Обработка зубчатых колёс и шлицевых поверхностей
В передачах современных машин широко применяют разнообразные по форме, размерам и профилю зубчатые колеса (рис. 7.1).
Наиболее широко распространены цилиндрические зубчатые колеса с прямыми и косыми зубьями (рис. 7.1, а и б). Эти колеса предназначены в основном для передачи крутящего момента от одного вала к другому при параллельном расположении осей валов.
На рис. 7.1, в приведена коническая передача с пересекающимися осями, причем угол пересечения осей может быть любой величины. Конические колеса изготовляются с прямыми и криволинейными зубьями.
Зубчатая передача со скрещивающимися осями может состоять из пары зубчатых колес с винтовым зубом (рис. 7.1, г).
Червячная передача (рис. 7.1, д) — передача со скрещивающимися осями — применяется для осуществления малых передаточных отношений, а также для передачи больших мощностей.
Реечная передача (рис. 7.1, е), одним элементом которой является зубчатое колесо с прямым или косым зубом, а другим — зубчатая рейка, передает движение как от зубчатого колеса к рейке, так и наоборот.
ГОСТом определены степени точности, которые располагаются в порядке понижения точности: 1, 2, 3, 4, 5. 6, 7, 8, 9, 10, 11 и 12. Для степеней точности 1, 2 и 12 допуски и отклонения в стандарте не предусмотрены.
График для сопоставления классов и степеней точности для цилиндрических, червячных и конических колес по различным ГОСТам представлен на рис. 7.2. Из этого графика видно, что 2-й класс точности соответствует примерно 7-й степени точности для цилиндрических и червячных колес и 8-й степени точности для конических колес, а 3-й класс соответственно 8-й и 9-й степеням точности.
|
|
Кроме технических условий и норм точности на готовые зубчатые колеса имеются технические условия на обработку заготовок до нарезания зубьев. Они характеризуются следующими основными данными: центральное отверстие изготовляют по 2-му классу точности и 7-му классу чистоты, центровые отверстия фланцевыхзубчатых колес — по 1-му или 2-му классу точности и 7-му классу чистоты, размер между торцовыми поверхностями фланцадля крепежных отверстий — по 3-му или 3а классу точности, чистота торцовых поверхностей — по 7-му классу. Посадочные шейки колес валовизготовляют по 2-му классу точности и по 7 — 8-му классам чистоты.
Отклонение от перпендикулярности торцов ступицы и зубчатого венца и оси отверстия (биение торцов) задается величиной 0,15 мкмна 1 мм диаметра.
Изготовление цилиндрических зубчатых колёс. Технологический процесс механической обработки зубчатых колес разбивается на два этапа. Первый этап включает операции, связанные с образованием геометрической формы заготовки зубчатого колеса до нарезания зубьев, а второй — зубонарезание и отделочные операции обработки зубьев и остальных элементов детали.
|
|
Характерными операциями первого этапа являются: предварительная токарная обработка, обработка отверстия, чистовая токарная обработка.
Основная специфика изготовления зубчатых колес проявляется во втором этапе. Образование зубьев цилиндрических колес и реек производится двумя методами: копированием и огибанием. Сам процесс зубообразования может выполняться резанием со снятием стружки или путем пластической деформации материала.
Метод копирования.При нарезании колес методом копирования профиль режущей части инструмента (фрезы, резца, протяжки) полностью соответствует профилю впадины зуба колеса. Профиль инструмента копируется на колесе.
Метод копирования в настоящее время находит применение времонтном производстве при отсутствии специальных зуборезных станков, при изготовлении крупных зубчатых колес и для предварительного нарезания зубьев.
Нарезание колес дисковыми модульными фрезами (рис. 7.3, а) производится на универсальных фрезерных станках, оснащенных делительными головками или столами, а также на зубофрезерных станках, имеющих устройство для индивидуального деления.
|
|
Дисковые модульные фрезы стандартизованы (ГОСТ 10996-64) для всего ряда модулей от 0,3 до 16 мм. Для каждого модуля применяется комплект фрез из 8, 15 или 26 шт. для чисел зубьев нарезаемых колес от 12
и более. Каждая фреза, входящая в набор, нарезает несколько зубчатых колес в определенном диапазоне чисел зубьев. Так, например, фреза № 1 (из набора 8 фрез) предназначена для нарезания колес с числом зубьев от 35 до 54 и т. д.
