Фрезерование фасонных поверхностей
В машиностроении фасонные поверхности встречаются очень часто, причем они могут представлять собой сочетание плоскостей, расположенных по отношению друг к другу под определенными углами, или иметь криволинейный профиль.
Обработка фасонных поверхностей относится к сложным и трудоемким операциям. На фрезерных станках она осуществляется двумя способами: фасонными фрезами и обычными фрезами с помощью приспособлений.
Обработка фасонными фрезами — один из производительных способов фрезерования, применяющийся в крупносерийном и массовом производстве. Обработка производится на горизонтально-фрезерных и продольно-фрезерных станках.
Фасонные фрезы — инструмент специальный, изготовляется он инструментальными цехами машиностроительных заводов.
Фасонные фрезы непригодны для работы по корке. Поэтому в целях рациональной эксплуатации фрез иповышения их производительности черные поверхности рекомендуется предварительно обрабатывать любым другим инструментом. Предварительная обработка применяется и в тех случаях, когда глубина резания, а также протяженность режущей кромки получаются достаточно большими.
Фасонные фрезы изготовляют с затылованным зубом и передним углом γ = 0. Заточка производится по передней поверхности.
Переточка фрез с затылованным зубом по передней поверхности уменьшает толщину зуба, а следовательно, и его прочность, что вызывает необходимость производить работу с меньшей подачей. Кроме того, фрезы имеют повышенное биение зубьев, а это ухудшает качество обработанной поверхности.
|
|
В настоящее время получили распространение фасонные фрезы с острозаточенным зубом. Они обеспечивают более спокойную (т. е. безударную) работу, чем фрезы с затылованным зубом, и имеют большее число зубьев. При переточке фрез по их фасонному профилю прочность остроконечного зуба не только не уменьшается, но даже увеличивается, так как высота его уменьшается.
Схема обработки кулачков фасонными фрезами приведена на рис. 5.7. Заготовки 2 закреплены на трех оправках 3, которые установлены в центрах трехшпиндельной делительной головки 4. Обработка ведется набором из трех фасонных фрез 1.
Фрезерование по разметке. Способ обработки фасонных поверхностей по разметке является малопроизводительным и неточным. Он применяется при изготовлении небольшого количества деталей. Работа производится чаще всего концевой фрезой преимущественно на вертикально-фрезерных станках при двух одновременно действующих ручных подачах. Величины этих подач должны быть такими, чтобы в результате одновременного их действия обрабатываемая поверхность получила заданную форму.
|
|
В ряде случаев удается усовершенствовать способ обработки фасонных поверхностей по разметке (рис. 5.8). На планке 2 размечается контур (например, штампа), который должен быть получен после фрезерования. Планка 2 устанавливается в вертикальном положении на плоскости заготовки 1. Размеченная сторона планки обращена в сторону фрезеровщика. На шпинделе 5 вертикально-фрезерного станка закрепляется указатель 4 в виде иглы, который показывает относительное перемещение заготовки 1 и шпинделя с фрезой 6. Правильность перемещений контролируют по разметочной риске 3, нанесенной на планку 2. Приспособление позволяет повысить производительность труда и точность обработки по разметке.
Обработка по копиру значительно повышает точность фасонного фрезерования. При обработке по копиру положение стола станка с деталью относительно оси фрезы при продольном и поперечном перемещениях стола ограничивается рабочей поверхностью копира. Схема обработки по копиру приведена на рис. 5.9. На обрабатываемую деталь 1, установленную в приспособлении 4, накладывают копир 2 с контуром, точно соответствующим контуру детали после обработки. Концевая фреза 3 кроме режущей имеет цилиндрическую часть диаметром, равным диаметру режущей части. Для воспроизведения по детали требуемого контура цилиндрическая часть фрезы должна находиться в процессе работы в контакте с поверхностью копира. Это достигается благодаря одновременному управлению вручную продольной и поперечной подачами стола.
|
|
При таком способе обработки фасонных поверхностей удается значительно уменьшить припуск на окончательную слесарную обработку контура детали.
При изготовлении небольшого количества деталей вместо копира используют одну из готовых деталей.
Обработка фасонных поверхностей с применением накладных копиров хотя и производительнее, чем по разметке, но все же утомительна для станочника, так как требует от него напряженного внимания и осуществления ручных подач. Поэтому в серийном производстве используют более совершенные схемы копирования на вертикально-фрезерных станках, снабженных специальными копировальными приспособлениями. Основным движением при фрезеровании по копиру является продольная подача стола или вращение круглого стола.
Схема фрезерования по копиру на станке с использованием круглого стола приведена на рис. 5.10. Заготовка детали 1 и копир 2 закреплены на круглом столе 3. В процессе фрезерования стол медленно вращается с помощью червячной передачи. Он установлен на салазках 4, которые могут перемещаться по направлению, указанному стрелкой К.Под действием груза 6 копир 2 всегда прижат к ролику 5, занимающему на станке неизменное положение. При вращении стола 3 копир с деталью также будет вращаться, а так как копир прижат к ролику, то в соответствии с контуром копира салазки 4 вместе с копиром и деталью получат дополнительное радиальное перемещение в ту или иную сторону. Благодаря этому фреза будет воспроизводить на детали требуемый контур.
|
|
На фрезерных станках моделей 6Н11, 6Н12 и 6Н13 для привода круглых столов в механизме передачи их имеется особый валик. На других моделях фрезерных станков передача может быть осуществлена от ходового винта стола.
Схема фрезерования незамкнутых контуров на продольно-фрезерных станках показана на рис. 5.11, а. Обрабатываемая деталь 8 и копир 2 закреплены на столе станка независимо друг от друга. На каретке 4, освобожденной от связи с ходовым винтом поперечной подачи, смонтированы копировальный шпиндель 5 с роликом 1 и фрезерная головка 6 с фрезой 7. Груз 3 обеспечивает постоянное прижатие копирного ролика 1 к копиру. При сообщении столу станка автоматической продольной подачи шпиндельная бабка будет получать поперечное перемещение, определяемое профилем копира. Поскольку расстояние М между осями ролика и фрезы остается постоянным (М = const), то эти оси будут описывать подобные кривые.
После переточки диаметр фрезы уменьшается. Если расстояние М оставить постоянным, то размеры детали увеличатся. Чтобы избежать этого, копирные ролики изготовляют коническими (рис. 5.11, б). В этих случаях для компенсации уменьшения диаметра фрезы на величину Δ d шпиндель с копирным роликом необходимо приподнять на величину h.
Обработка фасонных поверхностей на специальных станках. Внастоящее время станкостроительная промышленность выпускает специальные копировально-фрезерные станки со следящими системами, основанными на
электрических, гидравлических, гидропневматических и других принципах. В станках со следящими системами давление копировального щупа или ролика на копир значительно меньше, чем в системах с механической связью.
Большое распространение получили копировально-фрезерные станки с электрической системой.
Копировально-фрезерный полуавтомат мод. 6441Б имеет электрическую следящую систему. Станок предназначен для обработки пространственно-сложных форм (штампов, пресс-форм, металлических моделей и др.). Обработка на станке ведется по копиру или модели, изготовленным в масштабе 1:1. На станине 1 станка (рис. 5.12, а) расположен шпиндельный узел 2 со смонтированным на нем следящим устройством 3 и фрезерной головкой 4. Кроме того, на станине 1 установлен вертикальный стол 5, на котором закрепляются копир 6 и заготовка 7.
Шпиндельный узел 2 перемещается по направляющим вертикальной станины вверх и вниз и одновременно по горизонтальным направлениям вправо и влево. Вертикальный стол 5 передвигается только в продольном направлении.
Для осуществления объемной обработки фрезе необходимо сообщить три согласованных движения относительно заготовки. В данном случае фрезе сообщают вертикальное и поперечное движения, а столу — продольное. Все эти движения осуществляются с помощью отдельных регулируемых электродвигателей постоянного тока мощностью N = 0,37 кВт.
