Выбор вспомогательных операций
Благодаря двусторонней обработки в сепараторах на станках СДШ 200 и СДП 200. в проектируем техпроцессе значительно уменьшено количество вспомогательных операций, таких как блокирование , разблокировка и промывка. Они присутствуют только на заготовительных операциях: наклеивание пластинок на квадрат для грубого шлифования рабочих сторон и склеевание пластинок в столбик.
Наклеивание пластинок на квадрат происходит следующим образом:
Наклеечное приспособление в виде квадрата нагревают на плите накаливания до температуры плавления наклеечной смолы (приблизительно до 1000 С). Куском восковой смолы смазывают квадрат тонким слоем. На этот квадрат равномерно раскладывают пластинки, притерая их к поверхности наклеечного приспособления.
После проведения грубого шлифования первой стороны пластины переклеиваются следующим образом. Второй квадрат аналогично нагревают, смазывают восковой смолой и аккуратно накладывают на обработанную поверхность. После охлаждения нагревают блок со стороны первого блока и осторожно сдвигают его
После обработки второй стороны заготовки, их разблокировывают, протирают и склеивают в столбик.
Изм. |
Лисm |
№ докум. |
Подпись |
Даmа |
Лисm |
38 |
НАТК.15 17 00.500 ПЗ |
К параметрам, обычно контролируемых в процессе изготовления деталей, а также проверяемых в лабораториях и ОТК, относятся габаритные размеры ( толщина, диаметр, длина, ширина и т.д.), радиусы кривизны, фокусные расстояния и фокальные отрезки, углы призм, клинья и фаски, форма и чистота поверхностей, децентрировка .
|
|
Для измерения габаритных и некоторых других размеров обычно используются приборы и устройства общепринятого назначения. К ним, в частности, относятся микрометры, штангенциркули, индикаторы, угломеры и др. Кроме приборов стандартного типа при изготовлении оптических деталей, используются специальные приборы и инструменты, например, пробные стекла, компенсаторы, сферометры, интерферометры и т. д.
Тип используемых для измерительных средств зависит от длины измеряемого размера, допуска, вида обработки и шероховатости поверхностей, серийности выпуска и ряда других факторов, поэтому целесообразно разделить выбор по типу оптических деталей и стадии их обработки.
После грубого шлифования на станке 3Д756 контролируют толщину заготовки индикатором часового типа. Приспособление представляет собой массивное основание со стойкой, на которой крепится кронштейн. В отверстие кронштейна устанавливается индикатор часового типа. Вначале измерения он
|
|
Изм. |
Лисm |
№ докум. |
Подпись |
Даmа |
Лисm |
39 |
НАТК.15 17 00.500 ПЗ |
устанавливается на нуль или номинальную толщину детали. Помещая деталь между площадкой столика и наконечником индикатора, считываем размер.
После кругления диаметр пластины контролируют калибром – скобой, как показано на рисунке
Рисунок 10. Калибр – скоба.
Диаметр отверстия лимба контролируется калибром – пробкой диаметром 18f9.
Калибры и шаблоны предназначены для измерения детали по одному и тому же размеру и являются безшкальными инструментами. Их особенно широко
применяют в массовом и серийном производстве для контроля размеров, формы и взаимного расположения поверхностей.
Изм. |
Лисm |
№ докум. |
Подпись |
Даmа |
Лисm |
40 |
НАТК.15 17 00.500 ПЗ |
При контроле измерительные поверхности калибров должны быть слегка смазанными маслом. Применение чрезмерных усилий при измерении приводит к
Изм. |
Лисm |
№ докум. |
Подпись |
Даmа |
Лисm |
41 |
НАТК.15 17 00.500 ПЗ |
|
|
На стадии среднего и тонкого шлифования контролируют качество поверхности: Точность поверхности пробным стеклом
После полирования поверхность оптической детали должна соответствовать требованиям чертежа. Отступления от расчетного радиусаконтролируют рабочими пробными стеклами. Пробное стекло накладывается на контролируемую поверхность и притирается к ней и наблюдается интерференционная картина. Для определения знака ошибки осуществляют нажим на пробное стекло, направляя усилие нажима вдоль оси изделия. Если кольца стягиваются к центру, то в центре имеется зазор (яма), если кольца стремятся к краю – бугор.
