Конструкционные легированные стали
Маркировка легированных конструкционных сталей. Легированные конструкционные стали маркируются цифрами и буквами. Двузначные цифры, приводимые в начале марки, указывают содержание углерода в сотых долях процента. Буквы обозначают легирующие элементы, а цифры после них – примерное количество в процентах. Отсутствие цифры говорит о том, что содержание легирующего элемента не превышает 1,5%,
Буквенное обозначение легирующих элементов: А – азот, Б – ниобий, В – вольфрам, Г – марганец, Д – медь, Е – селен, К – кобальт, Н – никель, М – молибден, П – фосфор, Р – бор, С – кремний, Т – титан, Ф – ванадий, X – хром, Ц – цирконий, Ч– редкоземельный, Ю – алюминий. Например: сталь 12X2H4A содержит (в среднем) 0,12% С, 2% Cr, 4% Ni. "А" в конце марки говорит о том, что эта сталь высококачественная, в её составе меньше серы и фосфора.
Микроструктура конструкционных сталей
Конструкционные легированные стали в зависимости от химический состава делятся на: цементуемые (низкоуглеродистые.), улучшаемые (среднеуглеродистые), рессорно–пружинные (высокоуглеродистые), шарикоподшипниковые, износостойкие.
Цементуемые стали содержат углерода до 0,25%С. В зависимости от входящего в их состав легирующего элемента они делятся на хромистые (15Х, 20Х), хромомарганцовые (18ХГТ), хромованадиевые (20ХФ). В равновесном состоянии эти стали имеют в структуре П+Ф.
Улучшаемые стали: хромистые (30Х, 40Х), хромомарганцовые (40ХГ), хромоникелевые (40XH) – перлитного класса, содержат углерода от 0,25% до 0,6%С. После отжига структура стали состоит из феррита и перлита (рисунок 11.2 а). Из этих сталей изготавливают детали машин (коленвалы, оси, шатуны, ответственные детали турбин и т.д.). Их подвергают закалке и высокому отпуску (улучшению). После такой обработки структура стали – сорбит, деталь имеет высокий предел текучести, предел выносливости, хорошо обрабатывается резанием (рисунок 11.2 б).
|
|
Рисунок 11.2 – Микроструктура стали 30ХГСА:
а – после отжига – Ф+П; б – после закалки и высокого отпуска – сорбит х 250
Рессорно–пружинные стали перлитного класса с содержанием углерода 0,5…0,7% идут на изготовление автомобильных рессор (50ХГА, 60С2A), пружин клапанов (50ХФА).
Пружинные стали легируются, в основном, Mn (0,6…1,2%), Si (l.5…2.8%), Cr (до 1.2%), Ni (до l,7%), W (1,2%), V (0,25%). Эти элементы улучшают прокаливаемость стали, повышают релаксационную стойкость и предел упругости. Для улучшения механических свойств пружины подвергают термической обработке (закалка и средний отпуск). Срок службы рессор можно повысить дробеструйной обработкой, после которой предел выносливости увеличивается в 2 раза.
|
|
Шарикоподшипниковые стали ЩX15 (1%С; 1,5%Сr), ШХ15СГ (1,5% Cr; 1,5% Si; 1.5% Mn) обладают высокой твердостью, износостойкостью, их применяют для изготовления деталей подшипников качения. Кольца, шарики, ролики закаливают в масле от 850°С для получения структуры мартенсит с избыточными карбидами и твердостью НRС 65. После закалки делают низкий отпуск. Иногда для стабилизации размеров применяют обработку холодом.
Коррозионно–стойкие стали – это стали, устойчивые к электрохимической, химической и другим видам коррозии.
Коррозией называют разрушение металла под действием окружающей среды. Коррозионную стойкость имеет сталь, легированная хромом и никелем.
Хромистые стали содержат хрома не менее 12% и углерода до 0,4%. Стали марок 40X13, 30Х13 после охлаждения на воздухе имеют мартенситную структуру, сталь 20X13 – мартенситно–ферритную, а стали 12X13, 15Х25Т откосятся к сталям ферритного класса.
Коррозионная стойкость в воде, в атмосфере, в среде кислот, солей и щелочей повышается термической обработкой – закалкой при 1050°С и высоким отпуском. Микроструктура стали 2X13 показана на рисунок 11.3.