Обработка производится путем ощупывания копира копировальным пальцем 8 и синхронных движений фрезы 9. Палец 8 и фреза 9 смонтированы на общем корпусе фрезерной головки.
Схема электроконтактного следящего устройства представлена на рис. 5.12, б. Копирный палец 1, ощупывая профиль копира А, испытывает постоянное пульсирующее давление. Возникающие вследствие этого осевые перемещения передаются втулке 2 через подвешенный на пружине 4 груз 3 и якорю 5 датчика. При перемещении якоря 5 изменяются зазоры между якорем и сердечниками 6 и 7 трансформатора, а это, в свою очередь, приводит к изменению силы тока во вторичной обмотке трансформатора. После усиления электромагнитных импульсов они поступают в один из электродвигателей, который, вращая ходовой винт, перемещает фрезу 8 относительно обрабатываемой детали В в соответствии с профилем копира.
5.3. Обработка фасонных отверстий
Обработка внутренних фасонных поверхностей осуществляется фасонными инструментами или обычными с помощью копирных устройств.
Внутренние фасонные поверхности, так же как и наружные, образуются при помощи поворотных или поводковых приспособлений.
Поворотное приспособление для обработки сферической внутренней поверхности (рис. 5.13, а) устанавливается в центрах станка или в пиноли задней бабки. Приспособление имеет корпус-оправку 4, один конец которого вводится в предварительно обработанное отверстие детали 1 и опирается на передний центр, а второй закрепляется в пиноли задней бабки 7. Резец 2 устанавливается в державке 3, шарнирно закрепленной в передней части оправки 4. К державке привернута тяга 5, которая связана с колодкой б, расположенной на суппорте. При включении автоматической продольной подачи суппорта тяга 5 поворачивает державку 3 с резцом 2 вокруг ее оси, при этом резец перемещается таким образом, что его режущая кромка описывает радиус, величина которого определяется расстоянием от оси вращения державки до вершины резца.
|
Обработка сферической внутренней поверхности при помощи, поводкового приспособления приведена на рис. 5.13, б. Поводок 2 связывает верхнюю часть суппорта 3 с неподвижной осью 1. Расстояние между осями отверстия поводка равно R. Резец 4 растачивает сферическую поверхность 5 радиусом R при поперечной подаче суппорта. Криволинейное перемещение резца производится не вращением его вокруг оси, а путем параллельного перемещения.
Внутренние фасонные поверхности сложной формы растачиваются по копиру. При работе на станках токарной группы в большинстве случаев используются копирные устройства, аналогичные применяемым для обработки наружных фасонных поверхностей. Резец закрепляется непосредственно в резцедержателе станка или в консольной оправке. Так как при консольном закреплении резца трудно обеспечить необходимую жесткость технологической системы, то в этом случае обрабатывают фасонные отверстия с относительно небольшой длиной, при этом точность полученных отверстий невысокая. Для ее повышения необходимо уменьшать глубину резания, что приводит к большому числу операций (переходов). Часто по копиру осуществляют предварительную обработку, а фасонным инструментом — чистовую.
Лабораторная работа № 6
Тема: Абразивная обработка деталей машин
Задание и порядок выполнения работы:
1. Ознакомиться с инструкцией о выполнении работы.
2. Ознакомиться с теоретическими сведениями о способах и методах абразивной обработки деталей машин
3. Разработать технологический процесс абразивной обработки, с составлением всей необходимой технологической документации
4. Составить отчет о работе.
Содержание отчёта:
При составлении отчета необходимо:
I. Ознакомиться с краткими теоретическими сведениями по следующим вопросам:
1. Выбор абразивных материалов и инструментов
2. Круглое шлифование
3. Бесцентровое шлифование
4. Внутреннее шлифование
5. Плоское шлифование
II. Представить технологическую документацию необходимую для выполнения технологического процесса абразивной обработки одним из выбранных способов
III. Ответить на контрольные вопросы:
1. Чем характеризуются абразивные инструменты?
2. Какие материалы относят к естественным абразивным материалам?
3. Какие материалы относят к искусственным абразивным материалам?
4. Какой минерал состоит в основном из окиси алюминия?
5. Какие абразивные инструменты Вы знаете?
6. Назовите наиболее удобный способ шлифования валов.
7. Какой вид шлифования применяется при обработке относительно коротких участков на жёстких деталях?
8. Какой вид шлифования наиболее широко применяется в серийном производстве?
9. Какой вид шлифования применяют при обработке плоскостей и фасонных
линейных поверхностей?
10. Какого класса может достигать точность обработки деталей при шлифовании на бесцентрово-шлифовальных станках?
Литература:
Основная
1. Космачёв И. Г. Технология машиностроения. Лениздат, Ленинград – 1970, 400 с., ил.
Дополнительная
2. Антонов Л. П.и др. Практикум в учебных мастерских. Учеб. пособие для студентов пед. ин-тов по специальности «Общетехнические дисциплины и труд»-М.: «Просвещение»,1976.-400с. с ил.
3. Муравьёв Е. М. Технология обработки металлов: Учеб. пособие для учащихся 5 – 9 кл. общеобразоват. учреждений. - М.: Просвещение, 1995.-224 с., ил.
4. Муравьёв Е. М., Молодцов М. П.Практикум в учебных мастерских: Учеб. пособие для студентов пед. ин-тов по спец. № 2120 «Общетехнические дисциплины и труд» и учащихся пед. уч-щ по спец. № 2008 «Преподавание труда и черчения в неполной сред. шк.» В 2 ч. Ч.1. Обработка металлов /Под ред. Е. М. Муравьёва. - М.: «Просвещение», 1987.-272 с., ил.
Теоретические сведения
Введение
Процессы абразивной обработки получают всё более широкое распространение. Это объясняется внедрением в промышленность труднообрабатываемых сталей и сплавов, новых методов получения заготовок с минимальными припусками, рассчитанными в большинстве случаев только на абразивную обработку, и с возросшими требованиями к точности деталей и качеству поверхностей.
Появление новых типов шлифовальных станков и новых абразивных материалов – синтетических алмазов, кубического нитрида бора, хлористого электрокорунда и др. – дало возможность широко использовать абразивную обработку не только на чистовых, но и на подготовительных (резка) и черновых операциях.
Выбор абразивных материалов.
Абразивные инструменты характеризуются видом ма-
териала, зернистостью, связкой, твердостью, структурой, формой и размерами.
Абразивные материалы. Абразивные материалы делятся на естественные и искусственные. К естественным относятся кварц, наж-
дак, корунд и алмаз, а к искусственным — электроко-
рунд, карбид кремния, карбид бора, кубический нитрид бора и синтетические алмазы.
Естественные материалы. Кварц (Н) — эго минерал, состоящий в основном из кристаллического кремнезема (98,5 — 99,5% А1203) . Одна из разновидно-
стей кварца — кварцевый песок белого, желтого и дру-
гих цветов. Применяется он для изготовления шли-
фовальных шкурок на бумажной и тканевой ос-
новах и в виде шлифовальных зерен в свободном состоянии.
Наждак (Н) — мелкокристаллическая окись алюми-
ния (25 — 60% А1203). Используется для изготовления наждачного полотна и брусков для заточки режущего инструмента.
Корунд (Е и ЕСБ) — минерал, состоящий в основном из кристаллической окиси алюминия (80 — 95% А1203). Зерна корунда очень тверды и при разрушении обра-
зуют раковистый излом с острыми гранями. Естествен-
ный корунд имеет ограниченное применение. Исполь-
зуется он главным образом в виде порошков и паст для доводочных операций.
Алмаз (А) — минерал, представляющий собой чистый углерод. Имеет самую высокую твердость из всех из-
вестных в природе веществ. Алмаз встречается в виде
небольших кристаллов различной формы. Из кристаллов и их осколков изготовляют лезвийные режущие инстру-
менты и алмазно-металлические карандаши для правки
шлифовальных кругов.
