Определение расчетного момента сцепления
Сцепление автомобиля должно обеспечивать надежную передачу крутящего µρϐмомента двигателя к трансмиссии, в том числе при полном износе фрикционных накладок ведомого диска. Максимальное значение передаваемого сцеплением момента определяется по формуле:
Mсц = Memaxb, (2.1)
Memax – максимальный крутящий момент двигателя
b – коэффициент запаса сцепления; принимается для легковых автомобилей 1,2…1,75; для грузовых автомобилей 1,5…2,2; для автомобилей повышенной и высокой проходимости 1,8…3,0.
Момент, передаваемый сцеплением, создается в результате взаимодействия поверхностей трения ведомого диска с маховиком и нажимным диском. На фрикционном кольце (рис.2.12) выделим элементарную площадку dS и найдем элементарную силу трения:
dT = 0
dS =
0
и элементарный момент:
dM = 0
2d
(2.2)
где 0 =
-давление на поверхности накладки;
-коэффициент трения;
– радиус до элементарной площадки;
– центральный угол элементарной площадки;
R – наружный диаметр фрикционного кольца;
r – внутренний диаметр фрикционного кольца.
Наружный D и внутренний d диаметры фрикционных накладок, исходя из которых определяется Rср, задаются ГОСТ 12238-76. В табл. 2.1 приведены примеры фрикционных колец одно- и двухдисковых сцеплений. Наружный диаметр фрикционного кольца должен соответствовать диаметру маховика с учетом того, что к маховику крепиться кожух сцепления.
|
|
Таблица 2.1. Размеры фрикционных накладок сцепления
Модель автомобиля | D, мм | d,мм |
Однодисковые сцепления | ||
ВАЗ-1111 | 160 | 110 |
ВАЗ-2108 | 190 | 130 |
АЗЛК-2140 | 203 | 145 |
ГАЗ-3102 | 225 | 150 |
ГАЗ-53А | 300 | 164 |
Магирус-290 | 420 | 186 |
Татра-13881 | 350 | 195 |
Двухдисковые сцепления | ||
КАМАЗ-5320 | 350 | 200 |
МАЗ-5335 | 400 | 220 |
При двойном интегрировании выражения (2.2) по радиусу и по углу накладки получим выражение:
Mc = d
= 2
(R3-r3)/3. (2.3)
Подставив в данное выражение значение 0 =
,получим момент трения, передаваемый сцеплением:
Mc = Pпр i Rср, (2.4)
где Rср = - средний радиус трения;
i – число поверхностей трения: 2-для однодискового сцепления и 4 – для двухдискового сцепления.
2.4.2. Определение суммарного усилия нажимных пружини расчет пружин
|
|
Приравняв выражения (2.1) и (2.4), находим усилие, создаваемое нажимными пружинами (или пружиной) для обеспечения заданной надежности сцепления:
Pпр = . (2.5)
Число цилиндрических нажимных пружин при их переферийном расположении кратно числу рычагов выключения. При этом усилие одной пружины должно соответствовать условию: =
800Н. Это усилие зависит от деформации fпр и размеров пружины:
=
G, (2.6)
где dпр – диаметр проволоки;
DВ – средний диаметр витка пружины;
nрв – количество рабочих витков; полное число витков nпв = nрв + (1,2…2);
G = 8·104МПа – модуль упругости второго рода.
Эксплуатационные качества пружины зависят от ее жесткости, которая определяется по формуле:
Спр= =
. (2.7)
Напряжение кручения в витках цилиндрической пружины определяется по формуле:
=
(2.8)
|
|
и оно не должно превышать допускаемые значения [ ] = 700…900МПа.
Одна центральная нажимная пружина рассчитывается по этим же формулам, полагая
= Pпр.
Коническая пружина, применяемая обычно как центральная, имеет минимальную высоту в том случае, если навивка спирали позволяет при полном сжатии виткам совместиться в одной плоскости.
Усилие, создаваемое конической пружиной с прямоугольным сечением, определяется по формуле:
=
. (2.9)
Жесткость конической пружины равна:
Спр = =
. (2.10)
Напряжение, возникающее в витках при сжатии, определяется по формуле:
=
. (2.11)
В формулах применены следующие обозначения:
a и b - стороны сечения проволоки;
и
- коэффициенты, зависящие от отношения
(табл.2.2);
Dп и dп – соответственно, наружный и внутренний диаметры пружины.
|
|
Таблица 2.2. Коэффициенты для расчета спиральной пружины
a/b | 2,0 | 2,5 | 3,0 |
![]() | 0,246 | 0,258 | 0,267 |
![]() | 1,713 | 1,256 | 0,995 |
Расчетная схема для определения параметров диафрагменной пружины приведена на рис. 2.12.
