Сверление, зенкерование, развертывание
Сверление - один из распространенных способов получения глухих и сквозных цилиндрических отверстий в сплошном материале с точностью 4-5-го классов и шероховатостью поверхности 2-3-го классов.
Если необходимо образовать отверстие более высокой точности, то после сверления осуществляют зенкерование и развертывание его.
В сплошной заготовке отверстие выполняют сверлом. В зависимости от конструкции различают сверла спиральные, кольцевые, для глубокого сверления и центровочные. В машиностроении наиболее широко распространены спиральные сверла с коническим и цилиндрическим хвостовиками.
Инструментальная промышленность выпускает спиральные сверла с двумя направлениями канавок: правым и левым. Левые сверла имеют диаметр от 0,25 до 20 мм (ГОСТ 10902-64) и цилиндрический хвостовик. Используют их на токарных автоматах. Правые сверла с цилиндрическим хвостовиком по длине рабочей части делят на длинные диаметром от 2 до 20 мм (ГОСТ 886-64) и короткие диаметром от 0,25 до 20 мм . Сверла с укороченным хвостовиком (ГОСТ 4010-64) заводы-поставщики изготовляют по согласованию с потребителями по отдельным заказам.
В соответствии с ГОСТом 1093-64 спиральные сверла выпускают с удлиненным коническим хвостовиком диаметром от 6 до 30 мм и укороченным диаметром от 6 до 80 мм . Сверла мелкоразмерные с утолщенным хвостовиком изготовляют диаметром от 0,1 до 1,0 мм.
Спиральные сверла из сталей Р18Ф2,Р12,Р6М3 и Р9 используют для обработки металлов твердостью до 260-280 НВ, а из сталей Р9Ф5, Р18Ф2К5- для сверления труднообрабатываемых сплавов.
|
|
При работе сверлами больших диаметров (35-40 мм) из-за наличия у вершины сверла перемычки большой толщины возникают значительные осевые усилия. Поэтому отверстие больших диаметров сверлят за два прохода сначала сверлом меньшего диаметра, а затем требуемого. Чтобы перемычка второго сверла не участвовала в работе, а также для более равномерного распределения работы резания между обоими сверлами диаметр первого сверла d1 обычно принимают равным:
d1 ≈ (0,5 ÷ 0,6) d2,
где d2 - диаметр второго сверла.
Таблица 2.1.
Способы обработки отверстий в зависимости от заданной точности
Диаметр отверстия, в мм | Заготовка под отверстие | Классы точности | ||||
2 | 3 | 4 | ||||
До 10 | Сплошной материал | Сверление, развертывание черновое, развертывание чистовое | Сверление, развертывание | Сверление | ||
10-30 | Сплошной материал | Сверление, зенкерование или растачивание, развертывание черновое, развертывание чистовое | Сверление, зенкерование или растачивание, развертывание | Сверление, зенкерование | ||
Отлитое или прошитое отверстие с припуском до 4 мм на диаметр | Растачивание или зенкерование, развертывание черновое, развертывание чистовое | Растачивание или зенкерование, развертывание | Растачивание или зенкерование | |||
Отлитое или прошитое отверстие с припуском свыше 4 мм на диаметр | Растачивание или зенкерование черновое, зенкерование или растачивание получистовое, развертывание чистовое | Растачивание или зенкерование черновое, зенкерование или растачивание получистовое, развертывание | Растачивание или зенкерование черновое, зенкерование или растачивание чистовое | |||
30-100 | Сплошной материал | Сверление, рассверливание, зенкерование или вместо рассверливания и зенкерования-растачивания, развертывание черновое, развертывание чистовое | Сверление, рассверливание, зенкерование или вместо рассверливания и зенкерования - растачивания, развертывание | Сверление, рассверливание, зенкерование или вместо рассверливания и зенкерования -растачивание | ||
Отлитое или прошитое отверстие с припуском до 6 мм на диаметр | Растачивание или зенкерование черновое, развертывание черновое, развертывание чистовое | Растачивание или зенкерование, развертывание | Растачивание или зенкерование | |||
Отлитое или прошитое отверстие с припуском свыше 6 мм на диаметр | Растачивание или зенкерование черновое, зенкерование или растачивание получистовое, развертывание черновое, развертывание чистовое | Растачивание или зенкерование черновое, зенкерование или растачивание полу- чистовое, развертывание. | Растачивание или зенкерование черновое, зенкерование или растачивание получистовое |
Так как поперечная кромка сверла работает в неблагоприятных условиях и является причиной резкого увеличения осевой силы, ее подтачивают различными способа.
|
|
Подточка увеличивает передний угол поперечной кромки, уменьшает ее длину и тем самым снижает осевую силу резания.
Новатор В.И Жиров предложил конструкцию бесперемычного сверла из стали Р18 (рис. 2.1), которое имеет три пары режущих кромок с углами при вершине 2φ =116-118˚, 2φ1 = 70˚ и 2φ2 = 55˚.Для облегчения процесса стружкообразования в перемычке прорезается паз шириной 1,5-2,5 мм и глубиной 2 мм . Наличия паза в 2-3 раза уменьшает силу подачи и в 1,5-2 раза - момент сопротивления резания. А это приводит к уменьшению износа сверла и повышению его стойкости (в 2-3 раза по сравнению со стойкостью стандартных сверл).
|
|
При сверлении отверстий малых диаметров (менее 6-8 мм) также приходиться считаться с необходимостью уменьшения осевого усилия в связи с недостаточной прочностью и жестокостью сверла. В этих случаях целесообразно работать с большой скоростью резания при небольших подачах.