Рисунок 11.3 – Микроструктура 2Х13: а – после закалки от 1050°С – мартенсит;
б – после закалки и отпуска при 700°С – сорбит (х250).
|
|
Хромоникелевые нержавеющие стали относятся к аустенитному классу, т.е. после охлаждения на воздухе имеют аустенитную структуру. Представителями коррозионно–стойких сталей аустенитного класса являются, стали 12Х18Н9 (0,I2% C; 18% Cr; 9% Ni), I7X18Н9. Их применяют для работы в окислительных средах, они парамагнитны. В равновесном состоянии структура такой стали состоит из аустенита и карбидов хрома, железа.
Для получения наибольшей устойчивости против коррозии сталь нагревают до температуры 1000°С (для растворения карбидов в аустените) и закаливает в воде с получением структуры, аустенит (рисунок 11.4).
Рисунок 1.4 – Микроструктуры стали 12XI8H9:
а – в равновесном состоянии – аустенит и карбиды;
б – после закалки от 1100°С – аустенит
Жаростойкие стали. Повышение окалиностойкости (стойкость против газовой коррозии при температуре выше 550ºС) достигается легированием хромом, алюминием, кремнием. Окалиностойкость зависит от состава стали, а не от ее структуры, т.е. окалиностойкость (жаростойкость) ферритных и аустенитных сталей при равном количестве хрома практически одинакова. В машиностроении для изготовления различного рода высокотемпературных установок применяют жаростойкие ферритные (I5X25T, 12X17) и аустенитные (20Х23Н13 и др.) стали.
|
|
Износостойкие стали применяет для изготовления деталей, работающих на износ в условиях абразивного трения и ударов (щеки дробилок, черпаки землечерпальных машин, крестовины трамвайных путей).
Сталь 110Г13Л содержит 1,1% C; 13% Мn. После закалки от 1100°С с охлаждением в воде она приобретает аустенитную структуру. Сталь 110Г13Л с аустенитной структурой упрочняется и становится износостойкой под действием ударных нагрузок, когда происходит деформационное упрочнение аустенита и образование – мартенсита. При небольших ударных нагрузках или при чисто абразивном изнашивании мартенситное превращение не протекает и износостойкость стали невысокая.
Инструментальные стали
Инструментальные стали делятся на три группы: не обладающие теплостойкостью (содержание легирующих элементов до 4%); полутеплостойкие, работающие до 500ºС (содержат C>0,6% и до 18% Cr); в) теплостойкие до 650°С (содержат Cr, W, V, Mo, Со), получившие название – быстрорежущие.
Маркировка инструментальных сталей. Легированные инструментальные стали, Х, 9Х, 9ХС, 6ХВГ маркируют цифрой, которая указывает содержание углерода в десятых долях процента. Если цифры нет, то содержание углерода около 1%. Буква указывает легирующие добавки в стали, а цифры – их количество.
Быстрорежущие стали маркируют буквой «Р» и цифра указывает содержание вольфрама в процентах. Среднее содержание хрома в большинстве быстрорежущих сталей – 4%.
Не обладающее теплостойкостью легированные инструментальные стали перлитного класса, например: 5ХНМ, 5ХГМ, с содержанием углерода до 0,65% нашли применение для изготовлении инструмента для горячей обработки давлением (штампы, матрицы, пуансоны и др.).
Штампы закаливают в масле и делают отпуск при 500°С. В результате, получается структура – троостит.
Высокоуглеродистые стали перлитного класса (9ХС, ХВГ) используются для изготовления режущего и мерительного инструмента. Эти стали пригодны для резания материалов невысокой прочности (до =600 МПа) со скоростью резания до 14м/мин.
В теплостойких быстрорежущих сталях при охлаждении на воздухе получается структура мартенсит, поэтому их называют "самозакаливающимися".
Быстрорежущая сталь обладает красностойкостью, т.е. способностью сохранять высокую твердость, прочность и износостойкость при нагреве. Это дает возможность повысить скорость резания в 4 раза и стойкость инструмента в 20 раз.
Быстрорежущая сталь относится к карбидному (ледебуритному) классу. В структуре литой быстрорежущей стали присутствует сложная эвтектика, напоминающая ледебурит, располагающийся по границам зерен (рисунок 11.6 a). В результате горячей механической обработки сетка эвтектики дробится. Для снижения твердости, улучшения обрабатываемости резанием, подготовки структуры к закалке детали после ковки подвергают отжигу.
Для придания стали теплостойкости инструмент подвергают закалке и многократному отпуску по режиму (рисунок 11.5).
Рисунок 11.5 – График термической обработки стали P18
Нагрев до 850ºС надо вести очень медленно, чтобы избежать возникновения термических напряжений, трещин. Дальнейший нагрев должен быть очень быстрым, чтобы предотвратить обезуглероживание поверхности инструмента. Высокая температура нагрева обеспечивает более полную растворимость вторичных карбидов в аустените. После выдержки инструмент охлаждают в масле или на воздухе.