Искусственные материалы применяются в промышленности наиболее широко. Благодаря высокой твердости, большой однородности состава и другим цен-
ным свойствам они являются основным материалом для изготовления различных видов абразивных инструмен-
тов.
Электрокорунд нормальный (Э) представляет собой
корунд, получаемый путем плавки из шихты, составлен-
ной из естественных пород. В зависимости от содержа-
ния кристаллической окиси алюминия электрокорунд
нормальный выпускают следующих марок: Э91, Э93 и
Э95 (цифра показывает содержание А203).
Легирование абразивного зерна окислами титана
(ЭБТ) и хрома (ЭБХ) повышает режущую способность
абразивного инструмента. Из электрокорунда нормаль-
ного изготовляют абразивные инструменты и порошки.
Электрокорунд белый (ЭБ) получают при плавке в
электрических печах технического глинозема. В электро-
корунде белом содержится 96 – 99 % окиси алюминия.
В зависимости от содержания Аl2О3 электрокорунд
белье выпускают двух марок: ЭБ9, содержащий
в зерне X 40 не менее 98,5% А12О3 и не более 0,15%
Fe2О3, и ЭБ8, содержащий в зерне № 40 не менее 96,5%
А2О3 и не более 0,5% Fe2О3
Монокорунд (М) — одна из разновидностей электро-
корунда — содержит до 97% кристаллической окиси
алюминия А1203 и отличается высокими режущими свой-
ствами и прочностью.
Карбид кремния — химическое соединение кремния
с yглеродом — обладает большой твердостью и хрупко-
стью, чем элсктрокорунд. Карбид кремния бывает зеле-
ный (КЗ), имеющий цвет от светло- до темно-зеленого,
и черный (КЧ) — обычного черного и темно-синего
цвета.
Карбид кремния выпускается следующих марок: кар-
бид кремния зеленый — шлифзерно К39 и К38, шлиф-
порошки К37 и К36 и микропорошки К36; карбид крем-
ния черный — шлифзерно КЧ8 и КЧ7 и шлифпорошки КЧ-17 и КЧ5,
Цифры в маркировке показывают содержание SiC
в процентах. Например, марка КЗ9 означает: карбид
кремния зеленый с содержанием SiC около 99 %.
Карбид бора представляет собой соединение бора
с углеродом. Получают его из технической борной кис-
лоты и нефтяного кокса в электрических печах. Исполь-
зуется он в виде порошков и паст для доводки твердых
материалов.
Кубический нитрид бора (КНБ) — новый твердый
материал, представляющий собой соединение бора, кремния и углерода. По своим физико-механическим
свойствам КНБ не уступает алмазам, но имеет более
высокую температурную стойкость. Применяется для из-
готовления шлифовальных кругов для шлифования и
доводки инструментов из быстрорежущей (высокована-
диевой и кобальтовой) стали.
Искусственные (синтетические) алмазы (АС) ши-
роко используются в промышленности. Они имеют то
же строение, что и естественные. Физико-механические
свойства синтетических алмазов высоких сортов тожде-
ственны свойствам природных алмазов.
Синтетические алмазы выпускают трех марок;
АСО — алмаз синтетический обычной прочности, пред-
назначенный для изготовления инструментов на органи-
ческой связке, а также паст и порошков; АСП — повы-
шенной прочности для инструментов на металлической
и керамической связках; АСВ — высокой прочности для
инструментов на металлической связке, работающих
при высоких удельных нагрузках.
Зернистость характеризует крупность зерен аб-
разивных материалов — их линейный размер. Обозначе-
ния зернистости абразивных порошков (по ГОСТ
9206-59) и природных алмазных порошков (по ГОСТ
3647-59) приведены в табл. 6.1. Цифры, следующие
за буквой А, означают размер основной фракции.
Вёрхний предел размера зерна соответствует раз-
меру ячейки сита (в микронах), сквозь которое
зерно основной фракции проходит, а нижний пре-
дел — ячейки сита, на котором зерно основной фракции
задерживается.
Твёрдость. Абразивные материалы должны иметь
более высокую твердость, чем обрабатываемый мате-
риал.
Твердость минералов определяется различными ме-
тодами. Один из них основан на принципе царапания:
царапающее тело должно быть более твердым, а цара-
паемое — более мягким. Взяв несколько кристаллов ми-
нералов, путем царапания одного другим можно уста-
новить их относительную твердость.
Более точно установить твердость абразивного мате-
риала можно методом вдавливания в него алмазной
пирамиды с углом 136о. В этом случае микротвердость
определяется на приборах ПМТ-2 или ПМТ-З.
Таблица 6.1
Обозначение зернистости абразивных материалов
Наименование групп | Обозначение зернистости | Обозначение зернистости в дюймовой системе, в мешах | Размер зерен основной фракции, в мкм | |
природных алмазных порошков (ГОСТ 3647-59) | абразивных порошков (ГОСТ 9206-59) | |||
Шлифзерно | - - - - - - А50 А40 А32 А25 А20 А16 | 200 160 125 100 80 63 50 40 32 25 20 16 | 10 12 16 20 24 30 36 46 54 60 70 80 | 2500-2000 2000-1600 1600-1250 1250-1000 1000-800 800-630 630-500 500-400 400-315 315-250 250-200 200-160 |
Шлифпорошки | А12 А10 А8 А6 А5 А4 | 12 10 8 6 5 4 | 100 120 150 180 230 280 | 160-125 125-100 100-80 80-63 63-50 50-40 |
Микропорошки | АМ40 АМ28 АМ20 АМ14 АМ10 АМ7 АМ5 АМ3 АМ1 | М40 М28 М20 М14 М10 М7 М5 М3 М1 | М40 М28 М20 М14 М10 М7 М5 М3 М1 | 40-28 28-20 20-14 14-10 10-7 7-5 5-3 5-3 мельче 1 |
Величина микротвёрдости (в кг/мм2) некоторых аб-
разивные материалов составляет:
алмаза природного……………………………..10 060
алмаза синтетического…………………………10 100
кубического нитрида бора……………………..10 100
карбида бора ………………………………3700 — 4300
карбида кремния…………………………..2300 — 3500
монокорунда………………………………2 100 — 2 300
электрокорунда белого…………………...2 300 — 2 400
электрокорунда нормального……………2 000 — 2200
Абразивный инструмент делится па следующие виды:
шлифовальные круги общего и специального назначения, алмазные круги, шлифовальные и алмазные головки
и шлифовальные и алмазные сегменты.
Шлифовальные круги и характеризуются фор-
мой и геометрическими размерами, видом абразивного
материала и его зернистостью, видом связки, твердостью
и структурой.
Форма и размеры круга выбираются в зависимости
от конструкции станка и обрабатываемой детали. Рекомендуется применять круги возможно больших диамет-
ров. Исключения составляют отверстия, для обработки
которых требуются круги определенных размеров.
Абразивные шлифовальные круги изготавливают на
керамической, силикатной, бакелитовой, вулканитовой и
шеллаковой связках. Круги на шеллаковой связке при-
меняют редко, их заменяют инструментами на бакелито-
вой или вулканитовой связке.
Выбор круга по связке производят в зависимости от
способа и вида обработки, допускаемых окружных ско-
ростей, механической прочности круга и т. п.
Твердостью шлифовального круга принято называть
сопротивление связки вырыванию зерен. Получение раз-
личной твердости круга при одних и тех же номерах
зерна и структуры достигается изменением количества
связки.
Для облегчения подбора круга по твердости ГОСТ
3751-47 предусматривает шкалу степеней твердости
(табл. 6.2).
