Задание и порядок выполнения работы:
1. Ознакомиться с инструкцией о выполнении работы.
2. Ознакомиться с теоретическими сведениями о способах и методах образования резьбовых поверхностей
3. Разработать технологический процесс образования резьбовых поверхностей, с составлением всей необходимой технологической документации
4. Составить отчет о работе.
Содержание отчёта:
При составлении отчета необходимо:
I. Ознакомиться с краткими теоретическими сведениями по следующим вопросам:
1. Нарезание резьбы плашками, головками и метчиками
2. Нарезание резьбы резцами
3. Нарезание резьбы вращающимися резцами
4. Фрезерование резьбы
5. Накатывание резьбы
II. Представить технологическую документацию необходимую для выполнения технологического процесса образования резьбовых поверхностей на деталях машин одним из выбранных способов
III. Ответить на контрольные вопросы:
1. Какие бывают плашки для нарезания резьбы?
2. Сколько степеней точности в соответствии с ГОСТом различают у метчиков?
3. Какие по профилю резьбы можно нарезать резцами?
4. На каких станках можно нарезать наружную и внутреннюю резьбы резьбонарезными головками?
5. Какой величине равен задний угол α на вершине зуба у групповых резьбовых фрез?
6. Какой величине равен передний угол γ на вершине зуба у групповых резьбовых фрез?
7. Каким инструментом получают резьбу накатыванием?
8. Какие инструменты применяют при нарезании наружной резьбы?
|
|
9. Какие виды круглых плашек изготавливаются и применяются для нарезания резьбы?
10. Какие способы нарезания резьбы вращающимися резцами Вы знаете?
Литература:
Основная
1. Космачёв И. Г. Технология машиностроения. Лениздат, Ленинград – 1970, 400 с., ил.
Дополнительная
2. Антонов Л. П.и др. Практикум в учебных мастерских. Учеб. пособие для студентов пед. ин-тов по специальности «Общетехнические дисциплины и труд»-М.: «Просвещение»,1976.-400с. с ил.
3. Муравьёв Е. М. Технология обработки металлов: Учеб. пособие для учащихся 5 – 9 кл. общеобразоват. учреждений. - М.: Просвещение, 1995.-224 с., ил.
4. Муравьёв Е. М., Молодцов М. П.Практикум в учебных мастерских: Учеб. пособие для студентов пед. ин-тов по спец. № 2120 «Общетехнические дисциплины и труд» и учащихся пед. уч-щ по спец. № 2008 «Преподавание труда и черчения в неполной сред. шк.» В 2 ч. Ч.1. Обработка металлов /Под ред. Е. М. Муравьёва. - М.: «Просвещение», 1987.-272 с., ил.
Теоретические сведения
Нарезание резьбы плашками, головками и метчиками
Плашками нарезают крепёжные резьбы преимущественно на болтах, винтах и шпильках вручную и на револьверных станках, автоматах и реже на токарных станках.
|
|
Плашки бывают круглые, раздвижные и специальные (для нарезания труб).
Круглые плашки изготовляются цельными, разрезными и трубчатыми. Круглыми плашками нарезают резьбы диаметром от 1 до 52 мм за один проход. Цельные плашки обладают большой жесткостью и обеспечивают получение чистой резьбы, но они малопроизводительны и быстро изнашиваются.
Разрезные плашки в отличие от цельных имеют прорезь (0,5—1,5 мм), что позволяет регулировать диаметр резьбы в пределах 0,1—0,25 мм. Вследствие пониженной жесткости нарезаемая этими плашками резьба имеет недостаточно точный профиль.
Подготовка заготовки-стержня под нарезание резьбы плашкой сводится к правильному выбору его диаметра. Практика показывает, что диаметр стержня должен быть несколько меньше диаметра нарезаемой резьбы. Это объясняется тем, что при образовании профиля резьбы металл детали течет, вследствие чего происходит защемление витков резьбы в плашке.
Плашки устанавливаются в державки или патроны, которые в зависимости от конструкции обеспечивают либо жесткое крепление, либо такое, которое устраняет влияние несовпадения осей детали и отверстия плашки на точность обработки и делает ненужным точное согласование подачи с шагом резьбы.
|
|
Чтобы облегчить врезание плашки в металл, на конце заготовки рекомендуется снимать фаску шириной 2—3 мм.