Профиль фрезы каждого номера соответствует профилю впадины колеса, имеющего наименьшее число зубьев для этого диапазона. Остальные колеса данного диапазона будут нарезаться такой фрезой с некоторыми погрешностями. Чем больше фрез в наборе, тем точнее будут нарезаны колеса. Для нарезания колес с модулем до 9 используется набор из 8 фрез, а для обработки колес с модулем свыше 9 и более точных — наборы из 15 или 26 фрез.
Если степень точности нарезаемых колес по нормам плавности грубее 8-й, то дисковыми фрезами может осуществляться чистовая обработка.
Специальные дисковые фрезы могут оснащаться пластинками твердых сплавов. Такие двух- и трехрядные фрезы обеспечивают высокую производительность обработки.
|
|
Дисковыми фрезами можно нарезать короткие рейки на горизонтально-фрезерных станках с использованием индикаторных упоров и набора концевых мер.
Скорости резания при обработке дисковыми быстрорежущими фрезами цилиндрических и конических колес составляют 25 ÷ 40 м/мин. На полную глубину колеса нарезают при m < 6 мм, в два прохода — при т = 6 ÷ 12 мм и в три прохода — при т >12 мм.
Нарезание колес пальцевыми модульными фрезами (рис. 7.3, б) производится на универсальных фрезерных станках, оснащенных делительными головками или столами, а также на зубофрезерных станках, имеющих устройство для индивидуального деления и специальный суппорт для установки пальцевых фрез.
Пальцевые модульные фрезы не стандартизованы и изготовляются по нормалям заводов. Применяются они для нарезания зубчатых колес, имеющих модуль т = 10 ÷ 50 мм.
Наиболее целесообразно использование пальцевых фрез при изготовлении зубчатых колес с модулем более 20 мм 8-й степени точности по ГОСТу и грубее, а также для нарезания шевронных колес без канавки. При обработке шевронных колес каждая половина шеврона может нарезаться отдельно как косозубое колесо или же они могут обрабатываться на зубофрезерных станках со специальным устройством.
Протягивание зубьев осуществляется в основном при изготовлении открытых венцов зубчатых колес с внутренними прямыми зубьями при z < 50. На ряде предприятий производят протягивание внешних зубьев.
Внешние зубья протягивают охватывающими составными протяжками, которые могут обрабатывать одновременно либо все зубья колеса, либо часть их (секторной протяжкой) с последующим поворотом заготовки для протягивания других зубьев. Протягивание производится также комплектом протяжек методом единичного деления после обработки каждой впадины.
Долбление зубьев методом копирования осуществляется в массовом производстве при предварительной обработке зубьев прямозубых колес. Обработка производится при помощи многорезцовой головки, нарезающей одновременно все зубья колеса (рис. 7.4).
Резцы 1 расположены радиально по отношению к заготовке 2. Процесс нарезания зубьев происходит при возвратно-поступательном движении заготовки 2 и неподвижной резцовой головке. За каждый двойной ход заготовки подаются по направлению к центру колеса на определенную величину подачи. Процесс нарезания заканчивается после подачи резцов на полную глубину впадин.
Метод огибания (обкатки)— основной метод нарезания зубьев колес. В соответствии с ним зубья образуют фрезерованием червячными фрезами, долблением долбяками, строганием гребенками, горячим и холодным накатыванием.
Фрезерование червячными фрезами является основным процессом предварительной и чистовой обработки зубьев. Оно применяется для нарезания эвольвентных зубьев цилиндрических колес наружного зацепления.
Схема фрезерования зубьев червячной фрезой приведена на рис. 7.5, а. Фреза 1, вращаясь со скоростью резания vфр и осуществляя поступательное перемещение — продольную подачу snp — параллельно оси заготовки, обрабатывает зубья по всей ширине колеса. Движение круговой подачи осуществляется благодаря вращению заготовки 2 со скоростью vд. Это движение точно согласовано с числом оборотов фрезы. За время одногооборота фрезы заготовка должна повернуться на k зубьев, где k— число заходов фрезы.
Фрезу закрепляют в суппорте, который должен быть повернут таким образом, чтобы ось фрезы была наклонена под углом α подъема винтовой линии витков фрезы (рис. 7.5, б). Нарезаемое зубчатое колесо устанавливают на столе станка. Стол осуществляет перемещение по станине для установки на глубину зуба и вращательное движение, благодаря которому производится обкатка зубчатого колеса по фрезе. Суппорт с фрезой осуществляют подачу движением вдоль оси колеса.