Под структурой понимают строение абразивного ин-
струмента, характеризуемое количественным соотноше-
нием объема абразивных зерен, связки и пор. Различают три
Таблица 6.2
Твёрдость абразивного инструмента
Степень твёрдости | Подразделение твёрдости | Вид связки | Область применения |
Мягкий (М) | М1, М2, М3 | К | Обработка минералокерамических и твердосплавных инструментов |
Среднемягкий (СМ) | СМ1, СМ2 | Обработка твердосплавных инструментов | |
Средний (С) | С1, С2 | В | Обработка быстрорежущих инструментов |
Среднетвёрдый (СТ) | СТ1, СТ2, СТ3 | Обработка конструкционной стали | |
Твёрдый (Т) | Т1,Т2 | ||
Весьма твёрдый (ВТ) | ВТ1, ВТ2 | Б | Правка кругов |
Чрезвычайно твёрдый (ЧТ) | ЧТ1, ЧТ2 | ||
Примечание. Цифры 1, 2 и 3 характеризуют твёрдость в порядке её возрастания |
группы структур: структуры № 1-5 называют закрытыми, или плотными, № 6-10 – средниим и № 11-18 – открытыми.
Для заточки режущего инструмента присменяюит круги со средними или открытыми структурами, така как при этом облегчается удаление стружки из зоны резания и уменьшается возможность образования дефектов на затачиваемом инструменте.
Круги со структурами № 1-5 изготавливают на бакелитовой связке, а со структурами № 6-18 – на керамической.
Чтобы правильно выбрать круг, необходимознать
его характеристику. Эта характеристика в виде услов-
ных обозначений (маркировки) наносится несмываемой
краской на поверхность круга. Абразивный круг с такой
маркировкой, которая, по существу, является паспор-
том абразивного инструмента, показан на рис. 6.1.
В целях единообразия все условные обозначения
в маркировке располагают в следующем порядке:
1) одной или двумя буквами обозначается наимено-
вание абразивного материала, а следующей за ними
цифрой указывается маркировка абразива. На рис. 6.1 ЭБ — электрокорунд белый, а цифра 8 — его марки-
ровка;
2) следующие две (например, 40) или три цифры
обозначают зернистость;
3) буквы с индексом 1, 2 или 3 (СМ2) — твердость;
4) следующая буква (К) — материал связки;
5) последняя цифра (6) — структуру.
Кроме того, проставляется завод-изготовитель (ЧАЗ),
форма (ПП) и основные размеры круга (450X63Х12,7).
На кругах для скоростного шлифования (vкр
= 50 м/сек) дополнительно наносят красную полосу или
надпись «скоростной», а на кругах для внутреннего
шлифования с окружной скоростью vср = 65 м/сек — две
красные полосы. На высокопористых кругах делают дополнительные обозначения зернистости наполнителя.
Алмазные круги. Алмазный круг (рис. 6.2)
состоит из корпуса 1 и алмазоносного слоя 2. Корпус
изготовляют из дюралюминия или пластмассы, алмазо-
носный слой — из алмазного порошка, связки и испол-
нителя.
Алмазные круги характеризуются зернистостью, ви-
дом связки и концентрацией алмаза.
Наиболее распространённые связки алмазных кру-
гов — металлическая и бакелитовая (органическая).
Промышленность выпускает круги на металлических
металлических ммм связках марок М1, МИ, МК, М5 и др.
Основой является связка М1, состоящая из 80% меди
и 20% олова. Круги на этой связке выпускает большинство заводов. Разновидностями её являются связки МИ
и МК.
Круги на металлических связках служат для образования стружколомательных канавок, а также для
предварнтсльной заточки твёрдосплавных инструментов.
Изготавливают круги на бакелитовых связках Б1, Б2,
БЗ и Б4. Наиболее распространены круги на связках
Б1 и Б2, их выпускают многие заводы. В связке Б1
наполнителем является карбид бора (29,3%), а в связке Б2 — желелезо (56,5%)
Круги на бакелитовых связках применяют на операциях чистового шлифования и доводки инструментов.
Промышленность выпускает алмазные круги на керамической связке К1, К2
и КЗ. Эти круги обладают высокими режущими свойствами и применяются преимущественно для обработки
инструментов из быстрорежущей стали. Кроме того,
их можно использовать для одновременной заточки твердосплавной пластины и стальной державки.
По количеству алмазного порошка, содержащегося в 1 мм3 алмазного слоя, определяют концентрацию круга. За 100% - ную концентрацию принято
содержание 0,878 мг алмаза в 1 мм3 алмазоносного слоя.
Концентрация круга должна соответствовать связке
и характеру выполняемой операции. Круги на металли-
ческих связках бывают только 100%-ной концентрации,
а на бакелитовых — различной концентрации.
Для большинства операций шлифования и доводки наиболее универсальными являются алмазные круги на
металлической связке со 100%-ной концентрацией и на
органической связке с 50%-ной концентрацией.
Крупнозернистые (АС25 — АС12) круги на металлической и органической связках изготовляют со 100%-ной
концентрацией.
Для заточки резцов малого сечения и доводки фасонных деталей рекомендуется применять круги со
100% -ной концентрацией.
Форма и типоразмеры алмазных кругов определяются
ГОСТом и нормалями НИИ алмаза.
Круги специальной формы изготовляются по особым
заказам. В маркировке алмазного круга указываются
основные данные, характеризующие круг.
Например, маркировка АЧК125Х10ХЗХ32-АС012--
Б1-50-24-1200-2006-ТЗАИ обозначает: ИК — тип круга
(алмазный чашечный конический); 125 — его наружный
диаметр, в мм; 10 — ширина алмазоносного слоя, в мч; 3 — толщина алмазоносного слоя, в мм; 32 — диаметр
посадочного отверстия, в мм, АСО — вид алмаза (син-
тетический обычной прочности; 12 — зернистость; Б1--
связка (бакелитовая); 50 — концентрация, в %, 24-
содержание алмаза в алмазоносном слов, в каратах; 1200 — номер круга; 2006 — год его изготовления;
ТЗАИ — завод-изготовитель (Томилинский завод алмаз-
ных инструментов).
Круглое шлифование
Шлифование является основным методом чистовой
обработки наружных цилиндрических поверхностей.
Применяют следующие виды шлифования: обдирочное, точное, которое может быть предварительным и чистовым, и тонкое. Наиболее распространенным является
точное шлифование, при котором точность обработки
достигает 2-го класса, а шероховатость поверхности -
7 — 9-го классов.
Имеется несколько способов шлифования наружных
цилиндрических поверхностей: продольное шлифование осуществляется за несколько
продольных проходов с подачей на глубину на двойной
(или каждый) проход; глубинное шлифование — за один проход кругом,
установленным на глубину; врезное шлифование — с поперечной подачей на всю
ширину обработки — периодической или непрерывной
в радиальном или тангенциальном направлении; шлифование последовательными врезаниями — с радиальной подачей уступами; комбинированное шлифование.
Продольное шлифование. Продольное шлифование (рис. 6.3, а) — наиболее распространенный и удобный способ шлифования валов. В зависимости от конструкции станка обрабатываемая деталь 2 или круг 1 получает поступательно-возвратное движение (продольнаяподача) вдоль своей оси, при этом после каждого продольного хода осуществляется поперечная подача шлифовального круга. При предварительном шлифовании продольная подача составляет 0,5 — 0,8 высоты круга на один оборот детали, при окончательном — 0,2 — 0,5 высоты круга. Соответственно поперечная подача sп.п или
глубина резания, составляет 0,02 — 0,06 и 0,005 — 0,02 мм за один проход. В конце шлифования обычно производится несколько проходов без поперечной подачи — до прекращения искрения.
Глубинное шлифование. Глубинное шлифование (рис. 6.3, б) осуществляется при обработке относительно коротких участков на жест-ких деталях. При глубинном шлифовании весь или почти весь припуск снимают за один проход с малой продоль-ной подачей (sпр=2—10 мм/об. д). По окончании прохода шлифовальный круг возвращается в исходное положение. Заправку круга производят на конус или ступенчатую.