При нарезании резьбы на токарном станке работу начинают с нарезания нескольких ниток вручную плашкой, закрепленной в плашкодержателе, а затем уже включают шпиндель, упирая плашкодержатель в суппорт (рис. 3.1, а). Более производительным приемом следует считать нарезание первых витков при поджатии плашки пинолью задней бабки, которая сообщает плашке правильное направление (рис. 3.1, б).
Основной недостаток всех типов плашек — необходимость свинчивать их по окончании нарезания резьбы, что значительно увеличивает вспомогательное время.
Резьбонарезные головки. В серийном производстве резьбы нарезаются самораскрывающимися резьбонарезными головками. Это более производительный метод нарезания резьбы, чем обработка плашками, так как благодаря автоматическому раскрыванию головок обратного свинчивания их не требуется.
Резьбонарезными головками можно нарезать наружные и внутренние резьбы на сверлильных, револьверных, болторезных станках и автоматах.
|
|
Наружную резьбу нарезают винторезными головками, а внутреннюю — гайконарезными. Различают вращающиеся и невращающиеся головки.
Невращающимися головками с дисковыми гребенками нарезают резьбу диаметрами 4—42 мм на токарных и револьверных станках. На сверлильных станках и автоматах резьбу нарезают вращающимися головками с дисковыми гребенками.
В винторезных головках гребенки располагаются радиально или тангенциально к нарезаемой резьбе (рис. 3.2). В первом случае головки бывают с дисковыми (рис. 3.2, а) или с призматическими (рис. 3.2, б и в)гребенками, а во втором — только с призматическими. Головками с радиальным расположением гребенок нарезают точные резьбы, а с тангенциальным — менее точные резьбы.
Резьбонарезные головки наряду с высокой производительностью обеспечивают получение резьб 2-го класса точности с шероховатостью поверхности 5—6-го классов.
Наиболее распространенные типы самооткрывающихся головок для нарезания наружной резьбы приведены на рис. 3.3:на рис. 3.3, а показана головка с радиальным расположением дисковых гребенок, на рис. 3.3, б —с радиальным расположением призматических гребенок, а на рис. 3.3, в — с призматическими гребенками, расположенными тангенциально к нарезаемой резьбе.
Винторезные головки с дисковыми гребенками регламентированы ГОСТом.
Рис. 3.3. Самораскрывающиеся головки для нарезания резьбы |
Нарезание резьбы метчиками. Основным инструментом для нарезания внутренних резьб является метчик. В соответствии с ГОСТом метчики изготовляются четырех степеней точности: С, Д, Е и Н; машинно-ручные и гаечные метчики — двух степеней точности: С и Д, а ручные также двух — Е и Н.
Ручные метчики предназначены для нарезания резьб диаметром от 2 до 52 мм вручную. Они выпускаются комплектом, состоящим из двух или трех метчиков.
Гаечные метчики служат для нарезания резьб в сквозных деталях малой толщины как вручную, так и на станках. Они изготовляются с удлиненным хвостовиком для собирания на нем нарезаемых гаек. Номинальный диаметр нарезаемой резьбы — от 2 до 33 мм.
Машинные метчики предназначены для нарезания глухих резьб диаметром от 2 до 52 мм на сверлильных, револьверных и агрегатных станках, автоматах и полуавтоматах. Выпускаются они комплектом из двух метчиков и одинарные.
Для нарезания резьбы метчиками необходимо произвести предварительную обработку отверстия. В зависимости от необходимой точности резьбы отверстие предварительно сверлят, зенкеруют или растачивают.
При нарезании резьбы материал детали несколько выдавливается метчиком, и внутренний диаметр резьбы оказывается больше диаметра исходного отверстия. Это обстоятельство учтено в специальных таблицах, по которым выбирают диаметр отверстия под резьбу.
При нарезании резьб на станке метчики крепят в патронах — быстросменных, самоцентрирующих, качающихся и плавающих:
В быстросменных патронах обычного типа метчик жестко связан со шпинделем станка.
Качающиеся и плавающие патроны позволяют метчику самоустанавливаться в нарезаемом отверстии в первом случае благодаря отклонению его оси от вертикали, а во втором — за счет смещения его параллельно собственной оси.