Число проходов фрезы зависит от величины модуля. Колеса с модулем до 3 мм нарезают за один проход, а с модулем более 3 мм — за два и даже три прохода.
Червячные фрезы для нарезания цилиндрических зубчатых колес с эвольвентными профилями стандартизованы. Типы, параметры и размеры фрез для модулей 1—50 мм регламентируются ГОСТом.
Фрезы изготовляются трех типов и четырех классов точности: тип I — фрезы цельные прецизионные класса точности АА; тип II — фрезы цельные общего назначения классов точности А, В и С; тип III— фрезы сборные общего назначения классов точности А, В и С.
ГОСТ рекомендует использовать фрезы класса АА—для нарезания колес 7-й степени точности; класса А — 8-й степени точности; класса В — 9-й степени точности; класса С — 10-й степени точности.
Для нарезания колес 5-й и 6-й степеней точности червячные фрезы изготовляют по специальным техническим условиям или отбирают их из фрез класса АА.
Червячные фрезы бывают однозаходные и двухзаходные. Точность обработки двухзаходными фрезами невысокая, но они позволяют увеличить производительность. Их следует применять для черновой и получистовой обработки зубьев.
Зубчатые колеса нарезают на зубофрезерных станках. Полуавтомат мод. 5Е32 представляет собой одну из современных моделей вертикальных зубофрезерных станков с подвижной стойкой суппорта. Он предназначен для нарезания цилиндрических зубчатых колес средних размеров внешнего зацепления с прямыми и винтовыми зубьями, а также червячных зубчатых колес.
Нарезаниезубьев долбяками на зубодолбежных станках в основном осуществляется при обработке закрытых венцов с внутренними зубьями и зубчатых реек.
Схема нарезания зубьев цилиндрических колес с прямыми и косыми зубьями приведена на рис. 7.6, а. При обработке долбяк 1 и заготовка 2, синхронно вращаясь, обкатываются относительно друг друга и совершают следующие движения. Долбяк, закрепленный на штосселе станка, осуществляет возвратно-поступательное и вращательное движения. Поступательное движение долбяка вниз является движением резания, соответствующим скорости резания vр, а поступательное движение вверх — холостым ходом vх.
Во время холостого хода долбяка во избежание трения задних поверхностей его зубьев о поверхность резания долбяк отводится от обрабатываемой заготовки. Врезание зубьев долбяка в заготовку осуществляется подачей его в радиальном направлении (sp). Вращение заготовки вокруг своей оси является круговой подачей sк. Круговая подача выражается длиной дуги делительной окружности долбяка в миллиметрах, на которую он поворачивается за один двойной ход.
При нарезании косозубых колес косозубыми долбякамиприменяют винтовые копиры 3 (рис. 7.6, б), которые устанавливаются на верхнем конце штосселя 4 станка.
Долбяки изготовляют пяти типов и трех классов точности: тип I —долбяки дисковые прямозубые классов точности АА, А и В; тип II — долбяки дисковые косозубые классов точности А и В; тип III— долбяки чашечные прямозубые для закрытых венцов при d = 75, 100 и 125 мм классов точности АА, А и В, приd=50 мм классов точности А и В; тип IV — долбяки хвостовые прямозубые класса точности В; тип V — долбяки хвостовые косозубые класса точности В.
При изготовлении колес 6-й степени точности рекомендуется применять долбяки класса АА; 7-й степени точности — класса А; 8-й степени точности — класса В.
Так как зубья долбяка в любом сечении, перпендикулярном оси, очерчены по эвольвенте, то одним долбяком данного модуля можно нарезать колеса такого же модуля с любым числом зубьев.
Колеса 8—9-й степеней точности с модулем до 2,5 мм нарезают за один проход (обкатку), а с модулем более 2,5 мм — за два прохода. Колеса 7-й степени точности в зависимости от модуля нарезают за 2—3 прохода.
Шероховатость поверхности обработанных долбяками зубчатых колес соответствует 6—7-му классам чистоты.