Рис. 2.12. Расчетная схема диафрагменной пружины
Нажимное усилие диафрагменная пружина создает участком между опорными кольцами, закрепленными на кожухе, и наружным краем пружины, упирающимся в нажимной диск (рис. 2.7). Лепестки диафрагменной пружины выполняют функцию рычагов выключения, а их упругость способствует плавности включения сцепления. В сцеплениях автомобилей ВАЗ и АЗЛК их 18.
Толщина ленты, из которой штампуются диафрагменные пружины, находиться в пределах 2,0…2,5мм для легковых и 3,0…5,0мм для грузовых автомобилей.
Нажимное усилие диафрагменной пружины определяется по формуле:
Pпр= ln
[(H-
) (H-
) + h2], (2.12)
где =
;
Е = - модуль упругости 1-го рода;
= 0,25 – коэффициент Пуассона;
H – высота пружины;
h – толщина пружины;
a,b,c - размеры пружины (см. 2.12).
С помощью этого выражения может быть построена зависимость Pпр= f(
Усилие выключения сцепления может быть определено из равенства:
Pвык (c-e) = Pпр(b-c); Pвык = Pпр , (2.13)
где е – размер пружины (см. 2.12).
Ход выжимного подшипника определиться суммой перемещений сечения пружины (пружина в осевом направлении принимается недеформируемой) и лепестков при их деформации:
fпр = f1+f2 при значениях: f1 = (c-e) ; f2 =
,
где - угловое перемещение лепестков;
сл – жесткость лепестков;
- угол подъема пружины в свободном состоянии;
= 100…120.
Наибольшие напряжения возникают на малом торце при повороте пружины на угол т.е. когда пружина приобретает плоскую форму, поскольку суммируются напряжения растяжения
и изгиба
лепестков:
;
(2.14)
=
, (2.15)
где nл – количество лепестков;
Wи - момент сопротивления изгибу сечения лепестка.
Пружины диафрагменного типа изготавливают из высокоуглеродистых сталей марок: 65Г, 85Г, 60С2 и других. Расчетное допускаемое напряжение кручения принимается в пределах: [ ] = 700…800МПа.
2.4.3. Расчет элементов сцепления
Фрикционные накладки ведомого дискадолжны иметь высокий коэффициент трения. чтобы обеспечить при относительно небольших размерах сцепления гарантированную передачу крутящего момента двигателя. Расчетное значение коэффициента трения при проектировании сцепления принимается = 0,30. Фрикционные накладки должны выдерживать без разрыва угловую скорость вращения в два раза большую, чем максимальная угловая скорость коленчатого вала двигателя. температура накладок не должна превышать 2000С при длительной работе и 3500С при кратковременной.
В качестве материала фрикционных накладок применяются асбестосодержащие композиции с включением наполнителей из меди, латуни, бронзы, алюминия, цинка, свинца, графита и связующих смол, синтетического каучука и их комбинации. В последнее время широкое применение получили фрикционные накладки с минеральным содержанием асбеста или без него, как более экологичные при производстве и в эксплуатации.
Расчет фрикционных накладок производится по удельному давлению на их поверхности:
pуд = (2.15)
Значение удельного давления не должно превышать 0,15…0,25 МПа; при этом меньшие значения принимаются для сцеплений грузовых автомобилей, а большие значения для сцеплений легковых автомобилей.
Размеры нажимного и ведущего дисковопределяются размерами фрикционной накладки сцепления. Поскольку при трогании автомобиля с места эти диски нагреваются, то лучшего поглощения и рассеяния тепла, возникшего при буксовании сцепления, их делают массивными и жесткими, что предотвращает их коробление. Для восприятия дисками крутящего момента от маховика и кожуха сцепления предусматривается их соединение, конструктивные варианты которых приведены на рис.2.13.
Рис. 2.13. Типы соединений ведущих дисков с маховиком и кожухом: а - выступы нажимного диска; б - пальцы, запрессованные в маховик; в – зубья; г- пальцы, ввернутые в маховик; д – упругих пластин.
Наибольшее распространение получили упругие пластины (д), которые не препятствуют перемещению диска в осевом направлении и надежно передают крутящий момент, работая на изгиб и растяжение. Напряжение растяжения, которые испытывают такие пластины, определяется по формуле:
=
(2.16)
где - коэффициент. учитывающий распределение крутящего момента двигателя между дисками;
= 0,5-для нажимного диска однодискового сцепления и среднего ведущего диска двухдискового сцепления;
= 0,25 - для нажимного диска двухдискового сцепления;
R – средний радиус крепления пластин к кожуху сцепления;
z – число упругих пластин;
Sр – площадь сечения пластины;
Напряжение смятия элементов соединения по вариантам (а, б, в, г,) определяется по формуле:
=
(2.17)
где Sсм – площадь контакта связующих элементов.