При нарезании резьбы в отверстиях, не препятствующих свободному удалению метчика после рабочего хода, он пропускается полностью через отверстие и затем вставляется в патрон для нарезания следующей детали. Для сокращения времени на установку и снятие метчик в патроне не крепится. Крутящий момент передают квадрат, лыски или срезы на хвостовике. При работе на станках с вертикальной осью метчик свободно падает в конце прохода.
При нарезании резьбы на вертикально- и радиально-сверлильных станках во избежание поломок метчика при упоре его в дно глухого отверстия, а также при перегрузке применяются предохранительные патроны (рис. 3.4), позволяющие метчику останавливаться при вращающемся шпинделе, когда крутящий момент превысит безопасную величину. Предохранительный патрон состоит из корпуса 1 с коническим хвостовиком и ведомой втулкой 2, предназначенной для крепления метчика. Ведомая втулка 2 соединяется с ведущей 3 трапецеидальными зубьями. Ведущая втулка, связанная с корпусом шпонкой, прижимается к ведомой пружиной 4. При увеличении крутящего момента больше допустимой величины осевая составляющая сила на зубьях втулок превысит силу пружины, ведущая втулка продвинется вдоль оси, ее зубья выйдут из зацепления, и ведомая втулка остановится. Натяжение пружины регулируют гайкой 5.
Для каждого патрона существует определенный интервал диаметров нарезаемых резьб. Наиболее часто используют комплект из трех патронов: для нарезания резьб диаметрами 8—12, 12—30 и 18—42 мм.
В массовом производстве гайки нарезают на гайконарезных автоматах и полуавтоматах с кривыми метчиками, закрепленными в специальном патроне.
Схема нарезания резьбы невращающимся метчиком с изогнутым хвостовиком приведена на рис. 3.5. Заготовки гаек 1 при помощи толкателя 2 поступают в направляющую втулку 3, в которой они центрируются и приводятся во вращение зубчатыми колесами 4 и 5. В процессе нарезания резьбы гайка центрируется по метчику 6, благодаря чему и обеспечивается концентричность резьбы. Нарезанные гайки 7 движутся по метчику и, пройдя втулку 8, сходят с конца хвостовика в сборник.
Вследствие недостаточной прочности метчика на режущей части не должно быть одновременно более двух гаек.
Для получения резьбы 2-го класса точности скорость резания принимают в пределах 7—15 м/мин.
Точность резьбы, нарезаемой метчиками, может колебаться в широких пределах. Метчиком с нешлифованным профилем нарезают резьбу 3-го класса точности, а со шлифованным — 2-го класса. При тщательной подготовке отверстия метчиком со шлифованным профилем можно нарезать резьбу 1-го класса точности. Калибрование резьбы вручную также повышает ее точность.
Нарезание резьбы резцами
Нарезание треугольной резьбы. Существует много способов нарезания резьбы многолезвийными инструментами, однако наиболее широко распространен способ обработки резьбы резцами на токарных станках. Этот способ, ставший универсальным, почти всегда используется при нарезании резьбы на ответственных деталях, а с внедрением твердосплавных инструментов он сделался ипроизводительным.
В настоящее время применяют два способа нарезания резьбы на станках токарного типа:
1) резцами, неподвижно закрепленными в суппорте;
2) вращающимися резцами.
Треугольную резьбу нарезают по двум схемам (рис. 3.6). Первая схема (наиболее распространенная) характеризуется тем, что резец подается в поперечном направлении перпендикулярно к оси нарезаемой детали (рис. 3.6, а). В целях облегчения условий схода стружки и повышения стойкости резца перед каждым проходом его следует смещать на 0,1—0,15 мм поочередно то вправо, то влево осевой подачей верхнего суппорта. Эта схема рекомендуется для нарезания резьб с шагом s ≤ 2—2,5 мм.
При нарезании резьб с шагом s > 2—2,5 мм при черновых проходах резец подается не перпендикулярно к оси нарезаемой детали, а под углом, равным половине угла профиля резьбы (рис. 3.6, б). При нарезании по этой схеме значительно улучшаются условия работы — меньше деформируется и свободно выходит из зоны резания стружка, увеличивается стойкость резца. Для получения более точной резьбы окончательное нарезание выполняется по первой схеме.