Отверстия большого диаметра (свыше 60 ÷ 70 мм) целесообразно обрабатывать путем кольцевого сверления, так как при обычном сверлении в стружку уходит значительное количество металла. При использовании же кольцевого сверла (см. рис. 2.2) своими режущими пластинами 1, закрепленными в корпусе 3, выбирает кольцевую канавку в обрабатываемой заготовке. В стенках корпуса между винтовыми канавками под винтами 2 размещены шарики, которые придают сверлу постоянное направление в работе до тех пор, пока высверливаемый сердечник держится жестко и может служить направлением для сверла. Корпус соединен резьбой с оправкой 4, на которой закреплено кольцо 5 со штуцером 6 и резиновым шлангом 7 для подвода охлаждающей жидкости.
![]() |

При первом способе обработки, когда ось сверла совпадает с направлением подачи, но не совпадает с осью наружной поверхности детали (рис. 2.3, а), подача сверла будет осуществляться под углом по отношению к оси детали, и потому ось отверстия займет неправильное положение, т.е. произойдет увод оси. Отверстие в этом случае сохраняет
![]() | ![]() |
цилиндричность.
При обработке по второму способу при несовпадении оси сверла с осью детали отверстие будет иметь переменный по длине диаметр. Это объясняется тем, что при отклонении оси сверла от оси вращающейся детали диаметр отверстия будет определяться уже не радиусом сверла, а расстоянием от оси вращения до наиболее удаленной точки на периферии сверла (рис. 2.3, б). Так как это расстояние по мере движения сверла все время увеличивается, то и диаметр отверстия тоже будет возрастать и отверстие примет коническую форму. С другой стороны, вращение детали приводит к самоцентрированию сверла, так как боковое давление на сверло со стороны стенки отверстия уже не будет уравновешено давлением с противоположной стороны, как это бывает при не вращающейся детали. За счет разности этих боковых давлений сверло будет стремиться занять такое положение, при котором его ось совпала бы с осью вращения детали.
Следовательно, при обработке отверстий с вращением детали увод оси сверла от нужного направления будет меньше, чем при сверлении с вращением инструмента. Однако в большинстве случаев отверстия обрабатывают на станках сверлильной группы, т.е. с вращением инструмента. На этих станках легче обеспечить получение требуемой скорости резания благодаря вращению уравновешенного шпинделя с инструментом и не приходиться прибегать к соответствующим мерам для балансирования вращающихся масс станка.
Для уменьшения увода оси сверла при обработке на сверлильных станках применяют кондукторы с направляющими втулками. Обработка в кондукторах дает хорошие результаты при относительно небольшой длине отверстия. С увеличением длины отверстия вследствие значительного свободного вылета режущей части сверла влияние направляющей втулки оказывается недостаточным.
Для уменьшения увода оси сверла при обработке отверстий в сплошном металле на револьверных станках и автоматах перед сверлением рекомендуется произвести центрование - засверливание углублений небольшой длины коротким и жестким сверлом (рис. 2.4, а). Угол при вершине ε1 у этого сверла должен быть меньше, чем у спирального (ε2). Обычно он составляет 90˚.Предварительное центрование заготовок обеспечивает более точное направление сверла, так как его перемычка не будет участвовать в работе (рис. 2.4, б). Уменьшению увода оси сверла также способствует уменьшение осевого усилия. Поэтому целесообразно применять сверла с подточенной перемычкой, а при малых диаметрах их работать с малыми подачами и большими скоростями резания.
Совмещение центра сверла с центром обрабатываемого отверстия может производиться как по разметке, так и с помощью кондуктора.
Точность расстояния между осями отверстий при сверлении по разметке составляет ±(0,2 - 0,5) мм. В отдельных случаях она может быть повышена до ±0,1 мм.
![]() |
При работе по кондуктору обычной точности точность расстояния между осями отверстий диаметром от 3 до 80 мм составляет ±(0,06 - 0,2) мм, а при работе по кондуктору повышенной точности ±(0,04-0,10) мм.
В крупносерийной и массовом производстве применяют специальные конструкции кондукторов, а в единичном и мелкосерийном – групповые или универсальные со сменными элементами и другими устройствами, позволяющими производить быструю переналадку их Одновременная обработка нескольких отверстий одной детали повышает производительность труда благодаря сокращению периода резания и затрат времени на смену режущего инструмента. В крупносерийном и массовом производстве для одновременной обработки нескольких отверстий используют многошпиндельные сверлильные станки и многошпиндельные головки, в серийном – универсальные многошпиндельные сверлильные головки. Конструкция сверлильных головок, число шпинделей в них и способ регулирования расстояния отверстий, обрабатываемых при помощи универсальных многошпиндельных головок, приведены на рис. 2.5.
Если отверстия расположены в детали на одной высоте и имеют одинаковую глубину, то все они обрабатываются в одно и то же время. Если отверстия расположены на различной высоте или глубина их не одинакова, то обработка разных отверстий может начинаться и заканчиваться в разное время. В обоих случаях рабочий ход головки начинается с врезания ближайшего к детали инструмента и заканчивается по окончании обработки всех отверстий.
У большинства универсальных многошпиндельных сверлильных головок все шпиндели вращаются с одинаковой скоростью, поэтому условия резания будут благоприятными только при небольшом различии в диаметрах одновременно обрабатываемых отверстий.
