Задание и порядок выполнения работы:
1. Ознакомиться с инструкцией о выполнении работы.
2. Ознакомиться с теоретическими сведениями о способах и методах обработки фасонных поверхностей
3. Разработать технологический процесс обработки фасонных поверхностей, с составлением всей необходимой технологической документации
4. Составить отчет о работе.
Содержание отчёта:
При составлении отчета необходимо:
I. Ознакомиться с краткими теоретическими сведениями по следующим вопросам:
- Обработка фасонных поверхностей тел вращения
2. Фрезерование фасонных поверхностей
3. Обработка фасонных отверстий
II. Представить технологическую документацию необходимую для выполнения технологического процесса обработки фасонных поверхностей одним из выбранных способов
III. Ответить на контрольные вопросы:
1. Назовите виды фасонных резцов.
2. Какой величины не превышает ширина фасонных резцов?
3. Какова величина переднего угла γ фасонных фрез с затылованным зубом?
4. В основном при какой подаче работают фасонные резцы?
5. Каким методом производится определение искажения профиля резца?
6. Какое съемное поворотное приспособление нашло широкое применение, при фасонной обработке поверхностей?
7. С какой системой получили наибольшее распространение копировально-фрезерные станки?
8. Какой мощности необходим постоянный ток, для движения фрезы при осуществлении фасонной обработки?
9. Стержневые, призматические, дисковые — это виды каких по назначению резцов?
|
|
10.На каких принципах в настоящее время основано действие металлорежущих станков?
Литература:
Основная
1. Космачёв И. Г. Технология машиностроения. Лениздат, Ленинград – 1970, 400 с., ил.
Дополнительная
2. Антонов Л. П.и др. Практикум в учебных мастерских. Учеб. пособие для студентов пед. ин-тов по специальности «Общетехнические дисциплины и труд». - М.: «Просвещение», 1976.– 400 с. с ил.
3. Барбашов Ф. А. Фрезерное дело. Учебное пособие для учебных заведений профтехобразования.-М.: Высш. школа, 1973.-277 с., ил.
4. Денежный П. М., Стискин Г. М., Тхор И. Е.Токарное дело. Учебное пособие для проф.-техн. училищ.-М.: Высш. школа, 1972.-304 с., ил.
5. Иванова Г. А.Основы теории резания, инструменты, станки.- М.: Учпедгиз, 1963.-264 с.,ил.
6. Лернер П. С., Лукьянов П. М.Токарное и фрезерное дело: Учеб. пособие для учащихся 9-10 кл. сред общеобразоват. шк. - М.: Просвещение, 1986.–223 с., ил.
7. Рубинштейн С. А., Левант Г. В., Тарасевич Ю. С. Основы учения о резании металлов и режущий инструмент.-М.: Машиностроение, 1968.- 392 с., ил.
Теоретические сведения
Обработка фасонных поверхностей тел вращения
Фасонные поверхности можно обрабатывать фасонным инструментом, имеющим профиль обрабатываемой поверхности, а также нормальным инструментом (резцом), которому сообщается криволинейное движение относительно обрабатываемой поверхности при помощи копировальных устройств или вручную.
|
|
Обработка фасоннымиинструментами. Фасонные поверхности небольшой длины обрабатывают фасонными резцами (рис. 5.1). Различают стержневые, призматические и дисковые фасонные резцы.
Стержневыми резцами (рис. 5.1, а)обрабатывают фасонные поверхности сравнительно простой формы. Применяют эти резцы редко, так как стойкость их невелика, а заточка обычно искажает профиль.
Призматический фасонный резец (рис. 5.1, б)допускает значительно большее число переточек. Крепится резец 1 за выступ 2 в виде ласточкина хвоста в державке 4 и затягивается болтом 3. Так как паз у державки наклонный, при уста-новке резца автомати-чески обеспечивается получение переднего угла γ = 0° и заднего α = 12—15°.
Дисковый фасонный резец (рис. 5.1, в)имеет вырез, образующий переднюю поверхность 1. Резец крепится в державке с помощью специального болта, проходящего через отверстие 2.
Установка резца под определенным углом достигается с помощью нанесенных на торце рифлений 3.
|
|
Ширина фасонных резцов не превышает 40—60 мм. Только при обработке весьма жестких деталей на мощных станках применяются более широкие плоские резцы (шириной до 150 мм).
Для образования заднего угла передняя поверхность режущей части дискового фасонного резца (рис. 5.1, г)опускается ниже центра на величину h, которая определяется по следующей формуле:
h = sin α,
где D — диаметр резца, в мм;
α — задний угол резца, в град.
