубой цементитной сетки необходим отжиг.
Наличие феррита на поверхности цементованных деталей также анормально и является следствием низких температур (723…850º) цементации, малым временем выдержки, или вызвано тем, что карбюризатор истощён.
По толщине слоя концентрация углерода непостоянна и убывает от поверхности к сердцевине. За глубину цементации принимают расстояние от поверхности до структуры, в которой перлит занимает 50% площади шлифа. Схема микроструктуры цементованного слоя показана на рисунке 10.1.
Дата добавления: 2019-01-14; просмотров: 728; Мы поможем в написании вашей работы! |
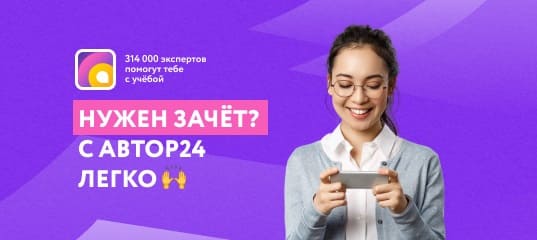
Мы поможем в написании ваших работ!