Шлифование закрепленными абразивными зернами
Почти все механические операции по обработке лимба производятся с помощью алмазно – абразивного инструмента. Поэтому необходимо знать его достоинства.
Эффективность шлифования стекла закрепленными абразивными зернами обусловлена несколькими причинами.
1. Закрепленные абразивные зерна работают как резцы, оставляя на обрабатываемой поверхности стекла сплошные пересекающиеся царапины.
2. Закрепленные зерна разрушаются только при воздействии на стекло, но не от перетирания одно о другое.
3. Рабочее давление инструмента сосредоточивается на небольшом числе зерен, выступающих из связки, и достигает значительных величин.
4. Скорость резания составляет 15—25 м/с, а рабочее давление 1 · 106 Па.
5. Неоднородность размеров зерен не проявляется, поскольку они работают только частью, выступающей из связки острыми гранями.
6. Обильная подача СОЖ эффективно удаляет разрушенное стекло и тепло.
7. При работе с малыми подачами образуются малые микронеровности поверхности при использовании зерен относительно крупной зернистости.
Изм. |
Лисm |
№ докум. |
Подпись |
Даmа |
Лисm |
26 |
НАТК.15 17 00.500 ПЗ |
Процесс шлифования закрепленными абразивными зернами служит для обработки вспомогательных поверхностей с шероховатостью до 6—7-го классов.
|
|
Производительность обработки закрепленными абразивными зернами на этих операциях определяется главным образом объемом припуска, удаленного в единицу времени.
Широкое распространение синтетических алмазов привело к шлифованию всех вспомогательных поверхностей оптических деталей только алмазным инструментом.
Шлифование закрепленными абразивными зернами начинает применяться и при тонком шлифовании оптических поверхностей. Это позволит избежать
перед полированием длительной технологической операции тонкого шлифования мелкими абразивными порошками и подготовить поверхность сразу к полированию. В этих случаях начинают применять алмазные инструменты с зернами мелких размеров и материал связки, имеющий некоторую пластичность. В дальнейшем, вероятно, станет возможным и алмазное полирование.
Абразивные материалы
Алмаз – кристаллическая модификация углерода. Кристаллизируется он в кубической системе. Твердость по минералогической шкале составляет 10; микротвердость порядка 100 000 МПа. В природе алмаз встречается в виде отдельных кристаллов кристаллов, вросших в горную породу, или же в продуктах
Изм. |
Лисm |
№ докум. |
Подпись |
Даmа |
Лисm |
27 |
НАТК.15 17 00.500 ПЗ |
|
|
В соответствии с этим их относят к различным маркам, которые регламентирует ГОСТ 9206—70. Область применения алмазных порошков определяется совокупностью свойств зерен. Для обработки оптических материалов их используют в основном в связанном состоянии. В свободном виде паст и суспензий они находят применение на завершающих стадиях обработки некоторых кристаллов.
Алмазные микропорошки ACM и АСН зернистостей 3/2-1/0 и субмикропорошки зернистостей 0,7/0—0,3/0 используют при полировании кристаллов. При определенных условиях, характеризуемых в основном свойствами связки, микропорошки применяют для полирования стекол.
|
|
Полировальные порошки
Качество порошков оценивают по их полирующей способности и чистоте обработанной поверхности. Полирующую способность характеризуют количеством стекла, сполированного в заданный промежуток времени с образца,
определенного размера, из стекла марки К8 в стандартных условиях испытания. Относительное знание способности для различных порошков близкого зернового состава приведено ниже.
Полирующий абразив | Относительная полирующая способность |
Окись хрома | 0,5 |
Полирит | 1,5 |
Окись тория | 2,2 |
Двуокись циркония | 1,0 – 2,0 |
Крокус | 1,0 |
Наличие в порошках царапающих примесей устанавливают, контролируя частоту полированной поверхности при помощи лупы с увеличением 6× в отраженном свете.
Полирование стекла
Цель полирования заключается в том, чтобы придать исполнительным поверхностям полную прозрачность для прохождения света и заданные значения N, ΔN, P.
Процесс полирования стекла водными суспензиями полирующих порошков имеет более сложную, чем шлифование, физико-химическую природу.
Изм. |
Лисm |
№ докум. |
Подпись |
Даmа |
Лисm |
28 |
НАТК.15 17 00.500 ПЗ |
|
|
Шероховатость такой поверхности должна быть трех – пяти сотых долей микрометра и установлена ГОСТ2789 – 73 по классам 14 и 13.
Наружный рельефный слой, образованный шлифованием, удаляется полированием полностью, а трещиноватый частично остается, но трещины на поверхности заполировываются частицами гидролизированного стекла и не мешают прохождению света.
