Определение нормального модуля
Согласно ГОСТ 21354-85 модуль зубчатого зацепления может быть определен по формуле:
mн = , (3.12)
где Mр – выбирают аналогично расчету на контактную прочность;
yF – коэффициент формы зуба, выбираемый по эквивалентному числу зубьев
Zэ = ;
– коэффициент, учитывающий изменение плеча действия нагрузки по линии контакта косозубого колеса;
; для
420 принимают
= 0,7;
kF – коэффициент нагрузки; kF = kFα kFbkFV – здесь коэффициенты, учитывающие соответственно распределение нагрузки между зубьями, неравномерность распределения нагрузки по длине контактной линии, динамическую нагрузку, возникающую в зацеплении; порядок нахождения этих коэффициентов определен ГОСТ 21354-85;
[ ] – допускаемое напряжение изгиба;
ψm= - коэффициент ширины зуба; ψm= 4,4…7,0 – для прямозубых шестерен; ψm=7,0…8,6 – для косозубых шестерен;
Z1 – число зубьев рассчитываемой шестерни.
В практике нормальный модуль зацепления выбирают по ГОСТ из размерного ряда с учетом передаваемого крутящего момента. В табл.3.1. приведены значения нормального модуля, рекомендуемые при соответствующих значениях крутящего момента двигателя.
Таблица 3.1. Значения нормального модуля для автомобильных коробок передач
Memax, Нм | 100…200 | 201…400 | 401…600 | 601…800 | 801…1000 |
mн, мм | 2,25…2,5 | 2,6…3,75 | 3,76…4,25 | 4,26…4,5 | 4,6…6,0 |
|
|
Во многих коробках передач модуль не одинаков на разных передачах; на низших передачах нормальный модуль может иметь большие значения. Однако, с технологической точки зрения, не рекомендуется применять в коробке больше двух значений нормального модуля в зацеплениях.
Шестерни коробок передач выполняют из легированных сталей марок 35X, 40X, 40XA, 12XH3A, 18XГТ, 30ХГТ и др. Для этих сталей допускаемые контактные напряжения составляют [ ]=1000…1200МПа и допускаемые напряжения изгиба составляют [
] = 700…800МПа.
Ширина зубчатого колеса зависит от величины передаваемого момента и от расстояния между осями валов. Приближенно ширину зубчатого колеса можно определить по формуле: bω = (5…8)mн.
Расчет валов
Нагрузки на валы коробки передач
На рис.3.10 представлена схема сил, действующих в зубчатом зацеплении, и реакции в опорах трехвальной соосной коробки передач с косозубыми шестернями.
.
Рис.3.10. Схема сил, действующих в коробке передач: а - на вторичном валу; в - на промежуточном валу; в – на первичном валу
Окружная сила на ведущей шестерни пары постоянного зацепления определяется по формуле:
Pпз = , (3.13)
|
|
где Memax – максимальный крутящий момент двигателя;
rопз – радиус начальной окружности шестерни первичного вала.
Осевая сила в косозубом зацеплении определяется по формуле:
Qпз = Pпз tg , (3.14)
где - угол наклона зубьев; для легковых автомобилей значение этого угла выбирают в пределах 250…400, а для грузовых в пределах 200…250.
Радиальная сила определяется по формуле:
Rпз = tg
, (3.15)
где - угол профиля зуба; обычно угол профиля зуба выбирают 200.
Окружная сила на других шестернях, а соответственно осевая и радиальная, определяются по формулам (3.13), (3.14), (3.15); расчетный крутящий момент определяется по Memax с учетом передаточного числа коробки i-ой передачи.
Расчет валов на прочность
Для трехвальной коробки передач расчет валов начинают с вторичного вала, чтобы вначале определить реакции в месте опоры этого вала на первичный вал. Далее рассчитывают первичный и затем промежуточный вал. В двухвальной коробке передач расчет начинают с ведущего вала. Валы коробки передач изготавливают из тех же марок сталей, что и зубчатые колеса, и рассчитывают на прочность и жесткость.
|
|
При расчете вторичного вала коробки передач, изображенной схемой на рис. 3.10,а, определяются реакции в опорах, а далее изгибающие моменты:
МизС = RC · n и MизD = RD · m,
крутящий момент-
Mкр = P · r0
и результирующие моменты:
MрезC = и MрезD =
(3.16)
По этим значениям результирующих моментов определяются результирующие напряжения изгиба в сечениях вала по формуле:
=
=
, (3.17)
где d – диаметр вала в опасном сечении.
Наибольший диаметр вала d предварительно может быть определен из соотношения к длине вала: для первичного (ведущего) и промежуточного валов d/l = 0,16…0,18, для вторичного - d/l = 0,18…0,21. Допускаемые напряжения на низших передачах могут приниматься [ ] = 400МПа.
При расчете промежуточного вала (рис. 3.10, б) вначале определяются силы, действующие на шестернях постоянного зацепления по формулам (3.13), (3.14), (3.15), затем силы на шестернях промежуточного вала для включенной передачи, результирующие реакции опор и результирующие напряжения. Определяются опорные реакции, строятся эпюры изгибающих и крутящего моментов (рис. 3.11). Используя принятые диаметры вала в различных сечениях, определяют результирующее напряжение и сравнивают его с допускаемым напряжением.
|
|
Рис. 3.11. Эпюра изгибающих и крутящего моментов, действующих на промежуточный вал трехвальной коробки передач
При расчете первичного вала (рис. 3.10, в) действующие силы на шестернях постоянного зацепления определяются так же, как и для промежуточного вала. Реакции опор и результирующие напряжения рассчитываются как для вторичного вала коробки передач.
Расчет валов на жесткость
Кроме расчета валов на прочность их необходимо проверить на жесткость по прогибу, по углу поворота сечения. Прогиб вала влияет на работу зубчатых передач, шумность коробки, ее долговечность. Осевые и радиальные силы вызывают прогиб валов в вертикальной плоскости (fв), а окружные силы – прогиб в горизонтальной плоскости (fг). При этом допустимые значения прогибов валов составляют: fв = 0,05…0,10мм; fг = 0,10…0,15мм.
Суммарный прогиб определяется по формуле:
f∑ = (3.18)
и не должен превышать 0,20мм.
Дата добавления: 2018-06-27; просмотров: 722; Мы поможем в написании вашей работы! |
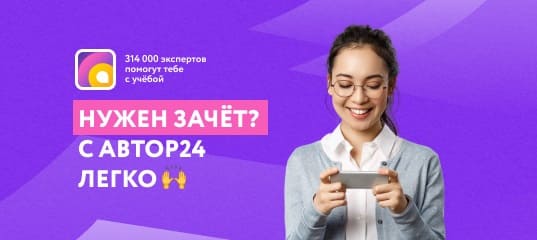
Мы поможем в написании ваших работ!