Контроль чистоты поверхностей оптических деталей
Контроль чистоты полированной поверхности заключается в следующем:
На обработанной поверхности не должно быть царапин, точек сколов, следов от предыдущей обработки. Контроль готовых деталей осуществляется в отраженном и проходящем свете на фоне черного экрана. Одновременно идет отбраковка деталей по дефектам стекла: пузырям, свилям. На чертеже оптических деталей класс чистоты обозначается буквой «Р» с добавлением номера, соответствующего классу чистоты. Номер обозначается римскими числительными, например, Р IV.
|
|
Царапина – вытянутая впадина на поверхности с соответствием размеров большей оси к меньшей более 3:1( участок, на котором несколько царапин очень близко расположены друг к другу, следует рассматривать как одну).
Точка – впадина или выступ поверхности, любого происхождения, в том числе и вскрытый пузырь с соотношением размеров большей оси к меньшей не более3:1.
Классы частоты поверхностей устанавливаются по допускаемым размерам, числу и расположению царапин точек на поверхности оптических деталей.
Изм. |
Лисm |
№ докум. |
Подпись |
Даmа |
Лисm |
42 |
НАТК.15 17 00.500 ПЗ |
В зависимости от расположения оптических деталей в приборе и их назначения следует устанавливать классы частоты поверхностей 0 – 10, 0 – 20, 0 – 40 – для поверхностей, расположенных в плоскости действительного изображения.
I, II, III, IV, V, VI, VII, VIII,IX – для поверхностей деталей, находящихся вне плоскости изображения.
Порядок контроля чистоты.
Подготовить рабочее место
Произвести влажную уборку, экрана, лампы, стола.
Покрыть стол черным бархатом, протереть лупу, приготовить спирт., батистовую салфетку, промыть беличью кисточку эфиром.
Протереть контролируемую поверхность для удаления жировых налетов и других загрязнений ватным тампоном, смоченным в спирте. Вытереть поверхность насухо батистовой салфеткой, смахнуть пыль беличьей кисточкой.
При определении чистоты поверхности детали должны просматриваться в косо направленном пучке походящего или отраженного света, то есть под углом к оси детали на фоне черного экрана.
Необходимо сфокусировать лупу на проверяемую поверхность и наблюдать дефекты по всей указанной в требованиях зоне. Сравнить максимально толстую царапину с эталоном чистоты и назначить класс чистоты.
Клиновидность лимба контролируют с помощью автоколлиматора
Автоколлиматор
Автоколлимационный метод контроля углов призм и клиновидности пластин в производственной практике обычно реализуется на автоколлимационных приборах путем сравнения с образцовыми или эталонными призмами, углы которых известны. Для этих целей можно использовать автоколлимационный прибор АКУ, имеющий трубу с фокусным расстоянием объектива 500 мм и ценой деления 0,5΄΄ точной шкалы оптического микрометра.
На рисунке 11 изображена оптическая схема АКУ. Пучок лучей от источника 9 после прохождения конденсора 8 и светофильтра 7 освещает автоколлимационную марку 6, расположенную в фокальной плоскости объектива 11. Марка представляет собой биссектор, нанесенный на стеклянную
Изм. |
Лисm |
№ докум. |
Подпись |
Даmа |
Лисm |
43 |
НАТК.15 17 00.500 ПЗ |
Рисунок 11 Оптическая схема автоколлимационного прибора АКУ
Величину фасок измеряют динаметром – лупой с сеткой, цена деления которой равна 0,01 мм. Для этого плоскость сетки динаметра совмещают с плоскостью фаски, ориентируя штрихи сетки параллельно краям фаски, считают количество делений. Количество делений, умноженное на цену деления даст истинный размер фаски.
Дата добавления: 2018-08-06; просмотров: 474; Мы поможем в написании вашей работы! |
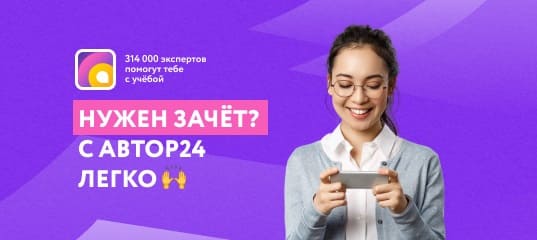
Мы поможем в написании ваших работ!