Врезное шлифование. Врезное шлифование (рис. 6.3, в) осуществляется широкими кругами сразу по всей длине обрабатываемой поверхности. Работа производится только с поперечной подачей, которая непрерывно или периодически на один оборот детали осуществляется шлифовальным кругом автоматически или вручную и составляет 0,02 — 0,010 мм на один оборот детали. В отдельных случаях кругу сообщается дополнительное осевое колебательное движение с небольшой амплитудой (до 3 мм), так называемое осциллирующее движение.
Врезное шлифование широко используется в крупно-серийном и массовом производстве для шлифования шеек коленчатых валов, кулачковых и ступенчатых валов и других цилиндрических, конических и фасонных поверхностей вращения длиной 200 — 300 мм. Это один из наиболее производительных способов шлифования.
Осуществляется одновременное шлифование нескольких поверхностей одним широким специально заправленным кругом либо несколькими шлифовальными кругами, установленными рядом на одном шпинделе. При-меры обработки нескольких поверхностей одним широким кругом приведены на рис. 6.4, а и б; двумя проти-воположно расположенными кругами — на рис. 6.4, б; тремя кругами, размещенными с одной стороны дета-ли,— на рис. 6.4, в.
Шлифование уступами (Рис. 3, г) осуществляется в серийном производстве при обработке жёстких деталей. По этой схеме поверхность детали шлифуют определёнными участками (1, 2, 3, 4 и 5) с поперечной подачей последовательно друг за другом с перекрытием соседнего участка на 5-15 мм.
Комбинированное шлифование.При шлифовании уступами (Рис. 6.3, д) на границах соседних участков получается небольшая ступенчатость. Для достижения требуемой точности и чистоты шлифование этим способом производят не на окончательный размер, а как предварительное. Оставшийся припуск 0,02 – 0,03 мм удаляют в той же операции двумя – тремя продольными проходами.
Оборудование и приспособления. Наружное шлифование цилиндрических, конических, фасонных и торцевых поверхностей осуществляют на круглошлифовальных станках. При обработке детали устанавливаются в центры или закрепляются в патроне. Поджим детали задним центром производится пружиной. Обработка в центрах производится при вращении шпинделя круга и обрабатываемой детали, непрерывной или периодической подаче на глубину и продольном перемещении стола. При автоматизации цикла шлифования дополнительно требуется быстрый подвод и отвод шлифовальной бабки, и отвод пиноли задней бабки.
Схемы шлифования на круглошлифовальных станках приведены на рис. 6.5. Круглошлифовальных станки разделяются на универсальные, неуниверсальные, врезные и специальные. Универсальные станки отличаются от неуниверсальных тем, что они имеют поворотные бабки детали или круга, позволяющие вести обработку конических поверхностей с большим углом конусности (рис. 6.5, а). Некоторые модели станков имеют дополнительные бабки для шлифования отверстий.
На неуниверсальных станках (рис. 6.5, б) можно шлифовать пологие конуса с углом наклона образующей к оси не выше 7о путём поворота подачи.
Произвольность станков, работающих методом врезания (рис. 6.5, в), значительно выше, чем работающих методом продольной подачи.
К группе специальных относятся станки для шлифования коленчатых валов, кулачковых валов автомобильных двигателей, дорожек качения у внутренних колец роликовых подшипников и др.
На центровых круглошлифовальных станках деталь устанавливается в неподвижных центрах. Форма и раз-меры центровых отверстий регламентированы ГОСТом.
Как правило, центровые отверстия смазывается. При обработке тяжелых деталей в качестве смазки применяют свинцовые белила, разведенные в индустриальном масле 30 или 45В. Эффективна также смазка, состоящая из 65% солидола, 25% мела, 5% серы и 5% графита.
При длительном шлифовании тяжелых деталей для обеспечения подачи смазки без снятия детали с центров рекомендуется пользоваться специальными центрами со смазочными канавками. При скоростном шлифовании используют центра, оснащенные твердым сплавом.
Передача вращения детали от поводковой планшайбы станка производится при помощи различных устройств. Самым обычным из них является винтовой хомутик.
Детали, имеющие отверстия больших диаметров, укрепляют на оправках с центровыми отверстиями для установки в центра станка.
Длинные и точные детали шлифуют с помощью люнетов.
Скоростное шлифование. Шлифование на повышенных режимах резания осуществляют специальными скоростными кругами, обеспечивающими безопасную работу при скоростях до 50 м/сек Станок должен быть жест-ким, чтобы при обработке исключались вибрации как круга, так и детали.
Повышение скорости резания при сохранении неизменными подач и глубины резания улучшает чистоту обработанной поверхности уменьшает количество снимаемого металла каждым работающим абразивным зерном в единицу времени и, следовательно, уменьшает износ круга. Повышение скорости резания при одновременном изменении остальных параметров режима реза-ния увеличивает производительность обработки.
Так, например, при увеличении скорости резания (без изменения остальных параметров режима резания) с 30 — 35 до 50 м/сек на 50% уменьшается износ круга и улучшается чистота поверхности, удельная производи-тельность круга повышается на 10 — 15%, а потребляе-мая мощность — на 20 — 30%.
При увеличении скорости резания до максимального значения и изменении подач машинное время обработки сокращается на 40 — 70%, расход круга на единицу об-работанной детали уменьшается на 30% и, кроме того, улучшается чистота обрабатываемой поверхности.
Одним из способов повышения скорости при шлифовании, является уста-новка шлифовального круга в прочное металлическое кольцо, охватывающее его по периферии. Рабочей по-верхностью круга в этом случае является внутренняя поверхность отверстия, а не наружная, как при обыч-ном круглом шлифовании. Этот способ, условно назван-ный охватывающим, позволяет осуществлять шлифование стандартными кругами со скоростью до 125 м/сек. При охватывающем шлифовании в резании участвует в 2,4 — 4,5 раза больше абразивных зерен, чем при обыч-ном круглом шлифовании, во столько же раз увеличи-вается и суммарное сечение среза металла, что значи-тельно повышает производительность процесса.
При шлифовании этим способом колец подшипников со скоростью резания 90—100 м/сек шероховатость по-верхности достигает 9—10-го классов чистоты.
Шлифование на повышенных режимах производят кругами прямого профиля, изготовленными из электрокорунда нормального, электрокорунда белого, реже -из монокорунда и еще реже — из карбида кремния зеле-ного или черного. Зернистость скоростных кругов — 40 и мельче; твердость — от среднемягких до твердых. Круги выполнены на керамических и органических связках.
Скоростное шлифование на круглошлифовальных стан-ках с автоматическим или полуавтоматическим циклом работы незакаленных сталей осуществляет кругами ЭБ40С1-С2К, а закаленных — кругами ЭБ40СМ1-СМ2К.
Бесцентровое шлифование
Бесцентровое шлифование применяют для обработки деталей, не имеющих центровых отверстий.
При шлифовании на бесцентрово-шлифовальных станках в зависимости от режимов резания и характери-стики круга точность обработ-ки может достигать 2-го клас-са, а шероховатость поверх-ности — 7—10-го классов чистоты. При бесцентровом шлифо-вании обрабатываемая деталь 2 (рис. 6.6) находится в кон-такте с опорным ножом 3, шлифовальным 1 и ведущим 4 кругами. -
Oбa круга вращаются в одном направлении с разными окружными скоростями. Ско-рость ведущего круга, как правило, равна 25 — 30 м/сек, а шлифовального — 30 — 35 м/сек, т. е. в 60-100 раз больше, чем ведущего.