Многошпиндельные сверлильные головки могут быть использованы и для одновременной обработки отверстий в нескольких деталях одного наименования, закрепленных в соответствующем приспособлении. На них можно осуществлять позиционную обработку последовательно несколькими инструментами отверстий подобно тому, как это производится на агрегатных станках. При позиционной обработке в то время, когда одно отверстие сверлят, другое - зенкеруют, а третье - развертывают. Одновременно с этим в четвертой позиции снимают обработанную деталь и устанавливают новую заготовку. Из одной позиции в другую детали перемещаются при повороте круглого стола.
Имеются специальные многошпиндельные сверлильные головки для обработки отверстий, расположенных по окружности. Четырех шпиндельная головка этого типа с раздвижными шпинделями показана на рис.6. Она состоит из корпуса 1 и крышки 3, стягиваемых болтами 2. Головку крепят к пиноли станка при помощи разрезного хомута и специального фланца (рис. 2.6)
В шпиндель станка входит валик 10. На нижнем конце его, нарезан зубчатый венец, который находится в постоянном зацеплении с зубчатыми колесами 9, передающими движение шпинделями 5 головки через зубчатые 4 и 8. Поворачивая диски 6 и 7, можно изменять расстояние от оси шпинделя головки до оси шпинделя головки станка в пределах 2е, где е-расстояние между осями колес 4 и 8. Для закрепления дисков 6 и 7 в определенном положении затягивают болты, прижимающие сухари 11.
Зенкерованиеслужит для увеличения диаметра предварительно подготовленного отверстия (литого, штампованного или просверленного). Для получения отверстий точностью до 4-го класса с шероховатостью поверхности до 6-го класса операция зенкерования может быть окончательной и предварительной - перед развертыванием. Зенкерование применяют также для обработки фасок, цилиндрических и конических углублений под головки заклепок, винтов и болтов и зачистки торцовых поверхностей.
В зависимости от назначения зенкеры подразделяются на спиральные, цилиндрические и конические.
Спиральные зенкеры служат для обработки сквозных цилиндрических отверстий. Зенкеры диаметром 12-35 мм изготовляют цельными с коническими хвостовиками и с тремя режущими зубьями, а диаметром 25-80 мм - насадными с четырьмя (реже шестью)режущими зубьями. Насадные зенкеры диаметром 60-175 мм выполняют со вставными рифлеными ножами, оснащенными пластинками твердых сплавов.
Для зенкерования отверстий большого диапазона диаметров – от 30 до 200 мм -применяются насадные двузубые зенкеры-улитки.
Цилиндрические зенкеры служат для обработки торцов у литых бобышек и отверстий под цилиндрические головки винтов.
Коническими зенковками обрабатывают конические гнезда под болты и заклепки и центровые отверстия.
Зенкер, имеющий по крайней мере три режущие кромки, значительно прочнее сверла, вследствие чего обработка отверстия зенкером производительнее растачивания и рассверливания. При зенкеровании лучше обеспечиваются прямолинейность оси обрабатываемого отверстия и правильное ее положение. Однако при неравномерном припуске, неодинаковой твердости обрабатываемого материала и при наличии в нем твердых вкраплений, возможен увод оси зенкера, причем в чугунных деталях больше, чем в стальных.
Он может быть значительным и в начале зенкерования отлитых или прошитых отверстий. Для предупреждения увода инструмента зенкерованию таких отверстий должно предшествовать растачивание их резцом до диаметра зенкера и на глубину, примерно равную половине его длины.
Поверхность отверстия, обработанного зенкером, получается чище, чем при сверлении и рассверливании. Точность диаметра отверстия, обработанного зенкером под последующее развертывание, достигается значительно проще, чем при растачивании, так как при зенкеровании отсутствует установка режущего инструмента на требуемый размер.
Для исправления положения оси отверстия, уменьшения увода ее и обеспечения заданной точности осуществляют зенкерование с направлением инструмента в кондукторных втулках. Различают три способа направления зенкера – верхнее, нижнее и двойное (рис. 2.7).
При верхнем направлении (рис. 2.7, а) зенкер 1 может направляться во втулке 2 либо специальной цилиндрической частью, либо непосредственно своими калибрующими ленточками.
Нижнее направление осуществляется во втулке 2, расположенной впереди детали 3 (рис. 2.7, б). В этом случае на одной оси с зенкером 1 имеется специальная направляющая, выполненная заодно с зенкером. Для обеспечения правильной начальной ориентации зенкера необходимо, чтобы его направляющая часть вошла во втулку прежде, чем начнется процесс резания.
Для обработки отверстий диаметром свыше 25 мм целесообразно осуществлять двойное направление зенкера (рис. 2.7, в). Для этой цели на зенкере предусматривается верхняя и нижняя направляющие.
При двойном направлении зенкера возникают некоторые затруднения, связанные с необходимостью совмещения большего числа осей технологической системы. Для исключения влияния погрешностей из-за несовпадения оси шпинделя с осями зенкера и направляющих втулок, из-за биения шпинделя и других погрешностей, связанных с работой станка, применяют шарнирное или плавающее соединение инструмента со станком. В этом случае положение оси обработанного отверстия будет в основном определяться соосностью направленных элементов приспособления и зенкера и точностью их изготовления.
Для зенкерования оставляют припуск, равный примерно ⅛ - диаметра отверстия. При работе двузубым зенкером-улиткой величина припуска может быть и большей.
Грубое зенкерование отверстий после литья или штамповки обеспечивает 5-й класс точности, а зенкерование после сверления или чернового растачивания-4-й класс. Шероховатость поверхности соответствует 4-5-му классам.