Установка резца относительно обрабатываемой детали при нарезании резьбы по второй схеме приведена на рис. 3.7. На рис. 3.7, а показана установка прямого резца с прямолинейной режущей кромкой, заточенной под углом 30° к его оси. Резец располагается в резцедержателе верхних салазок суппорта, повернутых под углом 30°, и подается на глубину в направлении стрелки Л. На рис. 3.7, б приведена установка правого отогнутого резца. Резцедержатель К в этом случае устанавливается прямо, как при обычном точении, что позволяет уменьшить вылет резца. Резец подается по стрелке А, как и в предыдущем случае.
При необходимости повысить точность изготовления резьбы, а также при нарезании резьб с крупным шагом работа распределяется между черновым и чистовым резцами.
Высокие скорости резания при образовании резьб требуют от рабочего большого напряжения и мгновенной реакции, чтобы своевременно отвести резец от детали в конце каждого прохода, особенно при нарезании внутренней и наружной резьб в упор.
В крупносерийном и массовом производстве целесообразно нарезать резьбы на полуавтоматах, работающих по методу многократных и последовательных проходов. Схема автоматического цикла нарезания наружной резьбы показана на рис. 3.8. На участке 1—2 осуществляется рабочий ход; на участке 2—3 — отход резца; на участке 3—4 — обратный ход резца в исходное положение и, наконец, на участке 4—1 резец подается на глубину резания.
Нарезание трапецеидальной и прямоугольной резьб. Взависимости от типа, размеров и точности резьбы применяется та или иная технология формирования ее профиля.
Нарезание мелких резьб (с шагом до 4 мм) производится быстрорежущими резцами полного профиля. Перемещение резца перед каждым проходом осуществляется поперечной подачей.
Нарезание более крупных резьб, а также точных мелких разделяют на предварительное и окончательное, выполняемое раздельно чистовыми и черновыми резцами.
Трапецеидальные и модульные резьбы с шагом до 4 мм (модуль до 1,5 мм) обрабатывают одним резцом. Точные резьбы таких же размеров нарезают двумя резцами — черновым с углом профиля меньше, чем 2α, и чистовым с углом профиля, равным 2α. Дно резьбовой канавки формируют черновым резцом.
Резьбы с шагом от 4 до 12 мм (модуль от 1,5 до 4 мм) обрабатывают двумя или тремя резцами. В условиях единичного производства черновым резцом прорезают
канавку не на полную глубину, а чистовым обрабатывают ее окончательно.
В серийном производстве резьбы с шагом 4—12 мм нарезают последовательно тремя резцами (рис. 3.9). Предварительно резьбу обрабатывают прорезными резцами 1 и 2 и окончательно — профильным резцом 3. Прорезным резцом 1 шириной, равной ширине канавки по среднему диаметру резьбы минус 0,2 мм, прорезают канавку до середины профиля резьбы (рис. 3.9, а). Затем прорезным резцом 2 шириной, равной ширине дна канавки, прорезают канавку до внутреннего диаметра резьбы (рис. 3.9, б). После этого профильным резцом 3 резьбу обрабатывают окончательно (рис. 3.9, в).
Более производительные схемы нарезания трапецеидальной резьбы приведены на рис. 3.10. Прорезным резцом шириной, равной полной ширине канавки у дна, прорезают канавку до внутреннего диаметра (рис. 3.10, а). Затем левым подрезным резцом обрабатывают левый боковой уступ (рис. 3.10, б), а правым — правый уступ (рис. 3.10, в).
Нарезание резьбы по этой схеме доступно токарям высокой квалификации.
При нарезании прямоугольных резьб в связи с большим углом подъема винтовой линии резец устанавливают двумя способами.
1. Режущая кромка резца аб располагается параллельно оси обрабатываемой детали в горизонтальной плоскости, проходящей через деталь (рис. 3.11). В данном случае все режущие кромки резца являются прямолинейными. Так как у прямоугольной резьбы ширина канавки в осевом сечении является постоянной величиной независимо от глубины нарезки, то при такой установке резца будет получена резьба с геометрически-правильным прямо
угольным профилем.
К недостаткам этого способа относится то, что при больших углах подъема винтовой линии у одной режущей кромки резца образуется тупой угол резания δ2, вследствие чего она скоблит, а не режет, а у другой — острый угол резания δ1, что сильно ослабляет режущую кромку. Кроме того, создается опасность врезания резца в металл под влиянием сил, возникающих вследствие трения одной из поверхностей резца о стенку канавки.