Обрабатываемая деталь, расположенная между кру-гами и опирающаяся на поверхность ножа, вращается примерно со скоростью ведущего круга за счет сил тре-ния между деталью и кругами. В связи со значительной разницей в скоростях вращения кругов трение между деталью и ведущим кругом больше, чем между деталью и шлифующим кругом. Так как на бесцентрово-шлифо-вальных станках применяют ведущий круг на вулкани-товой связке, то и коэффициент трения между ним и деталью выше, чем между шлифующим и деталью, и при обработке стальных деталей достигает 0,6 — 0,8.
Рис. 6.7. Способы подач на бесцентровых шлифовальных станках
Вследствие разности скоростей вращения шлифую-щего круга и детали и осуществляется процесс шлифо-вания.
Обработка деталей на бесцентрово-шлифовальных станках производится способами продольной подачи (на проход) (рис. 6.7, а), поперечной подачи (врезное шли-фование) (рис. 6.7, б) и до упора (рис. 6.7, в).
Способом продольных подач шлифуют гладкие дета-ли различной длины. В этом случае шлифующий 1 и ведущий 4 круги (рис. 6.7, а и 6.8, а) находятся на по-стоянном расстоянии друг от друга. Деталь 2 устанав-ливается на нож 3. Продольная подача осуществляется ведущим кругом 4 либо путем поворота его на опреде-ленный угол α, либо вследствие наклона опорного ножа 3 (рис. 6.8, б). Скорость продольной подачи определяется скоростью вращения ведущего круга и углом поворота этого круга или наклона ножа.
Из схемы подач (см. рис. 6.8) видно, что окружная скорость детали будет составлять:
vд= v cos α м/мин,
а скорость продольной подачи:
sпр=v sin α м/мин
где v – скорость ведущего круга, в м/мин;
α – угол поворота ведущего круга или наклона опорного ножа, в град.
Рис. 6.8. Схема продольных подач
Так как наибольший угол поворота α = 6о, а косинус этого угла составляет 0,9945, то практически скорость вращения детали равна скорости вращения ведущего круга, т. е.
vд ≈ v м/мин
При врезном шлифовании (см. рис. 6.7, б) деталь 2, опирающаяся на нож 8, только вращается, а подача на глубину производится перемещением ведущего 4 и шлифующего 1 кругов перпендикулярно к оси детали на величину припуска. После окончания шлифования ведущий круг вместе с ножом и деталью отводится от шлифующего и осуществляется смена детали.
Шлифование врезным способом ведется с различными величинами поперечных подач. Вначале большая часть припуска удаляется на повышенной подаче, а к
концу процесса подача снижается. На последних оборотах шлифование производится совсем без подачи (выхаживанием), чем и достигается хорошее качество обработанной поверхности.
При врезном шлифовании ведущий круг или направ-
ляющая линейка располагается параллельно оси шли-
фовального круга или же с небольшим наклоном (в пре
делах Оо30' — 1о) для более надежного прижима торца
детали к упору 5 (см. рис. 6.7, б).
Шлифование до упора является промежуточным меж-
ду продольным и врезным. Этим способом обрабатывают
детали с поверхностями, ограничивающими прохожде-
ние детали между кругами (болты, клапаны со стеблем и тарелкой, ступенчатые валики и т. п.).
Рис. 6.9. Схема бесцентрово-шлифовальных станков
При подходе детали к упору 5 (см. рис. 6.7, в) ка-
ретка суппорта и ведущий круг 8 отводятся от шлифую-
щего круга 1, и деталь 2 удаляется из рабочей зоны при
помощи выталкивателя 4.
Наружное бесцентровое шлифование производится на
универсальных станках и специальных, которые отлича-
ются от обычных расположением линии центров кругов,
способами осуществления подач и конструкцией механиз-
мов правки кругов.
Бесцентрово-шлифовальные станки бывают с гори-
зонтальным расположением линии центров (рис. 6.9, а),
характерным для большинства станков малых и сред-
них моделей, и с наклонным расположением линии цент-
ров (рис. 6.9, б), характерным для крупных станков,
предназначенных для чернового шлифования крупно-
габаритных деталей.
Поперечные подачи и настройка на заданный размер
осуществляется следующими способами:
перемещением ведущего круга и суппорта с опорным
ножом относительно неподвижно закрепленной на станке
шлифовальной бабки (модели 3180, 3182, 3183 и 3188);
перемещением шлифующего и ведущего кругов отно-
сительно неподвижно закрепленного на станке суппорта
с опорным ножом (модели 3А180, ЗА182 и ЗБ180);
перемещением обрабатываемой детали в сторону
шлифовального круга ведущим кругом, рабочая поверх-
ность которого выполнена по архимедовой спирали; весь
цикл шлифования происходит здесь за один оборот ве-
дущего круга.
Выбор шлифовальных кругов при бесцентровой обра-
ботке, как и при других способах шлифования, осуществ-
ляется в зависимости от вида операции (предваритель-
ная или чистовая), обрабатываемого материала и т. п.
В качестве ведущих используются шлифовальные
круги из электрокорунда на вулканитовой связке харак-
теристики Э (16 — 12) (СТ — Т) В. Для шлифования де-
талей диаметром до 15 мм применяются чугунные или
дюралюминиевые ролики. Металлические ведущие ро-
лики правятся твердосплавными резцами.
При назначении режимов шлифования надо стремить-
ся к наиболее полному использованию мощности станка.
Интенсивность съема металла Q определяется следую-
щим уравнением:
Q = vsо t= ndst,
где v — скорость вращения детали, в м/мин;
sо — продольная подача на один оборот детали, в мм/об (sо= );
t — глубина шлифования, в мм, определяемая по-
ловиной величины подачи на глубину по лимбу
станка;
d — диаметр шлифуемой поверхности, в мм;
s — продольная подача, в м/мин;
n — число оборотов детали в минуту.
При первых проходах, когда шлифование произво-
дится при больших значениях s и t, интенсивность съема
металла наивысшая: снимается 70 — 80% общего при-
пуска.
При назначении режимов бесцентрового шлифования
определяются следующие параметры: для сквозного шлифования с продольной подачей -
подача на глубину шлифования 2t, в мм, за один
проход на диаметр детали; число проходов i детали; скорость вращения детали v, в м/мин; угол поворота ведущего круга α, в град.; минутная продольная подача детали s, в мм/мин; для врезного шлифования с поперечной подачей – величина припуска 2t, снимаемого за операцию, на диаметр детали v, в м/мин; минутная поперечная подача sпоп, в мм/мин, на этом этапе врезная; время Твых и снимаемый слой 2t вых на этапе выхаживания детали.
Ориентировочные данные для установления режимов шлифования деталей способом продольной подачи на одном станке приведены в таблице 6.3.
При многопроходной обработке деталей на одном
станке шлифующий круг для всех переходов остается
одним и тем же. Варьирование режимов шлифования осуществляется
осуществляется пппппп только изменением числа оборотов ве-
дущего круга.
Внутреннее шлифование
Внутреннее шлифование является одним из основ-
ных способов обработки отверстий, при котором может
быть достигнута точность обработки по 1 — 3-му классам
и шероховатости поверхности по 7 — 9-му классам чи-
стоты. Оно используется во всех типах производства, а
также в поточно-массовом производстве и на автомати-
ческих поточных линиях.
Внутреннее шлифование применяют при обработке
цилиндрических и конических, сквозных и глухих отвер-
стий в деталях, изготовленных из незакаленной и зака-
лённой стали, чугуна, цветных металлов и неметалличе-
ских материалов.
Чаще всего оно осуществляется при обработке точных
отверстий в закаленных деталях или в деталях из высо-
котвердыx и труднообрабатываемых материалов, а также-
же точных отверстий с пересеченной поверхностью, на-
пример, с выточкой, со шпоночными и шлицевыми паза-
ми, диаметром свыше 100 мм, когда развертывание не-
т возможно, отверстий 2-го класса точности и выше.
