КОНСТРУКЦИЯ ИНСТРУМЕНТА ДЛЯ ПОЛИРОВАНИЯ
Рис. 1.2
Конструктивно корпус полировальника не отличается от шлифовальника, но, поскольку сила давления инструмента на заготовку при полировании должна быть меньше, чем при шлифовании, он выполняется из более легкого материала. Для изготовления корпусов полировальников с диаметрами до 250 мм используется цинковый сплав ЦМ4С. При большем размере применяют алюминиевые сплавы АЛ2, АЛ9 или АЛ11. В качестве материала, наносимого на рабочую поверхность полировальника, используются специальные полировочные смолы и грубошерстные технические ткани ( шерстяной войлок или сукно ). В последнее время все более широкое применение для этих целей находят полимерные материалы синтепол и полиуретан. Целесообразность применения того или иного материала определяется в зависимости от требований к точности геометрии обрабатываемой поверхности. Предельные значения параметров, характеризующих точность формы, достигаемую при использовании различных материалов, приведены в таблице1.1.
Таблица 1.1
Влияние материала рабочей поверхности полировальника на качество обработанной поверхности
Материал рабочей поверхности полировальника | Показатели качества поверхности | ||
Погрешности формы | ШероховатостьRZ, мкм | ||
N | ∆N | ||
Грубошерстная ткань | 6-15 | 2-5 | 0,1 |
Смола полировочная | 0,1 | 0,05 | 0,05 |
Синтепол, полиуретан | 5 | 0,5 | 0,1-0,05 |
Рабочие формулы для нахождения Dини Нинтакие же, как при расчете размеровшлифовальника ( см. формулы 1.3 - 1.5 на стр.22 настоящего пособия.). определяется из соотношения:
|
|
(1.1)
где «+» соответствует обработке выпуклой поверхности, а «-» - вогнутой.
Здесь через обозначена толщина слоя материала рабочей поверхности полировальника, при достижении которой следует обновить слой, увеличив его толщину до первоначальной толщины
,определяемой по формуле:
= ( 0,015 Dин + 0,5). (1.2)
Значение возрастает с увеличением
и лежит в пределах от 0,4 до 2,0 мм.
1.4. ПОЛИРУЮЩИЕ МАТЕРИАЛЫ.
При полировании в зону обработки вручную или автоматически подается водная суспензия полирующего порошка, отличающегося от порошков, применяемых для шлифования, как по химическому составу, так и меньшими размерами зерен (0,6-1,4 мкм ) и твердостью. В качестве полирующих материалов применяются полирит, крокус, окислы тория, циркония и ряда других металлов, а также алмазные микро- и субмикропорошки.
При обработке заготовок из оптического стекла наиболее распространен полирит, представляющий собой смесь окислов редкоземельных металлов, основным компонентом которой является окись церия (СеО2). Размер зерен основной фракции полирита составляет 1,3 – 1,4 мкм.
|
|
Для получения оптических поверхностей с нулевым и первым классами чистоты используется крокус. В его химический состав входит безводная окись железа (Fe2O3).Размер зерен в среднем составляет 0,6 - 1 мкм. Крокус обладает вдвое меньшей полирующей способностью, чем полирит, что обуславливает его ограниченное применение. Остальные полирующие материалы применяются реже и в основном - при обработке таких оптических материалов, как кристаллы, полимеры, полупроводники.
1.5.РЕЖИМ ПОЛИРОВАНИЯ.
Интенсивность режима обработки при полировании значительно меньше, чем при шлифовании. Поэтому, хотя толщина слоя припуска, снимаемого при полировании, не превышает 20 мкм, время, затрачиваемое на полирование, в несколько раз больше времени любого из переходов тонкого шлифования, на которых снимаются более толстые слои.
Выбор оптимальных скоростей вращения шпинделя нижнего звена ( ) икачания поводка верхнего звена (
) производят исходя из требуемой точности формы полируемой поверхности, габаритов обрабатываемой детали и ее конструктивной сложности. Расчет рекомендуемых значений указанных скоростей осуществляется с помощью следующих эмпирических формул:
|
|
,об/мин, (1.3)
,об/мин,(1.4)
где N- допустимое значение местной ошибки обрабатываемой поверхности, указанное на рабочем чертеже;
- диаметр заготовки (или блока заготовок, если обрабатывается не одиночная заготовка, а блок), мм;
- категория сложности обрабатываемой детали (определяется по таблице 1.1, представленной на стр. 20настоящего пособия).
Оптимальное давление р на поводок верхнего звена определяется по формуле:
р = 6,8 10 -2М
S
N
,Па , (1.5)
где М - количество заготовок на блоке, шт;
S- площадь обрабатываемой поверхности одной заготовки, см2.
1.6.УПРАВЛЕНИЕ ФОРМООБРАЗОВАНИЕМ
В процессе полирования периодически производят контроль формы обрабатываемой поверхности. По результатам контроля проверяют соответствие геометрических параметров обрабатываемой поверхности требованиям рабочего чертежа и находят отступления реальной поверхности от заданной формы в различных зонах поверхности заготовки. По соотношению найденных отступлений для различных зон определяют те участки, в которых необходимо при последующей обработке снять больший припуск. Полученные результаты дают опытному оптику возможность произвести поднастройку станка и инструмента таким образом, что максимальный съем стекла при дальнейшем полировании будет обеспечиваться именно в этих зонах заготовки. Тем самым осуществляется управление процессом формообразования поверхности детали и обеспечивается уменьшение погрешностей ее формы в процессе полирования.Настроечными параметрами являются скорости вращения нижнего и качания верхнего звеньев, размах качаний поводка, величины смещений траектории центра поводка относительно оси вращения нижнего.
|
|
Основным приемом управления формообразованием обрабатываемой поверхности является изменение рабочей поверхности смоляного полировальника, называемое подрезкой полировальника. Подрезка полировальника заключается в нанесении на рабочей поверхности бороздок ( «резов» ) шириной 1-4 мм и глубиной 0,1-0,3 мм. Резы наносятся путем срезания острым ножом поверхностного слоя смолы в зонах инструмента, соответствующих тем участкам заготовки, в которых толщина снимаемого при последующей обработке слоя стекла должна быть минимальной На рис1.3 изображены возможные варианты нанесения «резов» на поверхности смолы (1) и соответствующее им распределение съема стекла по поверхности заготовки (2).
Технологический контроль и изменение по его результатам настройки станка и геометрии инструмента повторяются до тех пор, пока не будетдостигнута заданная форма обрабатываемой поверхности. Количество сеансов обработки, которое может потребоваться для этого в значительной степени зависит от квалификации рабочего-оптика. Заключительный этап полирования, на котором производятся описанные выше действия, направленные на управление процессом формообразования, называется доводкой оптической поверхности.
Дата добавления: 2018-06-27; просмотров: 617; Мы поможем в написании вашей работы! |
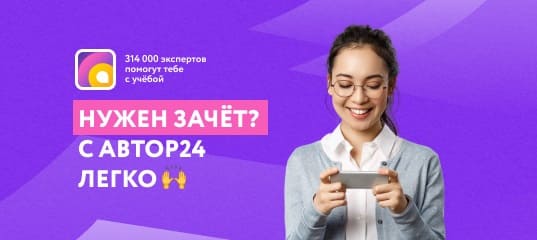
Мы поможем в написании ваших работ!