Допускаемое напряжение на смятие 10…15МПа
При изготовлении литьем нажимного и ведущего диска применяют серый чугун марки СЧ-21; рабочие поверхности подвергают шлифовке.
Ведомые диски делают из высокоуглеродистых сталей марок 60Г и 65Г и в однодисковых сцеплениях их делают упругими, чтобы улучшить плавность включения.
У ведомого диска рассчитывают шлицы ступицы на смятие и срез:
=
; (2.18)
=
, (2.19)
где dн и dв – наружный и внутренний диаметр шлицов;
z – количество шлицов;
lш и bш – длина и ширина шлицов.
В качестве материала ступиц ведомого диска используются стали марок 35 и 40Х. Допускаемые напряжения смятия шлицов [ ] =15…30МПа; допускаемые напряжения среза шлицов [
] = 5…15МПа.
Рычаги выключениясцепления соединяются с нажимным диском и кожухом сцепления шарнирно, обеспечивая согласование траекторий перемещения точек рычагов. Конструктивные схемы рычагов выключения приведены на рис. 2. 14. На рис. 2. 14а представлена конструкция рычагов выключения, где несоответствие кинематики внешнего и внутреннего концов рычага компенсируется за счет перекатывания ролика 1 по лыске оси рычага 2. Конструкция, представленная рис. 2.14б имеет подвижную среднюю опору, что не только компенсирует несоответствие кинематики, но обеспечивает это при минимальном трении. В конструкции, представленной рис.2.14в, рычаг выключения установлен свободно на оттяжном пальце 4. На рис. 2.14г приведена конструкция, в которой для уменьшения трения применена упорная пластина 3, которая позволяет пальцу 5 перемещаться по отверстию цапфы 6.
а) б) в) г)
Рис. 2.14. Конструктивные схемы рычагов выключения сцеплении
Рис. 2.15. Расчетная схема рычага выключения сцепления
При выключении сцепления на рычаги от силы Р действует изгибающий момент, вызывающий напряжение изгиба:
=
, (2.20)
где Рпр.в = 1,2 - суммарная сила от нажимных пружин при выключении сцепления;
U= – передаточное число рычага;
Wиз – момент сопротивления изгибу сечения рычага.
Рычаги выключения изготавливают из ковкого чугуна и из малоуглеродистых или среднеуглеродистых сталей. Допускаемое напряжение изгиба 320…400МПа.
При расчетах гасителя крутильных колебаний определяют напряжения в его пружинах, угловую жесткость и момент замыкания гасителя, момент трения в гасителе и крутящий момент, передаваемый гасителем.
Максимальное усилие сжатия одной пружины гасителя определяется по формуле:
Pг = , (2.21)
где r – средний радиус приложения усилия к пружине;
z – число пружин в гасителе.
Напряжение кручения в пружине определяется зависимостью:
=
, (2.22)
Dср – средний диаметр витков пружины;
d – диаметр проволоки пружины;
kкр = - коэффициент кривизны витков; с =
.
Допустимое напряжение кручения в пружине составляет 700…900МПа.
Угловой жесткостью пружины является момент, необходимый для поворота ведомого диска относительно ступицы на один градус:
= 17,4 Rср.пр. ·c· z, (2.23)
где c – жесткость пружины;
z – число пружин;
Rср.пр. – средний радиус расположения пружин гасителя.
Момент замыкания гасителя выбирается таким, чтобы он не выключался из работы в различных дорожных условиях:
Mз = (1,2…1,4) . (2.24)
Момент трения, создаваемый гасителем крутильных колебаний, равен:
Mтр = Pпр Rср.н.· i·
, (2.25)
где Pпр – усилие пружин для сжатия дисков сцепления;
Rср.н. – средний радиус фрикционных накладок сцепления;
i – число фрикционных накладок;
- коэффициент трения фрикционных накладок.
Момент трения в гасителе может быть проверен по выражению:
Mтр = (0,1…0,15)Memax. (2.26)
Крутящий момент, передаваемый гасителем крутильных колебаний, равен сумме:
Mг = Mтр + Mпр = Pпр·Rср.н.· i· + Pпр ·Rср.п.·z, (2.27)
где Mпр = Pпр ·Rср.п.·z - момент от усилия пружин гасителя.
Дата добавления: 2018-06-27; просмотров: 3351; Мы поможем в написании вашей работы! |
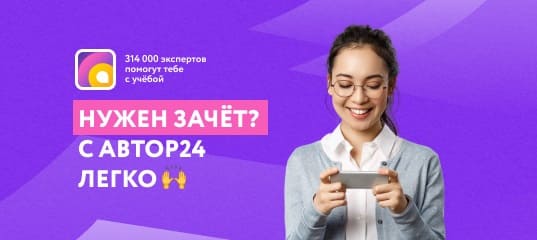
Мы поможем в написании ваших работ!