2. Режущая кромка резца а'б' располагается перпендикулярно к направлению винтовой линии нарезаемой резьбы (рис. 3.11), и недостатки, свойственные первому
способу, исключаются. В то же время возникает другое затруднение. Чтобы получить геометрически правильный профиль прямоугольной резьбы, все три режущие кромки резца должны быть криволинейными, что значительно усложняет изготовление и эксплуатацию резцов. Поэтому первый способ установки резцов применяют при чистовом нарезании резьбы, а второй — при черновом, когда можно пренебречь получающимися искажениями
профиля. Чистовое нарезание с большим углом подъема резьбы осуществляется тремя отдельными резцами с прямолинейными режущими кромками.
Прямоугольную резьбу обрабатывают стержневыми резьбовыми резцами. Резьбы с шагом до 4 мм нарезают одним резцом. В этом случае профиль резца должен соответствовать профилю резьбы. При нарезании резьбы с большим шагом или повышенной точности применяют последовательно два резца (рис. 3.12, а). Первым резцом — предварительным — удаляют основной припуск, а чистовым — окончательно профилируют резьбу. Ширина резцов для предварительного нарезания прямоугольной резьбы на 0,3—0,6 мм меньше ширины ее впадины. Резцы для чистового нарезания имеют профиль резьбы. Обычно ширина резца на 0,01—0,04 мм больше ширины впадины резьбы (с учетом упругих деформаций металла).
При повышенных требованиях к качеству резьбы предварительно нарезанная прямоугольная резьба окончательно формируется двумя чистовыми резцами — правым и левым, каждый из которых обрабатывает лишь одну сторону резьбовой канавки (рис. 3.12, б).
Нарезание многозаходной резьбы является одной из наиболее трудоемких операций, так как при этом много времени затрачивается на точный поворот детали перед обработкой каждой очередной винтовой канавки (нитки).
Существует несколько способов деления заготовки при нарезании многозаходной резьбы. Рассмотрим наиболее производительные из них.
Весьма просто осуществить деление при помощи поводкового патрона с несколькими пазами (рис. 3.13, а). Число пазов должно равняться числу ходов винта или быть кратным этому числу. После нарезания одной нитки резьбы заготовку снимают с центров и снова ставят на них таким образом, чтобы хомутик попал в следующий паз поводкового патрона. Затем нарезают вторую нитку.
Большое распространение нашел способ нарезания многозаходных резьб при помощи специального делительного патрона (рис. 3.13, б). Патрон состоит из двух дисков. Первый диск жестко закреплен на шпинделе станка. Второй, в котором при помощи хомутика и скобы крепится заготовка, может поворачиваться относительно первого на любой угол. На первом диске имеется риска, а на втором нанесено 360 делений через 1°.
Например, если требуется нарезать трехзаходную резьбу, то после каждого захода второй диск вместе с заготовкой поворачивают на угол, равный
= 120°, и затем жестко стягивают болтами оба диска.
Этот способ деления применяют для деталей, которые можно обрабатывать в центрах.
При одновременном нарезании многозаходной резьбы несколькими резцами, установленными в специальных державках, деление обеспечивается автоматически. При нарезании двухзаходных ходовых винтов пользуются резцедержателем (рис. 3.14), в котором закреплены два резца. Устанавливаются они по шаблону на расстоянии, точно соответствующем шагу между заходами. Таким образом, оба резца нарезают одновременно две канавки. Очевидно, что для обработки трехзаходной резьбы можно было бы таким же образом установить и три резца.
Дата добавления: 2018-11-24; просмотров: 334; Мы поможем в написании вашей работы! |
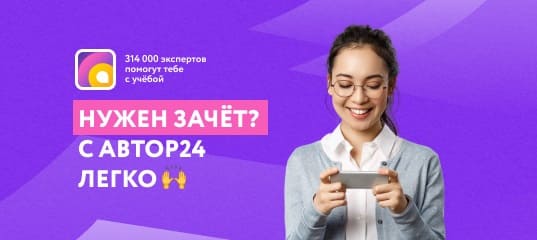
Мы поможем в написании ваших работ!