Обработка зубчатых колес долбяками производится на зубодолбежных станках. Зубодолбежный полуавтомат мод. 5В12 предназначен для нарезания цилиндрических колес с прямыми и винтовыми зубьями как наружного, так и внутреннего зацепления модулем от 1 до 4 мм. В крупносерийном и массовом производстве черновое и получистовое нарезание цилиндрических зубчатых колес наружного зацепления, блоков зубчатых колес, а также шлицевых валиков осуществляют резцовыми головками на зубодолбежном полуавтомате мод. 5120. Наша промышленность выпускает также аналогичные по принципу действия станки моделей 5110 и 5А130. Наименьший и наибольший модули нарезаемых на них зубчатых колес 2,5 и 6 мм.
Нарезание зубьев гребенками на зубострогальных станках производят при изготовлении точных прямозубых, косозубых и шевронных колес с внешними зубьями больших модулей, а также с зубьями большой длины.
Гребенки бывают прямозубые и косозубые. В торцовой плоскости зубьям гребенки приданы режущие свойства. По ГОСТу они имеют профиль рабочей рейки.
Схема нарезания зубьев гребенкой показана на рис. 7.7. Движение резания осуществляется при возвратно - поступательном перемещении гребенки. Гребенка, установленная на заданную глубину, перемещается из позиции 4 в позицию 1. Затем включается движение обкатки, при котором имитируется зацепление рейки и колеса, и совершаются согласованные движения — перемещение гребенки из позиции 1 в позицию 2, а также поворот нарезаемого колеса на заданный угол. После окончания обкатки, в ходе которой ого или нескольких зубьев, происходит формирование одного или нескольких зубьев, гребенка отходит от колеса — из позиции 2 она перемещается в позицию 3 изатем в исходную позицию 4. После этого процесс повторяется.
Из-за наличия холостых ходов и прерывистого процесса обкатки этот способ нарезания зубьев менее производителен, чем обработка зубодолбежным дисковым долбяком и тем более фрезерованием.
Накатывание зубчатых поверхностей. Процесс накатывания находит применение при изготовлении цилиндрических колес с прямыми, косыми и шевронными зубьями. Колеса с модулем до 1,5 мм накатываются в холодном состоянии, а с модулем свыше 1,5 мм и до 10 мм— в горячем состоянии.
Основными схемами накатывания, основанными на принципе обкатки, являются: накатывание с радиальной подачей валков и накатывание с осевой (продольной) подачей заготовки.
Накатывание зубчатых колес можно осуществлять не только на специальных станках, но и на токарных, револьверных, резьбонакатных и других с помощью приспособлений.
Накатывание с радиальной подачей валков колес диаметром более 60 мм целесообразно осуществлять двумя накатными роликами (рис. 7.8). Заготовка 3 устанавливается на оправку 5 и фиксируется штырями поводка 6. Оправка и поводок закреплены на стойке 12, которая свободно поворачивается на шарнире 13. Предварительное накатывание заготовки производят роликами 2 и 9, а окончательное—калибрующими роликами 4 и 10. Во избежание возможного выдавливания металла в осевом направлении торцов роликов устанавливаются ограничительные диски-реборды 11.
Заготовка и накатные ролики получают принудительное вращение от взаимно связанных колес 1, 7 и 8. Ведомое зубчатое колесо 7, жестко связанное и синхронно вращающееся с заготовкой 3, имеет такое же число зубьев, как иобрабатываемое колесо.
Накатывание по этой схеме обычно производится на двухроликовых гидравлических резьбонакатных станках с применениемспециального качающегося приспособления.
Схема накатывания колес в горячем состоянии зубчатым и гладким валками представлена на рис. 7.9. Заготовка 3, установленная на оправку, принудительно вращается между зубчатым 4 и гладким 1 валками, которые также получают принудительное вращение. Гладкий валок устраняет утечку металла с периферии зубьев, способствуя их уплотнению и калибровке. Боковые ролики 2, свободно вращающиеся при вращении заготовки, препятствуют осевому выдавливанию металла у торца. Индуктор 5 обеспечивает нагрев заготовки токами высокой частоты до необходимой температуры и поддержание этой температуры в процессе накатывания.
Накатывание с осевой подачей. Заготовки длиной свыше 30 ммцелесообразно накатывать с осевой (продольной) подачей роликами, имеющими заборную часть.
