ВЛИЯНИЕ ПОДРЕЗКИ ПОЛИРОВАЛЬНИКА НА РАСПРЕДЕЛЕНИЕ СЪЕМА
СТЕКЛА ПО ПОВЕРХНОСТИ ЗАГОТОВКИ
Рис. 1.3
1.7. КОНТРОЛЬ ОПТИЧЕСКОЙ ПОВЕРХНОСТИ ПРОБНЫМ СТЕКЛОМ.
Для описания формы реальной оптической поверхности вводится понятие ближайшей сферы. Последняя представляет собой идеальную сферическую поверхность, имеющую минимальные отступления от реальной поверхности. На рис.1.4представлены реальная оптическая поверхность 1, ближайшая сфера 2 и номинальная сферическая поверхность3, представляющая собой идеальную сферу, радиус которой в точности соответствует заданному на рабочем чертеже.
ПОГРЕШНОСТИ ФОРМЫ СФЕРИЧЕСКОЙ ПОВЕРХНОСТИ
Рис. 1.4
Форму реальной оптической поверхности характеризуют двумя параметрами: отступлением ближайшей сферы от номинальной сферической поверхности и отступлениями
точек реальной поверхности от ближайшей сферы.
Величина называется общей ошибкой поверхности. Ее допустимый размер характеризуется на рабочем чертеже оптической детали значением N.
Величина называется местной ошибкой поверхности. Она характеризуется на рабочем чертеже значением
N.
Наиболее распространенным способом контроля формы оптической поверхности в производственных условиях является контроль пробным стеклом.Пробное стекло представляет собой линзу или пластину, одна из оптических поверхностей которой имеет совершенную геометрическую форму в виде плоскости или сферы известного радиуса кривизны. Вторая оптическая поверхность пробного стекла выполняется плоской.
|
|
Для контроля отклонений формы оптической поверхности от заданной используют пробное стекло с радиусом кривизны эталонной поверхности, равным его номинальному значению и имеющим противоположный знак (рис. 1.5).
СХЕМА КОНТРОЛЯ ОПТИЧЕСКОЙ ПОВЕРХНОСТИ
ПРОБНЫМ СТЕКЛОМ
Рис. 1.5
Пробное стекло1накладывают эталонной поверхностью 2на контролируемую оптическую поверхность 3. При освещении пробного стекла рассеянным светом со стороны плоской поверхности часть излучения будет отражаться эталонной поверхностью, а другая часть - контролируемой поверхностью. Эти отраженные пучки, взаимодействуя друг с другом, образуют интерференционную картину, которую можно наблюдать невооруженным глазом, глядя сверху на пробное стекло. В общем случае интерференционная картина будет представлять собой чередующиеся светлые и темные полосы
Светлые участки картины находятся в тех местах, где удвоенная толщина зазора между эталонной и контролируемой поверхностями составляет четное число полуволн излучения, используемого для освещения. Темные участки соответствуют точкам, в которых удвоенная толщина зазора составляет нечетное число полуволн.
|
|
На рис. 1.6представлен пример контроля пробным стеклом оптической поверхности идеально сферической формы, имеющей погрешность радиуса кривизны.
КОНТРОЛЬ ОБЩЕЙ ОШИБКИ ПРИN>1
Рис. 1.6
Показан случай, когда радиус реальной поверхности больше номинального. В этом случае пробное стекло 1касается контролируемой поверхности 2по краю, а зазорплавно увеличивается от края к центру детали, достигая максимального значения на ее оси. Интерференционная картина 3 при этом будет иметь вид концентрических колец. Причем число колец будет соответствовать количеству длин полуволн, на которое увеличивается толщина зазора при переходе от края детали к ее центру. На изображенном примере число колец интерференционной картины составляет N = 3. При монотонном изменении зазора по поверхности заготовки каждое новое кольцо соответствует приращению толщины зазора на .
Таким образом, максимальный зазор определяется по формуле:
1≈N
/2. (1.6)
Для управления формообразованием по результатам контроля необходимо уметь отличать случаи, когда касание пробного стекла и детали происходит по краю, а максимальный зазор расположен в центре ("яма"),от случая, когда касание происходит в центре, а максимальный зазор на краю ("бугор"). Легко убедиться, что вид интерференционных картин в обоих случаях приблизительно одинаков. Для того чтобы отличить '"бугор" от "ямы", следует приложить к пробному стеклу небольшое усилие, направленное сверху вниз. При этом в результате деформаций зазор между пробным стеклом и деталью изменится и это приведет в случае "бугра" к "разбеганию" колец от центра к краю, а в случае "ямы" - к их "стягиванию" от края к центру.
|
|
При равенстве радиусов кривизны эталонной поверхности пробного стекла и контролируемой поверхности детали они будут устанавливаться друг по другу с минимальным зазором, одинаковым по толщине по всейповерхности заготовки. В этом случае при использовании белого света интерференционная картина имеет равномерную по всему полю соломенно-желтую окраску (так называемый "соломенный цвет").