Структура быстрорежущей стали после закалки представляет собой высоколегированный мартенсит, содержащий 0,4% С, нерастворимые избыточные карбиды и остаточный аустенит (до 30%), который понижает режущие свойства стали. На микрошлифе видны границы зерна аустенита, карбиды и очень плохо просматривается основная структурная составляющая – мартенсит (рисунок 11.6 б).\
Рисунок 11.6 – Микроструктура быстрорежущей стали Р18, х300:
а – ледебурит в литой стали; б – закаленная сталь;
в – отпущенная сталь; г – схема зарисовки микроструктуры
Во время трехкратного отпуска при 560°С остаточный аустенит превращается в мартенсит. Это сопровождается увеличением твердости. Микроструктура быстрорежущей стали после отпуска состоит из мартенсита и карбидов (рисунок 11.6 в). Схема зарисовки микроструктуры показана на рисунок 11.6 г.
Таблица 11.1 – Химический состав и назначение конструкционной стали ГОСТ4543– 71,
ГОСТ 1459
Марка стали | Химический состав, % | Назначение | ||||
С | Si | Ni | Cr | Mn | ||
20Х 40 | 0,17…0,23 0,36…0,44 | 0,17…0,37 0,17…0,37 | 0,5…0,8 0,5…0,8 | 0,7…1,6 0,8…1,1 | – – | Коленчатые валы, оси, шестерни, штоки, диски, втулки. |
30ХГС 30ХГТ | 0,28…0,35 0,24…0,32 | 0,9…1,2 0,17…0,37 | 0,8…0,11 0,8…0,11 | 0,8…1,1 1,0…1,3 | – 0,12 Mo | Валики, оси, шестерни, сварные конструкции |
12ХН3А 20ХН3А 40ХНМА 38ХМЮА | 0,1…0,16 0,17…0,24 0,37…0,44 0,35…0,42 | 0,17…0,37 0,17…0,37 0,17…0,37 0,17…0,37 | 0,3…0,6 0,3…0,6 0,5…0,8 0,3…0,6 | 0,6…0,9 0,6…0,9 0,6…0,9 1,4…1,7 | 2,8…3,2 2,8…3,3 1,3…1,6 | Шестерни, валы, оси Шестерни, валы, оси ролики, пальцы поршневые Шестерни, валики, болты, втулки, шпильки Коленчатые валы, шатуны, валы, штоки |
40ХР 37ХНВА | 0,37…0,45 0,33…0,41 | 0,17…0,37 – | 0,5…0,8 0,3…0,6 | 0,8…1,1 1,2…1,6 | – 3,0…3,5 | Гильзы цилиндров, шестерни, детали высокой износоустойчивости |
50С2 55С2 60С2 50ХГ 50ХГА 60СГА | 0,47…0,55 0,52…0,6 0,57…0,65 0,46…0,56 0,56…0,64 | 1,5…2,0 0,17…0,37 1,3…1,8 | 0,6…0,9 0,8…1,0 | – 9…1,2 | Различные рессоры и пружины |
11.6 Содержание отчёта
В отчёт включаются: цель работы, описание влияния легирующих элементов на свойства стали, буквенное обозначение легирующих элементов, классификацию легированных сталей по структуре и назначению, описание маркировки инструментальных и конструкционных легированных сталей, их структуры, применение, график термической обработки стали Р18, выводы.
11.7 Вопросы для контроля
11.7.1 Какие стали называются легированными?
11.7.2 Как изменяют легирующие элементы диаграмму Fе–Ц?
11.7.3 Как классифицируются легированные стали по структуре после нормализации и отжига?
11.7.4 Как классифицируются легированные стали по назначению?
11.7.5 Как маркируются конструкционные стали, их применение и ТО?
11.7.6 Как маркируются инструментальные легированные стели, их применение?
11.7.7 Термообработка быстрорежущей стали.
Дата добавления: 2019-01-14; просмотров: 904; Мы поможем в написании вашей работы! |
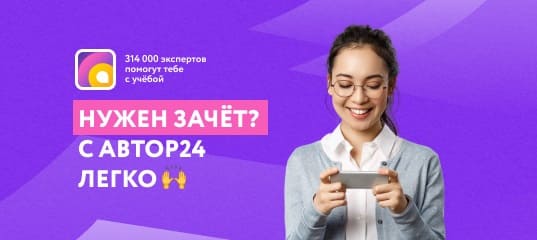
Мы поможем в написании ваших работ!