Обработка зенкером производится на сверлильных, расточных токарных, револьверных и других станках. Наиболее широко она применяется на станках с вращающимся инструментом.
Развертывание является основным способом чистовой обработки отверстий диаметром до 400 мм 1-го, 2-го и 3-го классов точности. Развертыванию всегда предшествует сверление, зенкерование или растачивание.
Различаются цилиндрические, ступенчатые и конические развертки. Ручные цилиндрические развертки с прямыми и винтовыми зубьями используются для обработки отверстий диаметром от 3 до 50 мм; машинные цельные с цилиндрическими и коническим хвостовиками - для отверстий диаметром от 25 до 80 мм; машинные со вставными регулируемыми ножами - для отверстий диаметром от 40 до 100 мм; машинные насадные твердосплавные - для отверстий диаметром от 52 до 300 мм.
Развертка снимает значительно меньший припуск, чем зенкер, имеет угол в плане и большее число зубьев. Зубья развертки снимают стружку малой толщины и большой ширины, что позволяет применять при развертывании большие подачи.
Конструктивные особенности разверток таковы, что в процессе работы они испытывают большие радиальные и незначительные осевые нагрузки. Поэтому развертки не обеспечивают точности направления оси отверстия, они сами стремятся установиться по отверстию.
Для обеспечения точности направления оси отверстия перед развертыванием необходимо расточить его резцом или другим инструментом с принудительным центрированием и точным направлением.
Закрепляться развертка должна таким образом, чтобы во время работы она свободно устанавливалась по отверстию или имела точное направление.
Это достигается с помощью самоустанавливающихся патронов качающихся и плавающих.
![]() |
Качающийся патрон (рис. 2.8, а) представляет собой оправку, на конусную часть которой насаживают развертку и закрепляют ее торцовой шпонкой. Второй конец оправки входит в корпус патрона с большим зазором. Этот зазор позволяет занять развертке правильное положение в обрабатываемом отверстии, благодаря качанию оправки на оси, закрепленной в корпусе патрона.
В плавающих патронах развертка может свободно перемещаться параллельно самой себе, центрируясь в обрабатываемом отверстии. Благодаря этому даже при несовпадении осей патрона и обрабатываемого отверстия она занимает правильное положение. Одна из конструкций плавающего патрона представлена на рис. 2.8, б.
Оправка 9, в которую вставляют конусный хвостовик развертки, связана с хвостовиком 1 патрона с помощью корпуса 7 и упорного шарикоподшипника, состоящего из обоймы 3,шариков 4 и опорной плиты 2. Вращение хвостовика 1 передается оправке 9 через поводок 5 и четыре шарика 6. Вырезы в оправке 9, в которых находятся шарики, позволяют ей вместе с разверткой перемещаться на небольшую величину параллельно оси шариков.
Для устранения зазора в упорном подшипнике патрон регулируют путем вращения корпуса 7. В нужном положении корпус закрепляют винтом 8.
Самоустанавливающий патрон, изображенный на рис. 2.8, в, создает возможность перемещения развертки параллельно самой себе и покачивания ее на некоторый угол. Здесь связь между оправкой 9 и хвостовиком 1 осуществляется поводком 5 с шестигранными головками, сдвинутыми относительно друг друга на 30˚. Корпус 7 при помощи пружины 11 удерживает поводок в отверстиях хвостовиком оправки. Между оправкой и хвостовиком расположен упорный шарикоподшипник 4. В осевом направлении патрон регулируют гайкой 10. Шаровые головки поводка позволяют наклонять оправку 9 вместе с разверткой под некоторым углом к вертикали, а упорный подшипник обеспечивает небольшое перемещение оправки параллельно ее оси.
Иногда развертку направляют кондукторные втулки. Так же как и при зенкеровании, направление может быть нижним, верхним или двойным. На направляющей части развертки образуют канавки для размещения стружки.
Принудительное направление применяют иногда для предотвращения разбивания короткого отверстия при входе и выходе развертки.
В зависимости от диаметра и требуемой точности отверстия развертывание производят одной или двумя развертками. Отверстия 3-го класса точности получают однократным развертыванием, 2-го класса точности – двукратным. При обработке развертками можно получить отверстия и 1-го класса точности, однако такая высокая точность экономически не оправдывает себя (повышаются затраты на содержание разверток в надлежащем состоянии, используется рабочие более высокой квалификации, а иногда и ручное развертывание).
Для отверстий диаметром от 6 до 120 мм общий припуск на предварительное и чистовое развертывание составляет 0,2-0,4 мм . При предварительном развертывании снимается 80 % величины припуска, а при чистовом - 20%.
Шероховатость поверхности при развертывании достигает 5-9-го классов.
При развертывании выделяется большое количество тепла, что приводит к нагреву детали и вследствие этого к конусности обрабатываемого отверстия. Поэтому точность размеров отверстия будет выше при развертывании на больших подачах с обильным охлаждением.
Отверстия больших диаметров, короткие, глухие и с прерывистыми поверхностями, как правило, развертками не обрабатываются.
Чистовая обработка отверстий развертыванием применяется преимущественно в единичном и мелкосерийном производстве. Объясняется это тем, что стоимость изготовления разверток, допускающих небольшое число переточек, а также расходы на их переточку значительно повышают стоимость выполнения операции. Кроме того, стойкость разверток невелика - 300-500 отверстий в чугунных деталях и 80-100 - в стальных.
В крупносерийном и массовом производстве отверстия обрабатывается протягиванием.