Если общая ошибка поверхности составляет доли кольца (N<1 ) или близка к единице, то ее достоверная оценка при контроле по схеме, представленной на рис. 1.6, невозможна. В этом случае интерференционную картину наблюдают по схеме с клиновым зазором между пробным стеклом 1и контролируемой деталью 2(рис. 1.7).
|
|
КОНТРОЛЬ ОБЩЕЙ ОШИБКИ ПРИ N ≤ 1
Рис.1.7
Для создания необходимого воздушного клина достаточно нажать на один край пробного стекла с небольшим усилиемF. При этом интерференционная картина приобретает виднезамкнутых полос. Если контролируемая поверхность обладает общей ошибкой, то полосы будут иметь форму дуг окружности, причем отношение стрелки спрогиба полосы, проходящей вблизи центра детали, к ширине dполосы определяет величину общей ошибки:
N= с/d. (1.8)
На примере, представленном на рис. 1.7, N 0,3. Опытный оптик определяет величину Nпо виду интерференционной картины с погрешностью, не превышающей 0,1 ширины полосы.
По этой же схеме производится контроль местных ошибок(рис. 1.8). При их наличии полосы приобретают отступления от правильной формы в виде дуг окружностей, получая местные искажения на тех участках, где поверхность имеет отступления от сферической формы. Размер Nэтих отступлений определяется отношением величины отклонения bинтерференционной полосы от идеальной формы дуги окружности к ширине dполосы:
N. = b/d. (1.9)
КОНТРОЛЬ МЕСТНОЙ ОШИБКИ
Рис. 1.8
Знак местной ошибки определяется следующим образом. Нажимают на край пробного стекла. В результате этого нажима образуется клиновой воздушный зазор между контактирующими поверхностями. Если при этом в месте дефекта полоса искривляется в направлении от точки нажатия ( на рис. 1.8- вправо ), то дефект имеет вид местного«бугра». При наличии местной«ямы» полоса искривляется в противоположном направлении.
2. ПРАКТИЧЕСКАЯ ЧАСТЬ.
2.1. ИСХОДНЫЕ ДОКУМЕНТЫ, ОБОРУДОВАНИЕ, ОСНАСТКА И
МАТЕРИАЛЫ.
Для выполнения лабораторной работы используются:
■ Рабочий чертеж обрабатываемой детали (вариант задания).
■ Блок заготовок, закрепленных на наклеенном приспособлении.
■ Станок 3ШП-350М.
■ Полировальник.
■ Кисть для подачи полирующей суспензии.
■ Полирующая суспензия.
■ Материал для промывки и чистки обработанных деталей.
■ Пробное стекло.
■ Кисть для удаления пыли с контролируемой оптической поверхности.
2.2. ПОРЯДОК ВЫПОЛНЕНИЯ РАБОТЫ.
2.2.1.Изучить раздел 1 настоящего описания и оформить теоретическую часть отчета по лабораторной работе.
2.2.2.Пользуясь формулами, содержащимися в разделе 1.3, определить основные размеры полировальника.
2.2.3.По формулам, приведенным в разделе 1.5, произвести расчет параметров, определяющих режим полирования.
2.2.4. Установить блок заготовок на шпиндель станка 3ШП-350М.
2.2.5.Произвести полирование поверхности заготовок, периодически подавая в зону обработки полирующую суспензию с помощью кисти.
2.2.6.По окончании обработки промыть блок от загрязнений и протереть обработанные поверхности заготовок салфеткой.
2.2.7.После высыхания блока удалить кистью пыль с поверхности одной из заготовок, установить на нее пробное стекло, по виду интерференционной картины определить общую (N) и местные ( N) ошибки поверхности, датьзаключение о соответствии обработанной поверхности требованиям рабочего чертежаи, при необходимости, - о методике ее доводки.
2.2.8.Закончить оформление отчета описанием практической части
работы.
Примечание: пп с 2.2.4 по 2.2.7 выполняются под руководством учебного мастера.
3.СОДЕРЖАНИЕ ОТЧЕТА.
Отчет по лабораторной работе предъявляется преподавателю по ее завершении и должен содержать следующие сведения:
■ основные положения теоретической части работы с необходимыми иллюстрациями ( рис. 1.2, 1.6 - 1.8 );
■ краткое описание методики расчетов режима полирования и размеров полировальника;
■ изложение методики контроля формы оптической поверхности с помощью пробного стекла и доводки поверхности по результатам контроля;
■ значения параметров Nи N,полученные по результатам контроля, и заключение о необходимости доводки с указанием способа подрезки полировальника.
4.КОНТРОЛЬНЫЕ ВОПРОСЫ.
4.1. Каково назначение операции полирования?
4.2. При каких условиях полирование оптической поверхности может выполняться по схеме свободной притирки?
4.3. Схема полирования сферической поверхности.
4.4. Какие станки используются для полирования оптических деталей?
4.5. Основные полирующие материалы и области их применения.
4.6. Конструкция полировальника
4.7. Какие параметры обрабатываемой детали определяют выбор режима полирования?
4.8. В чем заключается подрезка полировальника?
4.9. Какова цель подрезки полировальника?