Внешне картина процесса полирования происходит так. Зерна полирующего порошка, состоящего главным образом из окислов церия или железа, имеют размеры 0,2—2 мкм, они взвешены в воде и находятся между притирающимися поверхностями полировальника и стекла.
По сравнению со шлифующими зерна полирующих порошков имеют меньшую твердость и менее резко выраженные абразивные свойства самозатачивания при раскалывании. О раскалывании и притуплении зерен полирующих порошков, в большинстве случаев имеющих размеры 0,2—1,0 мкм, можно судить лишь по косвенным признакам.
Полировальник имеет смоляной рабочий слой. Площадки поверхностных неровностей шлифованной поверхности стекла и смоляной поверхности полировальника значительно больше размеров зерен полирующего порошка. Но на стекле неровности шлифованной поверхности имеют микрогеометрическую характеристику, а на смоле—макрогеометрическую. Рабочая поверхность вязкого смоляного полировальника, пластически деформируясь, выглаживается по микронеровной шлифованной поверхности.
Вода, в которой взвешены зерна, впервые моменты подачи, суспензии оказывает гидростатическое противодавление нажиму, но затем растекается и зерна закрепляются, адсорбируясь в наружном слое смолы. Часть зерен, еще не закрепившихся в смоле, перекатывается или, закрепившись на мгновение, продолжает движение по направлению вектора относительной скорости Vотн.
Зерна срезают вершины рельефного слоя, которые сразу становятся гладкими полированными. В дальнейшем размеры полированных площадок увеличиваются, высота неровностей уменьшается до свойственных 13—14-му классам шероховатости.
Изм. |
Лисm |
№ докум. |
Подпись |
Даmа |
Лисm |
29 |
НАТК.15 17 00.500 ПЗ |
кусочки коллоидной пленки, образующейся на поверхности стекла под химическим воздействием воды.
Остаточные неровности полированной поверхности меньше 0,03 мкм, т. е. меньше длины волны видимого излучения, так как размер части зерна, проникающей в стекло, не превышает 0,3 мкм.
В начале процесса полировании работа закрепленных зерен эффективнее, так как площадь каверн еще велика и перекатывающимся зернам негде закрепиться. Закрепленные зерна, срезая вершины конических выступов, если успела образоваться коллоидная пленка, имеющая пластические свойства, сдирают ее, а на поверхности образуются как бы столовые горы, т. е. площадки в совершенстве отполированной поверхности. Толщина сдираемых пленок уменьшается при расширении площади полированных участков и к концу процесса приблизительно равна высоте остающихся неровностей.
Пластические свойства смолы, удерживающей зерна, и коллоидной пленки способствуют тому, что работа зерен полирующего порошка не сопровождается появлением царапин с рваными краями и растрескиванием стекла в ширину и глубину. Благодаря пластическим свойствам коллоидной пленки кремневой кислоты борозды, образующиеся от снятия «стружки», затягиваются. Оставшиеся от шлифования трещины заполняются коллоидными продуктами гидролиза стекла.
При полировании химический процесс проявляется в том, что вода, действуя на стекло, образует коллоидную пленку. Толщина пленки растет быстро в зависимости от химической стойкости стекла данной марки, достигая предельной толщины приблизительно за одну минуту. Раньше считали, что процесс полирования может идти при взаимодействии зерен только с коллоидной пленкой, но теперь режимы обработки стали так интенсивны, что пленка не успевает образовываться и зерна полирующего порошка воздействуют на стекло, не имеющее поверхностной пленки.
Таким образом, механическое воздействие зерен имеет преобладающее значение и его усиление увеличивает эффективность полирования стекла. При полировании с помощью механических воздействий можно управлять процессом образования поверхности с заданными значениями N, AW и Р.
Изм. |
Лисm |
№ докум. |
Подпись |
Даmа |
Лисm |
30 |
НАТК.15 17 00.500 ПЗ |
Царапины в процессе полирования образуются при попадании под инструмент частиц более твердых и крупных, чем зерна полирующего порошка. Размеры дефектов чистоты полированных поверхностей оптических деталей указаны в ГОСТ 11141- 76.
Полирование выполняют на тех же станках, что и шлифование, но при меньшей частоте вращения рабочих органов. Шлифование длится минуты, а полирование – часы, тоесть время приблизительно в 20 раз больше времени шлифования.
Дата добавления: 2018-08-06; просмотров: 767; Мы поможем в написании вашей работы! |
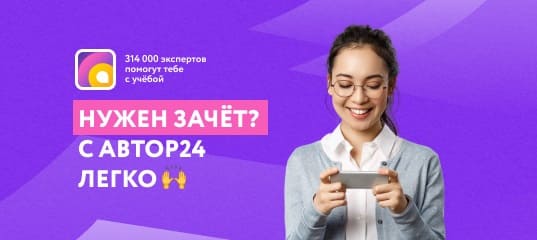
Мы поможем в написании ваших работ!