Обработка плоскостей фрезерованием
Наиболее распространенный метод обработки плоскостей – фрезерование их на горизонтально-, вертикально- и продольно-фрезерных станках, а также на карусельно-фрезерных, барабанно-фрезерных и других станках фрезерной группы. В качестве режущих инструментов применяются цилиндрические, торцовые, дисковые, концевые и другие фрезы.
Плоскости небольшой ширины обрабатывают цилиндрическими фрезами на горизонтально-фрезерных станках – наиболее распространенных и более универсальных, чем вертикально-фрезерных.
Фрезерование цилиндрическими, а также дисковыми фрезами может быть выполнено по двум схемам:
1) направление движения подачи направлено против вращения фрезы (рис. 4.3, а);
2) направления движения подачи совпадает с направлением вращения фрезы (рис. 4.3, б).
Фрезерование по первой схеме называют встречным, а по второй схеме – попутным.
При встречном фрезеровании сечение среза и нагрузка на зуб увеличиваются постепенно – от нуля при врезании зуба до максимума при выходе его из контакта с деталью. Горизонтальная составляющая усилия резания направлена в сторону, противоположную подаче. Преодоление этой составляющей в процессе работы приводит к устранению зазора, имеющегося в механизме подачи, и резание проходит плавно и спокойно.
При попутном фрезеровании зуб фрезы начинает работу со срезания слоя наибольшей толщины, которая в конце работы уменьшается до нуля. Горизонтальная составляющая совпадает по своему направлению с подачей и стремится затянуть деталь под фрезу.
|
|
При обработке заготовок с черной поверхностью попутное фрезерование применять не следует, так как при врезании зуба фрезы в твердую корку происходит преждевременный износ и выход из строя фрезы.
При обработке заготовок с чистыми поверхностями попутное фрезерование имеет преимущества перед встречным в отношении, как стойкости инструмента, так и шероховатости поверхности. При попутном фрезеровании необходимо, чтобы станок был в хорошем состоянии и имел устройство для устранения зазора в механизме подачи.
При попутном и встречном фрезеровании можно работать при движении стола в обоих направлениях, что позволяет выполнять черновое и чистовое фрезерование за одну операцию.
Цилиндрические фрезы широко используются в единичном и серийном производстве.
Торцовыми фрезами можно обрабатывать и ступенчатые и плоские поверхности, имеющие свободный вход и выход для фрезы.
Торцовые фрезы имеют ряд преимуществ по сравнению с цилиндрическими. Они обеспечивают равномерное фрезерование даже при небольших припусках на обработку, так как угол контакта фрезы с заготовкой зависит только от диаметра фрезы и ширины заготовки. Длина дуги контакта здесь значительно больше, чем при фрезеровании цилиндрическими фрезами. Для оснащения сборных торцовых фрез требуется меньше быстрорежущей стали или твердого сплава. Установка торцовый фрезы непосредственно в шпиндель станка исключает необходимость в примени длинных и недостаточно жестких оправок, неизбежных при работе цилиндрическими насадными фрезами, и позволяет использовать фрезы диаметром до 800 – 1200 мм, что повышает пределы ширины фрезерования примерно до 800 мм.
|
|
В настоящее время применяют торцовые фрезы с механическим креплением металло- и минералокерамических вставных ножей круглой и многогранной форм, что значительно повышает их стойкость, а следовательно, и производительность. Эти фрезы обеспечивают шероховатость поверхности 6 – 8-го классов.
Широкое распространение получили торцовые фрезы с неперетачиваемыми многогранными пластинками из твердого сплава. Конструкции этих фрез позволяют заменять отдельные ножи или весь комплект их непосредственно на станке. В собранном виде фреза имеет достаточно высокую точность: биение по главным режущим кромкам двух смежных ножей не превышает 0,03 – 0,05 мм, а двух противоположных – 0,06 – 0,1 мм, торцовое биение – 0,06 – 0,08 мм.
|
|
Диаметр D торцовой фрезы определяется по ширине B фрезеруемой поверхности, при этом пользуются зависимостью:
D = (1,4 – 1,7)В (мм).
Фрезерование плоскостей торцовыми фрезами осуществляется на вертикально- и продольно-фрезерных станках, а также и на горизонтально-фрезерных станках с установкой фрезы непосредственно в шпинделе станка.