Растачивание отверстий
Отверстия нестандартных размеров и большого диаметра ,глухие и короткие,точные по размерам и форме обрабатывают резцами на станках токарной группы, а также на расточных, агрегатных и других станках.
Растачивание может производиться как при вращении детали, так и при вращении инструмента. В некоторых случаях возможна обработка отверстий при совместном вращении детали и инструмента.
Растачивание на станках токарной группы – малопроизводительный способ обработки отверстий, что обусловлено недостаточной жесткостью расточного резца и плохой его теплоотводящей способностью. Однако оно широко осуществляется при обработке деталей на токарных станках. Это объясняется тем, что растачивании отверстий резцом можно достигнуть большей точности и более высокого класса чистоты, чем при обработке сверлением и зенкерованием. При обработке резцом удается выправить ось отверстия и придать ей заданное положение, обработать короткие глухие и больших диаметров отверстия.
Существенным недостатком процесса растачивания является трудность установки резца на размер. Однако на современных токарных станках, оснащенных точными лимбами, установка резца на размер упрощается.
Для обработки отверстий применяются расточные быстрорежущие и твердосплавные резцы.
Схемы обработки различных отверстий стандартными расточными резцами приведены на рис. 2.9.
![]() |
Схема растачивания сквозных отверстий диаметром до 100-150 мм показана на рис. 2.9, а; схема обработки ступенчатых и глухих отверстий – на рис. 2.9, б, в и г. При растачивании отверстий подрезаются и внутренние уступы. Эту операцию можно производить как с поперечной (см. рис. 2.9, в), так и с продольной (см. рис. 2.9, г) подачами. При подрезании с продольной подачей державку резца поворачивают на угол φ1 = 5˚.
Сквозные и глухие отверстия глубиной более 100-150 мм растачивают державочными резцами. При растачивании сквозных отверстий стержень резца устанавливается перпендикулярно оси державки (рис. 2.9, д), а при обработке глухих отверстий – под углом 45 или 60˚(рис. 2.9, е).
Наиболее простая и распространенная схема растачивания – обработка отверстия резцом, консольно закрепленными в суппорте, при этом создаются наиболее благоприятные условия для получения прямолинейной оси отверстия, совпадающей с осью вращения шпинделя станка. Поэтому при обработке деталей на станках токарной группы одним из переходов является растачивания отверстий, полученных путем литья, штамповки или сверления ,с целью обеспечения требуемого положения оси.
Для уменьшения отжатия резца при недостаточной его жесткости применяют инструменты с большим углами в плане, доходящими до 90˚.
![]() |
Повышение точности обработки и производительности достигается при осуществлении многорезцового растачивания. При установки резцов в державе последовательно друг за другом (рис. 2.10) работа резания распределяется между ними путем деления ширины реза (глубины резания). Для уменьшения деформации технологической системы рекомендуются двустороннее расположение резцов.
В серийном производстве отверстия обрабатывают пластинчатыми резцами, а также плавающими расточными блоками и головками. Пластинчатыми резцами (рис. 2.11) растачивают отверстия диаметром более 40 мм. В этом случае резание осуществляется путем деления толщины среза (подачи) между режущими лезвиями.
Сквозные отверстия растачивают пластинчатыми резцами с углом в плане φ = 45˚, а глухие – резцами с φ = 90˚. Угол φ1 = 2-3˚. Длина цилиндрического участка устанавливаются в пределах l = 0,1-0,2D, где D - диаметральный размер резца.
В крупносерийном и массовом производстве отверстия обрабатывают на специальных расточных станках при помощи расточных блоков.
Расточный блок, состоящий из корпуса 1, и нескольких резцов 2, закрепленных болтами 3, изображен на рис. 2.12, а. Конструкция блока позволяет регулировать и настраивать отдельные резцы на определенный размер по диаметру винтами 3. Каждый из резцов нижней пары настраивается на свой размер (d1 и d2 ) и выполняет черновое растачивание. В этом случае глубина резания делится между резцами.
![]() |
Верхняя пара резцов настраивается на окончательный размер по диаметру d и осуществляет чистовую операцию.
Чистовые резцы имеют микрометрические винты с точностью установки до 0,02 мм.
Комбинированный резцовый блок ЭНИМса (рис. 2.12, б) в зависимости от количества резцов состоит из двух или трех частей. В корпусе блока резцы закрепляют при помощи рифлений, которые позволяют регулировать их положения и настраивать на заданный размер по диаметру.
|
В настоящее время разработаны конструкции расточных блоков с механическим креплением многогранных пластинок твердого сплава.
Применение расточных блоков и головок, настроенных на определенный размер, обеспечивает наиболее высокую производительность труда.
![]() |
Для окончательной обработки отверстий диаметром от 25 до 600 мм используют плавающие пластины (рис. 2.13), условия работы которых приближаются к условиям работы самоустанавливающихся разверток.
Плавающие пластины 1 (см. рис. 2.13) свободно вставляются в паз державки 2 и закрепляются в ней при помощи винта 3.
Плавающие пластины бывают цельными и составные. Составные допускают регулировку ножей по диаметру с точностью до 0,01 мм. В промышленности наиболее широко используются пластины диаметром 50-150 мм при обработке отверстий на расточных станках.
Припуск под чистовую обработку здесь примерно такой же, как и при развертывании. Пластины и чистовые расточные блоки позволяют получать отверстия 2-го класса точности с шероховатостью поверхности 6-7-го классов. При чистовом растачивании резцом 3-го класса точности получают отверстия с шероховатостью поверхности 5-6-го классов.