Расположение передней поверхности по центру резца (рис. 5.1, д)недопустимо, потому что в этом случае задний угол равнялся бы нулю.
Так как передняя поверхность фасонного резца расположена ниже центра, его профиль не совпадает с профилем обрабатываемой детали. Определение искажения профиля резца производят либо графически, либо аналитически.
Фасонные резцы работают при поперечной подаче, поэтому их режущие кромки начинают резание с наружного слоя заготовки. При наличии на заготовке твердой корки резцы быстро изнашиваются. Во избежание этого целесообразно предварительно обтачивать заготовки обычным резцом без соблюдения профиля, а затем уже осуществлять окончательную обработку фасонным резцом.
Подачи при точении фасонными быстрорежущими резцами принимают в пределах от 0,01 до 0,1 мм/об, а скорости — от 15 до 55 м/мин. При высоких требованиях к шероховатости поверхности обработку рекомендуется производить при скоростях резания менее 4 м/мин.
|
|
При изготовлении незначительного количества деталей с большими фасонными поверхностями для обтачивания их используют обычные проходные резцы. Вначале за несколько продольных проходов проходным резцом поверхности придают ступенчатую форму, а затем при одновременной продольной и поперечной подачах вручную доводят ее до окончательной формы, которую контролируют шаблоном.
Обработка фасонных поверхностей с помощью приспособлений. Во многих случаях фасонные поверхности обрабатывают с помощью механических копировальных устройств с двусторонним или односторонним копиром. Одна из схем обработки фасонной поверхности на токарном станке с применением двустороннего копира приведена на рис. 5.2. К задней стенке станины станка прикреплен угольник, на горизонтальной полке которого расположена плита 1. На плите неподвижно установлены две копирные планки 3 и 4, профиль рабочей поверхности которых соответствует профилю детали 5. Копирные планки расположены таким образом, что между ними образован ручей А, куда сминимальным зазором входит ролик. Кронштейн 2 прикреплен к торцу поперечного суппорта, винт которого выключен. При продольной автоматической подаче резец получает дополнительное перемещение от копира в направлении поперечной подачи, что и позволяет образовать требуемую форму детали.
Двусторонние копиры обеспечивают надежное движение резца по заданному профилю. Однако они непригодны для обработки точных фасонных деталей вследствие наличия неизбежных зазоров между роликами и планками копира. Двусторонние копиры применяют для чернового обтачивания фасонных поверхностей.
Копировальное устройство, показанное на рис. 5.3, предназначено для более точной обработки фасонных поверхностей. Копир 8 расположен впереди поперечного суппорта и своей прямолинейной кромкой опирается нанеподвижный цилиндрический стержень 6. Щуп, 7, прикрепленный к переднему торцу поперечного суппорта, под действием пружин 1 постоянно касается криволинейной кромки копира, что при продольной автоматической подаче резца сообщает ему поперечное перемещение, обеспечивающее получение требуемых формы и размеров обрабатываемой фасонной поверхности.
Наличие тяги 5, шарнирно связанной с копиром и проходящей через кронштейн 3, который прикреплен к станине станка, дает возможность регулировать гайками 2 и 4 положение копира в осевом направлении.
Копировальное устройство, изображенное на рис. 5.3, позволяет обрабатывать детали с высокой точностью.
Весьма эффективно обтачивание фасонных поверхностей с помощью гидрокопировального суппорта. Гидросуппорт обеспечивает автоматическое копирование по заранее изготовленному копиру или же по одной из деталей партии, принятой за эталонную. Применение гидросуппорта при обработке фасонных поверхностей позволяет значительно повысить производительность труда благодаря уменьшению затрат как машинного, так и вспомогательного времени.
Схема обработки фасонных поверхностей при помощи гидросуппорта показана на рис. 5.4. Из схемы имеем:
,
где s — результирующая подача (скорость) резца, направленная по касательной к обрабатываемому профилю в рассматриваемой точке;
s1 — продольная подача суппорта станка;
s2 — дополнительная подача гидросуппорта с резцом вдоль оси цилиндра.
Продольная подача суппорта станка равна:
s1 = AO = CO+AC;
CO = BO cos α = s cos α;
AC=BC=BO sin α = s sin α,
где α — угол, образованный касательной к профилю детали в данной точке и осью детали (угол подъема профиля детали). Таким образом,
s1 = s cos α + s sin α,
откуда
s =
.