Точность фрезерования зависит от типа станка, режущего инструмента, режима резания и других факторов. В обычных условиях точность обработки достигает 3 – 4-го классов, а шероховатость поверхности – 6 – 7-го классов.
Чистовое (шабрящее) фрезерование обеспечивает шероховатость поверхности стальных и чугунных деталей до 7 – 8-го классов, а деталей из бронзы и алюминиевых сплавов – до 9-го класса и отклонение от плоскостности 0,02 – 0,03 мм на 1 пог. м.
Указанные точность и шероховатость поверхности достигаются фрезерованием за 2 – 3 прохода при глубине резания t = 0,05 – 0,1 мм, подаче s = 2 – 3 мм/об и скорости резания v = 200 м/мин. При обработке стальных деталей инструмент рекомендуется оснащать пластинками твердого сплава марки Т30К4, а чугунных – ВК3.
|
|
При чистовом фрезеровании ось вертикального шпинделя должна быть установлена под весьма малым углом к направлению подачи (рис. 4.4, а), чтобы след, оставленный зубом фрезы на поверхности детали, представлял собой так называемую полусетку (рис. 4.4, б). В этом случае длина пути резца вдвое меньше, чем при фрезеровании в сетку (рис. 4.4, в). Кроме того, при фрезеровании в полусетку зуб фрезы при каждом обороте фрезы срезает новый слой металла, в то время как при фрезеровании в сетку он скользит по наклепанному слою. Стойкость фрезы при обработке в полусетку выше, чем при фрезеровании в сетку.
Чистовое фрезерование алюминиевых сплавов осуществляют однозубыми фрезами, а черных и цветных металлов и сплавов – двузубыми ступенчатыми. У двузубых ступенчатых фрез зубья смещены по высоте на 0,05 – 0,3 мм и несколько отличаются формой заточки. Первый зуб предназначен для снятия основного припуска, а второй – зачистной – для отделочного резания.
Одним из основных путей повышения производительности при работе на фрезерных станках является усовершенствование технологии путем выбора наиболее рациональной схемы обработки.
В настоящее время повышение производительности труда обеспечивается при:
1) одновременном фрезеровании несколькими фрезами;
2) одновременном фрезеровании нескольких деталей;
3) позиционном и
4) непрерывном фрезеровании
Одновременная обработка несколькими фрезами осуществляется набором фрез, специальными фрезерными станками или многошпиндельными головками.
Наборы фрез в основном применяют при работе на горизонтально-фрезерных станках. Фрезы в этом случае устанавливаются на фрезерной оправке, опирающейся на центр или угловые (рис. 4.5, б), цилиндрические и дисковые (рис. 4.5, в и г), цилиндрические, угловые и фасонные (рис. 4.5, д).
При обработке набором фрез не только повышается производительность, но и лучше используется станок по мощности, а также возрастает точность фрезерования.
Набор фрез, по существу, представляет собой специальный инструмент. Первоначальная стоимость его велика, заточка гораздо сложнее, чем каждой фрезы в отдельности. При работе набором фрез не представляется возможным использовать каждую из них наиболее рациональным способом, так как при принятой скорости резания число оборотов должно назначаться по фрезе наибольшего диаметра, а подача – по фрезе с наименьшим числом зубьев. Из-за большой разницы в диаметрах фрез затупление и износ их протекает по-разному, поэтому при переточке одной фрезы приходится перетачивать все фрезы набора.
Из сказанного ясно, что применять набор фрез целесообразно в условиях крупносерийного и массового производства. В набор могут входить различные дисковые фрезы (рис. 4.5, а).
Одновременное фрезерование нескольких деталей может осуществляться параллельным, последовательным или параллельно-последовательным способом.
При параллельном способе фрезерования детали располагаются в ряд перпендикулярно движению подачи и обрабатываются одновременно одной или набором фрез.
При последовательном фрезеровании детали размещаются в ряд друг за другом в направлении подачи.
При параллельно-последовательном фрезеровании детали устанавливаются рядами как в направлении подачи. Так и в перпендикулярном направлении.
Позиционное фрезерование. Различают две основные разновидности этого способа обработки – позиционное фрезерование на специальных или универсальных поворотных столах или приспособлениях и маятниковое фрезерование, не требующее специальных поворотных устройств.
