Задание и порядок выполнения работы:
1. Ознакомиться с инструкцией о выполнении работы.
2. Ознакомиться с теоретическими сведениями о способах и методах обработки плоских поверхностей
3. Разработать технологический процесс обработки плоских поверхностей, с составлением всей необходимой технологической документации
4. Составить отчет о работе
Содержание отчёта:
При составлении отчета необходимо:
I. Ознакомиться с краткими теоретическими сведениями по следующим вопросам:
1. Обработка плоскостей строганием и долблением
2. Обработка плоскостей фрезерованием
3. Обработка плоскостей протягиванием
II. Представить технологическую документацию необходимую для выполнения технологического процесса обработки плоских поверхностей одним из выбранных способов
III. Ответить на контрольные вопросы:
1. Какой вид механической обработки плоских поверхностей применяется в мелкосерийном производстве?
2. Какие два вида строгания Вы знаете?
3. Каких величин достигают скорости резания на современных станках?
4. Какие детали обрабатывают на долбежных станках?
5. При каком виде фрезерования направление движения подачи направлено против вращения фрезы?
6. Какой способ фрезерования настоящее время обеспечивает повышение производительности труда?
7. При каком виде фрезерования направление движения подачи совпадает с направлением вращения фрезы?
8. Каким образом осуществляется комбинированное протягивание?
|
|
9. Что является недостатками протягивания?
10. Что является преимуществом обработки плоскостей протягиванием?
Литература:
Основная
1. Космачёв И. Г. Технология машиностроения. Лениздат, Ленинград – 1970, 400 с., ил.
Дополнительная
2. Антонов Л. П.и др. Практикум в учебных мастерских. Учеб. пособие для студентов пед. ин-тов по специальности «Общетехнические дисциплины и труд». - М.: «Просвещение», 1976.– 400 с. с ил.
3. Барбашов Ф. А. Фрезерное дело. Учебное пособие для учебных заведений профтехобразования.-М.: Высш. школа, 1973.-277 с., ил.
4. Денежный П. М., Стискин Г. М., Тхор И. Е.Токарное дело. Учебное пособие для проф.-техн. училищ.-М.: Высш. школа, 1972.-304 с., ил.
5. Иванова Г. А.Основы теории резания, инструменты, станки.- М.: Учпедгиз, 1963.-264 с.,ил.
6. Лернер П. С., Лукьянов П. М.Токарное и фрезерное дело: Учеб. пособие для учащихся 9-10 кл. сред общеобразоват. шк. - М.: Просвещение, 1986.–223 с., ил.
7. Муравьёв Е. М. Технология обработки металлов: Учеб. пособие для учащихся 5 – 9 кл. общеобразоват. учреждений. - М.: Просвещение, 1995.-224 с., ил.
8. Рубинштейн С. А., Левант Г. В., Тарасевич Ю. С. Основы учения о резании металлов и режущий инструмент.-М.: Машиностроение, 1968.- 392 с., ил.
Теоретические сведения
|
|
Обработка плоских поверхностей
Плоские поверхности определяют внешнюю конфигурацию большой группы деталей – станин, плит, блоков цилиндров, суппортов и рабочих столов станков, угольников, бабок и других подобных деталей.
Если при обработке поверхностей вращения основное внимание обращают на размер самой поверхности, в частности на ее диаметр, то при обработке плоских поверхностей, прежде всего, необходимо обеспечить правильное расположение плоскости относительно других поверхностей или осей и, кроме того, правильность геометрической формы поверхности в отношении плоскости.
Наружные плоскости корпусных и других деталей обрабатывают следующими основными способами: строганием, долблением, фрезерованием, протягиванием, точением и шлифованием.
Обработка плоскостей строганием и долблением
В единичном и мелкосерийном производстве при обработке плоских поверхностей широко используется строгание и долбление. Объясняется это тем, что для работы на строгальных и долбежных станках не требуется сложных приспособлений и режущих инструментов. На этих станках простыми резцами можно обработать довольно сложный профиль и за один проход снять большой припуск. Однако производительность этих станков низка из–за наличия холостых ходов и небольших скоростей.
|
|
Горизонтальные, вертикальные и наклонные плоскости больших и тяжелых деталей обрабатывают на продольно- строгальных станках. На них можно обрабатывать одновременно значительное количество небольших по размерам деталей.
В настоящее время станкостроительная промышленность выпускает уникальные продольно- строгальные станки с шириной строгания 5000 мм и длиной 15000 мм, на которых можно обрабатывать детали весом до 200 т.
Процесс строгания характеризуется низкой производительностью и прерывистостью резания. Систематические удары при врезании резца в обрабатываемую деталь оказывают весьма неблагоприятное влияние на стойкость резца, который часто разрушается.
Применение продольно- строгальных станков моделей 7212 и 7112 позволяет избежать этих недостатков. Для повышения производительности и работы без удара эти станки осуществляют автоматически следующие движения: медленное врезание инструмента в деталь; разгон стола до установленной скорости резания и обработку при этой скорости; снижение скорости движения стола перед выходом резца из заготовки; быстрый возврат стола; подачу суппортов с резцами.
|
|
Указанные станки имеют два диапазона работы – силовой и скоростной. На силовом диапазоне производится черновая обработка на оптимальных режимах резания, а на скоростном – чистовая при большой скорости резания и небольших глубинах и подаче.
Поперечно-строгальные станки с возвратно- поступательным движением инструмента и длиной обработки до 2000 мм предназначены для обработки горизонтальных, вертикальных и наклонных плоскостей.
Станки эти применяются в ремонтных и других цехах с резко выраженным единичным характером производства.