Полученное выражение показывает, что при обтачивании фасонных поверхностей результирующая подача резца s изменяется в процессе работы в зависимости от наклона касательной, т. е. профиля детали. При обработке конических поверхностей, где α = const, и при подрезке торцов, где α = 90°, значение s остается неизменным.
Из приведенной выше формулы можно сделать следующие выводы. При обработке фасонных поверхностей, у которых диаметр увеличивается по направлению к передней бабке, изменение результирующей подачи s происходит в сторону ее уменьшения по отношению к основной подаче суппорта. Наименьшего значения эта результирующая подача достигает при α = 45° и составляет s ≈ 0,7s1.
Для конических поверхностей с углом наклона образующей в диапазоне от α = 0 до α = 90° значение результирующей подачи 5 будет находиться в следующих пределах:
0,75s1 ≤ s ≤ s1.
Максимальное значение s, равное 0,75s1 будет иметь место при α =45°.
Для участков фасонного профиля с отрицательными углами наклона касательной, т. е. таких, у которых диаметры уменьшаются по направлению к передней бабке, результирующая подача s возрастает. При α = —30°, s = 2,73s1.
При больших значениях отрицательных углов а обработка фасонных и конических поверхностей с помощью гидросуппорта становится нецелесообразной из-за еще более резкого возрастания подачи s, величина которой стремится к бесконечности при α = —45°.
Применение гидросуппортов для обработки фасонных, конических и ступенчатых поверхностей экономически оправдывает себя даже в мелкосерийном производстве.
Сферические поверхности обрабатываются фасонными резцами и с помощью различных приспособлений в основном на токарных и расточных станках. В единичном производстве их можно обтачивать проходными (по шаблону) и фасонными резцами.
В большинстве случаев сферические поверхности обрабатывают при помощи различных приспособлений. Широко распространено съемное поворотное приспособление, так называемый шаровой суппорт (рис. 5.5). Корпусом 3 он закрепляется на месте резцедержателя или же в самом резцедержателе. В корпусе смонтированы салазки 4 резцедержателя, которые поворачиваются вокруг оси вала 6. Ось этого вала в вертикальной плоскости должна проходить через ось вращения шпинделя.
Салазки резцедержателя имеют направляющие, по которым с помощью винта 2 может перемещаться на величину заданного радиуса R резцедержатель 1. После, установки резца резцедержатель закрепляется. Врезание резца происходит при поперечной подаче суппорта станка. Вращение салазкам 4 сообщается с помощью рукоятки, насаженной на вал червяка, и червячной пары 5 и 7.
Сферические поверхности можно обрабатывать и фрезерованием. Для этого необходимы делительная головка и поворотный стол, приводимые в движение от механизма подачи стола. Инструментом служит полая либо торцовая фреза.
Сущность фрезерования сферических поверхностей заключается в следующем. Предположим, что нам надо обработать сферическую поверхность ABC (рис. 5.6) с центром в точке О. Представим себе, что конус с основанием АВ и вершиной в точке О вращается вокруг образующей ВО. Тогда все точки основания АВ конуса будут располагаться на шаровой поверхности. Если обработку будем вести торцовой фрезой с внутренним диаметром Dф, равным диаметру основания АВ воображаемого конуса, и установим эту фрезу так, чтобы ее ось расположилась под углом α, равным половине угла при вершине воображаемого конуса АОВ, то при вращении фрезы вокруг своей оси, а обрабатываемой детали вокруг оси ВО шаровая поверхность окажется обработанной после одного полного оборота детали.
Зная диаметр сферической поверхности Dш и высоту Н шарового сегмента, легко установить величину диаметра фрезы Dф и величину угла установки α:
Dф = ; sin α =
.
Величина угла установки а может быть выражена через Dш и Н:
sin α = .
Высокая производительность фрезерования сферических поверхностей позволяет использовать его не только в условиях мелкосерийного производства, но и в крупносерийном.
Дата добавления: 2018-11-24; просмотров: 314; Мы поможем в написании вашей работы! |
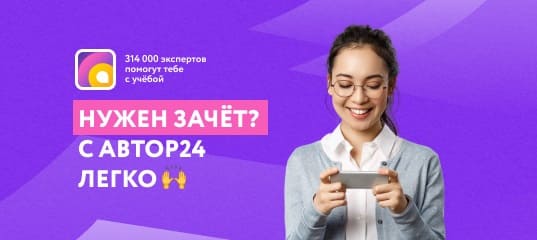
Мы поможем в написании ваших работ!