Конструкция трехролико-вого приспособления для накатывания пакета заготовок на токарно-револьверном станке мод. СМ36 изображена на рис. 7.10. Корпус 11 накатной головки крепится в конической втулке 12, устанавливаемой в револьверной головке станка. Каретки 4 с накатными роликами 2, которые вращаются во втулках 3 и фиксируются гайками 1, располагаются в пазах корпуса и крепятся гайками 6. Винты 5 позволяют перемещать каретки в радиальном направлении. В отверстие корпуса 11 устанавливается пиноль 10. В подшипниках 7 ее крепится упорный центр 8. Шпонка 9 предохраняет пиноль от проворота. Штревелем 17 пиноль связана с гайкой 16, на которой крепится пружина 15. Другой конец пружины крепится на ступице контргайками 13 и 14.
В процессе накатывания заготовок, установленных на оправке 20, ролики вместе с корпусом движутся в осевом направлении, а центр с пинолью остается неподвижным, вызывая растягивание пружин, при этом пакет заготовок сжимается еще большим осевым усилием, что препятствует вытеканию металла на торцы заготовок.
На корпусе накатной головки в державке 18 закреплен резец 19, который производит наружную обработку заготовок после накатывания при обратном ходе головки.
Диаметр заготовки из прутка для накатывания колес в холодном состоянии можно определить по следующей формуле:
где dд — диаметр делительной окружности обрабатываемого зубчатого колеса, в мм;
М — коэффициент, зависящий от числа зубьев обрабатываемого колеса (М — 0,965 — 0,995).
Отверстие в заготовке должно быть выполнено по 2-му классу точности. Биение наружной поверхности заготовки относительно отверстия не должно превышать 0,03—0,04 мм,допускаемые непараллельность торцов — 0,02 мм,неперпендикулярность оси центрального отверстия— 0,03—0,04 мм.
При накатывании мелкомодульных зубчатых колес в холодном состоянии с осевой ирадиальными подачами целесообразно работать со следующими скоростями:
Обрабатываемый материал Скорость накатывания, вм/мин
Дюралюминий, латунь, бронза 80—100
Стали марок 40, 50, 1X13, 2X13, 3X13, 4X13
и 30ХГСА 30—50
Рекомендуемые величины подач на оборот детали при накатывании зубчатых колес с осевой подачей приведены в табл. 7.1. Как видно из этой таблицы, подача зависит от длины пакета заготовок, так как при большой его длине увеличиваются осевые усилия, распирающие пакет.
Таблица 7.1
Рекомендуемые подачи и длины пакета при накатывании зубчатых колес (т=0,5 ÷ 0,8мм) из различных материалов
В качестве смазывающе-охлаждающей жидкости при нарезании зубчатых колес рекомендуется применять веретенное масло № 3 (ГОСТ 1707-51) или его смесь с водной эмульсией (80% веретенного масла № 3 и 20% эмульсии).
Хорошие результаты дает также смазка, состоящая из следующихкомпонентов(в % по весу):
веретенное масло № 3 (ГОСТ 1707-31).... …………………………………………92
петролатум(ГОСТ 4096-54)…………………………………………………………5
эмульсия………………………………………………………………………………3
Петролатум смешивается с маслом в разогретом (до жидкой консистенции) состоянии. Смазка должна подаваться в объеме 12—17 л/мин.
Точность зубчатых колес соответствует при горячем накатывании 9-й степени, а при холодном — 6—8-й степеням. В первом случае получают поверхность по 4—6-му классам чистоты, а во-втором — по 8—11-му.
Изготовление конических зубчатых колёс.
По назначению, конструктивным и технологическим признакам конические колеса можно разбить на три типа. К первому типу относятся ведущие или ведомые колеса (рис. 7.11, а), имеющие ступицу с отношением —
> 1; обрабатываются такие колеса на оправке с базированием по отверстию и торцу. Второй тип конических колес — венцовые ведомые колеса (рис. 7.11, б), изготовляемые в патроне с базированием по торцу и отверстию. К третьему типу относятся ведущие колеса-валы (рис. 7.11, в), обрабатываемые в центрах; базами здесь служат цилиндрические поверхности А1 и Б1.
У колес первого типа отверстие может быть шлицевым, со шпонкой или гладким. У колес второго типа — отверстия гладкие. Так как торец и отверстие колес второго типа являются технологическими базами, то их обычно обрабатывают с одной установки; базовые поверхности А1 и Б1 у колес-валов третьего типа подготовляются шлифованием до нарезания зубьев.
Конические колеса изготовляют в соответствии с ГОСТом. Для них также установлено 12 степеней точности. Для степеней 1—4-й и 12-й допуски не
предусмотрены. 1-й класс точности соответствует примерно 6—7-й степенямточности; 2-й класс — 8-й степени и 3-й класс — 9-й степени точности.