Особенностью внутреннего шлифования и его досто-
инством является возможность исправления направления
оси отверстия при ее уводе на предшествующих опера-
циях, а также обеспечение перпендикулярности торцо-
вой поверхности к оси отверстия при шлифовании от-
верстия и торца с одной установки. Однако особенности
этого способа обработки отверстий создают и ряд ограничений для его использования. К ним относятся: зависимость диаметра шлифовального круга от диаметра обрабатываемого отверстия детали;
недостаточная жесткость шпинделя, несущего шлифовальный круг.
Современные внутришлифовальные станки позволяют
обрабатывать отверстия диаметром от 5 мм, а в некоторых случаях — и от 1 мм. Эти станки подразделяются на
патронные, планетарные и бесцентровые.
Патронные станки получили наибольшее распространение и служат для шлифования отверстий в деталях средних размеров, которые удобно закреплять в патроне станка. На этих станках можно шлифовать торцы деталей, а при наличии поворотной передней бабки — и конические отверстия.
Диаметр детали, в мм | Элементы режима шлифования | Многопроходное шлифование на одном станке | |||||
Предварительное (черновое) | Окончательное (чистовое) | ||||||
Подача на глубину 2t, мм | Класс точности | ||||||
0,10-0,20 | 0,20-0,35 | 0,35-0,50 | 1 | 2 | 2а-3 | ||
10 | s | 3800 | 3500 | 2500 | 1600 | 1800 | 2000 |
v | Устанавливаются по уровню окончательного прохода | 60-45 | 50-40 | 45-37 | |||
α | 1о30'-2о | 2о-2о30' | 2о30'-3о | ||||
i | 1 | 1 | 1 | 3 | 3 | 2 | |
15 | s | 3600 | 2600 | 1900 | 1300 | 1700 | 1800 |
v | Устанавливаются по уровню окончательного прохода | 50-37 | 48-38 | 40-34 | |||
α | 1о30'-2о | 2о-2о30' | 2о30'-3о | ||||
i | 1 | 1 | 1 | 3 | 3 | 2 | |
25 | s | 3000 | 1850 | 1300 | 1200 | 1500 | 1700 |
v | Устанавливаются по уровню окончательного прохода | 45-34 | 43-34 | 39-32 | |||
α | 1о30'-2о | 2о-2о30' | 2о30'-3о | ||||
i | 1 | 1 | 1 | 4 | 4 | 3 | |
40 | s | 2900 | 1500 | 1000 | 1100 | 1300 | 1500 |
v | Устанавливаются по уровню окончательного прохода | 42-31 | 37-29 | 35-29 | |||
α | 1о30'-2о | 2о-2о30' | 2о30'-3о | ||||
i | 1 | 1 | 1 | 5 | 5 | 4 | |
60 | s | 2200 | 1200 | 750 | 1000 | 1200 | 1300 |
v | Устанавливаются по уровню окончательного прохода | 38-28 | 34-27 | 30-25 | |||
α | 1о30'-2о | 2о-2о30' | 2о30'-3о | ||||
i | 1 | 1 | 1 | 5 | 5 | 4 | |
80 | s | 1600 | 800 | 500 | 800 | 1000 | 1200 |
v | Устанавливаются по уровню окончательного прохода | 30-23 | 28-23 | 27-23 | |||
α | 1о30'-2о | 2о-2о30' | 2о30'-3о | ||||
i | 1 | 1 | 1 | 5 | 5 | 4 |
Таблица 6.3
На патронных станках внутренние поверхности, так же как и наружные, могут обрабатываться с продольной или поперечной подачей. Схема шлифования продольными подачами приведена на рис. 6.10, а, а поперечными — на рис. 6.10, б. Главное движение (скорость резания) в этих станках — вращение шлифовального круга.
Рис. 6.10. Схемы шлифования внутренних поверхностей
Скорость резания определяется по формуле:
vк= (м/сек),
где Dк — диаметр круга, в мм;
nк — число оборотов круга в минуту.
Круговая подача о, осуществляется вращением заготовки со скоростью
v3= ; м/мин
где D3— диаметр отверстия заготовки, в мм;
n3 — число оборотов заготовки в минуту.
Скорость вращения заготовки выбирается в зависимости от обрабатываемого материала и назначения операции. Обычно она находится в пределах vз = 25 — 115 м/мин. Продольная подача сообщается шлифовальному кругу либо (реже) заготовке. В зависимости от обрабатываемого материала и характера шлифования продольная подача принимается sп равной 0,25 — 0,75 ширины В
круга на один оборот.
Таким образом sпр = (0,25 ÷ 0,75) В мм/об.
Поперечная (радиальная) подача t сообщается кругу, а на некоторых станках – заготовке. Для чернового шлифования t = 0,05 ÷ 0,075 мм/ дв. ход.; для чистового t = 0,002 ÷ 0,01 мм/ дв. ход.
Рис. 6.11. Схема планетарного шлифования
Планетарные внутришлифовальные станки – горизонтальные и вертикальные – применяются для шлифования отверстий в крупных и тяжёлых деталях, вращение которых затруднено.
Схема планетарного шлифования приведена на рис. 6.11. Заготовка 1 в процессе обработки остаётся неподвижной, а шлифовальный круг 2 вращается одновременно вокруг своей оси со скоростью резания vk и вокруг оси отверстия со скоростью круговой подачи vз, чем обеспечивается планетарное движение. Продольная sпр и поперечная t подачи также осуществляются шлифовальным кругом. Поперечная подача очень мала – она выражается тысячных или сотых долях миллиметра. Эти станки имеют ограниченное применение.
Бесцентровые внутришлифовальные станки используются для обработки цилиндрических и конических отверстий после шлифования наружных поверхностей деталей, при этом обеспечивается высокая концентричность натужней и внутренней поверхностей.
Схема внутреннего бесцентрового шлифования показана на рис. 6.12, а. Деталь 1 устанавливают между опорным роликом 2 , ведущим кругом 3 и прижимным роликом 4. Шлифовальный 5 и ведущий 3 круги вращаются в разные стороны. Если диаметр детали (заготовки) меньше 30 мм, то опорный ролик заменяется опорным ножом 6 (рис. 6.12, б). Шлифовальный круг осуществляет движение резания vk и поперечную t подачу в конце каждого хода детали, а деталь – круговую подачу с окружной скоростью ведущего круга и продольную подачу вместе с ведущим кругом и роликом.
При шлифовании конических отверстий ведущий круг
и ролики вместе с деталью устанавливаются под углом
наклона образующей конуса к его оси (рис. 6.12, в).
Внутришлифовальные станки делятся на универсаль-
ные, полуавтоматы, автоматы, специализированные нор-
мальной точности и прецизионные.
Универсальные станки моделей ЗВ225, ЗЛ227, ЗА229
и др. предназначены для обработки отверстий диамет-
р 5 до 800 мм. Станки-полуавтоматы моделей
ЗЛ225Б, ЗА226Б, ЗА227Б, ЗА230Б и др. служат для шли-
фования отверстий диаметром от 16 до 500 мм. У станка мод. ЗА225Б число оборотов электрошпинделя состав-
ляет nк=96 000 об/мин., а число оборотов шпинделя баб-
ки — n3 = 600 ÷ 2400 об/мин.
Внутришлифовальные стан-
ки-автоматы моделей 3225Б и 3227А имеют загрузочные
устройства для подачи обрабатываемых деталей в зону
шлифования, автоматического закрепления и снятия их а также для автоматических измерений на ходу станка и
управления правкой круга.
Диаметр круга для внутреннего шлифования выби-
рают в зависимости от диаметра обрабатываемого от-
верстия. Эта зависимость определяется величиной дуги
контакта поверхности обрабатываемого отверстия и по-
верхности круга. При диаметре отверстия свыше 200 мм
диаметр круга меньше зависит от размера отверстия и
определяется диаметром шпинделя шлифовальной бабки.