Отверстия в корпусных деталях точно координированными осями обрабатывают на универсально-расточных станках, которые подразделяются на станки для обычных расточных работ и для точных. К точным станкам относятся координатно-расточные.
Основные отверстия в корпусных деталях обрабатывают на горизонтально-расточных станках. На них сверлят и растачивают отверстия, нарезают в них резьбу, фрезеруют плоскости. Эти станки применяют в единичном и мелко-серийном производстве.
В условиях массового производства для обработки отверстий расточными головками используют многошпиндельные расточные станки.
На горизонтально-расточных станках отверстия можно обрабатывать по трем схемам: 1) растачивать консольные оправками (рис. 2.14, а); 2) растачивать борштангами с использованием опоры задней стойки (рис. 2.14, б); 3) растачивать в кондукторных при шарнирном соединении расточных оправок со шпинделем станка (рис. 2.14, в).
При растачивании консольной оправкой упрощаются установка инструмента и оправки, а также отверстия. Точность обработки зависит от вылета инструмента и от способа подачи. Длина оправки от торца шпинделя и длина выступающей части шпинделя должна быть не более (5-6)d, где d-диаметр оправки. Оправки должны быть короткими и жесткими.
При подаче шпинделя вылет инструмента увеличивается, и точность обработки ухудшается. При подаче стола точность повышается.
Борштанги с использованием опоры задней стойки применяют для обработки крупных тяжелых деталей, имеющих отверстия в противоположных стенках, или при растачивании отверстий, у которых длина больше их диаметра.
![]() |
Точность размеров и формы при обработке по этой схеме зависит от точности борштанги и втулки задней стойки.
Точность расстояний между осями, а также точность положения отверстий относительно баз достигается при растачивании различными способами. Рассмотрим некоторые из них.
По разметке. Разметка не может обеспечить требуемой в современном машиностроении точности расстояний между осями, если допуски в сотых долях миллиметра. Поэтому растачивание по разметке применяется как предварительная операция в единичном и мелкосерийном производстве. Точность расстояний между осями при растачивании по разметке обычно составляет ± (0,2-0,5) мм, а при тщательном выполнении операции разметки может доходить и до ±0,1 мм.
При помощи оправок и концевых мер. Этот способ используется в единичном и мелкосерийном производстве при обработке деталей со сравнительно небольшими расстояниями между осями.
![]() |

,
где d - диаметр оправки.
Расстояние С может быть измерено также и штангенрейсмусом.
Перестановка шпинделя в вертикальном направлении для расточки второго отверстия, которое находится на расстоянии у от ранее обработанного, показана на рис. 2.15, б. В шпиндель станка и в точно обработанное первое отверстие вставляют оправки А и В и измеряют расстояние С1 :
,
где d1 - диаметр оправки В.
Высокая точность межосевых расстояний (порядка ±0,02 мм) может быть достигнута только при точном центрировании оправки В в отверстии (без зазора) и обработке отверстий с одной стороны.
Координатный способ растачивания систем отверстий является более совершенным и в настоящее время получил широкое распространение как в единичном, так и в серийном производстве. Этот метод применяется при обработке деталей, имеющих несколько отверстий с параллельными осями. Относительное положение оси каждого отверстия может определяться двумя размерами, которые связывают ось отверстия с двумя перпендикулярными плоскостями детали.
Сущность этого метода заключаются в том, что совмещение оси шпинделя с осями обрабатываемых отверстий производится путем перемещения детали или режущего инструмента во взаимно-перпендикулярных направлениях по установленным концевым мерам, отсчетным системам, шкалам и индикаторным устройствам с упорами. Эти устройства позволяют отсчитывать перемещение с точностью до 0,01 мм.
Координатное растачивание отверстий можно производить на токарных, горизонтально-расточных и других станках.
![]() |
Координатный способ растачивания на токарном станке показан на рис. 2.16. После предварительной разметки обрабатываемая деталь 3 крепится на планшайбе 1 в таком положении, чтобы одна ее базирующая плоскость плотно прилегала к угольнику 2; под вторую плоскость подкладывается блок концевых мер длины 4, размер которого должен быть равен С. После этого сверлится и растачивается первое отверстие детали (рис. 2.16, а).
Для последующей обработки деталь 3 передвигается по угольнику (рис. 2.16, б), при этом ранее установленный блок концевых мер не меняется, а под другую базовую плоскость подкладывается второй блок концевых мер, по размеру равный расстоянию В между центрами отверстий. При этой установке обрабатывается второе отверстие.
Остальные отверстия обрабатываются после перестановки детали на планшайбе, причем в случае, приведенном на рис. 2.16, в нижний блок мер снимается и деталь устанавливается прямо на плоскость угольника, а под вторую базовую плоскость подкладывается блок мер, равный чертежному размеру.
При обработке последнего отверстия (рис. 2.16, г) под деталь подкладывается блок мер размером С без изменения ранее установленного блока.
![]() |
Универсальное приспособление для координатной обработки отверстий (рис. 2.17) состоит из трех точных плит 1, которые скреплены так, что образуют три взаимно-перпендикулярные плоскости. Деталь 2 устанавливается базовыми поверхностями на плиты и прижимается к ним специальными прихватами. Обработка отверстия производится через кондукторную втулку 3, точное положение которой фиксируется концевыми мерами длины 4. Крепление втулок и блока мер осуществляется съемным зажимом, который условно показан стрелками 5. К приспособлению прилагается комплект концевых мер длины из 63 плиток и комплект кондукторных втулок для отверстий диаметром от 0,8 до 12 мм.