На долбежных станках обрабатывают детали небольших размеров – шпоночные пазы, канавки, наружные плоскости и т. п. – в условиях единичного и мелкосерийного производства. Детали устанавливают на столе, который может делать продольное, поперечное и круговое перемещения. Станки обычно имеют небольшую длину хода долбяка (до 500 – 700 мм).
К недостаткам долбежных станков следует отнести низкую производительность и повышенные требования в отношении квалификации рабочих.
Основными достоинствами процесса обработки плоскостей на строгальных и долбежных станках являются простота и дешевизна режущего инструмента. ГОСТ 10045 – 62 предусматривает пять типов быстрорежущих строгальных резцов, а ГОСТ 9796 – 61 – шесть типов. Долбежные быстрорежущие резцы общего назначения в соответствии с ГОСТом 10046 – 62 изготавливаются трех типов.
При обработке плоскостей на строгальных и долбежных станках специальные приспособления для закрепления детали применяют редко. Как правило, детали устанавливают прямо на стол станка и закрепляют универсальными зажимными устройствами. Способ установки деталей на стол станка с выверкой требует больших затрат вспомогательного времени и сравнительно высокой квалификации рабочего.
Строгание может быть предварительным (черновым) и окончательным (чистовым). При черновой обработке деталей больших размеров на продольно- строгальных станках глубина резания достигает 40 мм и более. Скорость резания обычно лимитируется возможностями станка и инерционными усилиями, возникающими при реверсировании стола. На современных станках скорости резания достигают 75-80 м/мин.
Черновое строгание выгодно осуществлять с большими подачами и небольшими скоростями. Так, например, при обработке чугуна с большими подачами твердосплавными резцами скорость резания составляет 12 – 20 м/мин, а при строгании быстрорежущими резцами – 6 – 12 м/ мин.
Смазочно-охлаждающие жидкости при черновом строгании не применяют.
Для получения высокой точности формы обработанной плоскости черновое и чистовое строгание рекомендуется выполнять на отдельных операциях.
На современных продольно-строгальных станках (например, моделей 7212 и 7112), имеющих плавное движение стола, можно производить чистовую обработку плоскостей. Сущность чистового строгания состоит в том, что специальными твердосплавными резцами с применением смазки с детали снимают тонкие (менее 0,1 мм) стружки. При чистовом строгании шероховатость обработанной поверхности достигает 6 – 7-го классов, отклонение от плоскостности – до 0,01 мм на 1 м и площадь несущей поверхности – до 60 – 70 %.
Чистовое строгание осуществляют стержневыми и чашечными резцами. Стержневые резцы бывают как с прямой, так и с изогнутой державкой (рис. 4.1, а). При строгании чугуна передний угол резца γ = 8 – 100 , задний α = 50, угол наклона главной режущей кромки λ = 150. Расположение режущей кромки под углом λ = 150 обеспечивает плавное врезание и выход резца и предохраняет от ударов его вершину. Стержневые резцы бывают широкие с длинной зачистной кромкой (10 – 25 мм) и сверхширокие, длина лезвия которых больше ширины обрабатываемой плоскости.
Чашечный резец (рис. 4.1, б) благодаря возможности поворота ножа при его затуплении имеет более высокую стойкость.
Чистовое строгание осуществляется минимум за два прохода. При первом проходе снимают основной припуск с глубиной резания t = 0,5 – 0,8 мм. При втором проходе глубина резания не должна превышать t = 0,05 – 0,08 мм. Величину подачи выбирают в зависимости от длины активной части режущей кромки резца.
Скорость резания зависит от свойств обрабатываемого материала, жесткости системы, конструкции и геометрических параметров резца. При обработке чугунов твердосплавными резцами для первого прохода v = 15 – 20 м/мин, для второго v = 4 – 12 м/мин. При появлении вибраций скорость резания надо снижать.
Перед чистовым строганием чугунных деталей обрабатываемую поверхность следует смачивать керосином или 0,03 %-ным водным раствором двухромокислого калия.
Повышение производительности при строгании может быть достигнуто при многорезцовом резании, одновременной обработке группы деталей, использовании широких резцов и специальных устройств.
На станках, имеющих несколько суппортов, многорезцовое резание осуществляется как путем одновременного использования их, так и при помощи многорезцовых державок. В этом случае одновременно могут обрабатываться либо разные поверхности, либо одна и та же.
При обработке одной и той же поверхности многорезцовое резание может производиться путем распределения между резцами ширины обрабатываемой плоскости (рис. 4.2, а), ширины среза (глубины резания) (рис. 4.2, б) и толщины среза (подачи) (рис. 4.2, в).
Одновременная обработка группы деталей одних и тех же или разных наименований, расположенных в один или два ряда на столе станка, также повышает производительность.
Наличие холостого хода при строгании и долблении значительно снижает производительность этих процессов. В связи с этим появились многочисленные предложения по использованию обратного хода стола. Однако, если первые конструкции продольно-строгальных станков позволяли производить строгание при прямом и обратном ходах стола, то в последних конструкциях такой возможности нет, а для повышения производительности веден ускоренный холостой ход.
Дата добавления: 2018-11-24; просмотров: 205; Мы поможем в написании вашей работы! |
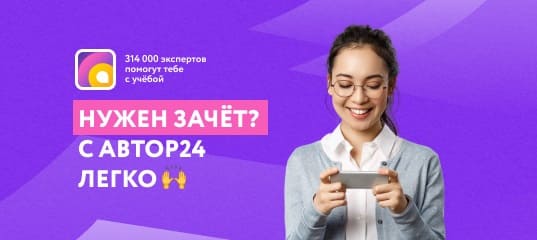
Мы поможем в написании ваших работ!