Рис. 6.12. Схемы внутреннего бесцентрового шлифования
Внутреннее шлифование, сопровождающееся значи-
тельным теплообразованием, следует осуществлять отно-
сительно крупнозернистыми кругами, более мягкими и с
более открытой структурой, чем при наружном шлифова-
ИИ, при этом предотвращаются прожоги и обеспечи-
вается лучший отвод стружки.
В качестве абразивного инструмента применяют цилиндрические круги формы ПП (ГОСТ 2424-60) диа-
метром D = 3 ÷ 200 мм и высотой Н = 1 ÷ 32 мм. Если
одновременно с отверстием надо обрабатывать и торец де-
тали или требуются круги большей высоты, то исполь-
зуют круги формы ПВ диаметром D = 10 ÷ 200 мм и вы-
сотой Н = 6 ÷ 40 мм.
Плоское шлифование
Плоское шлифование является наиболее распространённым способом обработки плоскостей и фасонных ли-
нейных поверхностей, к которым предъявляются высокие
требования по точности и шероховатости поверхности.
Плоское шлифование производится периферией или
торцом круга. Как в одном, так и в другом случае об-
работка может быть осуществлена на станках с прямолинейным (модели ЗГ71, 3701, 372Б, 3722, ЗБ724 и
МШ-123) или вращательным движением стола с обраба-
тываемой деталью (модели ЗА740 и ЗБ740).
Шлифование периферией круга можно осуществить
тремя способами: врезанием, глубинным способом и мно-
гократными последовательными проходами.
Шлифование врезанием (рис. 6.13, а) производится
при обработке мелких деталей, ширина которых меньше
высоты круга. При шлифовании врезанием происходит
очень большой износ круга, а точность обработки невы-
сока.
При глубинном способе шлифования (рис. 6.13, б) при-
пуск снимается за один проход круга по ширине детали.
Основная тяжесть работы падает на зерна, расположен-
ные около торца круга, при этом круг изнашивается на
конус. При обработке глубинным способом круг должен
иметь ступенчатую форму пли конический участок.
Шлифования многократными последовательными
проходами (рис. 6.13, в) наиболее широко используется
в промышленности. В этом случае после каждого продольного хода дольного хода стола круг или стол получает продольное
перемещение sпр вдоль оси круга. Эта продольная пода-
ча sпр необходима для снятия слоя металла по всей ши-
рине плоскости. Затем кругу или детали сообщается по-
перечная подача t для снятия следующего слоя металла.
Цикл повторяется до полного удаления пропуска.
При шлифовании периферией круга точность обра-
ботки достигает 0,005 мм на 500 мм длины, а шерохо-
ватость поверхности — 9 — 10-го классов чистоты.
Шлифование торцом круга — более производитель-
ный способ, так как он допускает обработку плоскостей большой ширины или одновременно у группы деталей,
при этом торец
Рис. 6.13. Схемы шлифования периферией круга
круга обычно перекрывает всю ширину
плоскости, и потому все движения в процессе шлифова-
ния сводятся квращению круга со скоростью резания vк,
к поступательному или вращательному движению детали
и к осевой подаче круга после каждого хода или оборота
стола. Схема плоского шлифования торцом круга на
станках с продольным движением прямоугольного стола
приведена на рис. 6.14, а и б, а с вращательным движе-
нием круглого стола — на рис. 6.14, в.
Для улучшения условий удаления стружки и сниже-
ния температуры в зоне резания необходимо выполнять
следующее:
1) искусственно сокращать зону соприкосновения
круга с деталью путем наклона шлифовальной бабки
(см. рис. 6.14, б) или правки торца круга под углом. При
небольшом наклоне шлифовальной бабки вместо геомет
рически правильной плоскости получается вогнутая по-
верхность, отступление которой от плоскости будет тем
значительнее, чем больше угол наклона оси круга α. Ве-
личина этого угла обычно не превышает 3 ÷ 5о;
2) применять обильное охлаждение;
3) использовать менее твёрдые и более крупнозернистые круги;
4) создавать прерывистую зону резания, применяя сегментные круги.
-ние
Рис. 6.14. Схемы шлифования торцом круга
При шлифовании торцом круга точность обработки составляет 0,02 мм для станков с круглым столом и 0,015 мм – для станков с прямоугольным столом на 1000 мм длины; шероховатость поверхности – до 9-го класса точности.
Лабораторная работа № 7
Тема: Обработка зубчатых колес и шлицевых поверхностей
Задание и порядок выполнения работы:
1. Ознакомиться с инструкцией о выполнении работы.
2. Ознакомиться с теоретическими сведениями о способах и методах обработки зубчатых колес и шлицевых поверхностей
3. Разработать технологический процесс обработки зубчатых колес и шлицевых поверхностей, с составлением всей необходимой технологической документации
4. Составить отчет о работе
Содержание отчёта:
При составлении отчета необходимо:
I. Ознакомиться с краткими теоретическими сведениями по следующим вопросам:
1. Обработка зубчатых поверхностей и шлицевых поверхностей
а) Изготовление конических зубчатых колес
б) Изготовление червячных колес
2. Отделочные способы обработки зубчатых поверхностей
а) Шевингование
б) Шлифование
в) Хонингование
г) Притирка зубьев
3. Обработка поверхностей шпоночных и шлицевых соединений
а) Обработка шпоночных пазов
б) Обработка шлицевых поверхностей
II. Представить технологическую документацию необходимую для выполнения технологического процесса обработки зубчатых колес и шлицевых поверхностей одним из выбранных способов
III.Ответить на контрольные вопросы:
1. Для каких степеней точности допуски и отклонения в стандарте не
предусмотрены?
2. На сколько этапов разбивается технологический процесс механической
отработки зубчатых колес?
3. Из скольких фрез состоит набор используемый для нарезания колес с модулем до 9?
4. Какой величины может достигать скорость резания при обработке дисковыми
быстрорежущими фрезами цилиндрических и конических колес?
5. Назовите основной метод нарезания зубьев колес применяемый на машиностроительных предприятиях.
6. На каком оборудовании производится зубонарезание?
7. Что представляют собой червячные фрезы
8. Как называют процесс снятие с боковых поверхностей зубьев тонкой волосообразной
стружки толщиной 0,001 - 0,005 мм при помощи специального инструмента?
9. Какой процесс механической обработки применяют для отделки зубьев закаленных зубчатых колес?
10. Какой процесс применяют для точной обработки сквозных и глухих цилиндрических, конических и ступенчатых отверстий?
Литература:
Основная
1. Космачёв И. Г. Технология машиностроения. Лениздат, Ленинград – 1970, 400 с., ил.
Дополнительная
2. Муравьёв Е. М. Технология обработки металлов: Учеб. пособие для учащихся 5 – 9 кл. общеобразоват. учреждений. - М.: Просвещение, 1995.-224 с., ил.
3. Муравьёв Е. М., Молодцов М. П.Практикум в учебных мастерских: Учеб. пособие для студентов пед. ин-тов по спец. № 2120 «Общетехнические дисциплины и труд» и учащихся пед. уч-щ по спец. № 2008 «Преподавание труда и черчения в неполной сред. шк.» В 2 ч. Ч.1. Обработка металлов /Под ред. Е. М. Муравьёва. - М.: «Просвещение», 1987.-272 с., ил.
Теоретические сведения
Дата добавления: 2018-11-24; просмотров: 3243; Мы поможем в написании вашей работы! |
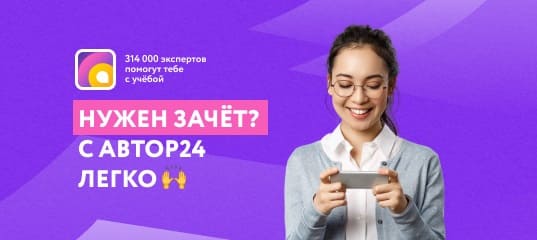
Мы поможем в написании ваших работ!