Схема позиционного фрезерования с использованием круглого поворотного стола приведена на рис. 4.6. Набором фрез обрабатывают боковые плоскости четырех квадратных деталей А, Б, В и Г. Вначале дисковые двусторонние фрезы 1 и 2 обрабатывают две плоскости детали А, а фрезы 3 и 4 – две плоскости детали Б. После обработки этих плоскостей стол поворачивается на 900, и деталь Б перемещается в новое положение – становится в позицию для фрезерования двух других плоскостей фрезами 1 и 2; фрезы 3 и 4 при этом положении стола будут обрабатывать две плоскости детали В. При следующем повороте стола на 900 деталь В устанавливается на место, которое в предыдущей позиции занимала деталь Б. При этом положении стола фрезы 1 и 2 фрезеруют у детали Б две последние плоскости. При третьем повороте стола деталь Б попадает на последнюю позицию, где она снимается, а на ее место устанавливается новая заготовка.
Схема фрезерования с применением маятниковой подачи приведена на рис. 4.7. При рабочей подаче стола от позиции 2 к позиции 3 торцовая фреза обрабатывает торец детали А. После этого направление подачи стола изменяется, и он ускоренно перемещается к позиции 4.
При работе подаче стола от позиции 4 к позиции 5 фреза обрабатывает деталь Б. После этого вновь изменяется направление подачи, стол ускоренно подается до позиции 6, и весь цикл повторяется снова. Во время фрезерования детали А обработанная деталь Б снимается (в поз. 7), а на ее место устанавливается новая заготовка.
Отечественные станки последних моделей, в частности мод. 6Н83, могут быть настроены на работу по маятниковому циклу.
Непрерывное фрезерование. В крупносерийном и массовом производстве получил распространение высокопроизводительный способ обработки плоскостей – непрерывное фрезерование. Осуществляется оно в большинстве случаев на карусельно-фрезерных или барабанно-фрезерных станках и иногда на вертикально-фрезерных станках (например, мод. 656П) с поворотным столом.
На карусельно-фрезерных станках (рис. 4.8, а) фрезеруют детали с размерами обрабатываемых плоскостей примерно до 600 мм. Станок имеет станину 1, две стойки 2, жестко соединенные горизонтальной балкой 3, и траверсу 4. На столе 6 станка устанавливают по кругу приспособления и закрепляют в них заготовки 8. Фрезерование производится при непрерывном вращении стола. При этом осуществляется параллельно-последовательная черновая и чистовая обработка, для чего станок имеет две шпиндельные головки 5 с самостоятельными приводами. Головка 5 смонтирована на траверсе 4. Снятие и установка заготовок 8 на столе производится без его остановки в секторе рабочего места 7.
В трехшпиндельных карусельно-фрезерных станках (например, мод. 623В) два правых шпинделя с фрезами диаметром до 300 мм предназначены для черновой обработки, а левый с фрезами диаметром до 600 мм – для чистовой.
Так как на карусельно-фрезерных станках отсутствуют механизмы вертикального перемещения стола, а также продольной и поперечной подач, они обладают большой жесткостью, обеспечивают высокую производительность и точность, особенно в отношении параллельности обрабатываемых поверхностей.
Барабанно-фрезерные станки (рис. 4.8, б) предназначены для обработки параллельных плоскостей заготовок одновременно с двух сторон. Заготовки 5 устанавливаются на гранях барабана 4, укрепленного на валу 3. Барабан вращается от отдельного электродвигателя 2 внутри станины 1. Он может иметь форму четырех-, пяти-, шести-, а иногда и восьмиугольника. Фрезы закрепляются на расположенных с двух сторон одношпиндельных или двухшпиндельных бабках 6.
Таких бабок по две с каждой стороны: одна для чернового фрезерования, а другая – для чистового. Установка и снятие заготовок производится на ходу станка, т. е. осуществляется непрерывное фрезерование.
Большая жесткость конструкции станка обеспечивает высокую и стабильную точность размеров между обрабатываемыми плоскостями.
Дата добавления: 2018-11-24; просмотров: 370; Мы поможем в написании вашей работы! |
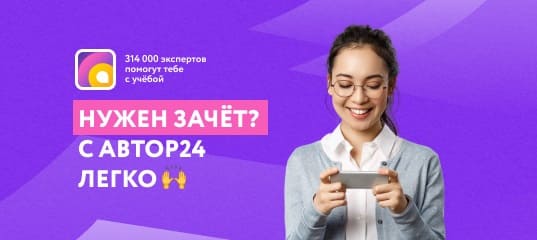
Мы поможем в написании ваших работ!