В соответствии с перспективным типажом зубообрабатывающего оборудования рекомендуется изготовлять конические колеса прямозубые, косозубые, с круговыми наклонными зубьями и скруговыми зубьями.
Нарезание колес методом копирования. Как уже указывалось, при обработке методом копирования режущим кромкам инструмента придается форма профилей нарезаемых зубьев.
Метод копирования из-за погрешностей в самой кинематической схеме образования зуба применяется только для предварительного нарезания или же для получения колес невысокой точности.
В массовом и крупносерийном производстве дисковыми модульными фрезами осуществляют предварительное нарезание прямых зубьев открытых венцов. В единичном и мелкосерийномпроизводстве дисковыми фрезами производят чистовое нарезание конических колес 10 — 11-йстепеней точности. Обработка ведется на универсальных горизонтально-фрезерных станках с делительной головкой ина стайках моделей ЕЗ-1 и ЕЗ-11.
Пальцевыми модульными фрезами осуществляют предварительное нарезание прямых и косых зубьев закрытых венцов колес 10-й степени точности, а также обрабатывают крупные конические колеса 10-й степени точности. Обработку производят на универсальных фрезерных станках с делительной головкой.
При нарезании крупных конических колес с прямыми зубьями и закрытыми венцами 9—10-й степеней точности в единичном имелкосерийном производстве осуществляют строгание зубьев по копиру на стайках моделей 5283 и 5А283.
При чистовом нарезании прямых зубьев открытых венцов колес 9-й степени точности в крупносерийном и массовом производстве осуществляют протягивание зубьев круговой протяжкой на станках моделей 5245 и 1222.
На станке мод. 528 методом копирования круговые зубья открытых венцов конических колес нарезают начерно. В качестве режущего инструмента используют специальную головку, резцы которой расположены по окружности и воспроизводят зуб колеса.
Нарезание колес методом огибания.Наиболее точным и производительным методом нарезания конических колес является метод огибания (обкатки), осуществляемыйна зубострогальных станках моделей 52G, 5A2G, 5282, 5П23Б и др. двумя резцами.
Схема нарезания прямозубого конического колеса приведена на рис. 7.12, а. Процесс нарезания основан на принципе зацепления обрабатываемой детали 1 с воображаемым плоским колесом 2, одним из зубьев которого как бы являются два строгальных резца, при этом
деталь должна быть установлена таким образом, чтобы образующая конус впадина зуба была параллельна направлению резания.
Зуб нарезаемого колеса 3 обрабатывается двумя резцами2 с возвратно-поступательным перемещением (рис. 7.12, б). Каждый из резцов обрабатывает одну сторону зуба колеса. Люлька 1 вместе с резцом представляет собой плоское коническое колесо. Это колесо и обрабатываемая деталь вращаются с такими угловыми скоростями, которые имеются в действительном зацеплении. Вначале резцы врезаются в деталь, а затем осуществляется формообразование зуба при совместной обкатке резцов идетали. После нарезания одного зуба деталь отходит от резцов (или наоборот), люлька опускается вниз, и деталь с помощью делительного устройства поворачивается на один зуб.
Схема обработки зуба конического колеса с предварительно прорезанными впадинами показана на рис. 7.12, б. Положения 1, 2 и 3 резцов относительно обрабатываемого зуба соответствуют начальному моменту обработки, середине ее и выходу резцов из зацепления с зубом в конце процесса нарезания.
После нарезания одного зуба резцы вновь приближаются к детали, и цикл повторяется. Обработка всех зубьев колеса происходит за один полный оборот заготовки.
Высокой производитель-ности достигают при нарезании прямых и прямых бочкообразных зубьев открытых зубчатых венцов колес 7—8-й степеней точности двумя дисковыми фрезами на станках моделей 5П23 и 5230. Схема фрезерования зубьев приведена на рис. 7.13. Движение резания осуществляется фрезами 1, режущие кромки которых воспроизводят в пространстве боковые поверхности зубьев плоского колеса.
