Типовой маршрут изготовления корпуса
Последовательность механической обработки корпуса призматического типа с плоским основанием и основным отверстием с осью, параллельной основанию.
005 Заготовительная
010 Фрезерная (протяжная)
015 Сверлильная020 Фрезерная Обработка плоскостей, параллельных базовой (при их наличии). Технологическая база – плоскость основания. Оборудование – (см. операцию 10).
025 Фрезерная Обработка плоскостей, перпендикулярных базовой (торцы основных отверстий). Тех. база – пл-ть основания и 2 точных отв. Оборуд. – гор.-фр. или гор.-раст. станок.
030 Расточная Растачивание основных отверстий
035 Сверлильная Сверлить (зенковать при необх.), нарез. резьбу в крепёж. отв.. Тех. база – та же. Оборуд.– рад.-свер., сверл. с ЧПУ, многооп., сверл. многошп. и агрегатный станки
040 Плоскошлифовальная
045 Расточная
В маршрут обработки разъёмных корпусов дополнительно к вышеприведённым операциям включают:
– обработку поверхности разъёма у основания (фрезерная);
– обработку поверхности разъёма у крыши (фрезерная);
– обработку крепёжных отверстий на поверхности разъёма основания (сверлильная);
– обработку крепёжных отверстий на поверхности разъёма крышки (сверлильная);
– сборку корпуса промежуточную (слесарно-сборочная операция);
– обработку двух точных отверстий (обычно сверлением и развёртыванием) под цилиндрические или конические штифты в плоскости разъёма собранного корпуса).
|
|
Качество машин. Способы обеспечения точности замыкающего звена при сборке
Качество – совокупность свойств и показателей, определяющих пригодность машины для удовлетворения определенных потребностей в соответствии с ее назначением.
Способы обеспечения точности замыкающего звена при сборке:
1) Метод полной взаимозаменяемости.
2) Метод неполной взаимозаменяемости (учитывает процент риска, т.е не все детали сборки годные).
3) Метод групповой взаимозаменяемости (искусственно увеличивают допуски сопрягаемых деталей в такое количество раз, которое обеспечивает возможность их рационального изготовления и сборки; после изготовления детали сортируются по группам, количество которых равно числу, на которое были умножены конструкторские допуски).
4) Метод регулирования (в размерную цепь вводят звено – компенсатор, с помощью которого обеспечивается заданный натяг или зазор в соединении).
5) Метод пригонки (на компенсирующем звене заранее оставляется необходимый припуск, удалением которого и обеспечивается заданная точность посадки).
Исходные данные для проектирования техпроцесса сборки. Особенности нормирования сборочных процессов.
Исходными данными:
|
|
1)прог-ма выпуска изделий и условия осуществления ТП
2)сбор. чертежи изделия узлов
3)тех условия сборки
4)раб. чертежи деталей входящих в изделие
5)объем кооперирования
6)каталоги и справочники по сбор. обор. и тех оснастке
7)образец собир. изделия
8)данные о сбор. про-ве
9)режим работы.
Нормирование сборочных операций
Заключ. этапом разработки ТП сборки машины являются нормирование сборочных работ, определение трудоемкости сборки и компоновка операций из переходов.
Нормирование – процедура организации и планирования процессов сборки с определением нормы времени на операцию. На основе технологич. нормирования определяются: 1)трудоемкость сборочных работ. 2)производит. рабочих мест. 3)устанавливаются расценки производимых операций. 4)определяют календарное планирование пр-ва. 5)реконструируют действующие или проектируют новые цеха
Норма времени – регламентир. вр. выполнения установленного объема работ в опред. произв. усл. одним или неск. исполнителями соотв. квалификации. В МС при сборке машин технологич. вр.устанавливается на технологич.операцию. Различают 3 метода нормирования вр.: 1-технический расчет норм по нормативам. 2-расчет норм на основе изучения затрат рабочего времени наблюдением (хронометраж и фотографирование). 3-определение по укрупненным нормативам – опытно-статистический метод
|
|
Для опред. длительности (цикла) сб. машин строят циклограмму. В избранном масштабе ц-рамма отражает последовательность затрат вр. на вып. операции и совмещение во вр. этих затрат. Она позвол.найти пути сокращ. цикла сб., что важно для уменьшения объема незавершенного производства.
При нормировании слесарно-сборочных работ определяют шт. вр. на операцию, причем нормирование ведется по нормативам вр. на слесарно-сб. работы. При сборке изделий партиями определяется штучно-кальк. вр. При поточной сборке в состав шт. вр. включается время на: 1 – перемещ. собираемого изделия (при периодически движущ. конвейере); 2 – возвращ. рабочего в исх. поз. (при непрерыв. движ. конвейере). Если первое вр. перекрывается др. эл-тами шт. времени, то оно не учит.
На основе шт. вр. опред.: - трудоемкость сборки всего изделия;- кол-во раб. мест, поз. и потоков, необх. для сб. одинак. изделий. В усл. поточного пр-ва длительность опер. д.б. равна или кратной такту сборки машины. Поэтому проводят корректировку операций.
Особенностью нормиров.сб. оп.явл. то, что доля машин. вр. в структуре нормы вр. значит. ниже чем при мехобработке. Это затрудняет внедрение технически обоснованных норм вр. и норма становится завис. от субъективного фактора.
Дата добавления: 2018-06-01; просмотров: 691; Мы поможем в написании вашей работы! |
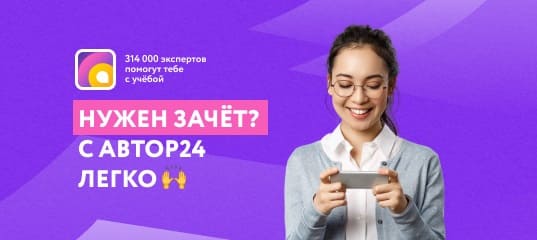
Мы поможем в написании ваших работ!