4.10. Методика определения способа подрезки полировальника по результатам контроля формы оптической поверхности.
4.11. Что такое пробное стекло?
4.12. Схема контроля формы оптической поверхности пробным стеклом.
4.13. Какие параметры оптической поверхности непосредственно измеряются с помощью пробного стекла?
4.14. Методика определения общей и местной ошибок поверхности по виду интерференционной картины, наблюдаемой при контроле пробным стеклом.
4.15. Как определяется знак общей и местной ошибок по виду интерференционной картины, наблюдаемой при контроле пробным стеклом?
Работа 4. АЛМАЗНОЕ СФЕРОШЛИФОВАНИЕ
Цель работы:Изучение операции алмазного сферошлифования.
При выполнении лабораторной работы студентами решается следующие задачи:
■ ознакомление со схемой обработки, основными видами оборудования и инструмента, применяемыми на операции алмазного сферошлифования;
■ получение навыков выполнения расчетов основных технологических параметров операции;
■ приобретение практических навыков обработки сферической поверхности на станке АЛ-1М с помощью кольцевого инструмента и контроля радиуса обработанной поверхности.
1. ТЕОРЕТИЧЕСКИЕ СВЕДЕНИЯ.
1.1.НАЗНАЧЕНИЕ АЛМАЗНОГО СФЕРОШЛИФОВАНИЯ.
Первым этапом формообразования сферической исполнительной поверхности является операция грубого шлифования. Ее цель - быстрое снятие с заготовки основной части припуска на обработку и формирование на заготовке сферической поверхности, которая в дальнейшем может быть преобразована в заданную на чертеже посредством снятия равномерного слоя припуска на тонком шлифовании и полировании.
Шероховатость грубо отшлифованной поверхности заготовкиоптическойдетали должна соответствовать значениям от Rа=1,6мкм до Rz=20мкм. Грубое шлифование сферической поверхности в оптической технологии может быть выполнено одним из 2-х способов:
- свободной притиркой с использованием суспензий абразивных порошков;
- алмазным сферошлифованием с использованием кольцевого алмазного инструмента.
Первый способ применяется в единичном и опытном производстве, реже - в мелкосерийном; второй - в серийном, крупносерийном и массовом.
1.2.СХЕМА ОБРАБОТКИ. ПРИМЕНЯЕМОЕ ОБОРУДОВАНИЕ
Кинематическая схема алмазного сферошлифования представлена на рис.1.1.Заготовка 1устанавливается на шпиндель 2нижнего звена станка, имеющий вертикальную ось O1O1'вращения. Инструмент 3, представляющий собой металлический корпус в виде полого кругового цилиндра с нанесенным на его нижнем торце алмазоносным слоем, установлен в шпинделе верхнегозвена. Ось вращения O1O1'шпинделя инструмента пересекает ось вращения заготовкии составляет с ней угол .Движение подачи осуществляется, как правило, линейным перемещением S заготовки в направлении оси ее вращения снизу вверх.
СХЕМА АЛМАЗНОГО СФЕРОШЛИФОВАНИЯ
Рис. 1.1
Для получения в результате обработки заготовки точной сферической поверхности требуемого радиуса R3 необходимо выполнение следующих условий:
а) угол наклона оси инструмента к оси заготовки должен удовлетворять
равенству
(Dин/(2R3), (1.1)
где DИН - диаметр режущей кромки инструмента;
б) режущая кромка инструмента должна пересекать ось вращения
заготовки ( на рис 1.1 точка их пересечения обозначена через А);
в) противоположный точке А участок режущей кромки инструмента
должен выходить за край заготовки.
При выполнении условий а и б ось вращения инструмента проходит через центр О2кривизны обрабатываемой поверхности. Одновременное выполнение условий би в обеспечивает снятие припуска по всей поверхности заготовки.
Рассматриваемая кинематическая схема реализуется на практике в сферошлифовальных станках для грубого шлифования кольцевым алмазным инструментом. К ним относятся станки серии «Алмаз», а также сферошлифовальные станки серии АШС. Одним из наиболее распространенныхстанков этого типа является станок AЛ-1M , на котором студенты выполняют практическую часть настоящей лабораторной работы.
1.2. ИНСТРУМЕНТ ДЛЯ АЛМАЗНОГО СФЕРОШЛИФОВАНИЯ
На операции алмазного сферошлифования используются кольцевые алмазные круги типов АК,2А2 , 2F2, а также чашечные круги АЧК и 12А2.На рис.1.2показана конструкция кругов типа АК , 2F2и 12А2.
Дата добавления: 2018-06-27; просмотров: 735; Мы поможем в написании вашей работы! |
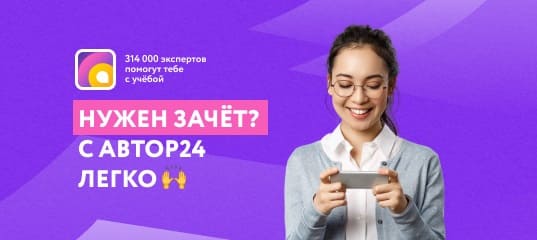
Мы поможем в написании ваших работ!