Движение обкатки состоит из вращения фрез вокруг оси О производящего колеса по стрелке Б1 и согласованного с ним вращения детали 2 по стрелке Б2. Деление на зуб происходит периодически при отведенной детали. В процессе обработки фрезы не имеют перемещения вдоль нарезаемых зубьев, поэтому на дне впадины получается вогнутость, которая увеличивается с уменьшением диаметра фрезы и с увеличением ширины венца колеса. Колеса диаметром до 320 мммодулем до 8 мм нарезаютдисковыми фрезами диаметром 150 мм при работе на станке мод. 5П23 и диаметром 275 мм — при обработке на станке мод. 5230.
На станках моделей 525, 528, 5П23А, 5А27С1, 5А27СЗ и 5А27С2 производится черновое и чистовое нарезание круговых зубьев открытых венцов конических колес 7—8-й степеней точности. Обкатка производится при
одновременномвращении в зацеплении плоского производящего колеса и нарезаемой детали.
Схема нарезания конического колеса с круговыми зубьями представлена на рис. 7.14. Резцовая головка 1 совершает главное движение резания, вращаясь вокруг своей оси по стрелке А. Движение обкатки состоит из вращения резцовой головки 1 вокруг осп производящего колеса 3 по стрелке Б и согласованного с ним вращения детали 2 вокруг своей оси по стрелке В.
Движение обкатки продолжается до тех пор, пока нарезаемая впадина не будет полностью обработана. После этого обрабатываемая деталь отводится от резцовой головки, а обкатная люлька с головкой поворачивается в обратном направлении. За время обратного (холостого) хода люльки деталь поворачивается на определенное число зубьев, затем цикл повторяется.
Изготовление червячных колёс. До нарезания зубьев червячные колеса обрабатываются так же, как и обычные цилиндрические аналогичных размеров.
Зубонарезание производится на универсальных зубофрезерных или специальных станках. В качестве режущего инструмента применяют червячные фрезы, изготовленные по номинальным размерам червяка с учетом припуска на шевингование, а также резцы-летучки, профилированные по осевому или нормальному сечению витков червяка.
Червячные фрезы — высокопроизводительные и точные инструменты — применяются в крупносерийном и массовом производстве, а резцы-летучки, более простые визготовлении, но менее производительные и точные,— в единичном и мелкосерийном.
Нарезание червячных колес фрезами может производиться с радиальной или тангенциальной подачами. В первом случае используются цилиндрические, а во втором — конические червячные фрезы. Выбор подачи зависит от параметров червячного зацепления и требований к точности профиля его зубьев.
При работе с радиальной подачей sр (рис. 7.15, а) межосевое расстояние А между фрезой и нарезаемым колесом непрерывно уменьшается до такого расстояния, как в собранной червячной паре. Обкатка достигается благодаря согласованным движениям — вращениям фрезыи нарезаемого колеса. За один оборот фрезы колесо поворачивается на число зубьев, равное числу ее заходов.
С радиальной подачей нарезают колеса 8—9-й степеней точности, а также предварительно обрабатывают более точные колеса средних и крупных моделей.
Нарезание червячных колес с тангенциальной подачей (рис. 7.15, б) производится фрезой, имеющей коническую заборную часть. Фреза врезается в колесо по мере постепенного перемещения вдоль своей оси и при этом обкатывает его зубья. При настройке станка фрезу устанавливают на полную глубину резания. В процессе работы расстояние А сохраняется постоянным. Кроме вращения фреза получает осевую подачу sос.
За один оборот фрезы нарезаемое колесо поворачивается на определенное число зубьев. Кроме того, оно получает дополнительный поворот в соответствии с величиной осевого перемещения фрезы для предотвращения срезания зубьями червячной фрезы зубьев, образованных на колесе.
С тангенциальной подачей нарезают колеса 7—8-й степеней точности.
Точные червячные колеса малых размеров нарезают комбинированнымифрезами сразу начисто с тангенциальной подачей. Такие фрезы, плавно переходящие в шеве р, а затем в притир, позволяют получать колеса 6—7-и степеней точности. Применяются они в крупносерийном производстве.
Дата добавления: 2018-11-24; просмотров: 1230; Мы поможем в написании вашей работы! |
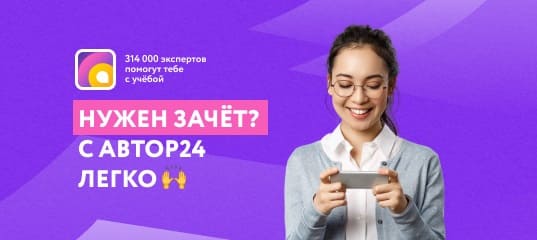
Мы поможем в написании ваших работ!