В промышленности обработка отверстий координатным способом чаще всего производится на горизонтально-расточных станках.
Совмещение оси шпинделя с осями обрабатываемых отверстий достигается перемещением шпиндельной бабки в вертикальном направлении, а стола – в поперечном горизонтальном направлении в соответствии с заранее рассчитанными координатами оси отверстия.
При перемещении стола и шпиндельной бабки отсчеты координат производят по шкалам, установленным на салазках стола и передней стойке станка. Так как точность установок по шкалам недостаточно высока, используют индикаторные устройства, концевые меры, штихмасы или другие средства.
При координатном способе обработки точность межосевых расстояний зависит от точности изготовления мерных стержней или от точности установки размера на штихмасе или блоке концевых мер. Точность обеспечивается в пределах 0,02-0,03 мм.
Современные горизонтально-расточные станки моделей 2620 и 2622 имеют оптические системы отсчета по шкалам и обеспечивают точность отсчета ±0,02 мм.
Значительно эффективнее координатное растачивание осуществляется на горизонтально-расточном станке мод. 262ПР с программным управлением.
Программное управление станком позволяет автоматически устанавливать по координатам стол в поперечном направлении и шпиндельную бабку в вертикальном направлении и шпиндельную бабку в вертикальном направлении с точностью ±0,05 мм.
При высоких требованиях к точности расположения отверстий растачивание производят на координатно-расточных станках. В современных моделях этих станков предусмотрены совершенные отсчетно-измерительные системы - индуктивные и оптические с экранной оптикой. Применяются штриховые меры, зубчатые рейки или винты-якорки индуктивных систем, не имеющие физического контакта с другими деталями измерительной системы станка и поэтому не подвергающихся износу. Точность установки координат на этих станках находится в пределах 0,002 мм - для станков малых размеров, 0,003-0,004 мм -средних и 0,006-0,008 мм - крупных. В координатно-расточных станках повышенной точности (мастер-станках) точность установок координат достигает 0,001 мм.
Обработка в кондукторах. В серийном производстве обработка производится с применением различных приспособлений, в том числе кондукторов.
В зависимости от размеров и конструктивных форм деталей используются кондукторы различных конструкций.
Мелкие детали, вес которых вместе с кондуктором не превышает 30 кг, обрабатывают на вертикально-сверлильных или горизонтально-расточных станках.
При обработке отверстий в кондукторах точность межосевых расстояний лежит в пределах ±0,02-0,03 мм.
Обработка отверстий на агрегатных станках. Для обработки отверстий в крупносерийном и массовом производстве применяются многошпиндельные агрегатные станки, скомпонованные из стандартных сверлильных головок.
На этих станках можно одновременно обрабатывать большое количество отверстий, расположенных в разных плоскостях с различных сторон детали.
Схемы компоновки многошпиндельных головок приведены на рис. 2.18.
Обработка отверстий в корпусных деталях производится на агрегатно-расточных станках. На них можно производить сверление, зенкерование, растачивание и развертывание цилиндрических и конических отверстий, подрезание торцов, снятие фасок, нарезание резьбы, растачивание канавок и п.т. Сравнительно небольшие участки наружных поверхностей обтачивают с помощью пустотелых зенкеров и головок. Применение специальных устройств позволяет фрезеровать плоскости, прорези и другие поверхности.
![]() |
Головки агрегатных станков могут перемещаться в вертикальном, горизонтальном и наклонном направлениях. Это дает возможность создавать большое количество технологических компоновок станков (см. рис. 2.18).
Для обработки отверстий на агрегатных станках широко используются многолезвийные, комбинированные и сборные инструменты, заранее установленные на требуемый размер.
Точность обработки отверстий на агрегатно-расточных станках соответствуют 3-му классу, а при использовании весьма точных режущих инструментов и приспособлений она может быть повышена.
Так как агрегатные станки являются специальным оборудованием, то их применение требует тщательных экономических обоснований.
Тонкое растачиваниеиспользуется для получения размеров геометрической формы, направления и прямолинейности оси отверстия высокой точности. Тонкое растачивание осуществляется при очень больших скоростях резания (100-1000 м/мин), малых подачах (0,01-0,12 мм∕об) и малых глубинах резания (0,05-0,4 мм). Детали из цветных металлов, сплавов и пластмасс растачивают алмазными резцами, а детали из черных металлов -твердосплавными резцами.
Рассмотрим примерные режимы резания при тонком растачивании.
При обработке деталей из чугуна скорости резания принимают от 100 до 200м∕мин, подачи - от 0,03 до 0,15 мм ∕об и глубина у резания – от 0,1 до 0,35 мм . При растачивании деталей из стали скорости резания должны составлять от 120 до 250м ∕мин, подачи - от 0,02 до 0,12 мм∕об и глубина резания – от 0,1 до 0,3 мм . При обработке деталей из цветных сплавов скорости резания принимают до 800 м ∕мин, подачи - от 0,02 до 0,1 мм ∕об и глубину резания - от 0,05 до 0,4 мм.
Тонкое растачивание производится на прецизионных расточных станках одношпиндельных и многошпиндельных, вертикальных и горизонтальных.
Отверстия диаметром 50-200 мм и длиной 75-200 мм обрабатывают на вертикальных станках, отверстия меньших размеров диаметров - на горизонтальных. Горизонтальные станки бывают односторонние и много-сторонние. Число оборотов шпинделя на этих станках - от 2000 до 6000 в минуту.
Резцы закрепляют в консольные жесткие оправки. Если жестокость оправки ограничивается размерами отверстия, то ее делают из твердых сплавов.
При тонком растачивании легко получают отверстия точностью 2-го и даже 1-го классов при шероховатости поверхности 9-10-го класса. При растачивании оправками из твердых сплавов погрешность формы (овальность, конусность) составляет 3-4 мкм.
При обработке на двусторонних горизонтальных станках получают высокую точность по соосности двух отверстий, расположенных в противоположных стенках детали.
Протягивание отверстий
Протягивание находит широкое применение в крупносерийном и массовом производстве. Это - высокопроизводительный процесс, обеспечивающий получение отверстий высокой точности.
Протягиванием обрабатывают отверстия разнообразного профиля диаметром от 3 до 300 мм с точностью 1-3-го классов и шероховатостью поверхности 6-9-го классов (рис. 2.19).Длина протягиваемого отверстия обычно не превышает трехкратной величины его поперечника. Перед протягиванием отверстия обрабатывают сверлом, зенкером или резцом.
![]() |
Высокая стойкость протяжек позволяет вести работу в течение нескольких смен без подналадки станка и инструмента, благодаря чему создаются условия для автоматизации процесса протягивания.
Различают профильное, прогрессивное и генераторное протягивание (рис. 2.20).
При профильной схеме резания (рис. 2.20, а) зубья протяжки срезают заданный припуск в такой последовательности, при которой окончательная форма и размеры обрабатываемой поверхности образуется последним зубом. Форма режущих кромок протяжки соответствует профилю обрабатываемой поверхности. При профильной схеме
![]() |
процесс резания происходит при малых подачах на зуб и при больших глубинах.
При генераторнойсхеме резания форма режущих зубьев протяжки не соответствует профилю обрабатываемой детали. Как видно из рис. 2.20, б, при обработке квадратного отверстия по генераторной схеме режущие кромки имеют форму дуг окружностей. Так как окончательная форма и размеры обрабатываемых поверхностей получаются от воздействия всех режущих зубьев, то на них образуется уступы. Точность обработки по этой схеме достигается тем, что несколько последних зубьев работает по профильной схеме.
При прогрессивной схеме резания (рис. 2.20, в) режущий периметр зубьев протяжки разделен на секции, благодаря чему каждый зуб срезает слой металла не по всему протягиваемому контуру, а на части его, при этом каждый зуб протяжки срезает слой толщиной в 5-10 раз большей, чем при работе по профильной схеме. При большой подаче на зуб можно протягивать черные поверхности, т.е. отверстия после литья или штамповки без предварительной обработки их.
Протягивание осуществляют на горизонтальных и вертикальных протяжных станках. Внутренние поверхности обрабатывают на горизонтально-протяжных станках с тяговой силой 10,20 и 40 т при рабочей скорости от 1,5 до 13 м ∕мин.
![]() |
В зависимости от предварительной подготовки деталей к протягиванию при обработке их устанавливают на жесткой или шаровой опоре. Когда торцовая поверхность детали подрезана, т.е. когда торец детали перпендикулярен оси отверстия, ее устанавливают на жесткой опоре (рис. 2.21, а). Если торцовая поверхность не подрезана или подрезана не перпендикулярно оси отверстия, деталь устанавливают на шаровой опоре (рис. 2.21, б). Когда у детали подрезана только одна торцовая поверхность, ее устанавливают на шаровой опоре необработанном торцом, чтобы зубья протяжки начинали резание с обработанного торца.
Если длина отверстий у деталей меньше 2-3 шагов между зубьями протяжки, то целесообразно протягивать отверстия одновременно у нескольких деталей.
Протягиванием можно образовать винтовые шлицы и канавки в отверстиях. Имеется несколько схем такой обработки. Одна из них основана на применении протяжек с винтовым зубом и приспособления, которое обеспечивает протяжке вращательное движение (рис. 2.22, а). При поступательном движении протяжка 1 получает принудительное вращение через пару зубчатых колес 2 и 3 и от валика 4, имеющего винтовую канавку. Благодаря наличию такой канавке на валике зубчатое колесо 2, перемещаясь по нему, вращается.
Наиболее простая схема протягивания внутренних винтовых канавок основана на свободном вращении детали 1 от самой протяжки 2 с винтовым зубом при ее поступательном движении (рис. 2.22, б), что обеспечивается шариковой опорой 3.
![]() |
Припуски на протягивание отверстий, полученных сверлением, зенкерованием или растачиванием, составляют от 0,5 до 1,5мм на диаметр. Отверстие под профильное протягивание изготовляют по 4-5-му классам точности.
Получаемая после протягивания шероховатость поверхности в значительной степени зависит от смазочно-охлаждающей жидкости. Обычно применяют сульфофрезол или 20%-ный раствор эмульсола с добавлением 4% мыла. При особо высоких требованиях к чистоте поверхности в качестве охлаждающей жидкости рекомендуется использовать ализариновую эмульсию.
Лабораторная работа № 3
Тема: Образование резьбовых поверхностей
Дата добавления: 2018-11-24; просмотров: 673; Мы поможем в написании вашей работы! |
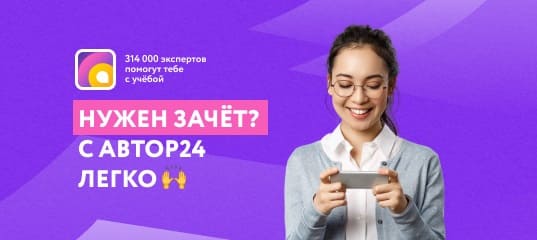
Мы поможем в написании ваших работ!